We value our partnerships with the media and welcome any inquiries about the ACG Group. Please use the resources on this page, or if you have any specific queries please reach out to the media contact listed below.
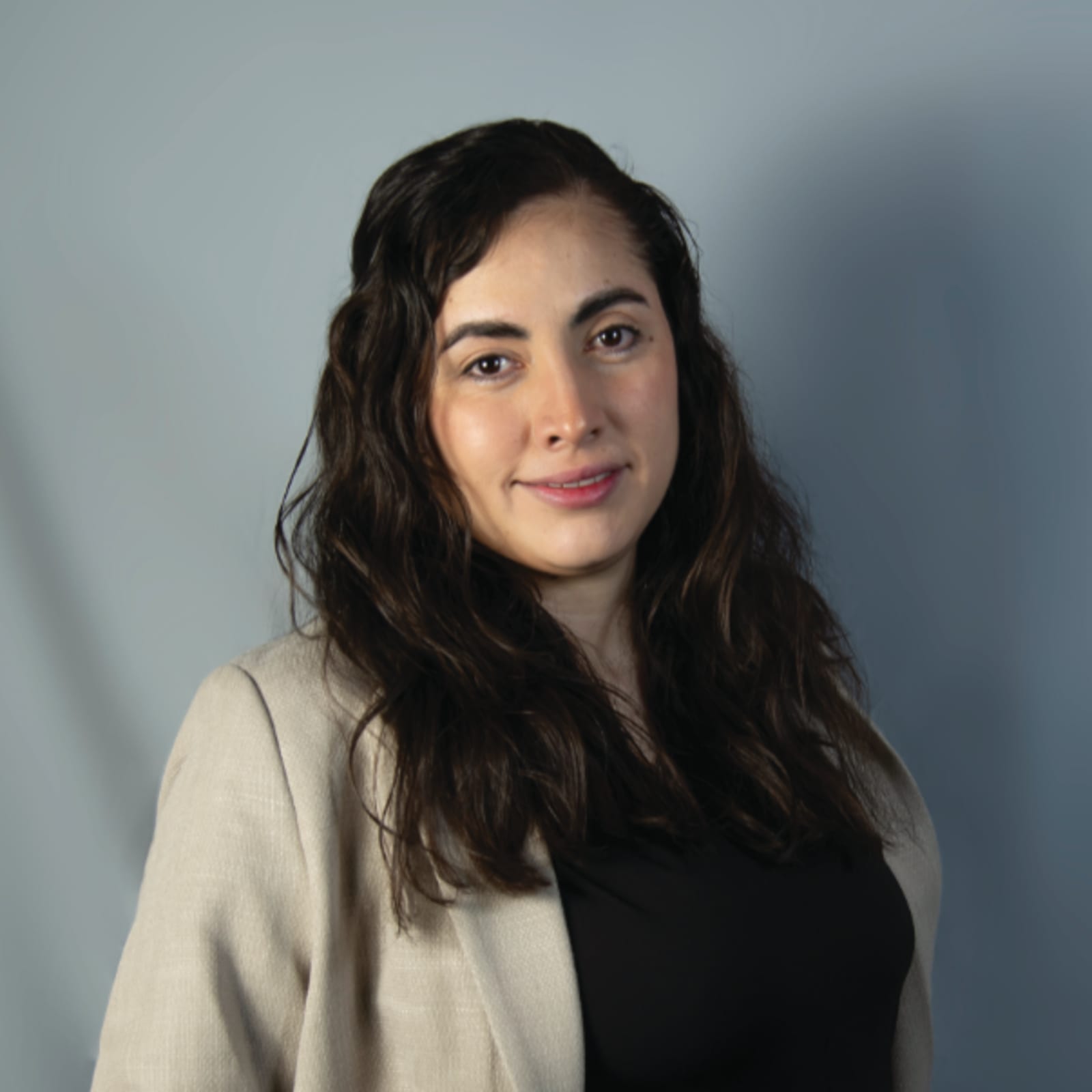
ACG to boost Mexico presence with appointment of Jessica Alfaro
ACG Engineering, a division of ACG, the world's only integrated pharmaceutical solutions and manufacturing company, is delighted to announce the appointment of Jessica Alfaro as territory sales manager for the Mexico region, as the company seeks to vastly increase its presence in the territory. In her new role, Jessica Alfaro will be responsible for promoting ACG’s portfolio of process and packaging machinery in Mexico, establishing new bonds with customers through the commitment of providing integral solutions to improve their processes. With a passion for engineering, Jessica previously worked as a sales engineer for Nicolás, Sven, Pacheco Y Andresen, Design and Engineering. Her responsibilities included the monitoring of technical specifications and industry standards, as well as the continuous development of the overall product offering. She also led board sessions, assigning requirements to valid use cases that highlighted the capabilities of the product. In addition, she worked closely with customers and the engineering team to determine the needs of the process and the requirements of the system. Commenting on the appointment, John Carey, vice-president of Sales at ACG Engineering, said: “We’re delighted to welcome Jessica into this pivotal new role. ACG is currently placing real focus and investment in the Mexico region for our process and packing machinery supporting both pharmaceutical and nutraceutical manufacturers with state-of-the-art technologies. We believe her experience and dedication will play a key part in building strong customer relations in the area.”Jessica Alfaro added: “I am delighted to be joining ACG, and embracing the challenges associated with gaining a deep understanding of our clients and providing them with the best solutions to help drive their business success. “I am excited by the idea of applying my analytical skills to design efficient and sustainable processes. My chemical engineering background gives me the opportunity to merge my passions for problem solving and teamwork, allowing me to contribute to the development of technologies and solutions that have a positive impact on the world around us.”About ACGFor over sixty years, ACG has been innovating the production solutions for pharmaceutical and nutraceutical companies, that help make people better. As the world’s most integrated provider of oral dosage products and services, we produce capsules, barrier packaging materials, manufacturing machinery, and visual inspection and traceability solutions. All fully compliant with international standards.Today, ACG fosters long-term collaborative partnerships with customers in 138 countries across six continents. Together, we share a common purpose: to solve the world’s greatest health challenges and make it better for everybody we serve. For more information, please contact the ACG media relations team:madhurima.chakraborty@acg-world.com
Read more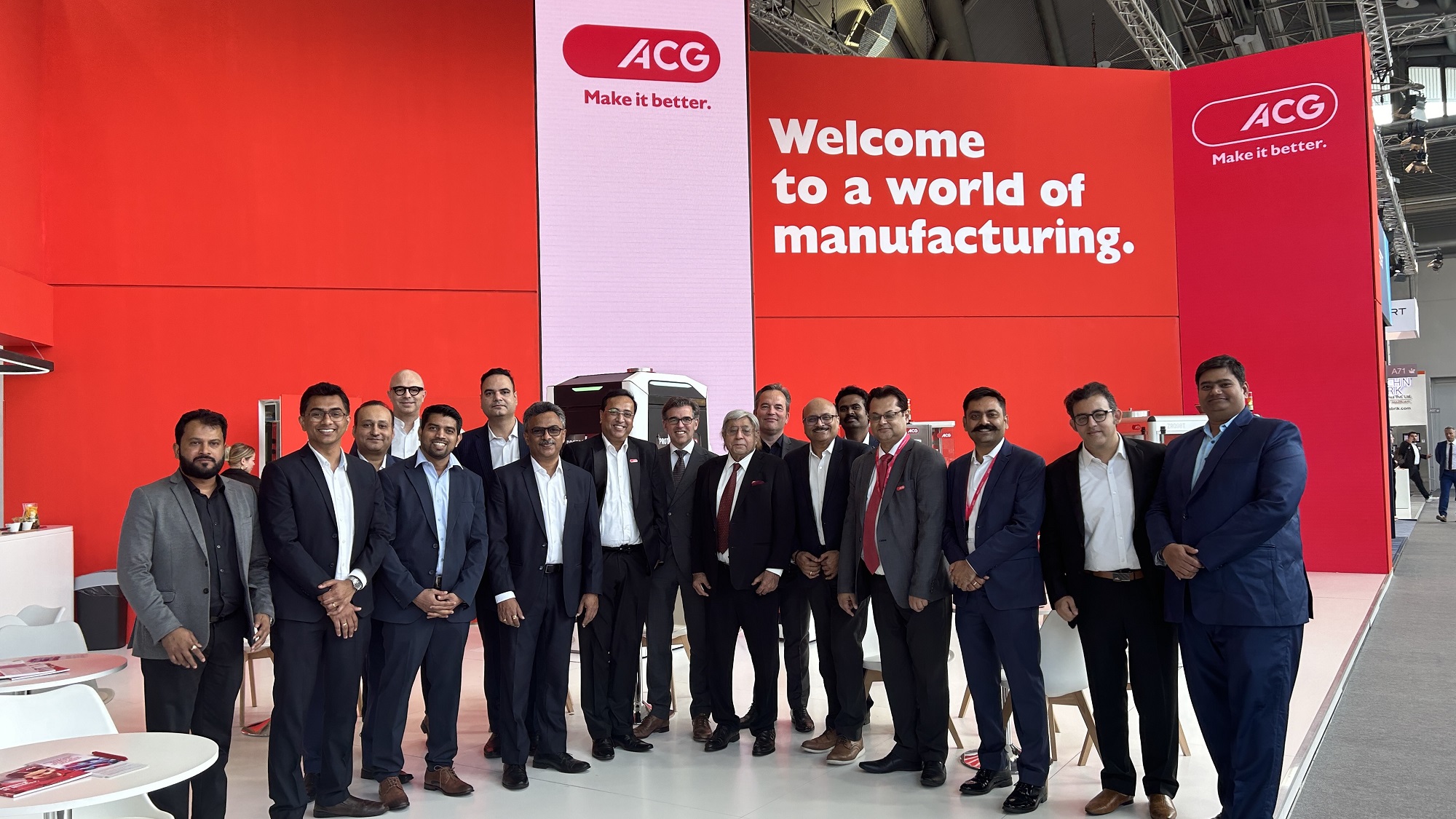
ACHEMA 2024: ACG Engineering on a mission to collectively ‘Make it Better’ World’s largest integrated supplier to the solid dosage manufacturing industry to display wide range of engineering and capsules products
At ACHEMA 2024 ACG Engineering, which provides end-to-end pharmaceutical engineering solutions,will be displaying its broadest range of products to date – underlining its commitment to ‘Making it Better’ for the industry and patients alike.The all-encompassing machines displayed will include the QUEST FB I, which is a highly versatile 'plug and play' fluid-bed unit for lab-scale feasibility studies. Also on show will be the ZRO 90T - a high-yield capsule filler. As will be the ACCURA 100FF - ACG's precision capsule checkweigher, suited for medium to large production batches with a capacity of 100,000 capsules per hour. Also on display will be the PROTAB 300 – a single rotary tablet press, which is suitable for R&D, small and medium-batch production, making scalability far easier, and the SECURECOAT TC III tablet coater, designed with operator safety and for use with highly potent active pharmaceutical ingredients (HPAPIs).Borja Guerra, vice president of international sales at ACG Engineering, said: “At ACG, we deliver efficient cutting-edge technology and a highly consistent ROI ratio for our global customer base, because we actively listen to them and their needs and take a collective approach towards ‘Making it Better’.“By aligning our shared strength and cross-divisional synergies with our Capsule and Films and Foils business units we are able to offer a whole world of different and highly targeted products and services – supporting large pharmaceutical companies and generic manufacturers with equal focus.”“We are really looking forward to ACHEMA 20024 and meeting with the industry to share knowledge and insights and to hopefully forge some new and exciting partnerships, continuing the expansion of ACG’s global footprint.”ACG will be exhibiting on stand A71 in Hall 3.1, between 10-14 June in Frankfurt.-Ends-About ACG For over 60 plus years, ACG has been innovating the production solutions for pharmaceutical and nutraceutical companies, that help make people better.As the world’s most integrated provider of oral dosage products and services, we produce capsules, barrier packaging materials, manufacturing machinery, and visual inspection and traceability solutions. All fully compliant with international standards.Today, ACG fosters long-term collaborative partnerships with customers in 138 countries across six continents.Together, we share a common purpose: to solve the world’s greatest health challenges and make it better for everybody we serve. For more information, please contact the ACG media relations team:madhurima.chakraborty@acg-world.com
Read more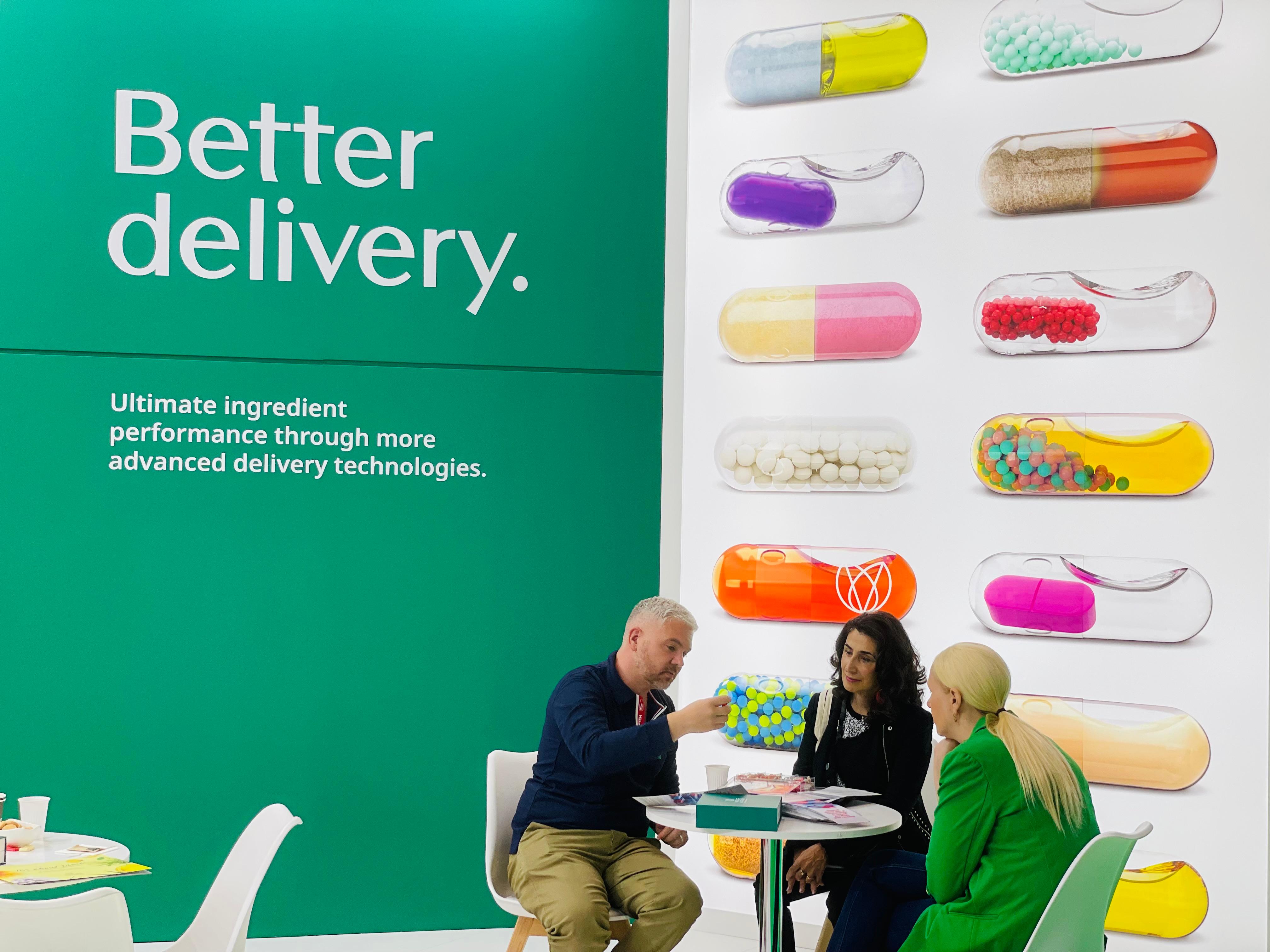
Vantage Nutrition to champion ‘better delivery’ at Vitafoods Europe 2024
At this year’s Vitafoods Europe, Vantage Nutrition (an ACG group company), will be showcasing and championing the term ‘better delivery’. With a real focus on innovation, the team will be debuting the outstanding beadlet technology, a complete product offering ultimate ingredient performance.Other ACG Capsules products on show will include ACGcaps™ H+, the world's first independently certified* ‘Clean Label' eco-friendly capsule, which is made using thermogelation technology (water and cellulose only). Alongside will be the ACGcaps™ TSafe opaque and TiO2-free clean capsules, with the enhanced version offering flexibility with pigmentation options.Aaron Quinn, head of business development at Vantage Nutrition – Europe, commented: “We know that the world’s healthiest products demand the world’s cleanest capsules performance through more advanced technologies. Through our innovations, we are committed to supporting nutraceutical brands when it comes to time consuming and costly R&D.“With the development of beadlet technology we are able to offer ultimate ingredient performance and enhanced delivery. Beadlets release ingredients over time, boost absorption and improve bioavailability. And by working with one supplier, manufacturers can ensure they have full control over all processes, with the 360 service – ensuring better results and enhanced uptake.”ACG is the world’s largest integrated supplier of pharmaceutical and nutraceutical solid dosage products and services. Along with the commitment to delivering integrated solutions and cutting-edge technology, Vantage Nutrition aims to provide the most comprehensive and advanced multiphase solutions to customers globally. The team’s focus in on turning product ideas into reality fast – helping companies enable, enhance, and differentiate nutra brands - from a full-service partnership to specific value additions.ACG will be exhibiting on stand H37, between 14-16 May in Geneva.* Certifications are applicable to certain colours and/or variants.About ACG For over 60 plus years, ACG has been innovating the production solutions for pharmaceutical and nutraceutical companies, that help make people better.As the world’s most integrated provider of oral dosage products and services, we produce capsules, barrier packaging materials, manufacturing machinery, and visual inspection and traceability solutions. All fully compliant with international standards.Today, ACG fosters long-term collaborative partnerships with customers in 138 countries across six continents.Together, we share a common purpose: to solve the world’s greatest health challenges and make it better for everybody we serve. For more information, please contact the ACG media relations team:madhurima.chakraborty@acg-world.com
Read more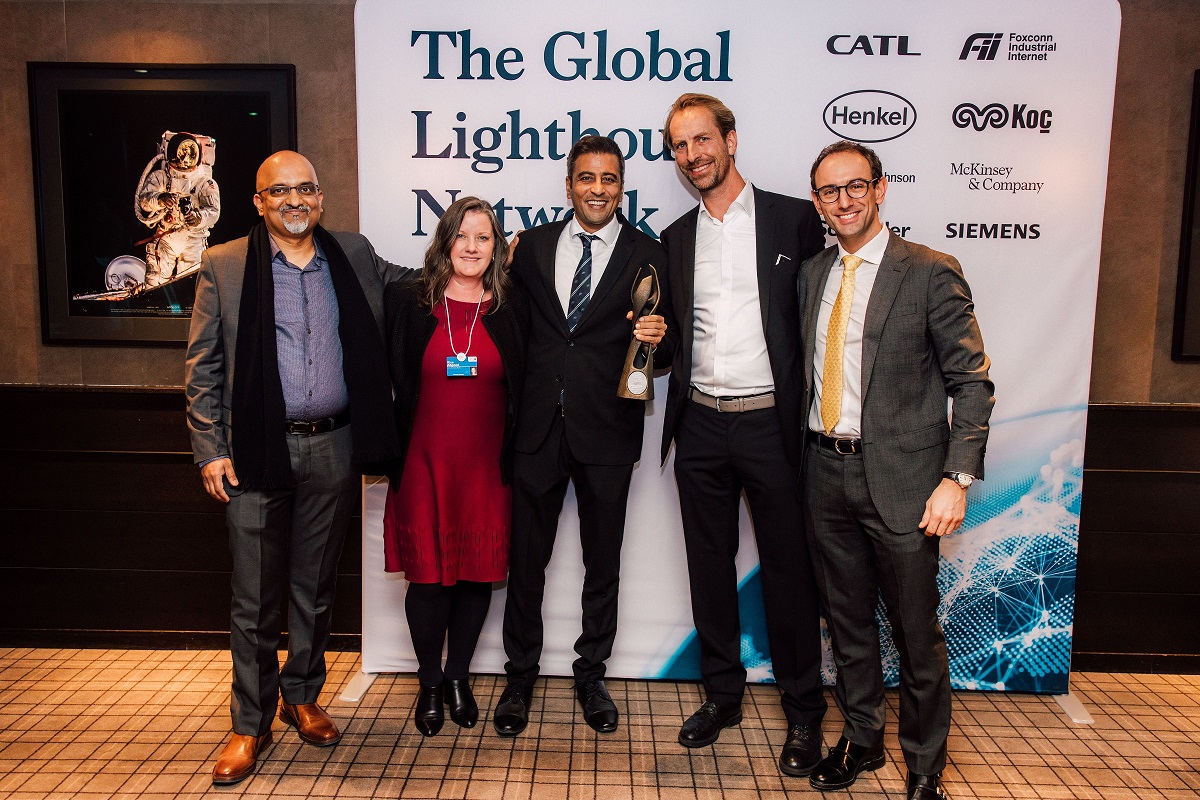
ACG Becomes the World’s First Capsule Manufacturing Factory to Join the Global Lighthouse Network Community 2023-24
ACG Capsules Pithampur, India is ACG’s 1st lighthouse to join the community Karan Singh, Managing Director and Balajikasiram Sundararajan, Chief Digital Officer attend the Global Light House Network ceremony in Davos to collect the award. ACG, the world's largest integrated supplier and service provider to pharmaceutical industry celebrated the inclusion of its capsule manufacturing facility in Pithampur, India, into the esteemed Global Lighthouse Network (GLN) by the World Economic Forum at the 54th Annual Davos Summit. The World Economic Forum’s Global Lighthouse Network has acknowledged the exemplary integration of Fourth Industrial Revolution (4IR) technologies, including artificial intelligence and big data analytics, by select factories globally. These facilities have been distinguished for their commitment to enhancing efficiency, fostering sustainable development, and simultaneously advancing their workforce’s skills and safeguarding the environment.Upon receiving the award, Mr. Karan Singh, Managing Director, said: “I am delighted to receive this recognition on behalf of my team. For me the most unforgettable part of our journey wasn't any technology or efficiency milestone, but the incredible team that made it all possible. Just ordinary people, united towards one goal, bringing about innovative collaborations to push boundaries of what is possible.” He added: “One of the stand-out features of our application was the Gen-AI integration. Something that was done in the less than two weeks. In between all the debate on what Gen-AI can do to humans it is a beautiful reminder that ‘technology is brilliant, but humans drive the change’. Let's remember that!”ACG operates across 138 countries in six continents and has positioned itself as a leader in the pharmaceutical sector by focusing on high-quality capsule production, increasing responsiveness, improving production yields, and boosting workforce efficiency. The company produces billions of capsules annually and has implemented over 25 innovative applications of 4IR technologies, including the industrial internet of things (IIoT), machine learning (ML), deep learning (DL), digital twins, extended reality, and generative AI.Selwyn Noronha, CEO, ACG Capsules, added: “We are extremely proud of our first factory lighthouse. From its inception the facility has pioneered in its field, but this latest honour recognises the excellence in adopting AI at speed and scale.“Our continued future-focused approach sets new benchmarks in quality and innovation, with the aim of ensuring maximum benefit for customers, regulators and the entire pharmaceutical ecosystem.”About Global Lighthouse Network Global Lighthouse Network is a collaborative platform bringing together forward-thinking manufacturers leading the charge in adopting Fourth Industrial Revolution technologies. Leveraging innovations like artificial intelligence, 3D-printing, and big data analytics, Lighthouses drive efficiency, competitiveness, and transformative business models at scale, fostering economic growth while championing workforce augmentation, environmental protection and providing a collaborative learning journey for all-sized manufacturers globally. The Global Lighthouse Network is a World Economic Forum initiative co-founded with McKinsey & Company and counselled by an Advisory Board of industry leaders, including Contemporary Amperex Technology (CATL), Foxconn Industrial Internet, Henkel, Johnson & Johnson, Koç Holdings, Schneider Electric, and Siemens. Factories and value chains that join the network are designated by an independent panel of experts.About ACG For over 60 plus years, ACG has been innovating the production solutions for pharmaceutical and nutraceutical companies, that help make people better. As the world’s most integrated provider of oral dosage products and services, we produce capsules, barrier packaging materials, manufacturing machinery, and visual inspection and traceability solutions. All fully compliant with international standards. Today, ACG fosters long-term collaborative partnerships with customers in 138 countries across six continents. Together, we share a common purpose: to solve the world’s greatest health challenges and make it better for everybody we serve.For more information, please contact the ACG media relations team:madhurima.chakraborty@acg-world.com
Read more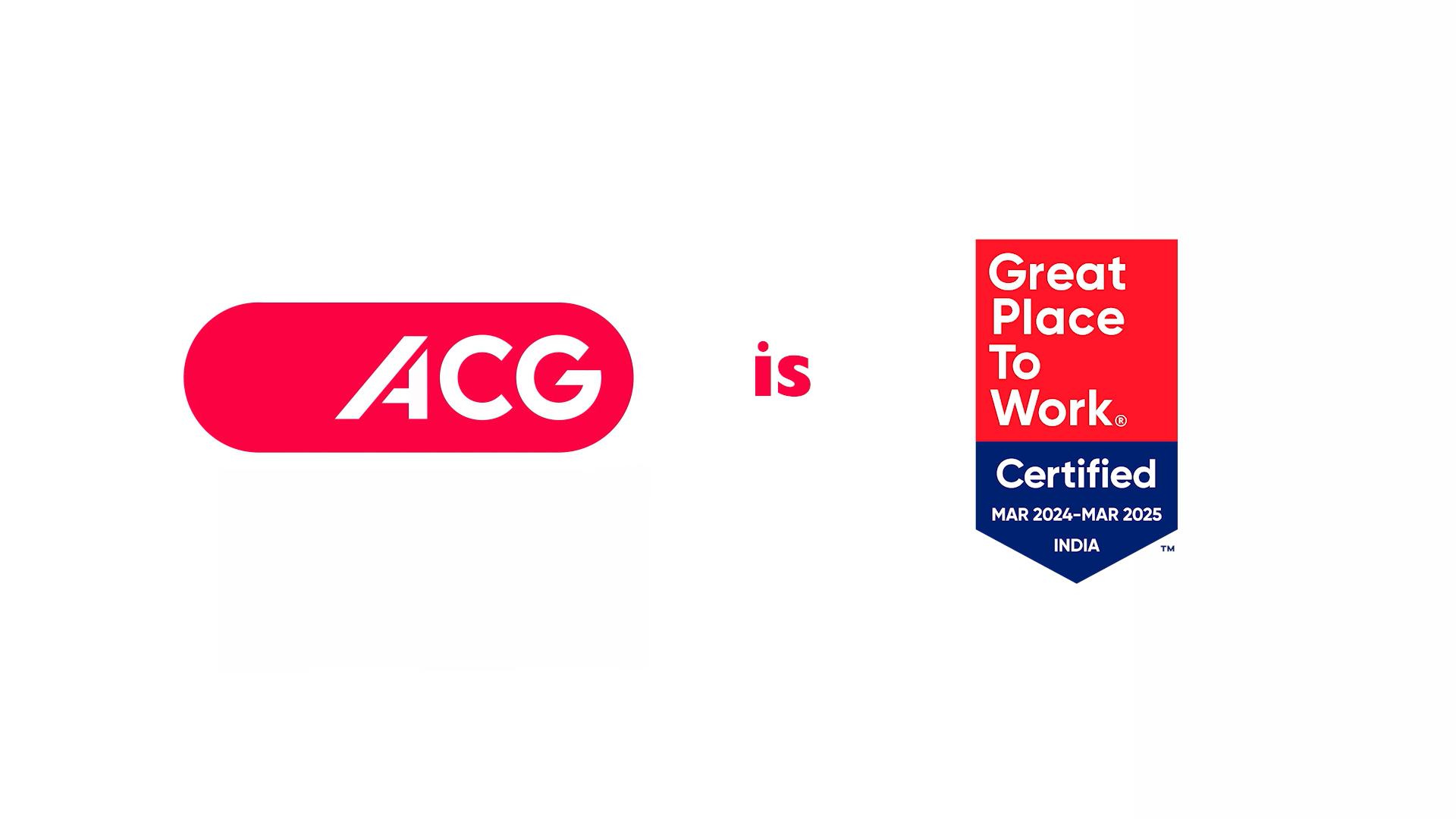
ACG awarded ‘Great Place To Work’ certification for a fourth consecutive year
ACG, the world’s largest integrated supplier and service provider to the pharmaceutical industry, is delighted to announce that for the fourth consecutive year, it has achieved the ‘Great Place To Work’ certification. This certification recognises employers who create an outstanding employee experience.Within ACG, five business units (Capsules, Corporate, Scitech – Research and Development Centre, Machinery, and Inspection), have been certified as a ‘Great Place to Work’. The comprehensive study, spanning five locations in India, encompassed approximately 3000 associates across management and plant categories. The process entailed a thorough survey based on key levers that define an organization's culture.Nikita Panchal, Group Head Talent, OD and DEI at ACG, said: “Winning this award for the fourth consecutive year fills me with pride and gratitude, recognizing the collective effort of our associates. It serves as a reminder of our commitment to excellence and the fact that institution-building is at the centre of all our actions as an organization.“ACG fosters collaboration by nurturing teamwork and effective communication. We care for our associates and the business community through support initiatives, and we remain progressive by supporting change and innovation. Our associates are encouraged to embrace our values, seize opportunities for growth and contribute their unique talents to shape a bright future together.”Sunil Jha, Group CHRO of ACG Group, added: “ACG thrives on collaboration through cross-functional teamwork, and – at all times – we prioritize the wellbeing of our associates.“Winning this award is incredibly gratifying and I am appreciative that all our associates have worked together to make this happen.”-Ends-About ACGFor over sixty years, ACG has been innovating the production solutions for pharmaceutical and nutraceutical companies, that help make people better. As the world’s most integrated provider of oral dosage products and services, we produce capsules, barrier packaging materials, manufacturing machinery, and visual inspection and traceability solutions. All fully compliant with international standards.Today, ACG fosters long-term collaborative partnerships with customers in 138 countries across six continents. Together, we share a common purpose: to solve the world’s greatest health challenges and make it better for everybody we serve. For more information, please contact the ACG media relations team:madhurima.chakraborty@acg-world.com
Read more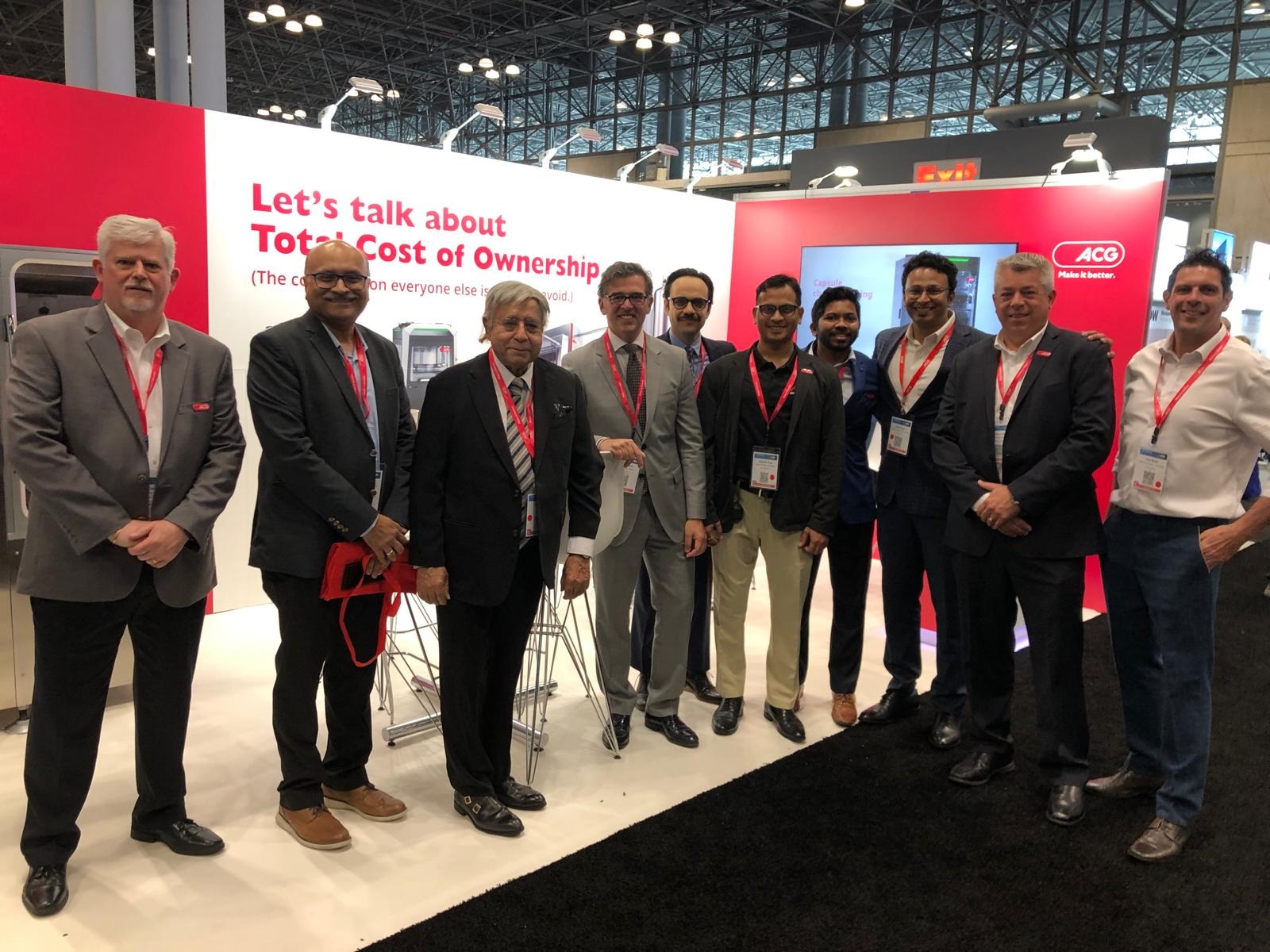
Interphex 2024: ‘ACG focuses on lowering manufacturer’s TCO’
At this year’s Interphex, ACG Engineering, part of ACG - the world's only integrated pharmaceutical solutions and manufacturing company - will be focusing on its cost-effective approach to taking generics to market.ACG’s methodology is based on speed-to-market, production efficiency and reducing manufacturing costs.Borja Guerra, vice-president of international sales at ACG, said: “As a highly experienced global supplier of process and packaging machinery of all oral solid dosage requirements, we are attuned to local market requirements. We aim to provide a low TCO (total cost of ownership) for premium pharmaceutical equipment.“With over six decades of experience partnering in the oral solid dosage space, we have taken over 8000 generics to market, working with more than 1000 pharmaceutical manufacturers to achieve this.”ACG will be showcasing its ACCURA 100 FF. The capsule checkweigher is designed specifically for precise, automatic, and continuous weighing of each capsule – whether empty, filled or partially filled, with anything from powder to pellets, and which is format free.ACG is the world’s largest integrated supplier of pharmaceutical and nutraceutical solid dosage products and services. The company will be exhibiting on stand 3515 between 16-18 April in New York.About ACG For over 60 plus years, ACG has been innovating the production solutions for pharmaceutical and nutraceutical companies, that help make people better.As the world’s most integrated provider of oral dosage products and services, we produce capsules, barrier packaging materials, manufacturing machinery, and visual inspection and traceability solutions. All fully compliant with international standards.Today, ACG fosters long-term collaborative partnerships with customers in 138 countries across six continents.Together, we share a common purpose: to solve the world’s greatest health challenges and make it better for everybody we serve. For more information, please contact the ACG media relations team:madhurima.chakraborty@acg-world.com
Read more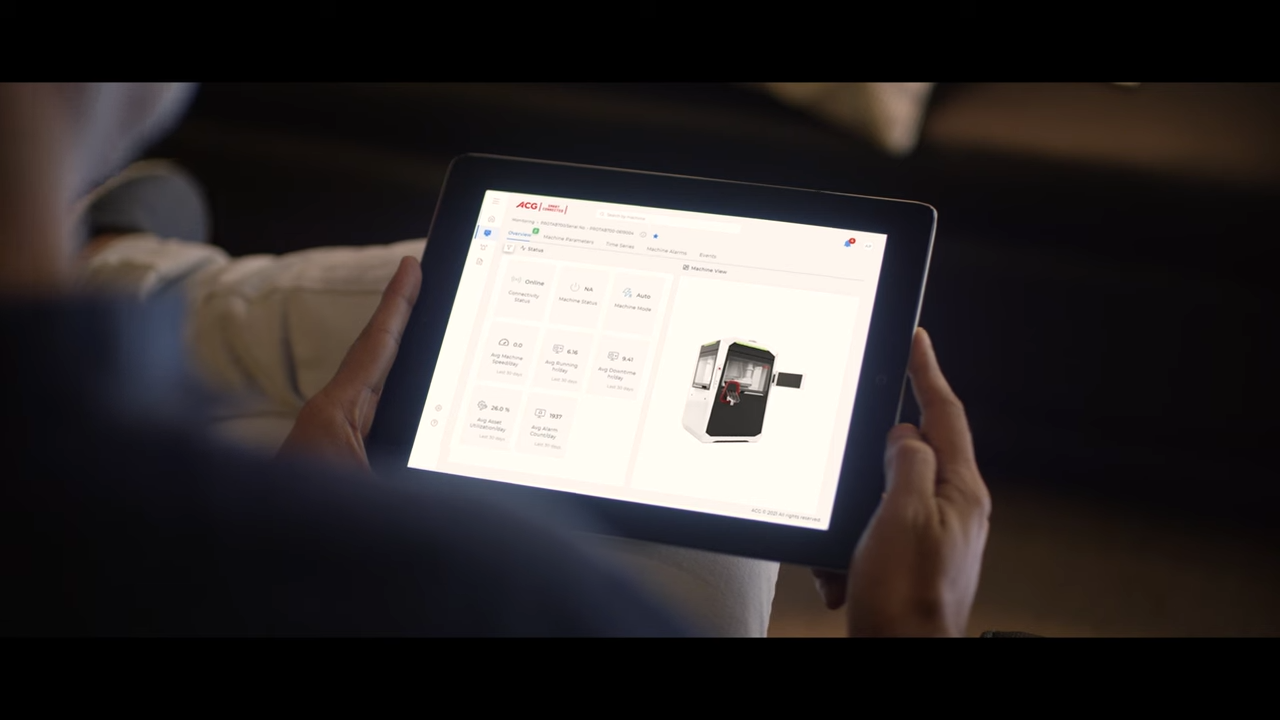
ACG Inspection launches new cloud-based offering to address upcoming VRS requirements under DSCSA regulations
In light of the impending Drug Supply Chain Security Act (DSCSA) regulations, ACG Inspection, a leading track and trace solutions provider for the pharmaceutical industry, has launched its new cloud-based Verification Router Service (VRS).The new system, which forms part of the ACG’s Inspections Life Sciences Cloud Service and Compliance Gateway, enables the automatic verification of saleable returns through product identifiers by routing requests and responses between stakeholders. Serialized products are assigned a unique identifier that can be used to track the product throughout its entire journey, enabling wholesalers to verify the authenticity of the products before they are resold.Shine Vijayan, CTO at ACG, commented: “The regulations, which have now been delayed by 12 months (coming into force in November 2024), will require all trading partners in the pharmaceutical supply chain to verify the identifier of any serialized drug product before redistributing it.“ACG’s existing VeriShield solutions tackles the implementation and interoperability challenges faced at Level 1, through to Level 3. With DSCSA’s regulation in place, ACG’s VRS covers level 4 - helping pharmaceutical manufacturers, distributors and retailers easily track and verify the saleable returns and secure their supply chain from counterfeit and substandard products.“ACG works closely with its customers, helping to address their pain points - one of which being concerns around data security. Our VRS employs robust security measures to safeguard serialized product information, guaranteeing the confidentiality and integrity of sensitive data throughout the verification process.”The system also guarantees real-time verification, to enhance operational efficiency and prevent supply chain delays. Additionally, it provides scalability assurance to accommodate an expanding volume of serialized data, to ensure continued robustness and reliability. And it incorporates exception handling, empowering stakeholders to address issues promptly to help maintain supply chain integrity.Shine Vijayan: “We are trusted experts and through our Life Sciences Cloud Service and Compliance Gateway, we can support counterfeit prevention, improving recall efficiency and data security. At all times, ensuring our clients are fully compliant with international standards and ready to meet the requirements as laid out in the impending DSCSA regulations.” -Ends- About ACGFor over sixty years, ACG has been innovating the production solutions for pharmaceutical and nutraceutical companies, that help make people better. As the world’s most integrated provider of oral dosage products and services, we produce capsules, barrier packaging materials, manufacturing machinery, and visual inspection and traceability solutions. All fully compliant with international standards.Today, ACG fosters long-term collaborative partnerships with customers in 138 countries across six continents. Together, we share a common purpose: to solve the world’s greatest health challenges and make it better for everybody we serve. For more information, please contact the ACG media relations team:madhurima.chakraborty@acg-world.com
