We value our partnerships with the media and welcome any inquiries about the ACG Group. Please use the resources on this page, or if you have any specific queries please reach out to the media contact listed below.
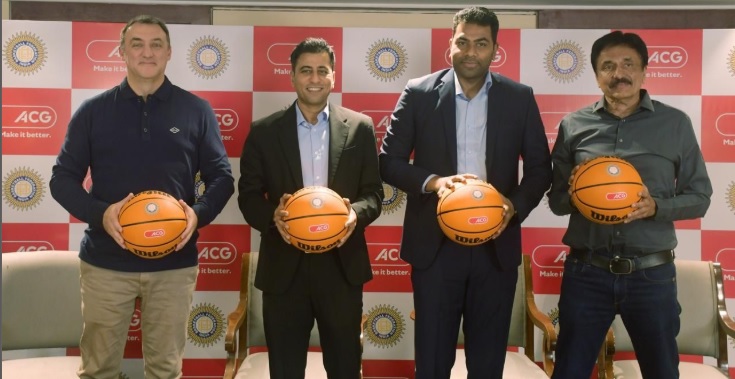
India's Basketball Revolution Begins: ACG launches India's First Professional Basketball League in association with BFI
Mumbai, June 6, 2025: Marking a transformative moment for Indian sports, ACG Sports Private Limited, has announced the launch of India’s first professional basketball league in association with the Basketball Federation of India (BFI). This groundbreaking initiative will feature structured competitive league in 5x5 and 3x3 formats for both men and women, establishing a comprehensive professional ecosystem that opens the door for athletes across the country to pursue basketball as a viable career.Designed to redefine how the sport is played, experienced, and supported in India, the league aims to shift basketball from a niche discipline into a mainstream pursuit. It will serve as a long-term catalyst for India’s presence on the global basketball stage, backed by world-class infrastructure, holistic athlete development, and robust community engagement.The league is being driven by ACG Sports Pvt. Ltd., a division of ACG, a global leader in integrated manufacturing solutions for the pharmaceutical and nutraceutical industries. Leveraging ACG’s deep-rooted commitment to societal advancement, this initiative represents a natural extension of its decade-long investment in grassroots basketball programs.To guide the league’s global strategy and operations, Mr. Jeremy Loeliger, Former CEO & Commissioner of Australia’s National Basketball League (NBL), has been appointed Director of ACG Sports. In his new role, Loeliger will lead the development of the league’s blueprint, bringing international standards of governance, competition, and commercial innovation to the Indian shores.“Basketball represents more than just a sport – it is a vehicle for building character, leadership, and opportunity," said Mr. Karan Singh, Managing Director of ACG. "Our decade-long journey, beginning with grassroots initiatives has focused on systematically making basketball accessible across India while building the professional pathways that young athletes need to thrive."He further added, "Our vision for this professional basketball league is to establish a self-sustaining ecosystem where every child with passion and talent can see a viable future in basketball in India. We're grateful for the partnership with BFI in making this dream a reality. While this is a commendable first step, we know that building a thriving basketball ecosystem will require sustained effort and collective support to reach its full potential.”ACG’s leadership role in this initiative goes far beyond league operations. As part of its long-term strategy, ACG will launch India’s first fully residential high-performance centre within the year. The academy will feature world-class facilities, attract top coaching talent from the U.S. and Australia, and offer comprehensive training programmes for players, coaches, and referees. Nutrition, mental wellness, and academic balance will be integral to the curriculum – ensuring holistic development of future stars.Mr. Aadhav Arjuna, President of the Basketball Federation of India, stated: “This partnership with ACG is unlike anything we’ve seen before. It is driven by vision, structured for long-term impact, and rooted in a clear understanding of what Indian basketball truly needs. We’re building not just visibility, but real momentum and global credibility. Our vision is to win medals at the Asian Games and Olympics”Mr. Kulvinder Singh Gill, Secretary General of the Basketball Federation of India, stated: “This league will unlock new opportunities for young Indian talent to grow, compete professionally, and gain invaluable exposure alongside international players and coaches.”The complete league framework including team structures, competition formats, player eligibility, and governance models – is currently in development with input from global basketball experts and key industry stakeholders. Detailed announcements on participation guidelines, venue requirements, and operational protocols will follow in a phased rollout.In the coming months, the newly formed League Council will begin overseeing standards and operations, while nationwide scouting initiatives, customised athlete development tracks, and dynamic fan engagement programs will begin laying the foundation for a vibrant, inclusive, and commercially sustainable basketball culture in India.About Basketball Federation of India (BFI)The Basketball Federation