Read more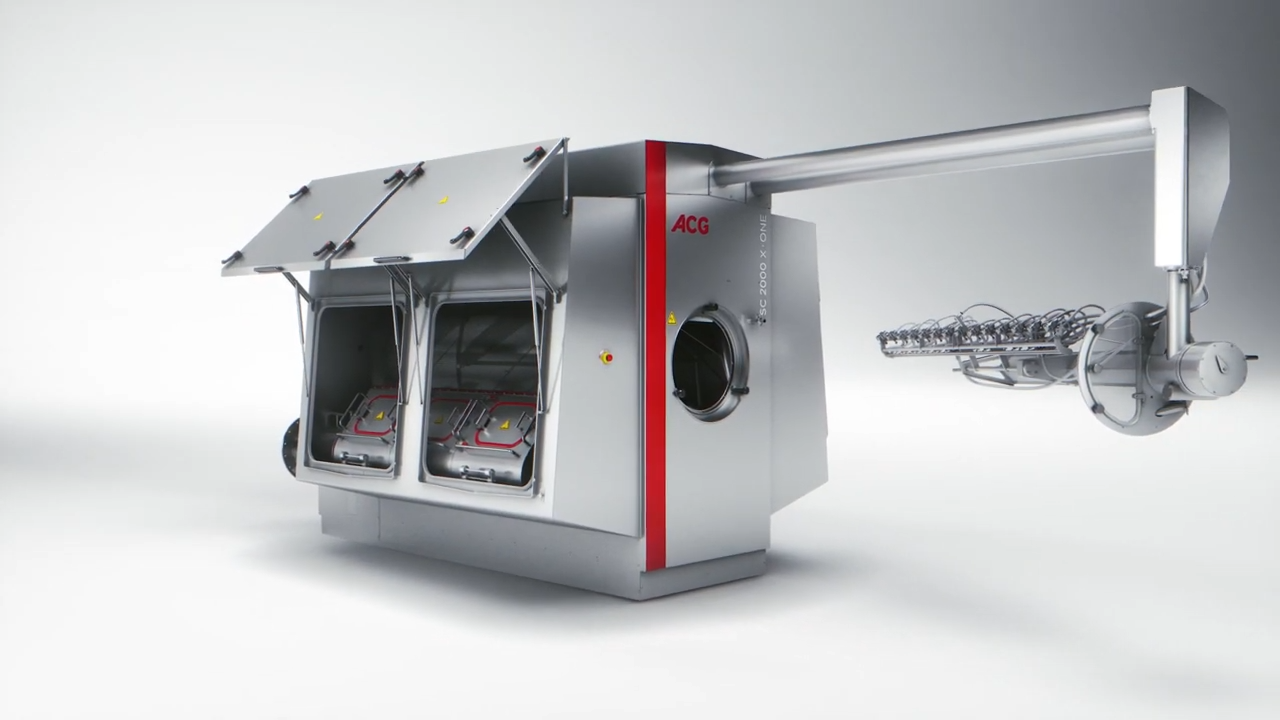
ACG Engineering launches the Smart Coater X.ONE Series Company’s fastest tablet coater ensures optimised production processes
ACG Engineering, a division of ACG, a leading supplier of integrated manufacturing solutions to the global pharmaceutical and nutraceutical industries, is delighted to launch its new Smart Coater X.ONE series, the company’s fastest tablet coater to date.The Smart Coater X.ONE has been designed to make tablet coating extremely fast, with an extra emphasis on process speed, efficiency and operator ease. Its advanced baffle design ensures the quickest process times for batches from 10-100%.Features of the new coater include a unique airflow pattern for optimized drying, a fully-perforated coating drum, closed dust-free charging, integrated discharge baffles, temperature sensor, a high-performing spray-arm and a 2.0 spray nozzle which has been developed with an anti-bearding cap. It also incorporates ACG’s exclusive X•ONE command and control system, designed to facilitate compliance with cGMP standards. Richard Stedman, CEO at ACG Engineering, said: “Our Smart Coater machines are already renowned for their innovative features and operator friendly designs. Now, after a lengthy period of development, we are excited to announce the launch of the X.ONE series.“Our quality-commitment philosophy means that the new machine has been crafted to achieve maximimum efficiency and flexibility for superior tablet coating, across every process – from charging to coating, discharging to cleaning. Each and every cycle is now swifter, more streamlined and profitable.“The fast tablet coater to date is already garnering real interest, and we look forward to continuing to showcase it capabilities at the upcoming CPhI event in Barcelona at the end of the month.” (XXX – may want to adapt this sentence, to reflect true accuracy)-Ends-About ACGFor over 60 years, ACG has been innovating the production solutions for pharmaceutical and nutraceutical companies, that help make people better.As the world’s most integrated provider of oral dosage products and services, we produce capsules, barrier packaging materials, manufacturing machinery, and visual inspection and traceability solutions. All fully compliant with international standards.Today, ACG fosters long-term collaborative partnerships with customers in 138 countries across six continents. Together, we share a common purpose: to solve the world’s greatest health challenges and make it better for everybody we serve.For more information, please contact the ACG media relations team:madhurima.chakraborty@acg-world.com
Read more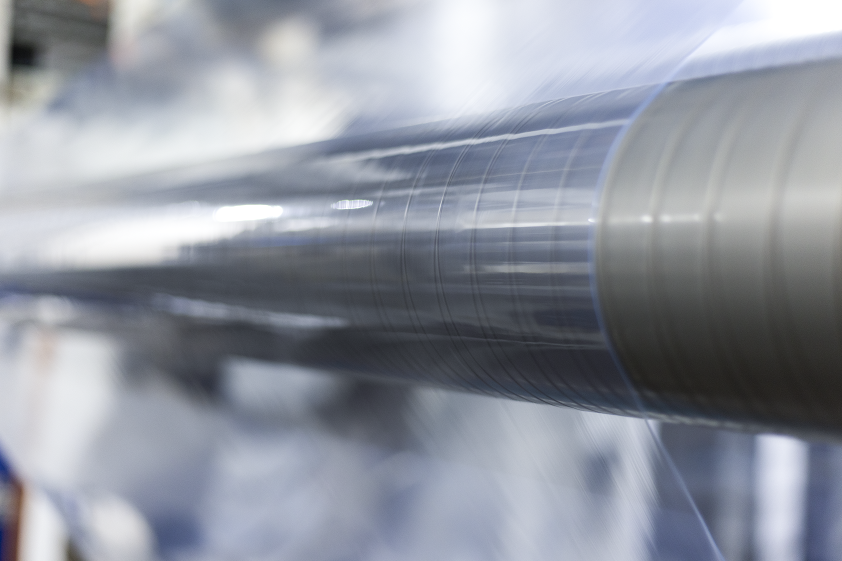
ACG acquires Technical Aluminium Foil Company
Further underpinning business growth across the Middle Eastern and African marketsACG announces full shareholding ownership of Technical Aluminium Foil Company (TAFC). This strategic move further solidifies ACG's growth trajectory across the Middle Eastern and African markets.As the world's only integrated pharma manufacturing solutions company, ACG offers a diverse range of products including capsules, films, foils, engineering equipment and inspection systems. The addition of TAFC, a prominent aluminium foil packaging company based in the UAE, strengthens ACG's position as a leading provider of comprehensive packaging solutions.TAFC boasts over a decade of experience serving the pharmaceutical and food industries with its extensive range of aluminium and specialty packaging foils renowned for their exceptional high barrier properties. The company's expertise in lacquering, lamination, printing and slitting further enhances ACG’s capabilities in meeting the diverse packaging needs of its clients.This acquisition represents ACG Group's inaugural venture in the Middle East, following recent successful acquisitions of ComboCap and AquaCap in the Americas. TAFC seamlessly aligns with ACG Films and Foils' existing business operations, enabling both entities to harness their collective strengths and expertise for accelerated growth.Shivshankar S.R., CEO at ACG Films & Foils, said: “We are excited to be making our first acquisition in the UAE. This strategic collaboration will further support our work in bringing innovative and high-quality packaging products to market, while reducing lead times and improving service levels.“By joining forces, the companies will be able to leverage their combined strengths and expertise to propel the business forward in the Middle Eastern and African markets.”-Ends-About ACGIn accordance with its commitment to making the world healthier, ACG has been delivering exceptional solutions to the global pharmaceutical and nutraceutical industry for sixty years, across six continents and in a hundred countries.Collaboration is at the core of ACG’s ethos. ACG is the world’s only integrated pharma manufacturing solutions company, with products ranging from capsules to films & foils, to engineering equipment and inspection systems – all that meet international regulatory requirements. For ACG, it’s always about finding innovative solutions to the world’s greatest health challenges, together.For more information, please contact the ACG media relations team:madhurima.chakraborty@acg-world.com
Read more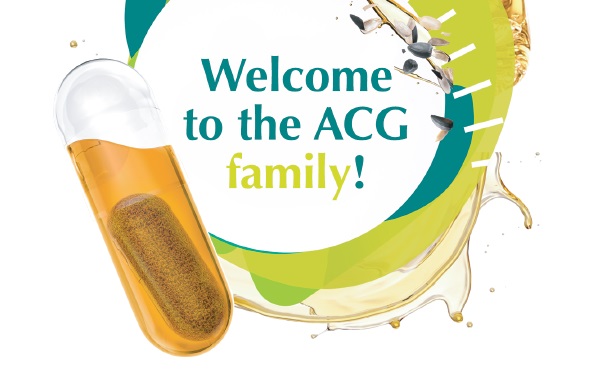
Vantage Nutrition LLC acquires ComboCap Inc
This acquisition positions Vantage Nutrition as the only company in the world supplying Sidebysideä health products to nutritional and pharmaceutical markets, for enhanced combinations.Vantage Nutrition, an ACG group company announces full shareholding ownership of ComboCap Inc (USA) and BioCap (South Africa).ComboCap is renowned for the invention and commercialization of its Sidebyside technology, the world’s first three-piece capsule health product that contains an internal divider, enabling wet and dry ingredients to be brought to market side by side, separated-but-together. Backed by 80 international patent awards ComboCap has been supplying nutritional brand customers with unique finished product solutions out of its cutting-edge cGMP plant in NJ, USA. This acquisition marks a significant milestone for Vantage Nutrition and ACG, as it further expands its technology and customer solutions footprint in North America and around the world.ACG is the world’s largest integrated supplier of pharmaceutical and nutraceutical solid dosage products and services. Vantage Nutrition, an ACG group company, already has an excellent reputation as an innovator of liquid filled capsule solutions. ComboCap marks Vantage Nutrition’s second US investment in less than a year, and first in S.A, after Philadelphia-based ‘AquaCap’ was acquired from Nestlé S.A. With this expansion of manufacturing capabilities and patented technology, along with the commitment to delivering integrated solutions and cutting-edge technology, Vantage Nutrition aims to provide the most comprehensive and advanced multiphase solutions to customers globally.Karan Singh, Managing Director at ACG, said, "As one of world’s largest producers of empty hard-shell capsules, at ACG we have often thought, what next? Strengthening our portfolio of most comprehensive vegetarian and gelatin capsules, in every imaginable size, I am thrilled to announce the acquisition of ComboCap Inc and BioCap. We now will hold the patented design and specialized equipment used inproducing the world’s first 2-in-1 capsule product with a movable membrane, becoming the sole proprietor of this technology globally.With our partners, we will usher a new era in new combinations of dietary supplements, and even non-prescription or over-the counter (OTC) remedies as well as prescription (Rx) medicines to be delivered in a single dose. This technological breakthrough is a solution to current formulation challenges with many combination therapies, including incompatible ingredients or molecules. Capsules are arguably the safest and most reliable way to deliver medicine and we at ACG strive to make it better.”Tobie Louw, a Founder and CEO of ComboCap Inc, said: “Vantage Nutrition is the perfect partner for our business, and we are very excited to be part of the ACG family. We share a passion for innovation and the commitment to bring nutraceutical and pharmaceutical customers the best possible solutions and services. By joining forces and leveraging our collective capabilities we’ll no doubt bring Sidebysideä to nutraceutical and pharmaceutical markets the world over.”-Ends-About Vantage NutritionVantage Nutrition, part of the ACG Group, is one of the world’s largest and most respected manufacturer of hard-shell liquid-fill capsule solutions. As a strategic consultancy and manufacturing partner in the nutraceutical space, Vantage Nutrition helps clients bring high-quality and innovative products to market, fast. About ACGIn accordance with its commitment to making the world healthier, ACG has been delivering exceptional solutions to the global pharmaceutical and nutraceutical industry for sixty years, across six continents and in a hundred countries.Collaboration is at the core of ACG’s ethos. ACG is the world’s only integrated pharma manufacturing solutions company, with products ranging from capsules to films & foils, to engineering equipment and inspection systems – all that meet international regulatory requirements. For ACG, it’s always about finding innovative solutions to the world’s greatest health challenges, together.For more information, please contact the ACG media relations team:madhurima.chakraborty@acg-world.com
Read more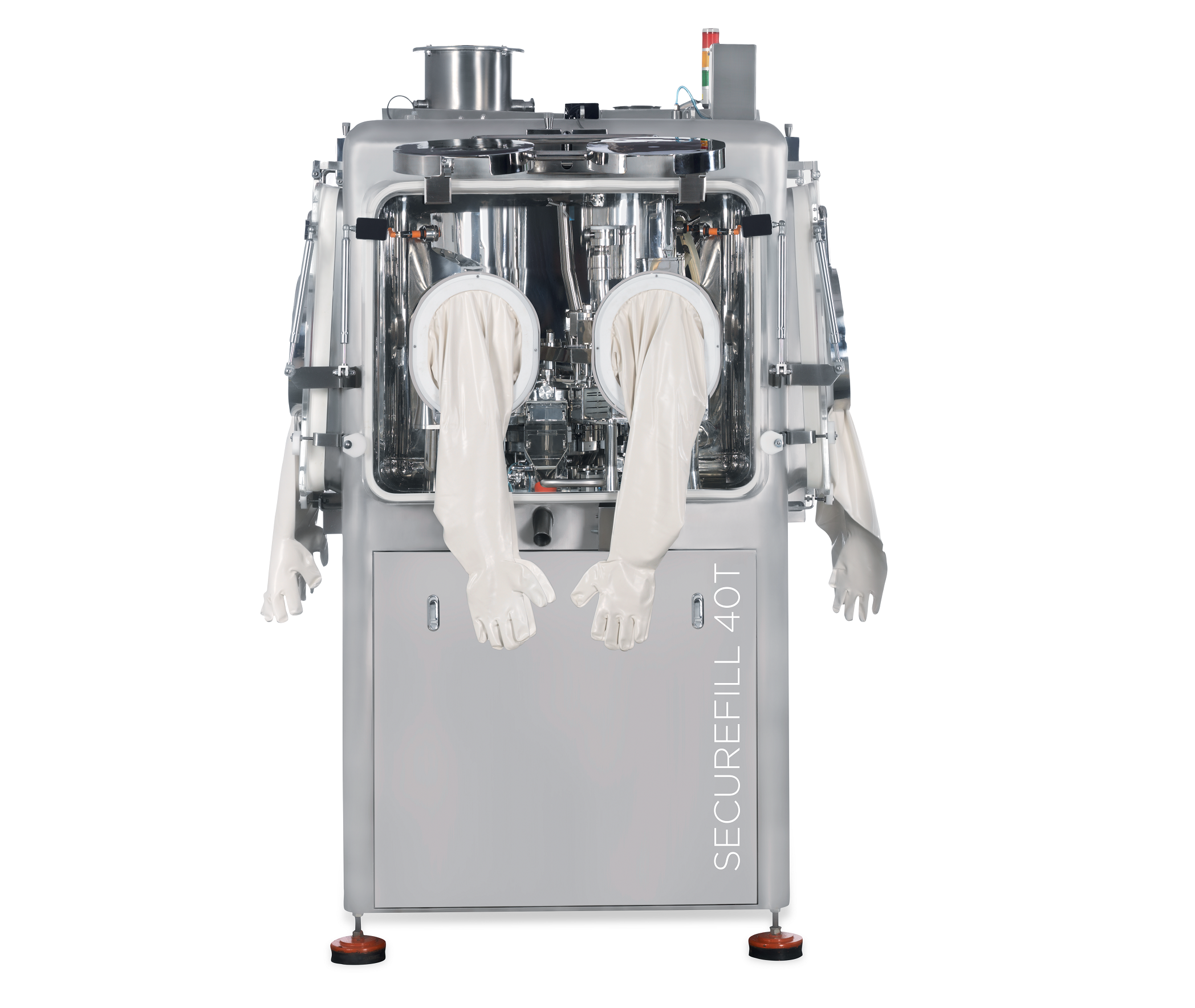
ACG Engineering – SECUREFILL 40T
Tablets & CapsulesCapsule Filling Equipment & Supplies (February 2023)ACG Engineering – SECUREFILL 40TThe Securefill series is ACG’s high-level containment capsule-filling machine range. Designed for filling capsules with highly potent and/or toxic drugs, the machines comply with occupational exposure band (OEB) up to level 4.Built with operator safety in mind, these machines are equipped for filling capsules with oncological, biopharmaceutical, antiviral formulations, and other such highly potent active pharmaceutical ingredients (HPAPIs).Features:• SS316L monoblock structure containing HEPA filters, a rapid transfer port (RTP), glove ports, and accurate dosing mechanisms maintained in a negative pressure environment.• Provision for contained charging and discharging.• Wet-in-place system to ensure wetting of all suspended particles in the pharma zone.• Can be integrated with check-weighers, metal detectors and de-dusters under containment conditions.Benefits:• Ensures complete containment, thereby avoiding operator contact within OEL range 1-10µg/m3.• Integrated containment philosophy for upstream and downstream processes.• Enables easy cleaning.• Supports the production of life-saving drugs that contain HPAPIs.Technical specifications: SECUREFILL 40T Capsule size 00 - 5 Maximum speed 40,000 capsules/hour OEL 1-10µg/m3About ACGIn accordance with its commitment to making the world healthier, ACG has been delivering exceptional solutions to the global pharmaceutical and nutraceutical industry for sixty years, across six continents and in a hundred countries.Collaboration is at the core of ACG’s ethos. ACG is the world’s only integrated pharma manufacturing solutions company, with products ranging from capsules to films & foils, to engineering equipment and inspection systems – all that meet international regulatory requirements. For ACG, it’s always about finding innovative solutions to the world’s greatest health challenges, together.For more information, please contact the ACG media relations team:madhurima.chakraborty@acg-world.com
Read more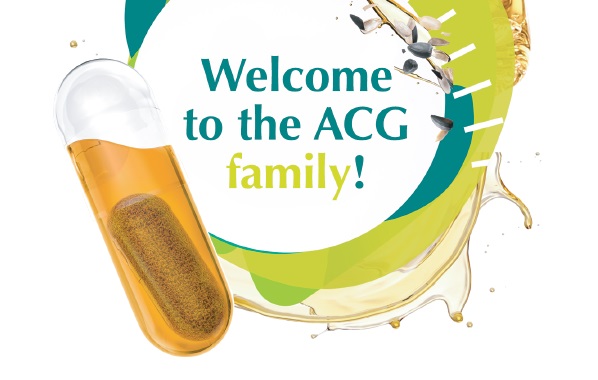
Vantage Nutrition LLC acquires Aquacaps from Nestlé Health Science
Vantage Nutrition’s innovative nutraceutical offering expands into North America.. Vantage Nutrition, an ACG Group company, announced on 1st December 2022 that it has acquired Philadelphia-based ‘Aquacaps’ – an asset of Nestlé Health Science. Aquacaps is a leading contract manufacturer of liquid-filled capsules within the nutritional supplement industry in the United States. Its novel liquid delivery technology allows for the liquid filling of hard gelatin and vegetarian capsules. ACG is the world’s largest integrated supplier of pharmaceutical and nutraceutical products and services. Vantage Nutrition, an ACG group company, already has an excellent reputation as an innovator of two-piece liquid fill capsule solutions. The company’s mission is to be the most efficient partner in delivering innovative and high-quality nutraceutical products to customers globally. Karan Singh, Managing Director of ACG, said: “Although ACG has been established in North America for the last 20 years, this marks our first acquisition in the territory and is a key next step in our global expansion strategy. With this increase in our footprint and manufacturing capabilities, coupled with Vantage’s innovative technologies and 360-degree service offering, we aim to provide the most advanced combination liquid-fill solutions for customers across the region.” About VantageVantage Nutrition, part of the ACG Group, is one of the world’s largest and most respected manufacturer of hard-shell liquid-fill capsule solutions. As a strategic consultancy and manufacturing partner in the nutraceutical space, Vantage helps clients bring high-quality and innovative products to market, fast. About ACGIn accordance with its commitment to making the world healthier, ACG has been delivering exceptional solutions to the global pharmaceutical and nutraceutical industry for sixty years, across six continents and in a hundred countries.Collaboration is at the core of ACG’s ethos. ACG is the world’s only integrated pharma manufacturing solutions company, with products ranging from capsules to films & foils, to engineering equipment and inspection systems – all that meet international regulatory requirements. For ACG, it’s always about finding innovative solutions to the world’s greatest health challenges, together.For more information, please contact the ACG media relations team:madhurima.chakraborty@acg-world.com
Read more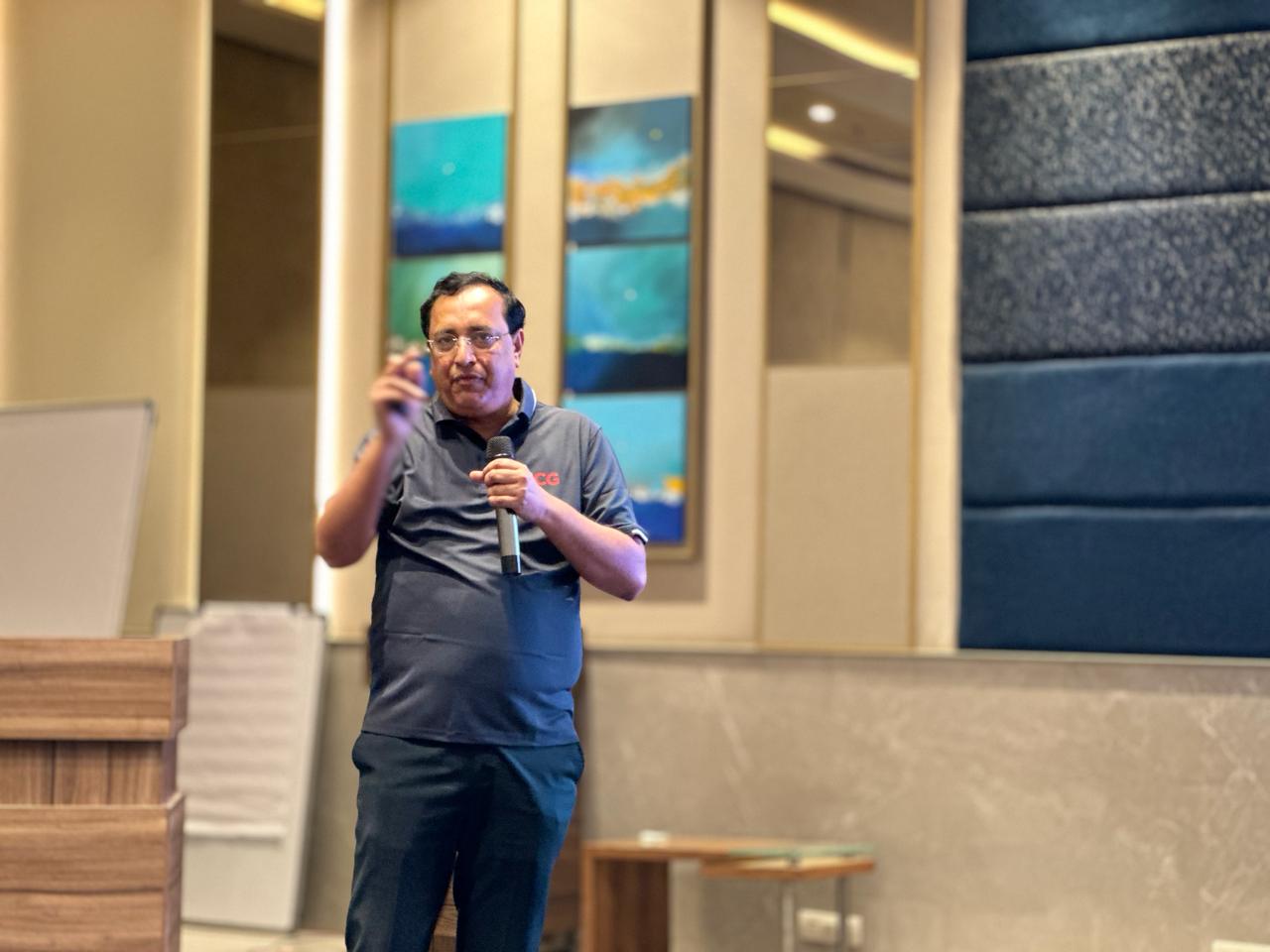
ACG appoints Shankar Gupta as Chief Sales Officer Industry authority to re-join business in a newly created role
ACG, the world’s largest integrated pharmaceutical and nutraceutical manufacturing solutions provider, is delighted to announce that Shankar Gupta will be re-joining the business in the newly created role of Chief Sales Officer.In his new role, Shankar will be responsible for driving sales across all four ACG divisions (Films and Foils, Capsules, Inspection and Engineering) in order to continue building the company’s ‘One ACG’ agenda. Essentially, this will involve bringing further uniformity to ACG's customer outreach processes, creating more integrated solutions, and ultimately providing a consistent brand experience to ACG’s global customers, regardless of business division or location. He will also focus on scaling new initiatives.Shankar will report directly into the managing director, Karan Singh, who comments:"I am so pleased that Shankar Gupta has decided to rejoin the business during this exciting time. His understanding of ACG and its deliverables, and deep insight into our customers’ businesses will help us to align ourselves better to their changing needs. More importantly, he will champion and support better collaboration and partnership with customers.“Shankar will be pivotal in calibrating and aligning our business units to our goal of ‘Making it Better’, and our belief that everyone deserves access to good medicine."Shankar Gupta adds: “I am excited to use my experience in the pharmaceutical industry to augment ACG's growth by aligning the organisation to the changing dynamics of the global healthcare Industry.“It will certainly call for a huge collaboration of efforts both internally and with our customers, but will ultimately lead to a richer, deeper and more numerous partnerships.”-Ends-About ACGIn accordance with its commitment to making the world healthier, ACG has been delivering exceptional solutions to the global pharmaceutical and nutraceutical industry for sixty years, across six continents and in a hundred countries.Collaboration is at the core of ACG’s ethos. ACG is the world’s only integrated pharma manufacturing solutions company, with products ranging from capsules to films & foils, to engineering equipment and inspection systems – all that meet international regulatory requirements. For ACG, it’s always about finding innovative solutions to the world’s greatest health challenges, together.For more information, please contact the ACG media relations team:madhurima.chakraborty@acg-world.com
Read more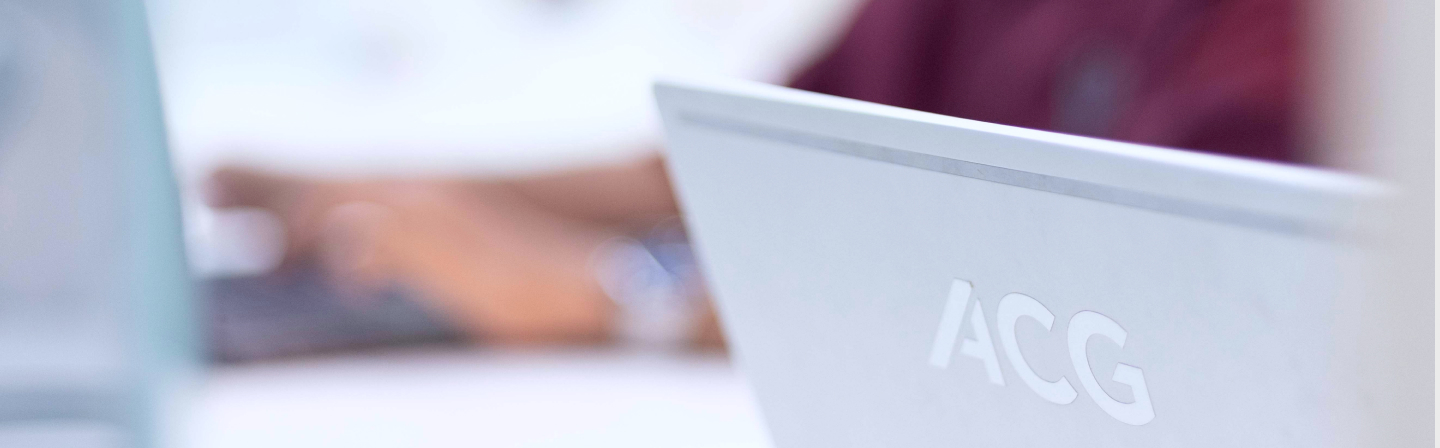
ACG to Launch German Process Laboratory in 2023
Following the success of its first-to-market laboratory for process development in India, ACG (the world’s biggest integrated pharmaceutical and nutraceutical manufacturing solutions provider) is now also committed to launching a sister process lab in Germany in 2023.This new process development laboratory will be located at ACG’s XERTECS GmbH site in Mulheim in the South West of Germany, with the first phase occupying approximately 250 square metres. ACG’s staffing recruitment plan for the lab will be to attract top academic talent from local universities, as well as trained and experienced process engineers, pharmacists and lab technicians.The aim of ACG’s new laboratory will remain consistent with the first – to provide customers and partners access to the latest knowledge, skills and equipment to collaboratively keep pushing the boundaries of all aspects of process development. So customers can test solid dosage optimisation limits, for example, and co-create alongside ACG’s team of experts to develop new process solutions.The extensive range of available equipment covers areas including feasibility studies, research and development work, pilot-scaling, and tailored in-house technical training courses. Customers also get to experience and test products from ACG’s portfolio and gain operational and maintenance training on premise.Dr Marcus Michel, CEO of ACG Engineering, explains: “ACG’s process labs reinforce our commitment to ‘making it better’. Requested by the Indian market, our first lab has enabled customers to build their competencies and capabilities, as well as to scale up – with many of these customers now operating at high capacity and efficiency. Our plan is simply to replicate this model in the European market, and we are working at full speed to ensure the launch of our new facility in 2023.“The lab in India is home to some of the smartest and finest technologies in powder processing, and is fully equipped for all aspects of granulation, drying, tablet compression and coating. Many of our machines are unique because they have been built or modified in direct response to our customers’ needs – helping them on their manufacturing journey.”About ACGIn accordance with its commitment to making the world healthier, ACG has been delivering exceptional solutions to the global pharmaceutical and nutraceutical industry for over sixty years, across six continents and in a hundred countries.Collaboration is at the core of ACG’s ethos, and ACG is the world’s only fully integrated pharma manufacturing solutions company, with products ranging from capsules to films & foils, to engineering equipment and inspection systems – all that meet international regulatory requirements. For ACG, it’s always about finding innovative solutions to the world’s greatest health challenges, together.For more information, please contact the ACG media relations team:madhurima.chakraborty@acg-world.com
Read more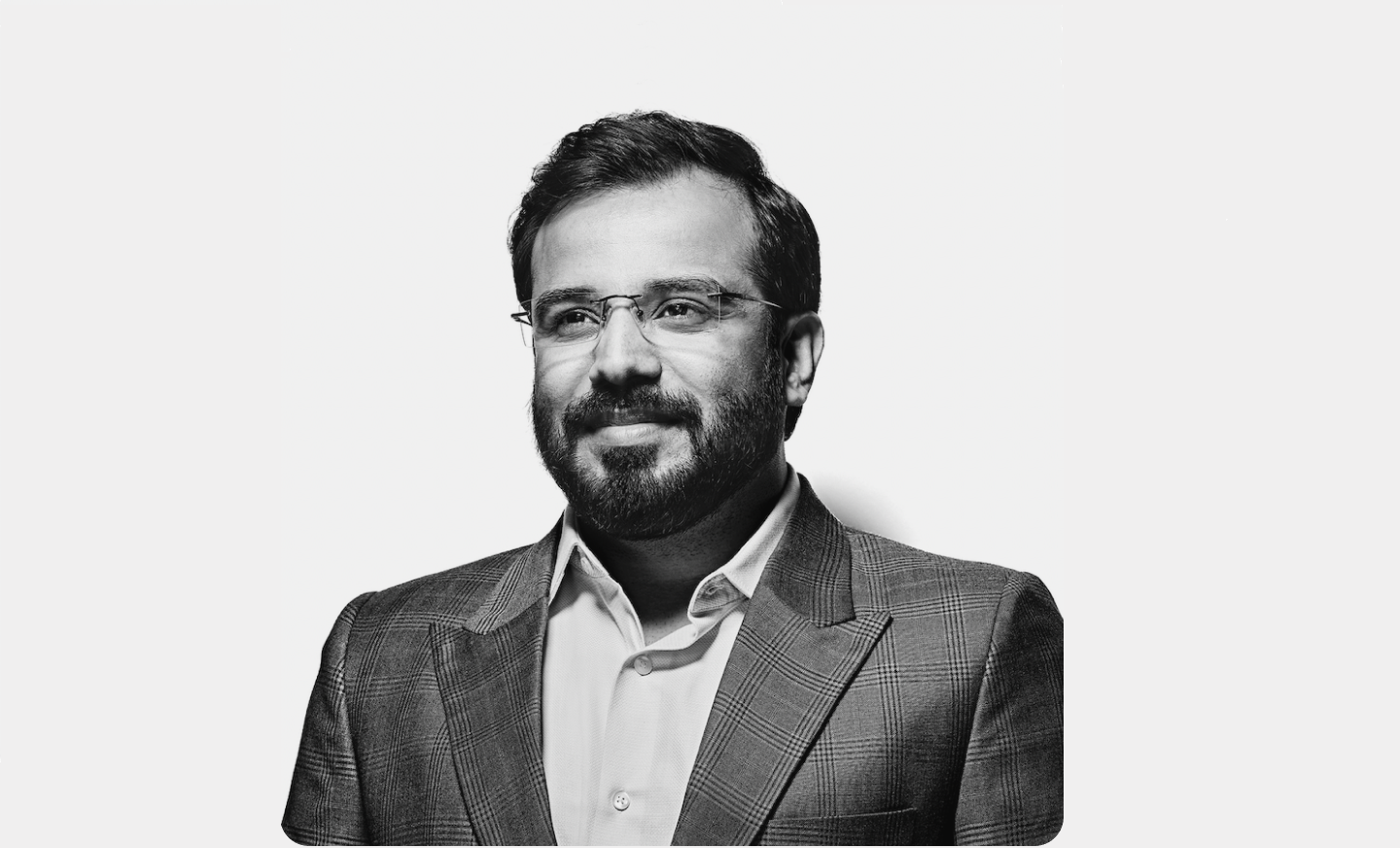
ACG appoints Udit K Singh as CEO of ACG Inspection
ACG, a leading supplier of fully integrated manufacturing solutions to the global pharmaceutical and nutraceutical industry, is pleased to announce the appointment of Mr. Udit K Singh as the new chief executive officer (CEO) of its Inspection Division.Mr. Singh will be supporting the company as it continues its growth and global expansion. He will be responsible for ensuring that every dose of medication that ACG Inspection’s pharmaceutical and nutraceutical partners provide is manufactured and delivered exactly as intended. That is down to the fact that ACG’s visual inspection systems track and monitor the manufacturing lines to guarantee flawless, safe products.Karan Singh, managing director, ACG said: “ACG is focused on building a diverse, world-class team by hiring top international talent. We are delighted to welcome Udit Singh to ACG Inspections. He has had an illustrious career and brings diverse and unique capabilities, including a robust understanding of the pharmaceutical sector.“The team looks forward to tapping into his deep experience to enrich our global work towards making the world safer and healthier. With his knowledge and expertise in this field, Udit Singh is sure to take ACG Inspection to newer heights.”Mr. Singh added, “I am pleased to join ACG and will work to ensure that our advanced serialisation, aggregation and anti-counterfeiting solutions track and protect medicines all the way through the supply chain, and into the hands of those who need them.“We are investing substantially to ensure our track and trace platform performs seamlessly and complies with regulatory requirements all over the world. I look forward to playing an integral role, and contributing towards the continued development, working with a world-class team.”About ACGIn accordance with its commitment to making the world healthier, ACG has been delivering exceptional solutions to the global pharmaceutical and nutraceutical industry for almost sixty years, across six continents and in a hundred countries.Collaboration is at the core of ACG’s ethos, and ACG is the world’s only integrated pharma manufacturing solutions company, with products ranging from capsules to films & foils, to engineering equipment and inspection systems – all that meet international regulatory requirements. For ACG, it’s always about finding innovative solutions to the world’s greatest health challenges, together.For more information, please contact the ACG media relations team:madhurima.chakraborty@acg-world.com
Read more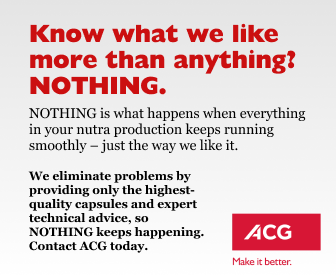
ACG Capsules launches campaign to promote problem-free pharmaceutical production
-One of the world’s largest producers of empty hard-shell capsules is on a mission to‘Love NOTHING’ when it comes to zero-problem productionACG, one of the world’s largest producers of empty hard-shell capsules, has launched its global pharmaceutical campaign: ‘ACG loves NOTHING’. The campaign is aimed at significantly improving pharmaceutical production through collaboration and industry-leading innovation. With a host of value-added services on offer, ACG has taken a pledge to strive for zero-problem pharmaceutical and nutraceutical manufacturing.Alex Robertson, CMO at ACG, said: “The messaging at the centre of this campaign is: ‘ACG loves NOTHING’ – we are putting every effort towards zero-problem production. That’s because when ‘nothing’ happens during pharmaceutical and nutraceutical production, everything runs reliably, and our customers can get the products they make to the people who need them. We will achieve this by providing the highest quality empty capsules and all the holistic advice and expertise required for seamless operations.”Founded 60 years ago, ACG was created on the simple principle of ‘Make it Better’. As the world’s largest integrated supplier of solid dosage pharmaceutical and nutraceutical products, and with the most comprehensive ranges of vegetarian and gelatin capsules globally, ACG has the scale and range to have a far-reaching impact on pharmaceutical production and human health.Selwyn Noronha, CEO ACG Capsules, added: “The pharmaceutical sector is regulated and highly competitive. Companies operating within it need a diverse range of quality capsules that help them stand out from the crowd, while also meeting demands for clean and natural products.“Beyond exceptional products, these companies need expertise and a lifetime of targeted support to ensure efficient manufacturing and guarantee regulatory compliance. With proficiency in all aspects of manufacturing from capsules to machines and protective barriers, for the last 60 years ACG has been the only company to offer this level of support, and it continues with this focus at the heart of operations.”So, at ACG, there really is something about NOTHING. The company is on a mission to drive towards problem free production and collaborating with its customers to collectively deliver on its mission of creating a healthier world.About ACGIn accordance with its commitment to making the world healthier, ACG has now been delivering exceptional solutions to the global pharmaceutical and nutraceutical industry for 60 years, across six continents and in 138 countries.‘Collaboration’ is at the core of ACG’s ethos, and ACG is the world’s only integrated pharma manufacturing solutions company, with products ranging from capsules to films & foils, to engineering equipment, and inspection systems – all that meet international regulatory requirements.For ACG, it’s always about finding innovative solutions to the world’s greatest health challenges, together.For more information, please contact the ACG media relations team:madhurima.chakraborty@acg-world.com
Read more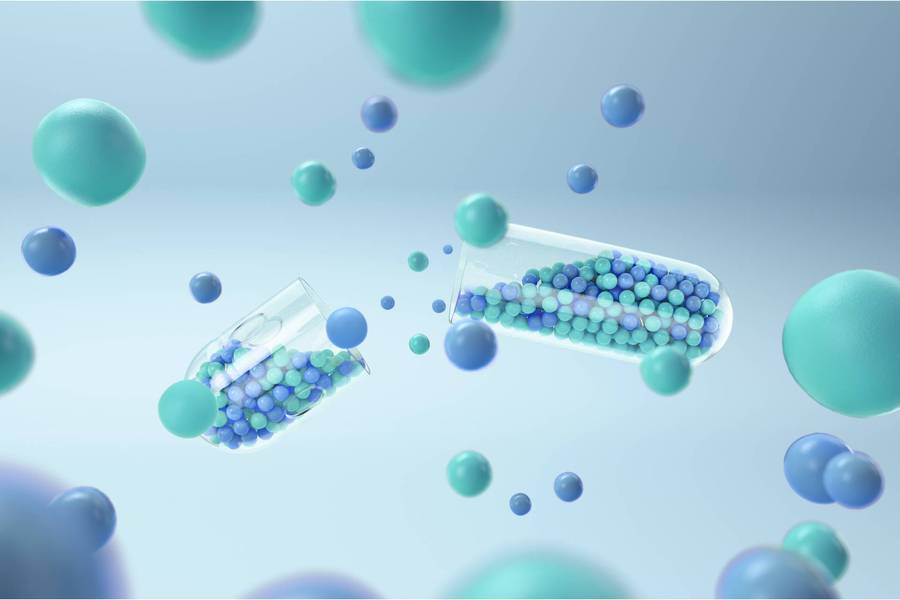
Ingredient Processing: The Way Forward for Nutraceutical Products
Ingredient Processing: The Way Forward for Nutraceutical Products
This shift in focus has given rise to the dynamic and rapidly growing nutraceuticals sector. Nutraceuticals are products derived from natural food sources that offer health benefits beyond basic nutrition. They include supplements, functional foods, and beverages designed to improve overall health, prevent chronic diseases, and enhance performance.As this segment continues to expand, nutraceuticals are becoming a crucial part of modern health and wellness, empowering individuals to take control of their health with targeted, natural solutions. Whether for supplements designed for immunity, heart health or cognitive function, consumers are increasingly seeking out products that align with their unique wellness goals. As such, the global nutraceutical market has seen remarkable growth, valued at $383.69 billion in 2022 and expected to surge to $868.38 billion by 2031. This growth reflects a strong compound annual growth rate of 9.50% from 2024 to 2031.Furthermore, advancements in nutraceutical formulations have led to the development of more innovative and effective products. These advanced products are designed to meet the growing demand for natural, scientifically backed solutions, which promote long-term health and vitality. Innovations in nutraceuticals have the potential to significantly impact the industry, but success hinges on manufacturers' ability to incorporate high-quality, stable and effective ingredients into products. To accomplish this, manufacturers must meticulously select ingredients and fine-tune processing techniques.The Need for Careful Ingredient SelectionOne of the fastest-growing areas within the nutraceutical market is functional foods, which are enhanced with additional nutrients or bioactive ingredients that offer more than basic nutrition. Functional foods, such as those fortified with vitamins, minerals, probiotics, prebiotics, fiber and Omega-3 fatty acids are gaining popularity with consumers seeking to improve their overall health and well-being through better nutrition.Alongside functional foods, dietary supplements are also experiencing rapid growth within the nutraceutical sector. These supplements are carefully formulated to address specific health concerns, such as boosting immune function, supporting digestion or enhancing cognitive performance. Whether in the form of capsules, powders, or liquids, these supplements provide a convenient way for consumers to fill nutritional gaps and achieve specific health goals, further driving the growth of the market.However, the success of both segments hinges on the careful selection of active ingredients and processing methods. The effectiveness and safety of these products are directly impacted by the quality of the components used and the formulation strategies applied. Manufacturers must meticulously select ingredients and fine-tune processing techniques in order to maintain the desirability and efficacy of the final product.To stay aligned with current trends, manufacturers are adopting advanced techniques such as coating, fluid bed processing, encapsulation, pelletization, spray drying and freeze-drying. This drive for innovation is closely linked to progress in nutraceutical ingredient processing technologies, which have become valuable assets for manufacturers seeking to enhance product quality and effectiveness.Transforming Ingredients with Advanced ProcessingIngredient processing is one of the promising and cost effective approaches helping to meet current market demands. It is a method of conversion of raw materials into value-added products that can be used as a starting product for development or as an end product. The primary objective of this process is to produce high-quality, stable and effective ingredients that can be incorporated into products to promote health and wellness.The process involves state-of-the-art techniques such as encapsulation, coating, granulation and mixing, which are used to strategically modify the physical and chemical properties of active ingredients. This transformation optimizes their functionality, boosting both the nutritional value and the overall benefits of nutraceutical products. The result is a higher standard of excellence and performance to help meet stringent industry demands.One of the key advantages of ingredient processing is its flexibility as a tool to customize products based on specific customer preferences and formulation needs. Whether enhancing product stability, improving bioavailability, or masking undesirable tastes or odors, processing technologies offer the ability to tailor products for various health and dietary applications. From aiding the manufacturing process to enabling product modifications, ingredient processing has become a vital tool in the development of high-quality nutraceuticals.Addressing Manufacturing ChallengesOne significant challenge in manufacturing, particularly when handling powdered ingredients, is the issue of dusting. This not only does it create a less efficient production process but it also leads to material wastage. Ingredient processing technology addresses this by transforming powders into microbeadlets or minibeadlets, improving the flowability of the material, reducing dust and minimizing wastage. This enhancement not only streamlines production but also ensures a more precise and consistent formulation.Another major challenge in the nutraceutical industry is the delivery of unstable liquid ingredients, extracts and oleoresins — many of which are botanically derived and unsuitable for direct use after extraction. Advanced ingredient processing technologies offer a practical solution by converting these unstable or incompatible liquid actives into stable solid forms, such as powders, pellets or beadlets. This transformation simplifies handling and delivery, while also enhancing the product’s effectiveness by ensuring better stability, shelf life and ease of use.Natural raw materials are often unstable and can degrade over time. Techniques like coating and encapsulation help stabilize these active compounds, extending their shelf life and preserving their potency throughout the product’s lifespan. Additionally, processes such as microencapsulation, nanoencapsulation and emulsification enhance the bioavailability of ingredients that are otherwise poorly absorbed, improving their absorption and effectiveness. Some nutraceutical ingredients also have strong tastes or odors that can negatively impact the consumer experience. Processing methods can mask these unwanted characteristics, making the final product more pleasant and user-friendly.Moreover, ingredient processing offers the added advantage of customizing formulations. Technologies such as blending and extrusion enable the creation of tailored products that meet specific formulation needs. By optimizing the delivery of active ingredients, these methods enhance the overall performance of products, ensuring that ingredients are utilized in a way that maximizes their impact.This approach is particularly valuable in the fortification process, where additional nutrients are integrated into products, for example: enriching protein powders with B vitamins or incorporating calcium into multivitamin blends, iodine in salt or iron in wheat and maize flour etc. This process significantly boosts the nutritional value of both nutraceuticals and food products, making them more effective in meeting dietary needs and improving public health. Also, techniques like beadlet formation further enhance this process by improving ingredient stability and controlling the release of active compounds. For instance, in Omega-3 supplements, beadlets can increase bioavailability, ensuring the body absorbs more of the active ingredient.The Evolving Nutraceutical LandscapeInnovations in nutraceuticals have the potential to significantly impact the industry, and ingredient processing plays a crucial role in this evolution. This sustainable and eco-friendly approach to raw material and final product handling is becoming increasingly important in the formulation of many products.Advancements in ingredient processing technologies are driving the development of innovative products that stand out in the market. Companies that invest in these technologies are better positioned to offer unique and high-quality products, attracting customers and maintaining a competitive edge. By leveraging these advanced technologies, the nutraceutical industry can produce products that not only meet specific health needs and consumer preferences but also satisfy the formulation need. Products formulated using these methods often achieve higher levels of purity, safety and efficacy, as required by regulatory bodies enhancing the overall quality and credibility of the brand.Ingredient processing is not just a functional necessity — it is a strategic asset for creating nutraceutical products that stand out in the market. By investing in advanced processing technologies, manufacturers can deliver safe, effective and tailored products that satisfy both regulatory standards and consumer expectations, thereby strengthening their brand and competitive edge. Author DetailsManali Dalvi, Lead, Formulation R&D, ACGManali Dalvi’s primary responsibilities include writing and publishing scientific research articles, developing segmented solutions and technical content as part of thought leadership programs. She is also involved in all the industry and institutional related collaborations and research activities. Dalvi received a Master’s in Pharmacy from Savitribai Phule Pune University.Jnanadeva Bhat, Ph.D., Vice President and Head, Formulation R&D, ACGJnanadeva Bhat is head of formulation R&D (Pharma & Nutra) at ACG Group. Bhat has been associated with the pharmaceutical industry for more than two and a half decades. As a product formulator, he has worked on various dosage forms that include tablets, soft gelatin and hard capsules, injectables and lyophilized formulations. At ACG, he heads the formulation R&D lab where he primarily leads new product development projects and customer interface.Surya Singh, Ph.D., Senior Manager Product Development (Nutra), ACGSurya Singh is part is a key member of Vantage Nutrition LLP, where he spearheads formulation development for the nutraceutical division. With over 15 years of experience in capsule formulation, Dr. Singh specializes in liquid-fi ll and pellet-fi ll technologies, bringing expertise in creating innovative, high-value nutraceutical products. His leadership drives the development of cutting-edge solutions that meet the evolving needs of the market, positioning his team at the forefront of industry advancements.Publication DetailsThis article appeared in Tablets and Capsules Magazine:Vol. 23, No. 1January/February 2025Pages: 13-15Source: https://www.tabletscapsules.com/3641-Technical-Articles/617376-Ingredient-Processing-The-Way-Forward-for-Nutraceutical-Products/
Read more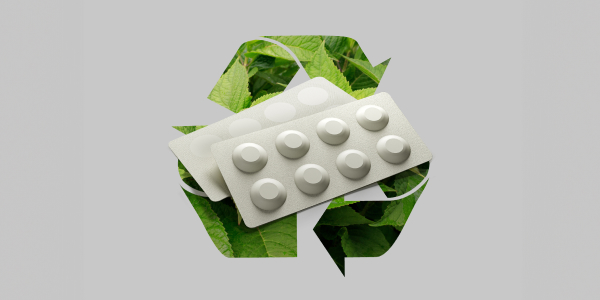
ACG to Showcase Sustainability Innovations at Pharmapack Europe 2025
ACG to Showcase Sustainability Innovations at Pharmapack Europe 2025
During Pharmapack Europe, ACG will be highlighting their CelluPod paper-based, recyclable, and compostable blister system for products that require low water vapor transmission rates (WVTR). The company is also featuring its packaging solutions that are free of polyvinyl chloride (PVC). These include its PVC and Halogen-Free Thermoforming Blister System for products requiring low to medium WVTR. ACG also provides an eco-friendly alternative in its Bio D PVC. The company’s Halogen-Free Cold Form Blister System also provides a high-performance sustainable solution without halogen and PVC.The company also announced its new head of Global Sales for ACG Packaging Materials, Jochen Scheil. With a background in mechanical engineering and more than 20 years of experience in large sales and service organizations in Europe, Asia Pacific, and the Middle East, Scheil previously held roles at Windmoeller & Hoelscher and Uhlmann Pac-Systeme."Joining ACG Packaging Materials at such a pivotal time is an incredible opportunity. I am thrilled to contribute to the company’s mission of driving innovative, sustainable packaging solutions globally,” said Scheil in the press release (1). With the launch of these products and our ongoing commitment to reducing emissions, ACG is setting a new standard for sustainability in the pharmaceutical industry.""We’re delighted to welcome Jochen to the team. His leadership and vast experience in pharmaceutical packaging, combined with the efforts of his team in showcasing our sustainable products and processes, will play a crucial role in advancing our European expansion,” said Sheikh Akbar Ali, general manager, Development and Technology of ACG Packaging Materials, in the release.At the Pharmapack event, ACG will also unveil its new state-of-the-art warehouse and slitting facility, which is located at its European site in Croatia.In October 2024, Pharmaceutical Technology EuropeTM sat down Anil Andrade, vice-president of Global Sales at ACG World, during CPHI Milan to discuss growth in demand in the pharma industry and efforts put forth to achieve sustainable operations. In the interview, Andrade talked about the changing perceptions of the industry and the importance of sustainability in pharmaceutical operations. During the past 10 to 15 years, ACG has seen global growth in demand, and more so in Europe, North America, and Asia. Andrade also emphasized efforts to achieve sustainability to reduce the impact on the environment (2).“Manufacturing capsules consumes a lot of water, and we have been trying to make our operations more efficient so that they consume less water, less paper, less plastic. In Croatia, as an example, we have reduced the paper consumption by almost 25 tons in a year. Same with plastic, we have reduced the consumption of plastic by 25 tons, and that has related to the benefits that we see going forward,” Andrade explained.Listen to the full interview with Andrade at https://www.pharmtech.com/view/cphi-milan-2024-growth-and-sustainability-in-the-pharma-industry.ReferencesACG. ACG to Showcase Sustainable Packaging Innovations at Pharmapack Paris 2025. Press Release. Jan. 20, 2025.Thomas, F. CPHI Milan 2024: Growth and Sustainability in the Pharma Industry. Oct. 18, 2024. https://www.pharmtech.com/view/cphi-milan-2024-growth-and-sustainability-in-the-pharma-industry Source: https://www.pharmtech.com/view/acg-to-showcase-sustainability-innovations-at-pharmapack-europe-2025