of India (BFI) is the governing and controlling body of basketball in India. It is responsible for the development and promotion of the sports at all levels. BFI manages all the national-level basketball operations in India.First national level tournaments were organized in India in 1934. The India national basketball team became a member of FIBA in 1936. The governing body, BFI, was formed in 1950. Mr. Aadhav Arjuna is the President of Basketball Federation of India.About ACGFor over 60 plus years, ACG has been innovating the production solutions for pharmaceutical and nutraceutical companies, that help make people better.As the world’s most integrated provider of oral dosage products and services, we produce capsules, barrier packaging materials, manufacturing machinery, and visual inspection and traceability solutions. All fully compliant with international standards.Today, ACG fosters long-term collaborative partnerships with customers in 138 countries across six continents.Together, we share a common purpose: to solve the world’s greatest health challenges and make it better for everybody we serve.ACG Sports Private Limited is a wholly owned subsidiary of ACG, and while it operates in a different sector, it is firmly grounded in the same institutional principles of precision, scalability, and long-term value creation.For more information, please contact the ACG media relations team:madhurima.chakraborty@acg-world.com
Read more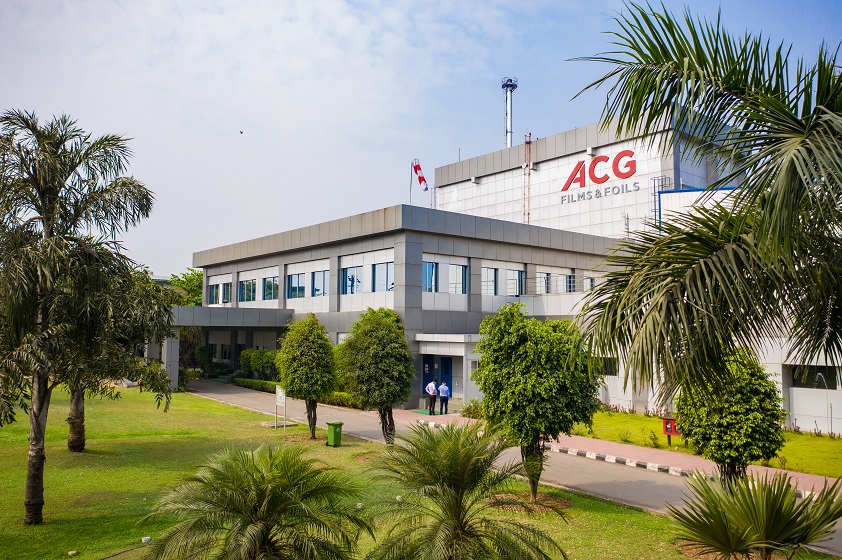
ACG Packaging Materials GHG Commitment Validated and Approved by SBTi
ACG Packaging Materials, a leading global supplier of integrated manufacturing solutions for the pharmaceutical and nutraceutical industries, has taken a significant step forward in its sustainability journey as the Science Based Targets initiative (SBTi) officially validated the company’s greenhouse gas (GHG) emission reduction targets. This validation aligns with ACG’s core philosophy of Making it Better, reinforcing its commitment to impactful progress toward a sustainable future.ACG Packaging Materials has committed to reducing absolute Scope 1 and 2 GHG emissions by 90%. The company has also committed to reducing Scope 3 GHG emissions from purchased goods and services, fuel and energy-related activities, and upstream transportation and distribution by 97% per tonne of products produced within the same timeframe.Speaking on this milestone, Karan Singh, Managing Director of ACG, said, “At ACG, we recognise that the future of the pharmaceutical and nutraceutical industries depends on our ability to innovate responsibly and operate sustainably. This validation provides us with a clear, science-backed framework to drive meaningful progress in reducing our environmental impact. As we move forward, our focus will be on integrating sustainable practices across our operations, investing in advanced technologies, and collaborating with stakeholders to build a resilient, low-carbon future. This milestone is a testament to our dedication to making it better while ensuring that our industry remains aligned with global climate goals”Mr. Shivshankar S.R, CEO of ACG Packaging Materials, “The SBTi validation solidifies our commitment to a business model that thrives in a carbon-conscious future. We're not simply aiming for incremental improvements; we're undertaking a fundamental shift in how we operate. Our ambitious interim targets—reducing absolute Scope 1 and 2 emissions by 54.6% and Scope 3 emissions by 61.07% per tonne of products by FY2033—demonstrate our dedication to tangible progress. This commitment enhances our ability to attract sustainability-focused investors, fortifies our supply chain, and establishes ACG as a leader in responsible manufacturing”Sunil Kumar, Head of CSR and Sustainability at ACG said, “This validation is a testament to our unwavering commitment to environmental stewardship and social responsibility. At ACG, we believe that business success is intrinsically linked to the well-being of our planet and communities. Our focus now is on expanding our sustainability initiatives beyond our operations, engaging our employees, and partnering with local communities to create a lasting positive impact. We are dedicated to building a more sustainable and equitable future for all”The Science Based Targets initiative (SBTi), a collaboration between the Carbon Disclosure Project (CDP), United Nations Global Compact (UNGC), World Resources Institute (WRI), and Worldwide Fund (WWF), provides a globally recognized framework for companies to set GHG reduction targets aligned with climate science. It specifies how much and how quickly emissions must be reduced to limit global warming to well below 1.5°C above pre-industrial levels.