Read more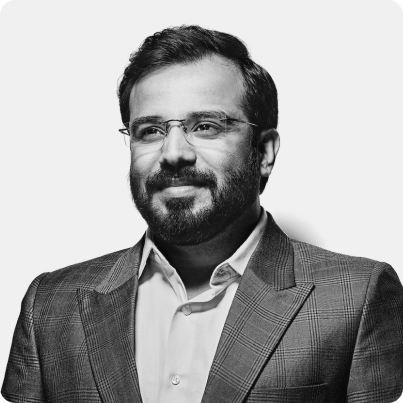
ACG covers every facet of the pharma process, all under one roof and seamlessly…
ACG covers every facet of the pharma process, all under one roof and seamlessly interconnected
ACG Inspection is launching its Life Sciences Cloud in India at the CPHI IndiaPMEC India show, which had its US launch at the Pack Expo US 2024. What has been the response to the US launch in terms of clients who are inquiring from clients or clients who have signed up?Existing clients who use our products across platforms were excited about ACG’s Life Sciences Cloud, as it represents a complete end-to end solution for their pharmaceutical supply chain needs. Our team has been busy engaging with clients in scenario-based demonstrations and discussing custom solutions to best fit their requirements. The feedback from existing clients has been overwhelmingly positive. New prospects are, naturally, evaluating it among competing options, comparing modules, and assessing the unique benefits we offer. We welcome their questions and are glad to engage in discussions that help them understand where we differ from others in the industry. After these in-depth discussions, we look forward to formalising partnerships with these new clients.What’s the upfront cost for a new customer or a new client (implementing this solution) versus an existing client? An existing client already has some parts of the solution and this life sciences cloud is the overlying layer which unites everything. Whereas a new customer might have bits and parts from different solution providers. Thus the interoperability between these different moving parts might be a concern. Also, how long does it take to train the staff to adapt to a new technology provider?I’ll address the transition first. We built this platform with flexibility and ease of integration in mind. For clients shifting from other providers, the Life Sciences Cloud is designed to integrate seamlessly, regardless of whether they currently use multiple vendors or a single provider. There’s no need for additional coding or customisation on the client’s end to fit into our platform.Regarding costs, aside from the recurring cloud subscription fees, we’ve structured the Life Sciences Cloud so that the cost of migration and integration is effectively zero. Our clients won’t bear any extra expenses for transitioning their systems, as we’ve designed the platform to support smooth interoperability with other systems on the floor.On the overall cost, we envision a flexible model that adapts to different client needs. For instance, the cost may be as low as per-serialnumber charges for regulatory reporting, or it could scale for broader uses like complete supply chain visibility, manufacturing analytics, and operator efficiency. Each client’s setup is unique, so costs are tailored according to the specific modules and integrations they require.As it’s an analytical and traceability solution, it would benefit a lot of pharma companies who are exporting. Is it compliant with the various supply chain regulations which are coming up like the Verification Router Service (VRS) in Drug Supply Chain Security Act in the US, etc?We’re deeply committed to regulatory compliance, with partnerships that keep us ahead of the curve. ACG collaborates closely with governing bodies, GS1 Global and similar regulatory bodies to ensure our systems meet international standards. We are the Gold Partner of GS1 Nigeria. These proactive engagements allow us to offer compliance solutions well before new regulations are mandated.Our participation with the Global Standard teams and the amount of deliberation that we do with them in terms of upcoming regulations, the amount of feedback we give, the amount of feedback they give (us) is way more advanced before the regulation actually hits the market before even it becomes a mandate.The cloud solution aims to deliver end-to-end supply chain traceability from raw material to end consumer, keeping the sanity of the integration and data exchange. This encompasses supporting global regulatory compliances, including the impending Drug Supply Chain Security Act (DSCSA) regulation.Many of our clients also use our systems to pilot new regulations, simulating production environments to understand and address potential challenges. Through these collaborations, we provide regulatory compliance deliverables early, allowing clients to validate their processes and prepare for real-world implementation.Who would be your client? Would it be a large pharma company? Would it be a midsize pharma company? A small one, which is scaling up? And a small company would have cost constraints. Can they approach ACG and expect a solution to help them scale up?ALSC gives global pharma companies the ability to visualise the entire manufacturing process on a very simplistic dashboard providing powerful insights enabling maximum OEE. Our modular technology caters to all types of pharma companies, from small-scale producers to major enterprises. Smaller companies can use selective modules, while larger organisations can leverage the full suite, integrating it across their entire supply chain. The system is also ideal for contract manufacturers (CMOs/CPOs), enabling smooth integration with diverse client systems and providing them with critical flexibility and cost efficiency.It has the range to cater to global pharma companies. When I say small, I’m talking about small in terms of volumes or small in terms of what they like to do with the L4 system in place. Vis-a-vis with big customers, big in terms of what they like to accomplish with L4 in terms of how many products they have, what the volume of the product is, how far along in the supply chain they want to track, how much regulatory reporting they want to do.What is ACG’s USP that you hope will draw customers to walk into your stall at PMEC India, and what are your expectations from the exhibition?We are one ACG. Our brand can be a bit of an enigma—are we a materials provider, a machinery manufacturer, or a technology provider? The answer is all of the above. As the pre-eminent integrated service provider of oral dosage, producing capsules, encapsulation, tabletting, barrier packaging materials, process manufacturing and packaging machinery, quality inspection systems and traceability solutions to the pharmacies of the world, ACG covers every facet of the pharmaceutical process, all under one roof and seamlessly interconnected. This unified ecosystem provides our clients with an unmatched return on investment, as they can avoid the fragmentation that often occurs when dealing with multiple vendors.ACG’s unique value lies in our holistic approach to the pharma industry, a journey that started 60 years ago with capsules and has since expanded to include everything from filling machines and packaging to advanced supply chain technology like the Life Sciences Cloud. At PMEC India, we’re excited to showcase new advancements in both machinery and technology. Our clients, many of whom are longstanding partners, will have the opportunity to explore the full capabilities of our Life Sciences Cloud, and we’re confident they’ll recognise its unique strengths over other solutions. Source: https://www.expresspharma.in/acg-covers-every-facet-of-the-pharma-process-all-under-one-roof-and-seamlessly-interconnected/
Read more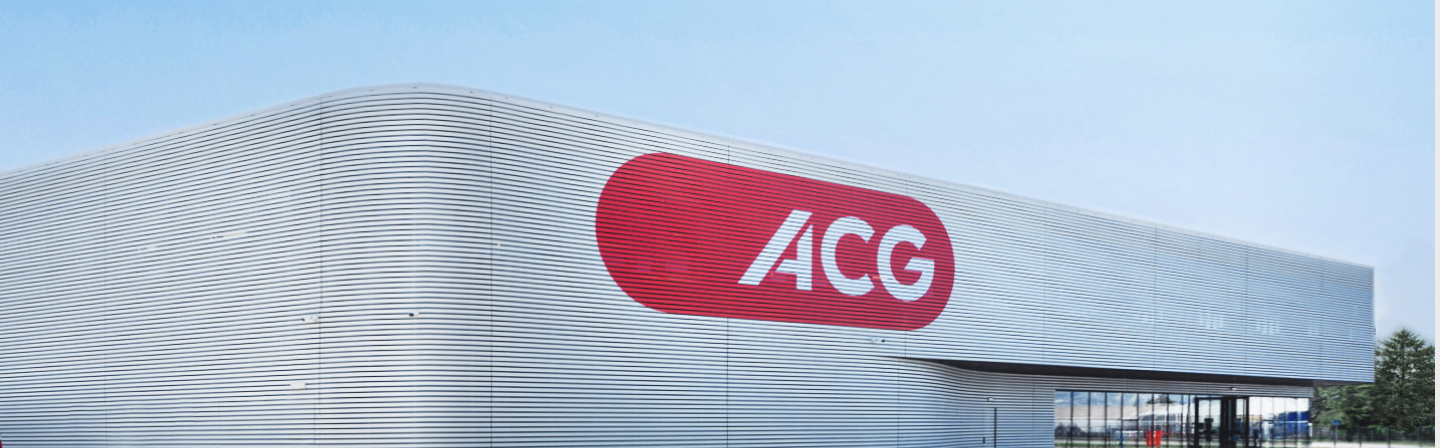
Q&A: ACG expands in Croatia - ACG speaks exclusively to European Pharmaceutical…
Q&A: ACG expands in Croatia - ACG speaks exclusively to European Pharmaceutical Manufacturer
1. With the expansion of capsule production capabilities at ACG's Croatian facility, how does this enhance the company's ability to meet global demand for oral solid dose capsules?The importance of increasing capacity at ACG's Croatian facilityACG's decision to expand its capsule manufacturing capacity at the Croatian facility comes at a critical time. This expansion is a consequence of our customer’s growing confidence in our supply from this plant and is designed to enhance the company's ability to meet the rising demand in Europe for high-quality empty hard capsules. By significantly increasing production capacity in Croatia, ACG is positioning itself as a reliable supplier to help mitigate supply chain disruptions and ensure a steady, high-quality supply of capsules for the pharmaceutical industry. This move not only strengthens ACG's position in the European market but is also an invitation to those customers who aspire to work with a progressive growing company that is investing and creating jobs locally in a region. ACG’s global expansion strategyRecognising that the Croatian facility alone cannot fully address the growing global need for empty hard capsules, ACG is taking proactive steps to expand its manufacturing capacity worldwide. The company is investing in facilities and production lines across multiple regions, ensuring that it can provide a reliable supply of capsules to markets around the globe. This expansion is critical to establishing a resilient, diversified supply chain that can withstand regional disruptions and provide pharmaceutical companies with the certainty they need to meet market demands.2. Is there a growing interest in advanced drug delivery systems?Multi-particulate formulations (MPFs) have garnered significant attention from product developers in recent years due to their superior benefits over traditional tablet formulations. These include improved drug release profiles, reduced risk of dose dumping, enhanced bioavailability, and flexibility in designing controlled release systems. As a result, MPFs are increasingly being adopted for advanced drug delivery systems, driving year-on-year growth in this area of pharmaceutical development.Since capsules are the ideal medium for encapsulating and delivering these multi-particulate formulations in a presentable and effective format, ACG plays a critical role in supporting the pharmaceutical industry’s transition to MPFs. The company recognises that providing the right empty hard capsules is essential to ensuring the success of these advanced drug delivery systems.To address this growing need, ACG is working closely with customers at the start of their development journey. By offering expert guidance on choosing the right capsule types, ACG helps prevent formulation failures later in the process, which could result in costly delays and wasted time. This proactive support ensures that pharmaceutical developers avoid making mistakes that could jeopardise their product’s success in the market.Furthermore, ACG is committed to creating awareness and educating its customers on the advancements in capsule manufacturing technologies, particularly the use of Hypromellose (HPMC)-based empty hard capsules as an alternative to traditional gelatine capsules. HPMC capsules offer distinct advantages, such as being vegetarian, suitable for a wider range of formulations, and offering better stability for certain active pharmaceutical ingredients (APIs). This shift towards HPMC capsules reflects the evolving demands of both regulatory requirements and consumer preferences for more versatile and sustainable options.By partnering with customers and providing them with the right tools and knowledge, ACG is not only supporting the growth of advanced drug delivery systems but also positioning itself as a key enabler for the pharmaceutical industry’s future success in this rapidly advancing field.3. How is ACG addressing the growing demand for patient-friendly dosage forms, such as easy-to-swallow capsules and personalised medicine?At ACG, our customer-centric mindset has enabled us to become an extremely flexible supplier, dedicated to meeting the evolving demands of the market, particularly in the development of patient-friendly dosage forms. We understand the importance of delivering medications in formats that are convenient, aesthetically appealing, and easy to use, which is why we continuously adapt our products to address these needs.Flexible sizes for ease of swallowingACG has proven its flexibility by offering capsules in a variety of sizes to ensure that drugs can be encapsulated in the smallest possible capsules, making them easier for patients to swallow. By offering a range of capsule sizes, ACG ensures that medications are delivered in a form that maximises patient compliance.Aesthetic and natural coloured capsulesACG is mindful of the aesthetic preferences of patients, and we have developed capsules in a variety of coloured combinations, including natural-coloured options. This is particularly important in overcoming the "pill effect"—a common issue where patients are reluctant to take medicines. Our natural-coloured capsules provide a more neutral, less intimidating appearance, enhancing patient acceptance.Easy-to-open capsules for swallowing difficultiesMany of our customers have proactively turned to regular capsules as an ideal solution for patients who have difficulty swallowing pills. These capsules can be opened, allowing patients to sprinkle the contents into food or beverages, making it more convenient for patients with swallowing difficulties to consume their medication without stress.Delayed-release capsules for specialised needsIn response to the growing demand for advanced drug delivery systems, ACG offers delayed-release capsules designed to protect sensitive ingredients like probiotics and enzymes. These capsules provide the necessary protection from the acidic environment of the stomach, ensuring that the active ingredients are delivered effectively to the areas where they are most needed in the digestive system.Unique capsule designs with anti-counterfeit featuresACG also offers innovative capsule designs such as Clinicaps and Tabsules. These capsules not only provide functional benefits but also include anti-counterfeit features, adding an extra layer of security for both patients and pharmaceutical manufacturers. These designs can be integrated into dosage forms to enhance brand protection and ensure that patients are receiving the correct medication.ConclusionBy staying true to its customer-centric philosophy, ACG has proven itself as a highly adaptable partner in addressing the growing demand for patient-friendly dosage forms. Our flexible approach allows us to meet the diverse needs of the healthcare industry, from offering capsules in various sizes and colours to providing advanced solutions like delayed-release colourscapsules and anti-counterfeit designs. This commitment to innovation ensures that we are well-positioned to help pharmaceutical companies deliver medications in formats that enhance patient compliance and overall treatment outcomes. Source: https://pharmaceuticalmanufacturer.media/pharmaceutical-industry-insights/pharmaceutical-manufacturing-insights/q-a-acg-expands-in-croatia/
Read more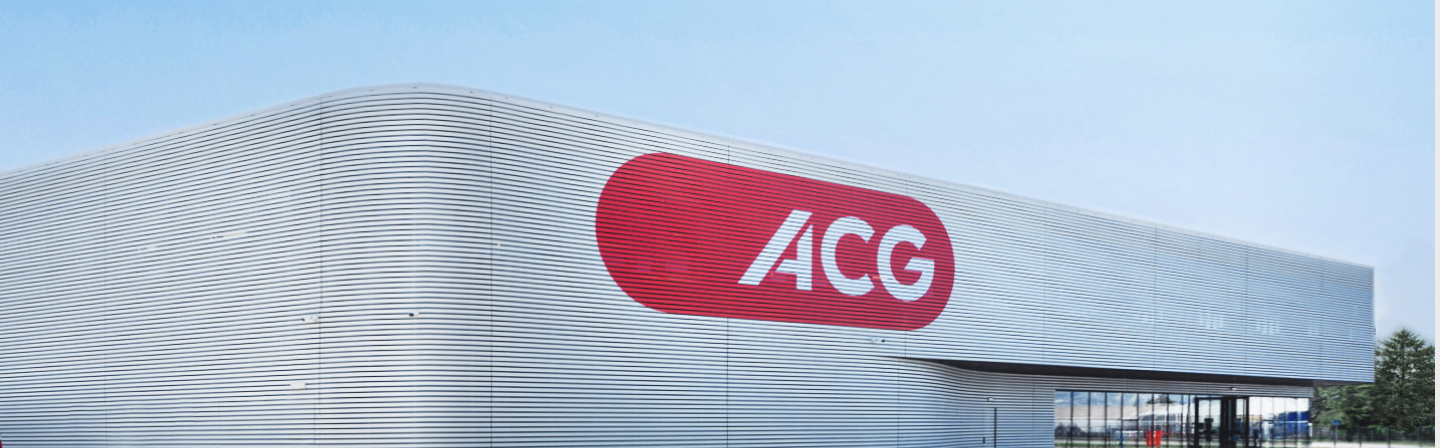
ACG expands capsule production capabilities at its Croatian facility
ACG expands capsule production capabilities at its Croatian facility
ACG has expanded its European footprint with an upgrade to its Croatian facility.The extension of its existing site enhances its capsule shell manufacturing capacity, while also offering novel warehouse and slitting facilities.This will allow ACG to cater to the increasing demand amongst the pharmaceutical industry for capsule solutions, while also strengthening its European presence.It will also allow the company to streamline the region's supply chain.Since ACG acquired the capsule manufacturing site in Croatia, the compaby has invested more than €50m into the infrastructure and technology of the facility, while also focusing on process optimisation.This recent expansion — according to the company — will be completed by the end of 2024.CEO of ACG Capsules, Selwyn Noronha, commented: "The expansion of our Croatian facility marks a pivotal moment in our European strategy. By boosting production and logistics capabilities, we are not only improving lead times but also contributing to the local economy by creating new job opportunities.""This facility meets the highest global manufacturing standards, and we are replicating our sustainability initiatives here, ensuring our operations benefit both the environment and the communities we serve."SR Shivshankar, CEO at ACG Packaging Materials, added: "The opening of our new warehouse in Croatia is a crucial step in increasing our agility and better serving our European customers. With shorter lead times and enhanced flexibility, this warehouse will allow us to respond to market demands faster and more efficiently. We are excited for the facility to be fully operational by November 2024."ACG will showcase its offerings at CPHI Worldwide in Milan from October 8 to 10, at stand 6B20. Attendees are invited to join the team for an open meeting on October 9th, from 10:00 to 12:00, where refreshments will be served.Source: https://www.manufacturingchemist.com/acg-capsule-production-facility-capability-expansion-croatia
Read more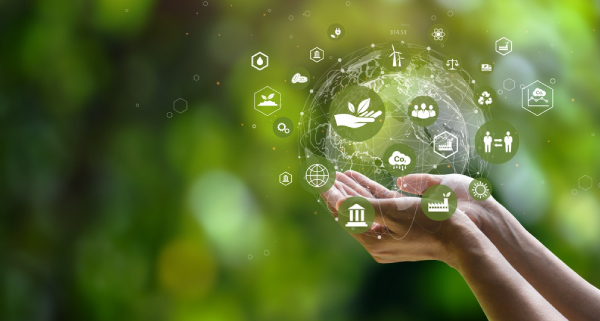
Tapping the Value of Conscientious Stewardship
Tapping the Value of Conscientious Stewardship
It is important for companies, including those in the life sciences industry, to proactively set targets and focus on long-term initiatives that will provide value realization and business transformation toward creating a more sustainable and resilient future. Indeed, within our own business, our adherence to the Science-Based Targets initiative through our strategic partnership with EY Parthenon1 underscores our commitment to conscientious corporate stewardship.At the time of the announcement, I had noted that our alliance with EY Parthenon marks a pivotal advancement in our sustainability pursuit and that by leveraging its expertise in industrial decarbonization, we are poised to expedite our net zero objectives. Our hope, as a result, is effectuating a meaningful reduction in our carbon emissions. Keeping that in mind, when it comes to net zero objectives, I am referring to “we” as large-scale manufacturers.S R ShivshankarOverall, embarking on the journey toward decarbonizing entire processes will undoubtedly prove overwhelming for many. Still, if we want to restrict global temperature fluctuations, then it is one that we must all embrace.Ultimately, it’s about looking toward the future and trying to understand wide-ranging stakeholder needs to create long-term and effective solutions. When it comes to addressing environmental schemes and proposals, every part of the manufacturing process needs to be considered. Organizations could look at a number of measures to reduce their carbon footprint, which could include:• Implementing an energy management system and increasing the usage of renewable energy sources, includ- ing solar power. This is something we do, with the aim of reducing fossil fuel consumption by 20% to 25%. • Improving overall equipment effectiveness by addressing machine time hours to reduce energy consumption. • Looking at how and which devices can be used with the internet of things, in order to continually monitor energy consumption, as well as to create energy-efficient designs. • Reducing waste generation within premises and upcycling where possible. • Promoting the use of electric vehicles and making the move toward hybrid models. • Undertaking sustainable practice through the use of zero liquid discharge, which can enable plants to save power and generate daily energy. • Creating biodegradable and compostable barrier films and coatings, promoting the use of single polymer plastics when it comes to packaging materials, while also working with companies to reduce overall packaging size.The mission to reduce the overall carbon footprint remains a driving principle for the pharmaceutical sector, with a focus on making manufacturing “contained, continuous, and connected,” while optimizing raw material use and reducing waste. We must continue to work collectively to achieve this goal, ensuring clear communication and complete transparency. We are moving in the right direction and already we’re seeing visible gains.About the AuthorS.R. Shivshankar is CEO at ACG Packaging Materials.Reference1. Kulkarni, M. ACG Joins Forces with EY-Parthenon For Strategic Partnership. Pharma Now. June 13, 2024. https://www.pharmanow.live/latest-news/ acg-joins-forces-with-ey-parthenon-for-strategic-partnershipSource: https://www.pharmaceuticalcommerce.com/view/tapping-the-value-of-conscientious-stewardship
Read more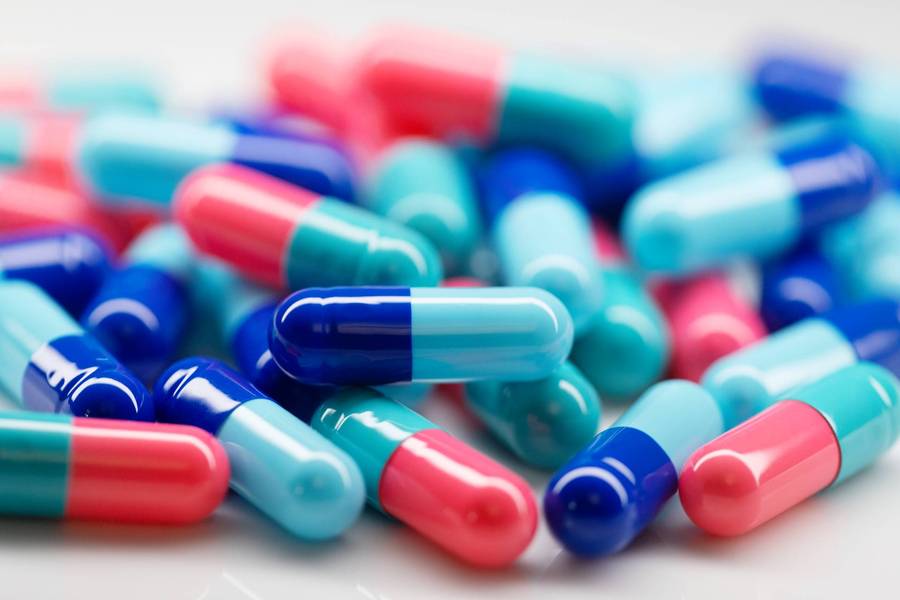
Encapsulation Evolution: A Catalyst for Transformative Change in Healthcare
Encapsulation Evolution: A Catalyst for Transformative Change in Healthcare
In the dynamic landscape of pharmaceutical development, innovation is the cornerstone of progress. As researchers, technicians and manufacturers continually strive to overcome challenges in drug formulation, delivery and patient adherence, one technology stands out for its transformative potential: encapsulation.Encapsulation, the process of enclosing active pharmaceutical ingredients within a protective shell, has revolutionized drug delivery. It provides solutions to myriad formulation hurdles such as: enabling the delivery of incompatible drugs, dual-release profiles, liquid filling with enhanced bioavailability, peptides for oral delivery, as well as enhancing the patient experience.This article delves into the multi-faceted benefits of encapsulation technology and its profound impact on pharmaceutical development — where empty hard capsules are not just containers but have become catalysts for real progress in healthcare.A Preferred Choice for Accelerated Product DevelopmentAmong the many options available, empty hard capsules have emerged as a preferred choice for encapsulating and delivering new chemical entities (NCEs), due to their versatility, compatibility and patient-centric advantages. Empty hard capsules offer unparalleled flexibility, accommodating a wide range of drug formulations, including solids, semi-solids and liquids. Their compatibility with diverse drug compounds, from poorly soluble to sensitive molecules, makes them an ideal choice for encapsulating NCEs with varied physicochemical properties. Whether it’s immediate or modified release formulations, enteric coating, or specialized delivery systems, empty hard capsules provide a customizable platform to meet the specific needs of NCEs both during development and commercialization.One of the primary challenges in NCE development today is achieving optimal bioavailability, especially for compounds with limited solubility issues. Empty hard capsules address this challenge by facilitating the formulation of drug compounds in bioavailable forms, such as lipid-based or self-emulsifying formulations.Additionally, the inert nature of hard capsules provides a readily available protective barrier against environmental factors, preserving the shelf life of NCEs, thereby ensuring product quality and compliance with regulatory standards.Ideal for Clinical TrialsDouble-blind clinical studies are the gold standard for evaluating the safety and efficacy of new pharmaceuticals, providing unbiased and reliable evidence for regulatory approval and clinical practice. Central to the success of these studies is the selection of appropriate dosage forms that ensure blinding integrity, dosing accuracy and patient compliance.Clinicaps, specialized capsules designed for clinical trials, have emerged as a preferred choice for encapsulating investigational drugs in double-blind clinical trials, offering unique advantages and considerations that enhance study integrity and efficiency.Empty hard capsules provide an ideal vehicle for encapsulating investigational drugs, as they can be easily filled with active or placebo formulations whilst — at the same time — maintaining identical appearance, size and taste. The opaque nature of hard capsules prevents visual identification of the encapsulated drug, further enhancing blinding integrity and minimizing potential sources of bias. Furthermore, the availability of different capsule sizes enables dose escalation or adjustment without compromising this integrity, which offers flexibility to accommodate varying dosing regimens in clinical trials.Empty hard capsules contribute to enhanced patient compliance by offering a convenient and familiar dosage form that is easy to swallow and tolerable for participants. Unlike tablets or powders, which may have undesirable taste or texture, capsules are generally well-accepted by study participants, minimizing the risk of non-compliance due to medication aversion or discomfort.Empty Hard Capsules: Guardians of Drug StabilityEnsuring drug stability is paramount in pharmaceutical formulation to maintain potency and efficacy throughout shelf life. Empty hard capsules serve as an indispensable tool in this regard, providing a protective barrier against moisture, oxygen and light, thereby safeguarding drug integrity.Moisture, oxygen and light pose a significant threat to the stability of sensitive drugs, ultimately leading to degradation due to hydrolysis, oxidation, or photolytic reactions, each of which respectively contributes towards loss of efficacy. Empty hard capsules act as a barrier, preventing ingress of moisture and minimizing oxygen permeation, thus protecting the encapsulated drug from the above deleterious effects. The physical barrier due to the thick shell wall ensures that the drug remains shielded from humidity and oxidative degradation, even in challenging storage conditions, thus extending shelf life and maintaining product quality. Opaque empty hard capsules offer light-blocking properties, shielding the encapsulated drug from photodegradation due to harmful UV and visible light, preserving product stability in light-exposed environments.The Efficiency of Capsules in Reducing ExcipientsUnlike tablets that often require multiple processing excipients, capsules have minimal requirement of excipients along with the drug substance to be filled in the capsule shell. This simplicity not only streamlines the formulation process but also reduces the complexity of regulatory submissions and quality control procedures, saving time and resource for pharmaceutical developers. By minimizing the number and quantity of excipients, capsules mitigate the risk of such interactions, enhancing the long-term stability and shelf life of pharmaceutical products. Moreover, the use of fewer excipients in the formulation process can improve patient safety by reducing the potential for allergic reactions, intolerances or any adverse effects associated with excipient exposure. Capsules also offer a more patient-friendly dosage form, as they eliminate the need for taste masking agents and coatings. As a result, this enhances patient acceptance and adherence to prescribed therapies, particularly in sensitive patient populations such as children, elderly individuals, or patients with swallowing difficulties.Making Multiple Dosage Strengths Cost-Effective and ScalableDuring the development and commercialization of pharmaceutical products, dosage variations are common to accommodate different patient populations and therapeutic regimens. Encapsulation technology simplifies the process of scaling up and modifying dosages without necessitating changes to the underlying formulation. For instance, a manufacturer producing a cardiovascular medication may need to offer multiple dosage strengths to accommodate patients with varying degrees of disease severity. Encapsulation allows for the seamless adjustment of dosage strengths by filling dose equivalent contents in readily available standard capsule sizes without re-developing the core formulation – saving time and resources. From a manufacturing standpoint, empty hard capsules offer cost-effective solutions for drug delivery. Their compatibility with high-speed encapsulation equipment allows for efficient and scalable production, reducing manufacturing costs and time-to-market for pharmaceutical companies.Tailoring Release Profiles and PharmacokineticsA real boon for formulators, empty hard capsules offer the flexibility to design tailored release drug profiles, to help optimize drug pharmacokinetics and therapeutic outcomes.By modulating the size, composition and coating of multiparticulate systems filled in capsules, researchers can tailor the release kinetics of drugs to match desired dosing regimens and therapeutic targets. This enables precise control over drug release profiles, minimizing fluctuations in plasma drug concentrations and reducing dosing frequency, therefore improving patient compliance, particularly for medications with narrow therapeutic windows or sustained therapeutic effects.Availability of ready-to-use delayed-release and enteric capsules enable drug release in the intestines, thus maximizing therapeutic efficacy of acid-sensitive molecules. Empty hard capsules have also proved to be an ideal carrier for formulating poorly soluble drugs, including lipid-based or self-emulsifying liquid formulations, thereby enhancing drug solubility and permeability — translating into higher systemic exposure and therapeutic efficacy.Enabling Product Differentiation & AestheticsIn today’s competitive market, product differentiation is essential for brand recognition and market success. Encapsulation technology provides opportunities for customizing capsule types, colors and printing options, allowing manufacturers to create distinct product identities. For example, a manufacturer may use encapsulation to produce visually appealing capsules using a variety of different colors and shapes, catering to consumer preferences, and enhancing brand recognition on store shelves. Additionally, encapsulation technology enables the delivery of multiple-colored pellets within a single capsule, enhancing the overall aesthetic appeal of pharmaceutical products. For instance, a multivitamin supplement may contain pellets of different colors representing various vitamins and minerals encapsulated together in a single capsule.ConclusionIn conclusion, encapsulation technology represents a pivotal advancement in pharmaceutical science, offering a multitude of benefits across the drug development continuum. From streamlining formulation processes to enhancing drug stability, bioavailability and patient adherence, encapsulation has proven to be a versatile and indispensable tool for researchers and manufacturers alike. With its various applications, encapsulation is not merely a technical innovation but a catalyst for transformative change in healthcare.Author DetailsDr. Subhashis Chakraborty, Head of Global Product Management- ACG CapsulesPublication DetailsThis article appeared in Tablets and Capsules Magazine: Vol. 22, No. 4 September/October 2024 Pages: 29-31
Read more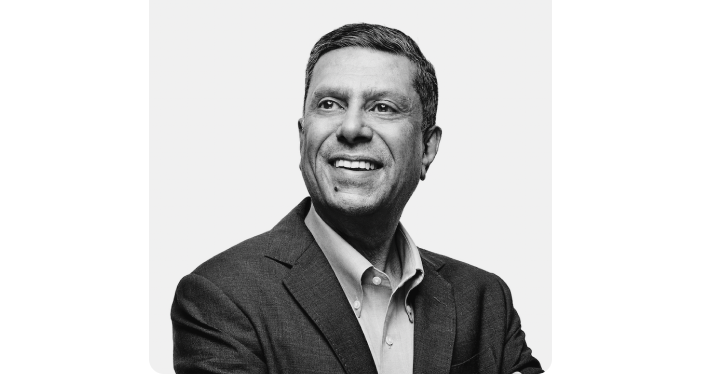
Why it is important for organizations to set long-term goals when planning for …
The Value in Committing to Conscientious Corporate Stewardship
Sustainability has become a real necessity and the pursuit of organizations across the globe, as many now throw down the scientific gauntlet.It is important for organizations to proactively set targets and focus on long-term initiatives that will provide value realization and business transformation toward creating a more sustainable and resilient future. Indeed, within our own business, our adherence to the Science Based Targets initiative (SBTi) through our strategic partnership with EY Parthenon1 underscores our commitment to conscientious corporate stewardship.At the time of the announcement, I had noted that our alliance with EY Parthenon marks a pivotal advancement in our sustainability pursuit and that by leveraging their esteemed expertise in industrial decarbonization, we are poised to expedite our net zero objectives, thereby effectuating a meaningful reduction in our carbon emissions. Keeping that in mind, when it comes to net zero objectives, I am referring to “we” as large-scale manufacturers.Overall, embarking on the journey toward decarbonizing entire processes will undoubtedly prove overwhelming for many. Still, if we want to restrict global temperature fluctuations, then it is one that we must all embrace.Ultimately, it’s about looking toward the future and trying to understand wide-ranging stakeholder needs to create long-term and effective solutions. When it comes to addressing environmental schemes and proposals, every part of the manufacturing process needs to be considered. Organizations could look at a number of measures to reduce their carbon footprint, which could include:• Implementing an energy management system and increasing the usage of renewable energy sources, including solar power. This is something we do, with the aim of reducing fossil fuel consumption by 20-25%.• Improving overall equipment effectiveness (OEE) by addressing machine time hours to reduce energy consumption.• Looking at how and which devices can be used with the internet of things (IoT), in order to continually monitor energy consumption, as well as to create energy-efficient designs.• Reducing waste generation within premises and upcycling where possible.• Promoting the use of electric vehicles and making the move toward hybrid models.• Undertaking sustainable practice through the use of zero liquid discharge, which can enable plants to save power and generate daily energy.• Creating biodegradable and compostable barrier films and coatings, promoting the use of single polymer plastics when it comes to packaging materials, while also working with companies to reduce overall packaging size.The mission to reduce the overall carbon footprint remains a driving principle for the pharmaceutical sector, with a focus on making manufacturing “contained, continuous and connected,” while optimizing raw material use and reducing waste.We must continue to work collectively to achieve this goal, ensuring clear communication and complete transparency. We are moving in the right direction and already we’re seeing visible gains.About the AuthorShivshankar S.R is the CEO of ACG Packaging Materials.Reference1. Kulkarni M. ACG Joins Forces With EY-Parthenon For Strategic Partnership. Pharma Now. June 13, 2024. https://www.pharmanow.live/latest-news/acg-joins-forces-with-ey-parthenon-for-strategic-partnership
Read more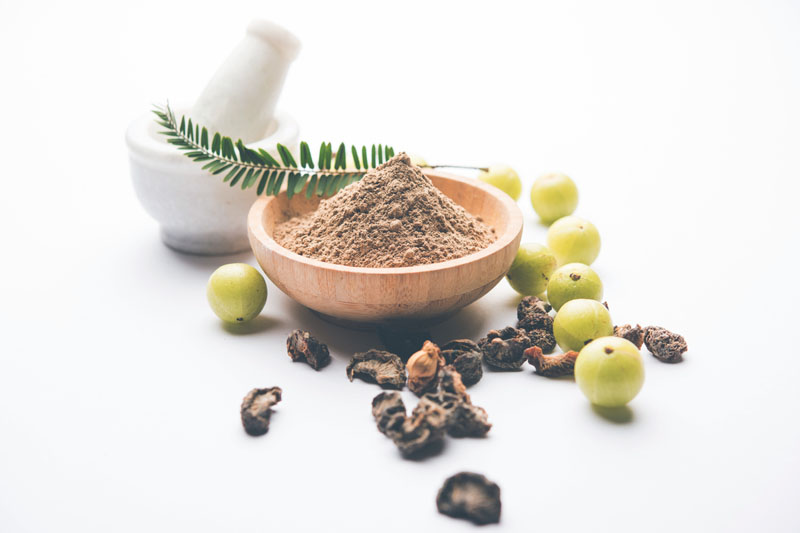
Recognising the benefits of making Ayurveda more accessible and palatable from …
Modernising Ayurveda: transforming traditional remedies for global markets
Ayurveda translates to “knowledge of life” and is a natural system of medicine that originated in India more than 3000 years ago. It is based on the idea that disease is caused by an imbalance or stress in a person's consciousness.Associated treatments aim to encourage certain lifestyle interventions and natural therapies to restore the balance between the body, mind, spirit and the environment.1This emphasis on promoting balance and taking a natural/holistic approach to healthcare and well-being is a key contributor to Ayurveda’s increase in popularity and growth in new markets around the world.According to research quoted by the CBI Ministry of Foreign Affairs, the European Ayurvedic market is projected to reach a value of €1.6 billion by 2028 with an average annual growth rate of 12% for 2022–2028.2New markets, new opportunitiesThe growth and expansion of herbal medicines outside their native India is opening doors for new opportunities in product design and dosage forms — making the formulations more accessible and stable … as well as reducing manufacturing times and costs.One example of this is Kadha, a classic Ayurvedic formula described as being a decoction obtained after boiling a mixture of herbs with water under a low flame until the volume is reduced to form a concentrated solution/suspension. Kadha may be used as a medicine by itself or to prepare other dosage forms.3Traditionally, batches of Kadha would percolate for days on kitchen hobs and take a long time to produce. The result — effective as a home remedy — is generally bitter to taste and lacks standardisation, thereby limiting its marketability on a global scale.Packed into glass bottles, it also has a short shelf-life and expensive shipping costs. Finding a way to transform these traditional remedies into viable oral solid dosage (OSD) formulations is helping to tackle these challenges, smoothing the way toward growth and the widespread adoption of Ayurveda around the world.This article highlights a new chapter in Ayurveda’s evolution.It delves into how we at ACG (an original equipment manufacturer [OEM]) are teaming up with key industry players to help reduce the associated production times and manufacturing costs, while — at the same time — increasing the shelf-life and palatability of this ancient medicine.Trialling new techniquesEarlier this year saw one of the first trials combining the benefits of traditional Kadha with modern manufacturing methods using single-pot equipment to create viable OSD formulations without compromising on quality and efficacy — resulting in commercially available tablets to treat joint pain diseases such as osteoarthritis.At the start of the trial, a reputable Ayurveda company prepared a Kadha base from several medicinal extracts and concentrated it to form a dispersion with a solids content of 30–40%.The resulting viscous suspension was then evenly spread on trays to dry in the open.Once dry, the base formed a sticky hard cake, which was flaked, milled, sieved, blended, lubricated and — finally — compressed into tablets. This initial formulation process posed several challenges that needed solving, including the following:• an uneven material that required additional processing time• hours of manual work owing to multistep, multivessel procedures• batch-to-batch inconsistencies and variations in colour, taste, appearance, hardness and disintegration• long cleaning and changeover times• low yield, efficiency and productivity levels• a process that was too rigid to meet surges in demand• high transport and packaging costs• a short product shelf-life• high tablet-disintegration times.Overcoming the obstaclesTo address these issues and make the formulation process more technically and commercially viable, we — together with the client — studied the traditional processes involved in producing Kadha.This involved brainstorming ways to modernise it while still maintaining formulation integrity. A new fluid-bed process was introduced as a result. The Kadha decoction (30–45% solids) was sprayed and adsorbed on to a substrate with top-spray fluid-bed equipment.To ensure a more controlled agglomeration process, all process parameters were optimised, including air flow, spray rate, product temperature and exhaust temperature.Speeding up process timesThese changes yielded a simplified process with a substantial process time reduction: from several days down to 18 hours. The resulting product also met the requisite quality standards in terms of porosity, viscosity, flow characteristics and efficacy.This was achieved with ambient air flow conditions (without any dehumidification system) at the client’s facility.We were also able to further decrease the batch process time from 18 hours down to 10.5 hours (with no dehumidification) and then down to 9.5 hours by introducing a dehumidification system.Overall, compared with the manufacturer’s traditional method, the process was now 10 times quicker. A top-spray plant achieved another 44% reduction.Further productivity potentialAlthough the initial results from the trial have been encouraging, our technical team has developed more ways to enhance productivity, including• fine tuning the process parameters with a dehumidification system• partial addition of gum resin powder as a dry mix or extra-granular form• increasing the solid concentration of Kadha for greater yields.