Read more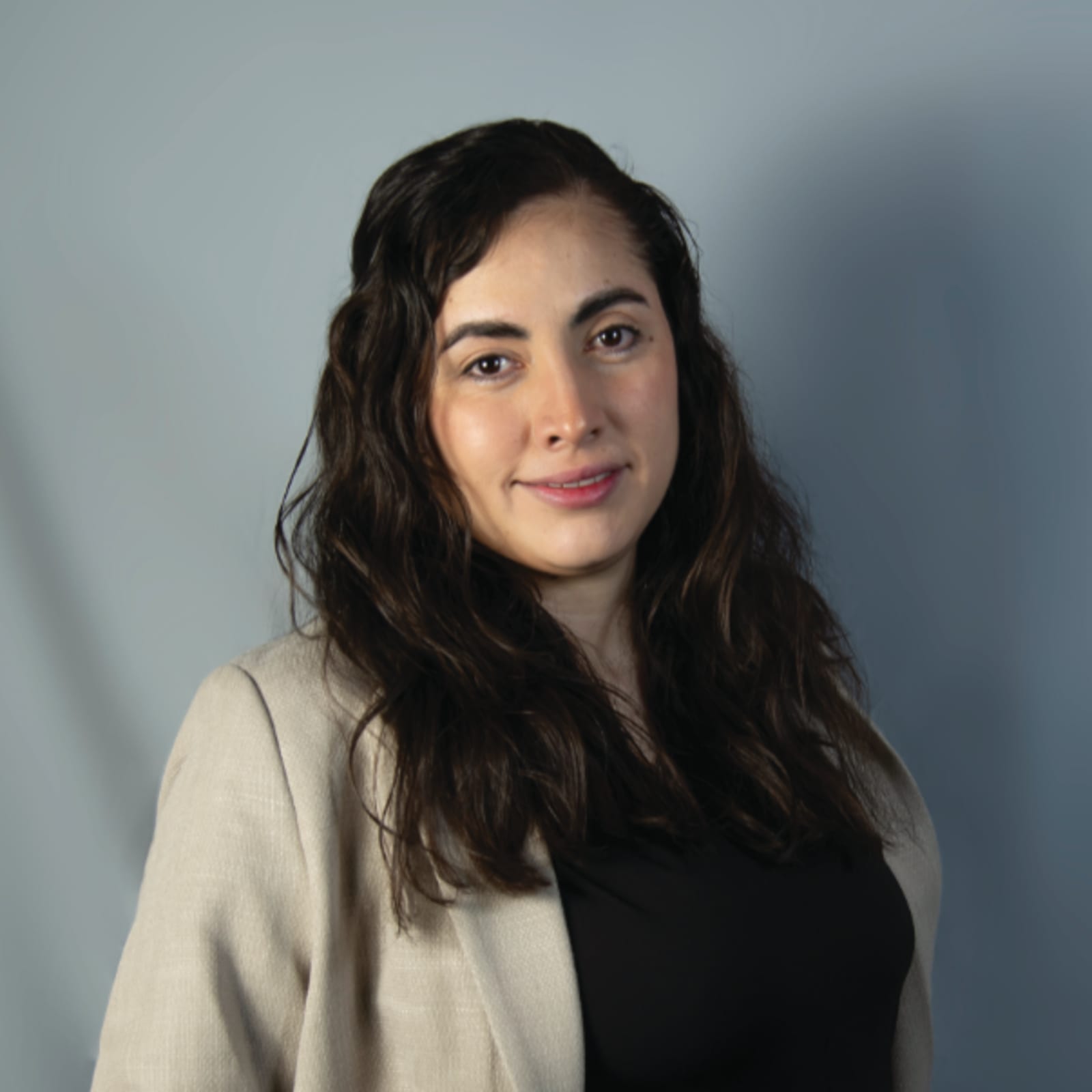
ACG to boost Mexico presence with appointment of Jessica Alfaro
ACG Engineering, a division of ACG, the world's only integrated pharmaceutical solutions and manufacturing company, is delighted to announce the appointment of Jessica Alfaro as territory sales manager for the Mexico region, as the company seeks to vastly increase its presence in the territory. In her new role, Jessica Alfaro will be responsible for promoting ACG’s portfolio of process and packaging machinery in Mexico, establishing new bonds with customers through the commitment of providing integral solutions to improve their processes. With a passion for engineering, Jessica previously worked as a sales engineer for Nicolás, Sven, Pacheco Y Andresen, Design and Engineering. Her responsibilities included the monitoring of technical specifications and industry standards, as well as the continuous development of the overall product offering. She also led board sessions, assigning requirements to valid use cases that highlighted the capabilities of the product. In addition, she worked closely with customers and the engineering team to determine the needs of the process and the requirements of the system. Commenting on the appointment, John Carey, vice-president of Sales at ACG Engineering, said: “We’re delighted to welcome Jessica into this pivotal new role. ACG is currently placing real focus and investment in the Mexico region for our process and packing machinery supporting both pharmaceutical and nutraceutical manufacturers with state-of-the-art technologies. We believe her experience and dedication will play a key part in building strong customer relations in the area.”Jessica Alfaro added: “I am delighted to be joining ACG, and embracing the challenges associated with gaining a deep understanding of our clients and providing them with the best solutions to help drive their business success. “I am excited by the idea of