• More specifically, the compression process can be made more efficient by• eliminating the downstream process step of starch-paste granulation• optimising the concentration of extra-granular components/excipients such as disintegrants and lubricants (magnesium stearate)• optimising lubrication with magnesium stearate from 30 to 10 minutes• segregating the blending and lubrication steps• incorporating natural superdisintegrants to improve disintegration times• avoiding overdrying to control hardness and disintegration properties.Worldwide adoptionWith the results of trials such as these already on the shelves, the ever-improving manufacturing processes will continue to fuel the expansion, availability and popularity of Ayurveda products beyond their traditional roots.Converting Kadha-based formulations using modern technology promises to make Ayurvedic formulations more robust, efficient, reproducible and cost-effective, without compromising their efficacy.As manufacturers continue to improve and fine-tune these processes, shelf-lives will increase, packing and transportation costs will be reduced and patient compliance will improve — allowing people around the world to access and benefit from this ancient knowledge of life.Referenceswww.hopkinsmedicine.org/health/wellness-and-prevention/ayurveda.www.cbi.eu/market-information/natural-ingredients-health-products/trends#growing-interest-in-ayurvedic-and-traditional-medicine.www.ncbi.nlm.nih.gov/pmc/articles/PMC7329714/.https://nutraceuticalbusinessreview.com/modernising-ayurveda-transforming-traditional-remedies-for-global-markets
Read more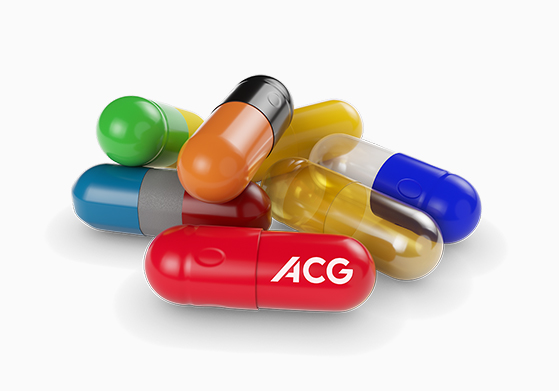
From Bitter to Better: How Capsules Improve Patient Acceptance of Medications
From Bitter to Better: How Capsules Improve Patient Acceptance of Medications
A number of factors can significantly affect medication acceptability, including product design, route of administration, dosage forms, taste, and appearance. These may sometimes be influenced by the physical and physiochemical properties of active ingredients or drugs. Among these factors, especially for the oral route of administration, taste, and odor have emerged as a major concern in pharmaceutical development, often posing a significant challenge due to the bitterness or unpleasant flavor of certain drugs and excipients. This inherent taste profile presents an often formidable task for formulators striving to create appealing products. In response to this critical aspect of healthcare, pharmaceutical companies are increasingly integrating criteria into their formulations aimed at improving medication acceptability while simultaneously preserving efficacy. These techniques involve employing strategies to mask or disguise the unpleasant taste and odor of medications, thereby enhancing their palatability and overall patient compliance.Amidst this, capsules have emerged as a valuable tool in taste and odor masking, offering an ideal solution for administering bitter and unpleasant-tasting medications. By encapsulating medication within a protective layer, capsules prevent direct contact with the taste buds in the mouth, thereby increasing patient acceptability and - in turn - compliance.Taste Masking in Oral PharmaceuticalsThe development of oral drug formulations demands meticulous attention to organoleptic properties, especially taste and palatability, given their significant impact on medication acceptability. They hold considerable importance not only in pharmaceuticals but also in gastronomical contexts, influencing consumer choice and adherence to medication regimens.Pharmaceuticals typically consist of pure drugs combined with additives, some of which may impart a bitter or unpleasant taste that affects the medication’s overall palatability. This can lead to potential reluctance or even refusal to take medication, making it essential for pharmaceutical companies to address taste concerns. For instance, drugs like antibiotics, anti-inflammatories, analgesics, antiepileptics, anticoagulants, oral vaccines, and sex hormones often have a dominant taste that significantly impacts how patients experience them. This taste can create a negative perception, which can deter patients from complying with their treatment plans. Consequently, opting for better-tasting alternatives poses challenges for pharmaceutical companies in terms of maintaining patient adherence and therefore subsequent profitability.Adherence problems are common among children and the elderly because of taste sensitivity. Children have more taste buds than adults, making them pickier about the flavor of medicines. On the other hand, the elderly often take multiple medications, which can make it harder for them to keep track and stick to their treatment plans. So, making medicines taste better is important to help them keep taking them regularly and get the best results from their treatment.In this context, capsules stand out as vital for ensuring adherence to medication. Renowned for their long-standing presence and numerous benefits, capsules hold a top spot among traditional dosage forms. Their superiority is underscored by their exceptional palatability, valued since ancient times. Capsules offer a range of advantages, including versatility in formulation, space for innovation, an appealing appearance, and – notably - effective taste masking. With their ease of use and widespread acceptance, capsules clearly play a significant role in promoting medication adherence.Factors Affecting the Taste of PharmaceuticalsTaste indeed pertains to the capability to identify the flavor of a substance upon its entry into the mouth. This recognition takes place as the drug dissolves in saliva and interacts with the taste buds. Hence, even minute quantities of a drug with a potent, unpleasant taste can be discerned upon exposure to saliva. Following exposure, this perception is transmitted to the gustatory receptors, specialized cells located on the taste buds, which then trigger the sensation of taste.In the case of pharmaceuticals there exist various parameters that can affect the overall taste of the formulation. These factors encompass the chemical structure of the active ingredient, the presence of functional groups, the solubility of the compound, its stability, concentration, and so on.Many active pharmaceutical ingredients (APIs) inherently carry bitter or unpleasant flavors, as a result of their chemical composition. These taste attributes are intrinsic to the compound and are difficult to alter. Specific functional groups present within the molecular framework of APIs play a role in bitterness. For example, compounds featuring nitrogen or sulphur atoms may induce bitter tastes. These functional groups engage with taste receptors on the tongue, eliciting a bitter sensation. Furthermore, aromatic compounds, characterized by benzene rings or analogous structures, can also contribute to bitterness.Certain additives or excipients possess the ability to chemically interact with the API, leading to alterations in its taste profile. These interactions may result in the formation of compounds with bitter or unpleasant tastes, thereby worsening taste-related difficulties in the formulation. Additionally, specific excipients are deliberately formulated to mask the taste of pharmaceuticals. However, there are occasions when these additives fail to adequately conceal the bitterness or unpleasantness of the drug, leading to a suboptimal taste experience for the patient.The hydrophobicity or water-repellent nature of certain compounds can affect their taste. These molecules tend to interact more strongly with taste receptors on the tongue compared to hydrophilic molecules. When hydrophobic APIs come into contact with saliva, they may linger longer in the mouth, allowing for prolonged interaction with taste receptors.Nevertheless, even with a comprehensive understanding of these compound characteristics, developers often encounter difficulties in significantly modifying the product to enhance its palatability, particularly during the developmental stage. This challenge is exacerbated by the paramount importance of ensuring the safety and efficacy of such compounds. This evaluation usually occurs in early-phase studies utilizing non-human primates, overlooking the palatability considerations frequently due to the absence of human subjects.At times, the therapeutic effect takes primacy importance over palatability modifications, leading to neglect of additional enhancements. Additionally, the physicochemical attributes of the drug, including solubility, permeability, and stability, place constraints on formulation strategies aimed at taste enhancement.However, in the current landscape, taste masking has become an essential aspect of development. Several methods are currently employed for the creation of palatable medications, some of which are outlined below.Taste Masking MethodsTaste masking methods encompass both traditional and advanced approaches to mitigate the unpleasant taste of medications. Conventional methods typically involve incorporating sweeteners and flavor enhancers. Recent advancements offer sophisticated techniques such as pro-drugs, ion exchange resins, hot melt extrusion, solid dispersions, microencapsulation, spray drying, and coating. However, these methods often entail complex processes and additional ingredients, which can affect the development timeline and manufacturing costs.In contrast, replacing taste masking methods with capsules offers a convenient alternative for enhancing medication palatability. By leveraging the inherent properties of capsules as a taste-masking dosage form, pharmaceutical developers can streamline formulation processes, enhance patient experience, and ultimately, promote better medication adherence and therapeutic outcomes.Capsules for Effective Taste MaskingCapsules present a straightforward yet highly effective solution to the challenge of taste masking in pharmaceutical formulations. Their inherent capability to act as a barrier between the drug and taste receptors minimizes direct taste perception, particularly beneficial for medications with inherently bitter or unpleasant tastes. Examples include drugs like quinine, celecoxib, etoricoxib, levofloxacin, ofloxacin, sparfloxacin, ciprofloxacin, cefuroxime, erythromycin, clarithromycin, ibuprofen, where simple flavors or sweeteners may not suffice due to their overpowering taste profiles, the capsule encapsulation may provide an effective solution. Additionally, it also aids in masking odors, further enhancing patient acceptance. The design of capsules facilitates effortless carrying and administration, augmenting their attractiveness. This convenience factor plays a significant role in encouraging patients to stick to their medication regimen, contributing to improved treatment adherence and ultimately better health outcomes.From a manufacturing standpoint, capsules stand out as the preferred choice in the pharmaceutical industry due to a number of core advantages. Their straightforward formulation process simplifies production, requiring fewer steps compared to complex taste masking processes. This reduction in complexity translates to saved time and resources during formulation development. Additionally, capsules offer cost-effectiveness, attributed to efficient manufacturing processes, making them a financially viable option for pharmaceutical companies. Furthermore, the ease of preparation enhances efficiency on the manufacturing line. Capsules can be filled with precision and consistency, minimizing production errors and maximizing output. Importantly, capsules eliminate the need for additional taste masking additives or coating agents, simplifying the formulation, and reducing the risk of potential interactions or side effects. It also maintains the bioavailability of the medication, ensuring optimal delivery of active ingredients without compromising absorption or efficacy due to their inert nature.In medication formulation, the dose of the specific drug utilized to treat the ailment holds significant importance. For instance, with low-dose drugs, there is ample space to adjust the taste profile of the formulation by incorporating additional excipients. However, high-dose drugs pose a challenge due to limited space for supplementary excipients. In such cases, capsules emerge as the optimal choice. It offers the flexibility to accommodate the drug without the need for extra excipients, effectively fulfilling their role in taste masking and pharmaceutical delivery.Furthermore, capsules represent a versatile option for pharmaceutical delivery, facilitating various formulation modifications to meet specific needs. In addition to providing a physical barrier, capsules can function as suitable containers to deliver the drug to the intended site of action. If necessary for the enhanced formulation need, it can encapsulate taste-masking agents or coated drug particles, further reducing the likelihood of taste detection until the capsule dissolves in the gastrointestinal tract. This additional safeguard shields patients from unpleasant pharmaceutical tastes, streamlining taste masking while bolstering patient acceptance and adherence through the familiar and more palatable dosage form.In addition to their formulation flexibility, capsules offer a notable array of customization options. They possess the versatility to accommodate a wide range of drug formulations, encompassing immediate-release, extended-release, and modified-release variants, all while retaining their taste-masking properties. Moreover, capsules can be tailored with varying shell compositions, sizes, and colors. These present opportunities for personalized medication delivery, which aligns precisely with consumers’ preferences and requirements.The capsule shell, typically composed of materials such as gelatin, HPMC, or acrylate polymers, serves as a protective barrier for the encapsulated drug. This polymer shell is widely favored in pharmaceutical capsules for its ability to form a sturdy, flexible, and taste-neutral enclosure. HPMC capsules, for instance, are renowned for effectively masking the taste of drugs, ensuring a seamless and pleasant swallowing experience for patients.Moreover, with recent advancements, the capsule shell itself can undergo further modifications to incorporate flavors if desired. Capsule formulation allows for the addition of flavoring agents, enabling the outer membrane to impart a specific taste to the medication. These flavored capsules offer an additional dimension of customization, enhancing patient acceptability and compliance by catering to individual taste preferences.SummaryIn the rapidly evolving therapeutic landscape, patients are becoming increasingly discerning about their choices, even within the pharmaceutical sector. The medication acceptability is becoming essential during product development, particularly considering the taste and palatability of oral pharmaceuticals. Despite being the simplest method of pharmaceutical administration, oral formulations have demonstrated effectiveness in delivering both simple and complex molecules. However, to enhance formulation acceptability and align with industry trends focusing on palatability, numerous adaptations have been made.A successful oral dosage form should not only be effective but also enhance palatability and garner patient acceptance. The pharmaceutical industry has significantly contributed to meeting these objectives through various methods. Among these, capsule dosage forms emerge as a straightforward yet effective solution. Leveraging their inherent properties, capsules improve taste perception and increase patient acceptance, making them a preferred option for delivering medications effectively while ensuring a positive patient experience. With the simplicity and effectiveness of capsule formulations, they have become an effective means to enhance palatability and acceptability in pharmaceuticals.Author DetailsJnanadeva Bhat- Head-R&D-Formulation development (Pharma & Nutra), ACG; Manali Dalvi- Lead-R&D-Whitepaper and publications; (Pharma & Nutra), ACGPublication DetailsThis article appeared in American Pharmaceutical Review:Vol. 27, No. 5July/Aug 2024Pages: 55-57https://www.americanpharmaceuticalreview.com/Featured-Articles/614440-From-Bitter-to-Better-How-Capsules-Improve-Patient-Acceptance-of-Medications/
Read more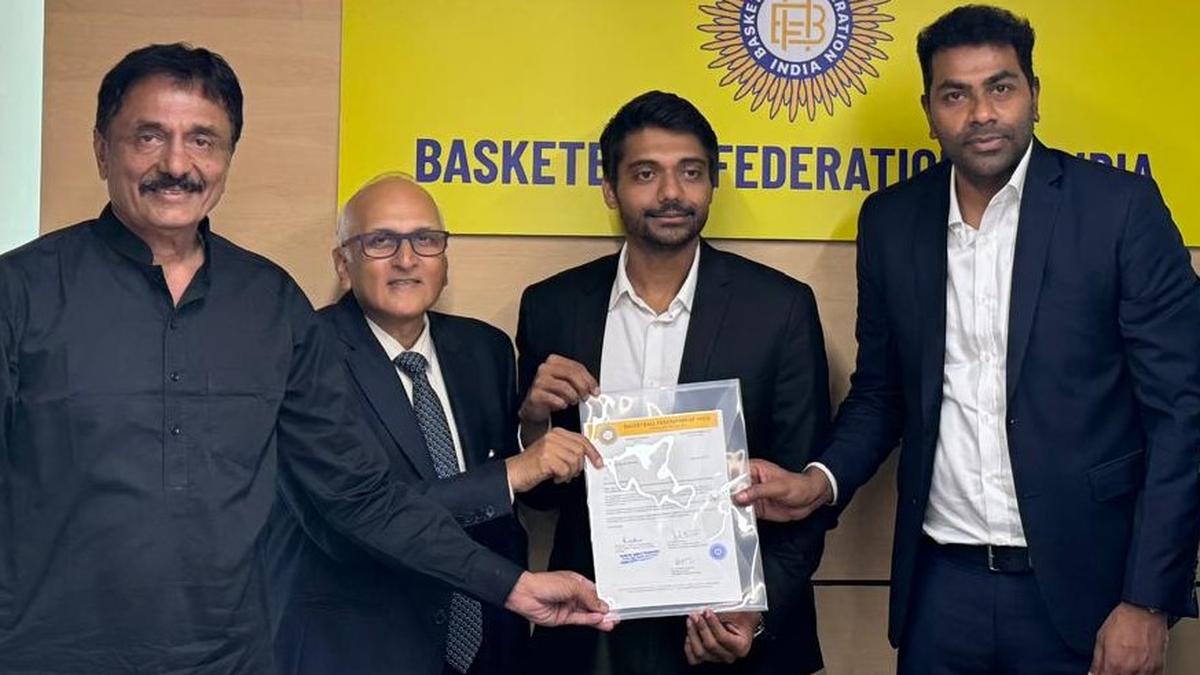
BFI president Aadhav Arjuna, right, and secretary general Kulvinder Gill, left,…
BFI signs seven-year deal with ACG Sports for professional basketball league
Addressing the media here on Friday, the president of BFI, Aadhav Arjuna said that for each year, the amount would be Rs. 20.6 crore rupees for the 5x5 format and Rs. 10.3 crore for the 3x3 format.“It was a transparent system, and we gave it to the highest bidder. It is a medical group of companies, and has already been associated with supporting basketball through many events,” said the BFI president al Star Basketball League in Delhi on Friday.The Basketball Federation of India (BFI) has signed a seven-year deal with ACG Sports Limited, with a guarantee of Rs.216.30 crore for hosting the National Star Basketball League for men and women.Addressing the media here on Friday, the president of BFI, Aadhav Arjuna said that for each year, the amount would be Rs. 20.6 crore rupees for the 5x5 format and Rs. 10.3 crore for the 3x3 format.“It was a transparent system, and we gave it to the highest bidder. It is a medical group of companies, and has already been associated with supporting basketball through many events,” said the BFI president “It is a new beginning for Indian basketball. We hope to pay substantial money to our players. We call all the big corporate companies and sponsors to invest in the league and make it a success,” Arjuna said.“We will host both the men’s and women’s leagues. The BFI would hold 100% ownership of the league so that we put the revenue generated back into the game for our developmental projects,” he said.It was stated that about 100 Indian players would stand to benefit from the league, which would also feature about four foreign players in each team.“We call all the players and coaches, to be ready, and to be fit, for the new journey,” said Arjuna.The league is expected to feature 10 men’s teams, and eight women’s teams.While the 5x5 format is expected to be played in stadiums, the 3x3 format could be staged on the beach, parks and malls so as to take the game to the people.The BFI president also said that he had an extensive tour of the USA to collaborate with the NBA for the betterment of Indian basketball.“We already have Scott Flemming for the men’s team. We will soon have an American coach for the women’s team and an American fitness coach also,” he said.Some of the money generated from the league is expected to be invested in making world-class infrastructure for Indian basketball.“In the USA, even colleges have a world-class stadium,” said Arjuna.The secretary general of BFI, Kulvinder Gill said, “Now Indian players can take up basketball as a career. We have enough talent in the country to nurture and build.”The details of the teams, structure, venues and fixtures are expected to be announced in a few weeks time. Source: BFI signs seven-year deal with ACG Sports for professional basketball league
Read more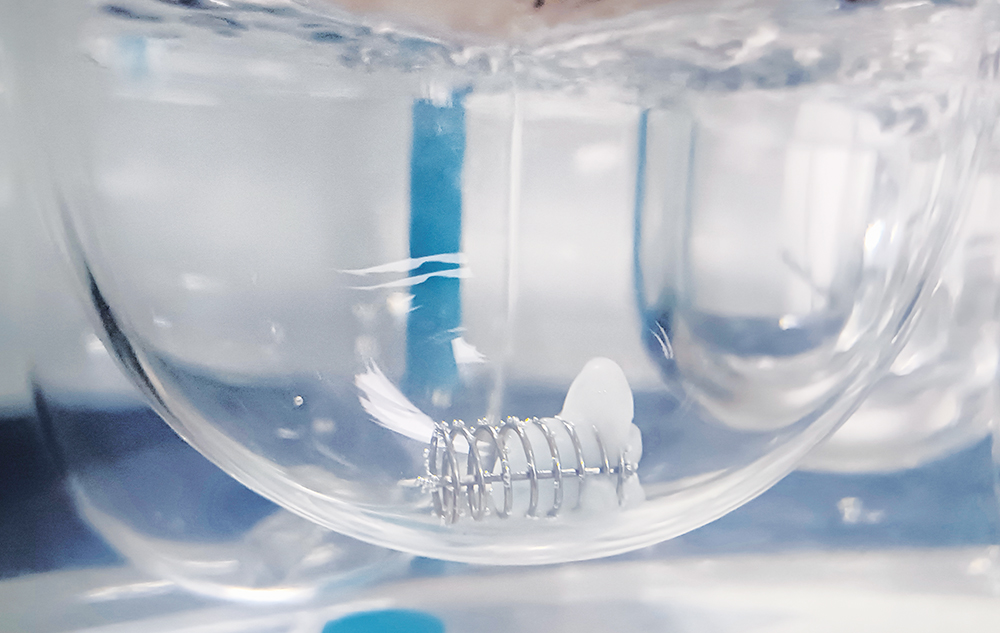
Strategies to mitigate gelatin cross-linking in oral solid drug delivery
Strategies to mitigate gelatin cross-linking in oral solid drug delivery
The oral solid drug delivery system is a prominent mode of drug administration. It is recognised for being non-invasive, patient compliant and convenient; steadfastly catering to the multifaceted demands of the market through its pioneering methodologies.Despite the emergence of cutting-edge techniques such as biologics, molecular delivery and parenteral administration, the prevalence of solid delivery systems continues to undergo ongoing innovation. From traditional pills and capsules to novel variations, such as gummies, soft chews, granules, lozenges and pastilles, the oral delivery mechanism has revolutionised pharmaceutical formulations, capturing the attention of both healthcare professionals and consumers. Its adaptability, accessibility and effectiveness have propelled it to the forefront, surpassing even the established parenteral and intravenous routes.Irrespective of the product type, the fundamental goal of processing oral solid dosage (OSD) forms remains unwavering: to create formulations that guarantee consistent dosing, reliable distribution of ingredients, and uniform dissolution and bioavailability. However, achieving this objective is contingent upon the dosage forms, actives and excipients employed.Gelatin often serves as a crucial excipient in OSD formulations. Whether encapsulating active ingredients within hard or soft shells or serving as a coating agent for tablets or a gelling agent in any other formulations, gelatin emerges as a fundamental ingredient across various oral delivery formats. Its versatility finds applications in a wide range of dosage formats.However, despite its extensive use, OSD manufacturers grapple with a persistent challenge: gelatin cross-linking within formulations, initially observed in 1974 for hard capsules containing chloramphenicol. This phenomenon poses a threat to the dissolution of pharmaceutical products, underscoring the need for strategies to mitigate such barriers. As we navigate the complexities of drug formulations, addressing issues such as gelatin cross-linking becomes paramount in advancing the efficacy and reliability of oral drug delivery systems.CROSS-LINKING IN THE GELATINFollowing the ingestion of gelatin capsules or gelatin-coated tablets, the primary objective of the formulation lies in releasing the inner content into the biological media. However, it is often observed that gelatin-based formulations tend to experience dissolution failures upon ageing, which is primarily attributed to cross-linking in stressed gelatin-containing products. It causes the formation of a swollen, thin, tough, rubbery, water-insoluble membrane, known as a pellicle (Figure 1). This may act as a barrier to the drug release from the formulation, resulting in the slower release of the filled formulation, which consequently leads to a decrease in dissolution values or no release at all in in vitro studies. The degree of cross-linking can vary within and between capsules, making it difficult to predict the extent of the issue. Once formed, these pellicles are irreversible, rendering the gelatin insoluble. As a consequence, dissolution results will have higher variability when gelatin capsule/coated tablets are cross-linked. This phenomenon – during the early stages of drug insertion into the market – often results in failure to meet regulatory guidelines for in vitro studies, prompting regulatory authorities to recall the product.MECHANISM OF GELATIN CROSS-LINKINGGelatin, derived from collagen via hydrolysis, is a soluble protein mixture primarily composed of amino acids (Figure 2). These amino acids, linked by amide bonds, form a linear polymer with molecular weights ranging from 15,000 to 250,000. Cross-linking in gelatin can arise from chemical interactions between its peptide chains or individual amino acids. These interactions can be triggered by small amounts of aldehydes, which are present in excipients or APIs. They may also occur from the breakdown of formulation components or packaging materials – or exposure to harsh conditions such as high temperatures and humidity. Figure 2: Gelatin structure.There are two main types of cross-linking reactions observed in gelatin: internal and external. Internal cross-linking takes place when gelatin capsules are exposed to high temperatures and humidity, primarily affecting their inner surfaces. In contrast, external cross-linking occurs when gelatin-based formulations, such as hard or soft capsules and gelatin-coated tablets, interact with substances such as aldehydes, peroxides or sulfonic acids.These substances cause chemical changes in the gelatin molecules, transforming them from a random coil configuration to a collagen triple helix structure.The mechanism of gelatin cross-linking involves three distinct pathways, each driven by specific molecular interactions and catalytic factors.Intrastrand and Interstrand Cross-Linking: Gelatin’s reactivity stems from interactions among amino acids within the same gelatin molecule (intrastrand) or between neighbouring molecules (interstrand). Key amino acids involved in this process (most notably lysine) exhibit trifunctional properties. Lysine residues in close proximity undergo oxidative deamination, yielding terminal aldehyde groups. These aldehyde groups can then react with neighbouring ε-amino groups of lysine, forming imine intermediates. Subsequent aldol condensation reactions lead to the formation of cross-linked products containing pyridinium rings. This cascade of reactions is catalysed by external factors such as heat and relative humidity or the presence of a chemical agent.Reaction with Carbonyl Groups: Another mechanism involves the interaction between lysyl ε-amino groups and aldehydic impurities present as contaminants. This reaction generates hydroxymethylamino derivatives, which undergo dehydration to form imines. These imines then engage in further reactions with hydroxymethyl lysine residues, forming dimethyl ether bridges. Ultimately, rearrangement reactions result in methylene linkages between lysyl ε-amino groups, facilitating cross-link formation. Similar reactions can occur with aldose sugars commonly found in pharmaceutical formulations, wherein imine intermediates react with free amino groups to yield ketose sugars. Subsequent reactions between imines and sugars lead to cross-linking via carbonyl functionalities.Formation of Aminals: Additionally, gelatin cross-linking can occur through the formation of aminals, which are amine derivatives of acetals. This process is influenced by the pH of the environment. Aminals formed between gelatin chains contribute to cross-linking, further enhancing the structural integrity of the gelatin network.FACTORS CONTRIBUTING TO GELATIN CROSS-LINKINGCross-linking in gelatin formulations can stem from various environmental and chemical factors, significantly impacting their stability and performance (Table 1). Drug NameDosage FormUSP ApparatusSpeed (RPMs)MediumVolume (mL)Recommended Sampling Times (minutes)UpdatedLopinavir/RitonavirCapsulte (Soft-Gelatin)II (Paddle)50Tier 1: 0.5 M Polyoxyethylene 10 Lauryl Ether with 10 mM Sodium Phosphate monobasic (pH 6.8) Tier II: same as above with NMT 1750 USP units/L of Pancreatin90010,15, 30 and 4506/18/2007CelecoxibCapsuleII (Paddle)50, 100 and 200 mg: 50 rpm; 400 mg: 75 rpmTier I Medium: 0.04 M tribasic sodium phosphate (pH 12) with 1% SLS. Tier II Initial Medium: 750 mL of simulated gastric fluid, USP (includes pepsin); At 20 minutes, while stirring, add 180 mL of appropriate concentrations of SLS solution (for a final concentration of 1% SLS). Add about 70 mL of 1.2 N NaOH to adjust the pH to 12.Tier I: 1,000 mL Tier II: 750 mL (initial) 1,000 mL (final)10, 20, 30, 45 and 6007/01/2010Table 1: Representative two-tier dissolution method.Environmental FactorsElevated humidity, temperatures and intense light exposure can trigger cross-linking reactions within gelatin-based formulations, resulting in prolonged in vitro dissolution times. The presence of high humidity facilitates direct catalysis of imine formation, a crucial step in cross-linking reactions.Additionally, certain excipients may produce byproducts in moist environments, further promoting cross-linking. For example, corn starch may contain hexamethyl tetramine, which decomposes in humidity, generating ammonia and formaldehyde, thus facilitating cross-linking in gelatin. Moreover, high humidity conditions can induce arginine-arginine cross-linking in gelatin. Elevated temperatures accelerate the rate of cross-linking reactions, hastening the formation of insoluble gelatin networks.Light or ultraviolet (UV)-visible radiation exposure can influence dissolution properties. Intense light exposure correlates with reduced in vitro dissolution rates, adding complexity to the matter of gelatin cross-linking in pharmaceutical products.Chemical FactorsSeveral chemical factors can exacerbate gelatin cross-linking in pharmaceutical formulations (Table 2). HumidityHeatLightExcipients or APIs with carbonyl functional groupAldehydes (furfural, acrolein, formaldehyde, glyceryl aldehyde) and ketonesIminesSugars (glucose and aldose sugar)Oxidising agentPEGs (containing peroxide/aldehydes)Metal ions (colorants/dyes)Sulfated polysaccharides (chondroitin sulfate)Table 2: Causative agents for cross-linking.One prominent contributor is formaldehyde, which can be released from various sources commonly found in formulation excipients. These sources include plasticisers, preservatives and polyethylenated compounds, such as polyethylene glycol (PEG). Interestingly, ethers of PEG, aliphatic alcohols or phenols, polyethylenated glycerides and non-ionic surfactants can all contribute to formaldehyde release, thus promoting the cross-linking of gelatin. PEGs, frequently employed as solvents in pharmaceutical formulations, can release low-molecular-weight aldehydes when exposed to aerobic conditions, thereby further enhancing gelatin cross-linking. Additionally, aldehydes such as furfural, commonly found in bottles containing rayon coils, have been demonstrated to react with gelatin, resulting in the formation of insoluble cross-linked products.To confirm whether gelatin cross-linking has occurred, instrumental techniques such as various spectroscopies have been applied, including nuclear magnetic resonance (NMR), UV spectroscopy using 2, 4, 6-trinitrobenzene sulfonic acid (TNBS) assay, fluorescence spectrophotometry (FS), near infrared (NIR) and Fourier transform-infrared (FT-IR). However, it is important to note that these spectroscopic techniques may have limitations for identifying cross-linking in gelatin capsule shells when the formulations experience dissolution slowdown due to stress tests in stability studies or a long-time storage of marketed formulations.STRATEGIES TO MITIGATE THE CHALLENGE POSED BY CROSS-LINKING IN GELATIN-BASED FORMULATIONSOvercoming the challenge of cross-linking in a dissolution study is crucial for innovators facing hurdles in the in vitro evaluation of gelatin formulations. Fortunately, there are several ways to mitigate the issue of cross-linking within the formulation. One such approach involves leveraging different grades of gelatin, each exhibiting distinct behaviours regarding cross-linking. Notably, type B gelatin demonstrates reduced cross-linking compared with type A gelatin.Another effective approach involves inhibiting the formation of aldehydes, which are crucial catalysts for cross-linking in capsules. Compounds such as lysine, phenylalanine, glutamine, p-aminobenzoic acid and glycine serve as potent scavengers for carbonyl compounds, obstructing aldehyde interaction with the gelatin shell and thereby significantly reducing cross-linking. Using glycine to scavenge aldehydes in the formulation effectively neutralises reactive aldehydic functional groups, preventing further cross-linking. Furthermore, combining glycine with citric acid proves highly effective, offering dual benefits by scavenging aldehydes and facilitating pH manipulation within the formulation.Other inhibitors, such as semicarbazide, piperidine and hydrochloride, can also modify capsule properties, effectively inhibiting cross-linking. An alternative approach involves using aldehyde-free excipients, presenting a promising avenue for tackling the dissolution challenge. Importantly, safeguarding formulations against moisture, temperature fluctuations and light exposure will also play a pivotal role in maintaining stability and preventing undesirable cross-linking reactions.A collaborative effort between the US FDA’s CDER, the United States Pharmacopeia (USP) and academia in the early 1990s yielded valuable insights into gelatin capsule non-compliance during dissolution tests and its impact on bioavailability.1 Notably, while cross-linking primarily occurs in vitro, the behaviour shifts markedly during in vivo testing. Cross-linked capsules face minimal hurdles in vivo, suggesting a divergence between laboratory and real-world outcomes. This is due to the presence of the enzymes in the gastrointestinal (GI) environment acting as biological scissors, effectively breaking down the cross-linked bonds in capsule shells.This research led to the development of two-tier dissolution testing, which incorporates enzymes into the dissolution medium in some cases to account for potential in vivo enzyme activity, highlighting the importance of considering both in vitro and in vivo data when evaluating drug delivery systems. The USP two-tier dissolution method offers a standardised approach for handling formulations that fail initial dissolution assessments. This methodology aligns well with bioequivalence studies, streamlining processes and reducing associated time and costs.The USP General Chapters Dissolution <711>and Disintegration and Dissolution of Dietary Supplements <2040> offer provisions for incorporating enzymes into dissolution media when dosage forms fail to meet dissolution acceptance criteria due to gelatin cross-linking. More than 25 pharmaceutical products have used two-tier dissolution methods, as per the FDA’s dissolution database and USP standards (Table 1). In particular, GI enzymes such as pepsin and pancreatin have proven effective in breaking down cross-linked gelatin within the stomach, operating within specific pH ranges to optimise protease activity. By integrating these enzymes into dissolution studies, the observed slow drug release in vitro can be addressed effectively. This strategic inclusion ensures that dissolution assessments accurately reflect the intended performance of the formulation, aligning with regulatory standards and facilitating robust evaluation of product efficacy.The implementation of two-tier dissolution testing – primarily introduced in the First Supplement of USP 24 – involves the strategic addition of enzymes to dissolution media. Pepsin, added to acidic mediums or water, aims for an activity level of 750,000 units per litre or less. However, it demonstrates optimal proteolytic activity up to pH 4 and diminishes above pH 5.5, rendering it unsuitable for two-tier dissolution testing when the medium exceeds pH 4.On the other hand, pancreatin USP, included in mediums at or above pH 6.8, targets a protease activity level of not exceeding 1,750 units per litre. Pancreatin, renowned for its wide substrate specificity, boasts enzymes such as trypsin, α-chymotrypsin, carboxypeptidase, lipase and amylase, enabling it to hydrolyse proteins, fats and polysaccharides effectively. With a favourable proteolytic activity range around pH 6–8, pancreatin presents a versatile option for addressing gelatin cross-linking during dissolution testing.While pepsin and pancreatin offer valuable solutions for in vitro dissolution challenges, it is important to acknowledge their limitations in mimicking in vivo conditions fully. Factors such as the presence of bile salts and gastric motility, crucial in vivo mechanisms, are challenging to replicate accurately in routine dissolution testing. At this point, enzymes such as papain and bromelain, derived from papaya and pineapple, respectively, could be considered. These enzymes, not naturally found in the human body, are primarily employed to digest cross-linked gelatin during dissolution tests. Papain, with an optimal pH range of 4–7, and bromelain, optimal at pH 4.5–7.5, both exhibit potent protease activity and can be evaluated using the case in digestive power test, as delineated in the USP monographs.While these remedies offer promise in resolving the cross-linking challenge, careful consideration must be given to the cautionary note regarding the use of other additive media components when designing dissolution media. For example, the inclusion of surfactants such as sodium lauryl sulfate for solubility enhancement can compromise the activity of enzymes, introducing complexities in the two-tier dissolution study (Table 1). In such cases, a prudent approach involves pre-treating cross-linked gelatin capsules with enzyme-containing media devoid of surfactants. This ensures the maintenance of enzymatic activity, thus preserving the accuracy of dissolution testing. By navigating these intricacies thoughtfully, researchers could optimise dissolution protocols to emulate physiological conditions, thus enhancing the reliability of their findings more closely.SUMMARYWhile cross-linking in gelatin-based pharmaceuticals may pose challenges to dissolution during in vitro studies, it is important to note that in vivo dissolution is often unaffected. This is due to the enzymatic activity within the GI tract which digests cross-linking efficiently, aiding dissolution. Nonetheless, despite this natural process, several precautions should be taken to ensure regulatory acceptance of the product.Various strategies exist to prevent cross-linking during the formulation stage. These include tailoring gelatin formulations to specific grades, incorporating cross-linking inhibitors, integrating stability enhancers or exploring alternative excipients less prone to cross-linking. These approaches effectively mitigate cross-linking issues.However, if cross-linking does occur during formulation, strategic use of the USP two-tier dissolution method would be crucial, especially in capsule formulations. Optimising dissolution studies in this manner can enhance pharmaceutical evaluations, supporting the reliability and efficacy of drug development processes. Through these proactive measures, researchers can confidently and precisely navigate the complexities of cross-linking in gelatin-based pharmaceuticals.REFERENCEAikman M et al, “Collaborative development of two-tier dissolution testing for gelatin capsules and gelatin-coated tablets using enzyme-containing media”. Pharmacopeial Forum, Vol 24(5), Sep-Oct 1998. Source: Strategies to mitigate gelatin cross-linking in oral solid drug delivery
Read more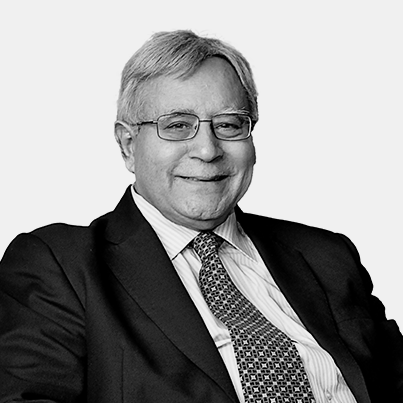
Ajit Singh
Ajit Singh earned his graduation degree from Cambridge University, UK, and post-graduation degree from Harvard Business School, USA. He currently resides in Mumbai, India, and travels widely to study pharmaceutical and allied industries.