applying my analytical skills to design efficient and sustainable processes. My chemical engineering background gives me the opportunity to merge my passions for problem solving and teamwork, allowing me to contribute to the development of technologies and solutions that have a positive impact on the world around us.”About ACGFor over sixty years, ACG has been innovating the production solutions for pharmaceutical and nutraceutical companies, that help make people better. As the world’s most integrated provider of oral dosage products and services, we produce capsules, barrier packaging materials, manufacturing machinery, and visual inspection and traceability solutions. All fully compliant with international standards.Today, ACG fosters long-term collaborative partnerships with customers in 138 countries across six continents. Together, we share a common purpose: to solve the world’s greatest health challenges and make it better for everybody we serve. For more information, please contact the ACG media relations team:madhurima.chakraborty@acg-world.com
Read more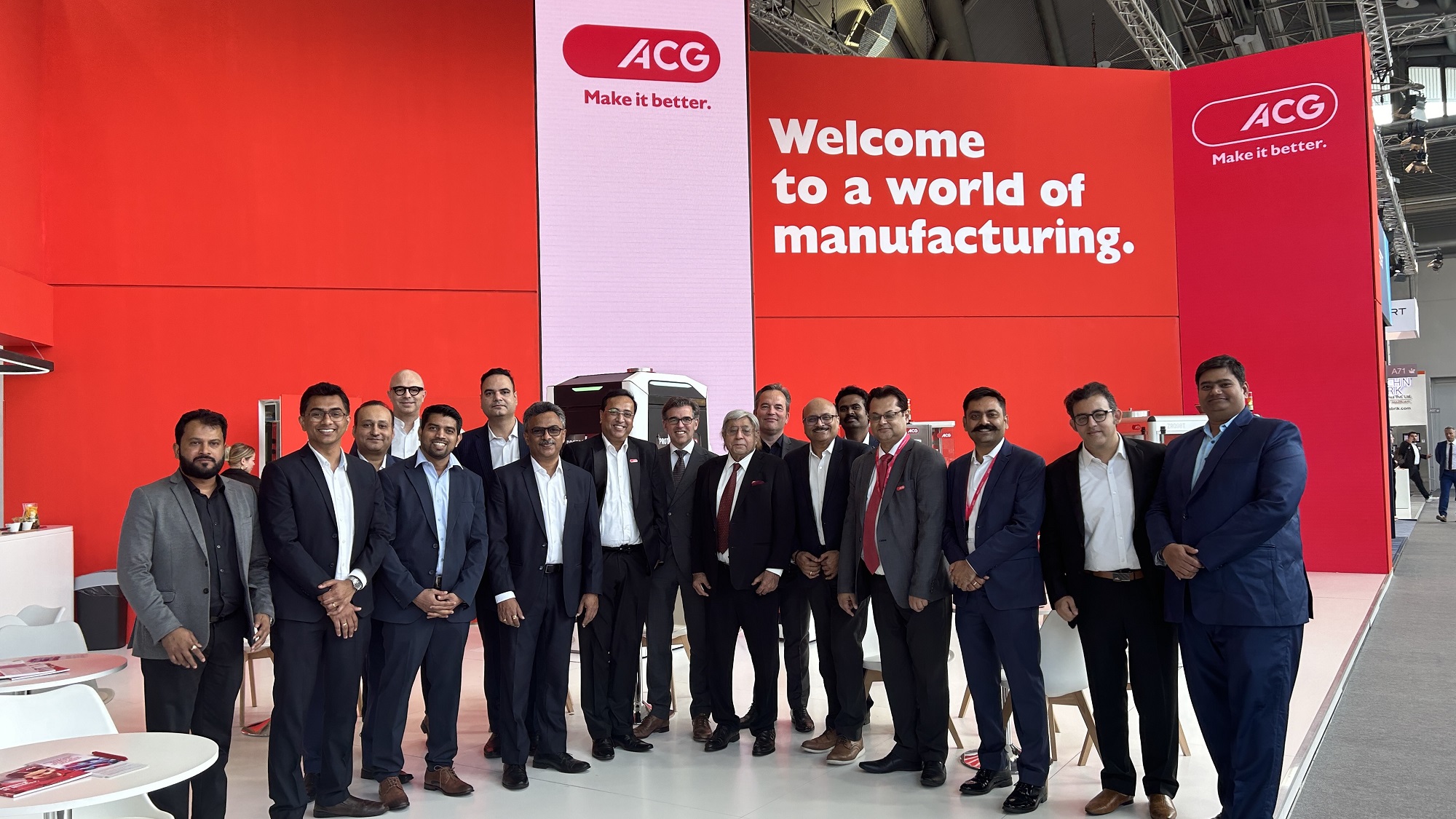
ACHEMA 2024: ACG Engineering on a mission to collectively ‘Make it Better’ World’s largest integrated supplier to the solid dosage manufacturing industry to display wide range of engineering and capsules products
At ACHEMA 2024 ACG Engineering, which provides end-to-end pharmaceutical engineering solutions,will be displaying its broadest range of products to date – underlining its commitment to ‘Making it Better’ for the industry and patients alike.The all-encompassing machines displayed will include the QUEST FB I, which is a highly versatile 'plug and play' fluid-bed unit for lab-scale feasibility studies. Also on show will be the ZRO 90T - a high-yield capsule filler. As will be the ACCURA 100FF - ACG's precision capsule checkweigher, suited for medium to large production batches with a capacity of 100,000 capsules per hour. Also on