Ajit is the Chairman of the ACG Group (formerly known as the Associated Capsules Group of Companies), which is headquartered in Mumbai. He has played a prominent role in the development of the pharmaceutical and allied industries in India and has served as an executive committee member of the Federation of Indian Chambers of Commerce & Industry (FICCI), a regional council member of the Confederation of Indian Industry (CII), Western Region, and other prominent pharmaceutical associations in India. He has also been conferred with prestigious awards for his contributions and thoughtful leadership to the pharmaceutical industry.
Ajit was a founder-member of the Young Presidents’ Organization – India Chapter and the first Indian to be invited to serve on its international board in the USA.
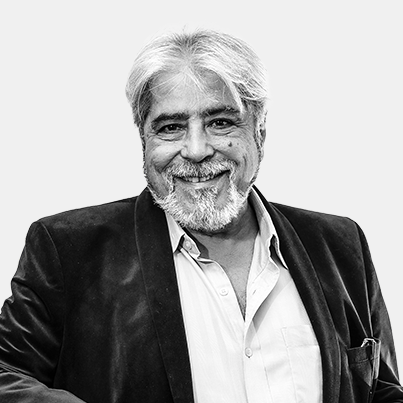
Jasjit Singh
Along with his brother, Ajit, Jasjit started the Associated Capsules Group in Mumbai in 1962.
Jasjit has always been interested in technology – particularly that relating to machine design – and earned a degree in Mechanical Engineering from London University. He has dozens of patents to his credit, and under his leadership the ACG Group has received numerous global awards for technology, excellence and social welfare.
Jasjit has been actively involved with starting new Forums of the Young Presidents’ Organisation. He served as the Chairman of the Mumbai Chapter, and helped found the Kolkata Chapter before becoming a founding President of the World Presidents’ Organisation. Jasjit has also received the Vijay Ratna Award for leadership in Industry, and recognition from UNIDO for his contribution to the fields of pharmaceutical technology and environmental science.
Jasjit’s other interests include self-education, reading, music, collecting rare works of arts and helping young contemporary artists, cooking, and travelling to different parts of the world – especially with his family.
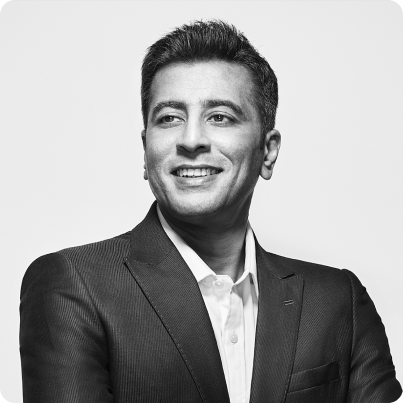
Karan Singh
An organisational psychologist by education, Karan has transformed ACG from a modest Indian business into a world-renowned institution, revolutionising its vision and long-term strategy to ensure global growth. Karan has overseen ACG’s remarkable digital transformation, adopting breakthrough technologies that not only keep medicines safe, affordable, and accessible – but also vastly improve manufacturing and supply chains. Meanwhile, he has led a series of tuck-in acquisitions that ensure ACG pioneers continuously in terms of innovation and scale.
Passionate about converting ideas into growth opportunities, he supports entrepreneurial visions that solve real-world challenges. As an investor and mentor to more than 35 health-tech start-ups, guiding strategy, technology, expertise and networks, Karan seeks to consolidate the next generation of leadership – one that will secure better access and bridge availability across the global health industry.
Karan serves on the India Advisory Board for the India-Brazil Chamber of Commerce, is Co-Chair for FICCI LAC Regional Council, a key advisor to Nasscom, and an active contributor to the Global Lighthouse Network community of the World Economic Forum. Years of keen basketball-playing underpin his leadership, communication, and competitive spirit, and have brought about ACG-NBA Jump, a grassroots programme to give Indian basketballers a global platform.
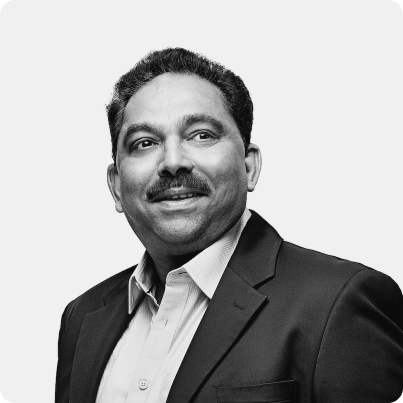
Selwyn Noronha
CEO ACG CAPSULES
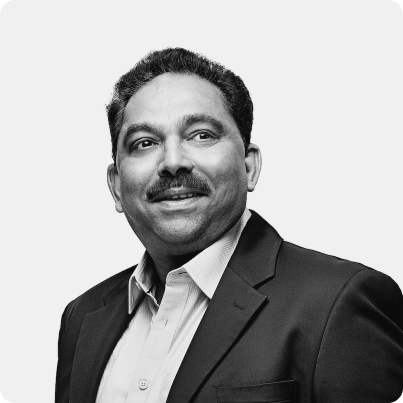
Selwyn Noronha
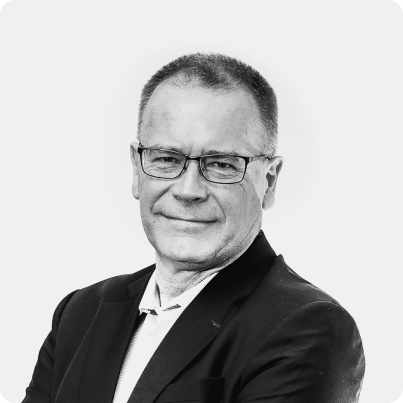
Richard Stedman
CEO ACG ENGINEERING
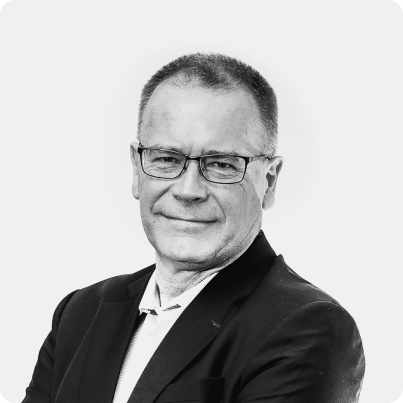
Richard Stedman
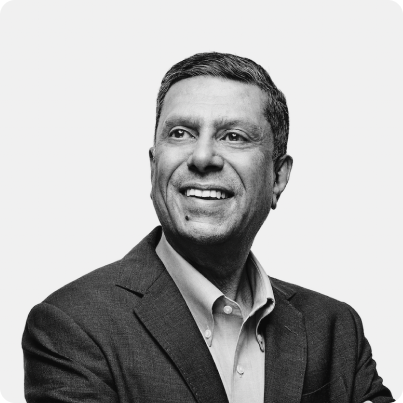
SR Shivshankar
CEO ACG PACKAGING MATERIALS
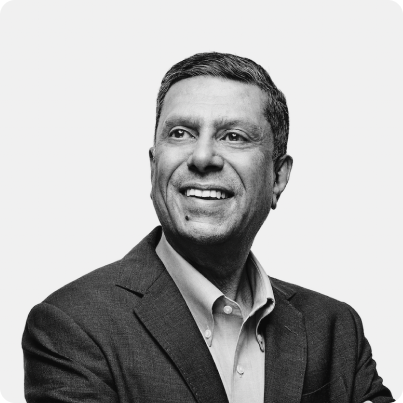
SR Shivshankar
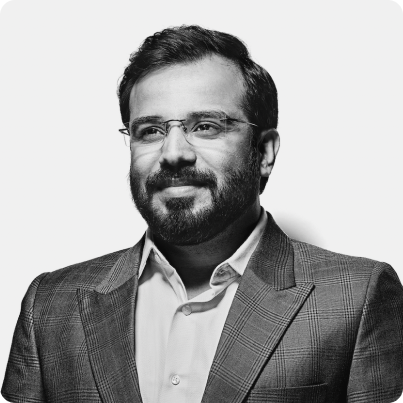
Udit Singh
CEO ACG INSPECTION
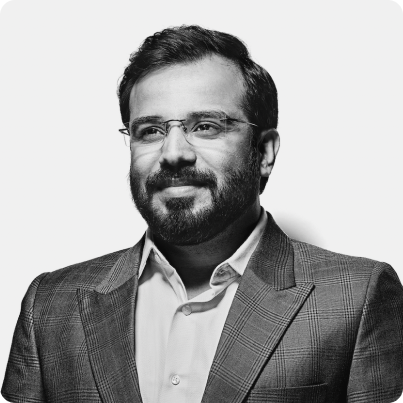
Udit Singh
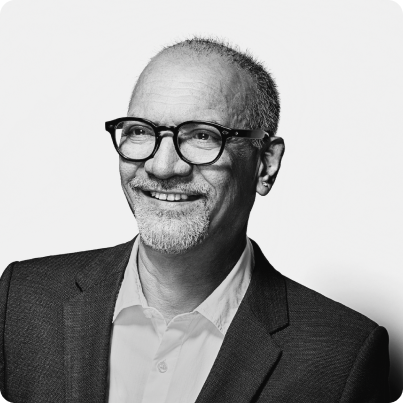
Sunil Jha
Chief Human Resource Officer
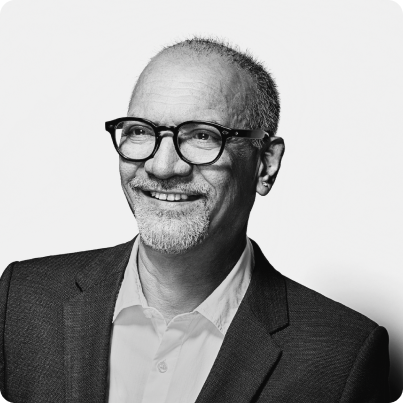
Sunil Jha
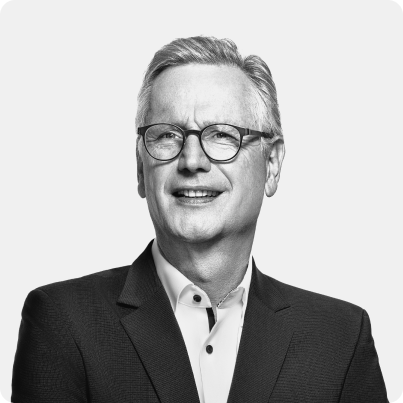
Werner Bongers
CEO SCITECH
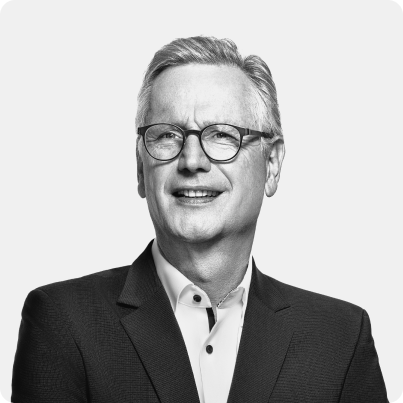
Werner Bongers
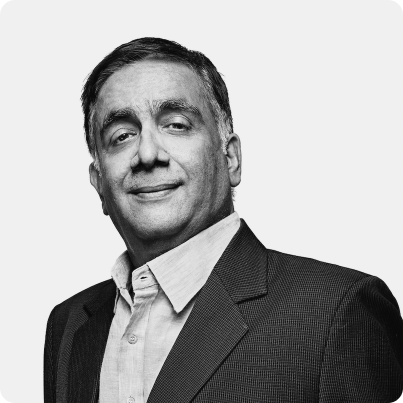
Nitin Desai
Chief Commercial Officer
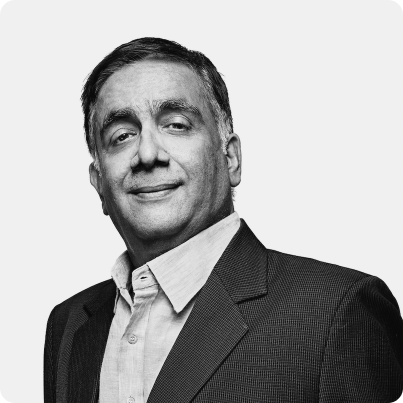
Nitin Desai
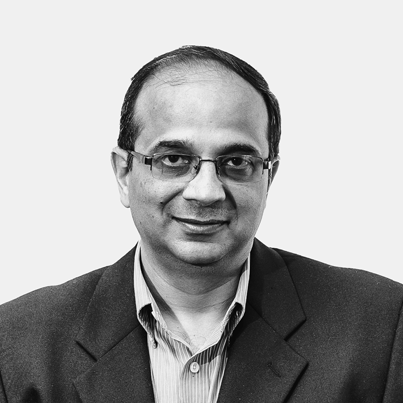
Parag Shah
Chief Financial Officer
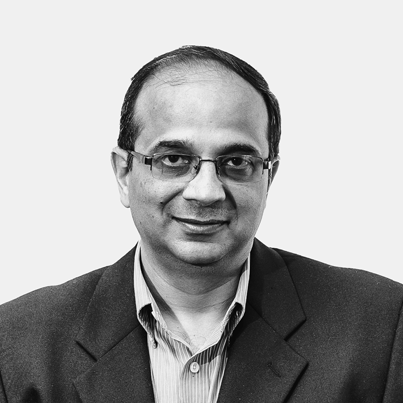
Parag Shah
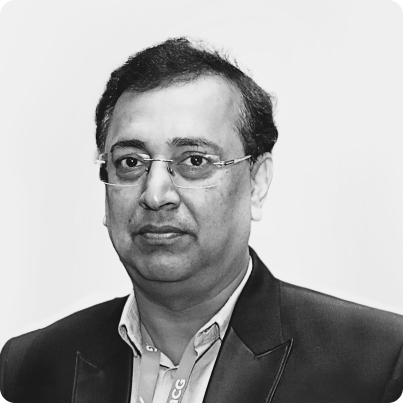
Shankar Gupta
Chief Sales Officer
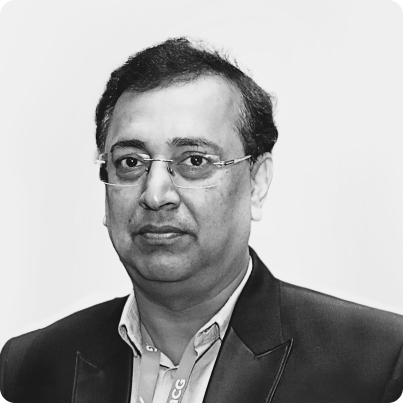
Shankar Gupta
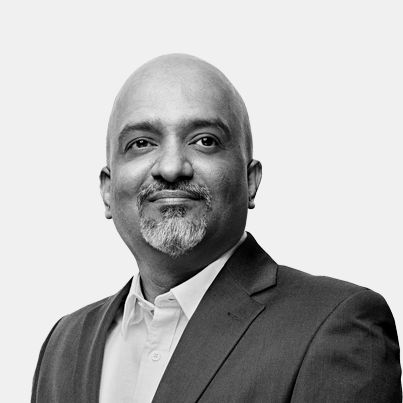
Balajikasiram Sundararajan
Chief Digital Officer
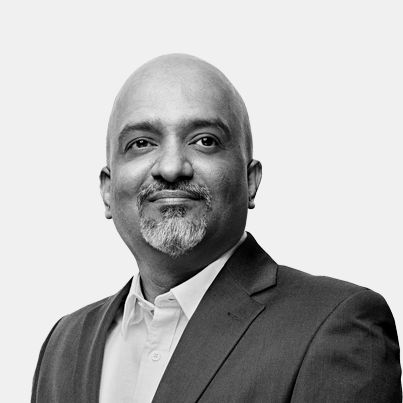
Balajikasiram Sundararajan
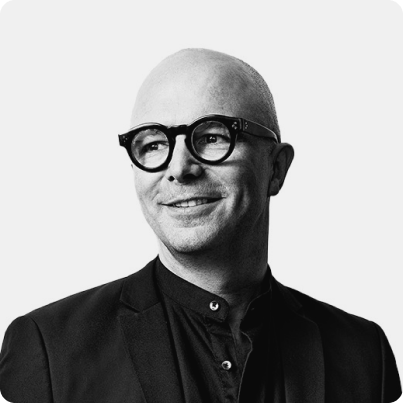
Alexander Robertson
Chief Marketing Officer
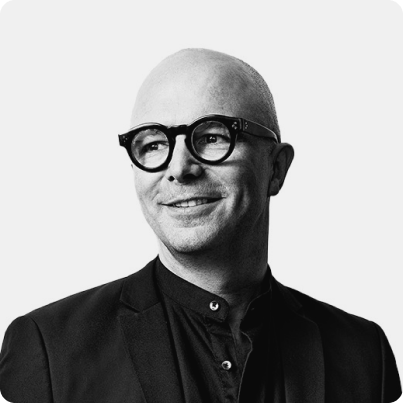
Alexander Robertson
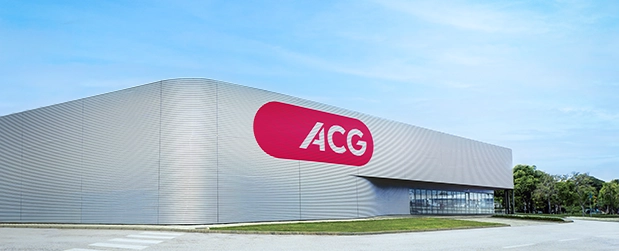
Boilerplate
For over 60 plus years, ACG has been innovating the production solutions for pharmaceutical and nutraceutical companies, that help make people better.
As the world’s most integrated provider of oral dosage products and services, we produce capsules, barrier packaging materials, manufacturing machinery, and visual inspection and traceability solutions. All fully compliant with international standards.
Today, ACG fosters long-term collaborative partnerships with customers in 138 countries across six continents.
Together, we share a common purpose: to solve the world’s greatest health challenges and make it better for everybody we serve.