display will be the PROTAB 300 – a single rotary tablet press, which is suitable for R&D, small and medium-batch production, making scalability far easier, and the SECURECOAT TC III tablet coater, designed with operator safety and for use with highly potent active pharmaceutical ingredients (HPAPIs).Borja Guerra, vice president of international sales at ACG Engineering, said: “At ACG, we deliver efficient cutting-edge technology and a highly consistent ROI ratio for our global customer base, because we actively listen to them and their needs and take a collective approach towards ‘Making it Better’.“By aligning our shared strength and cross-divisional synergies with our Capsule and Films and Foils business units we are able to offer a whole world of different and highly targeted products and services – supporting large pharmaceutical companies and generic manufacturers with equal focus.”“We are really looking forward to ACHEMA 20024 and meeting with the industry to share knowledge and insights and to hopefully forge some new and exciting partnerships, continuing the expansion of ACG’s global footprint.”ACG will be exhibiting on stand A71 in Hall 3.1, between 10-14 June in Frankfurt.-Ends-About ACG For over 60 plus years, ACG has been innovating the production solutions for pharmaceutical and nutraceutical companies, that help make people better.As the world’s most integrated provider of oral dosage products and services, we produce capsules, barrier packaging materials, manufacturing machinery, and visual inspection and traceability solutions. All fully compliant with international standards.Today, ACG fosters long-term collaborative partnerships with customers in 138 countries across six continents.Together, we share a common purpose: to solve the world’s greatest health challenges and make it better for everybody we serve. For more information, please contact the ACG media relations team:madhurima.chakraborty@acg-world.com
Read more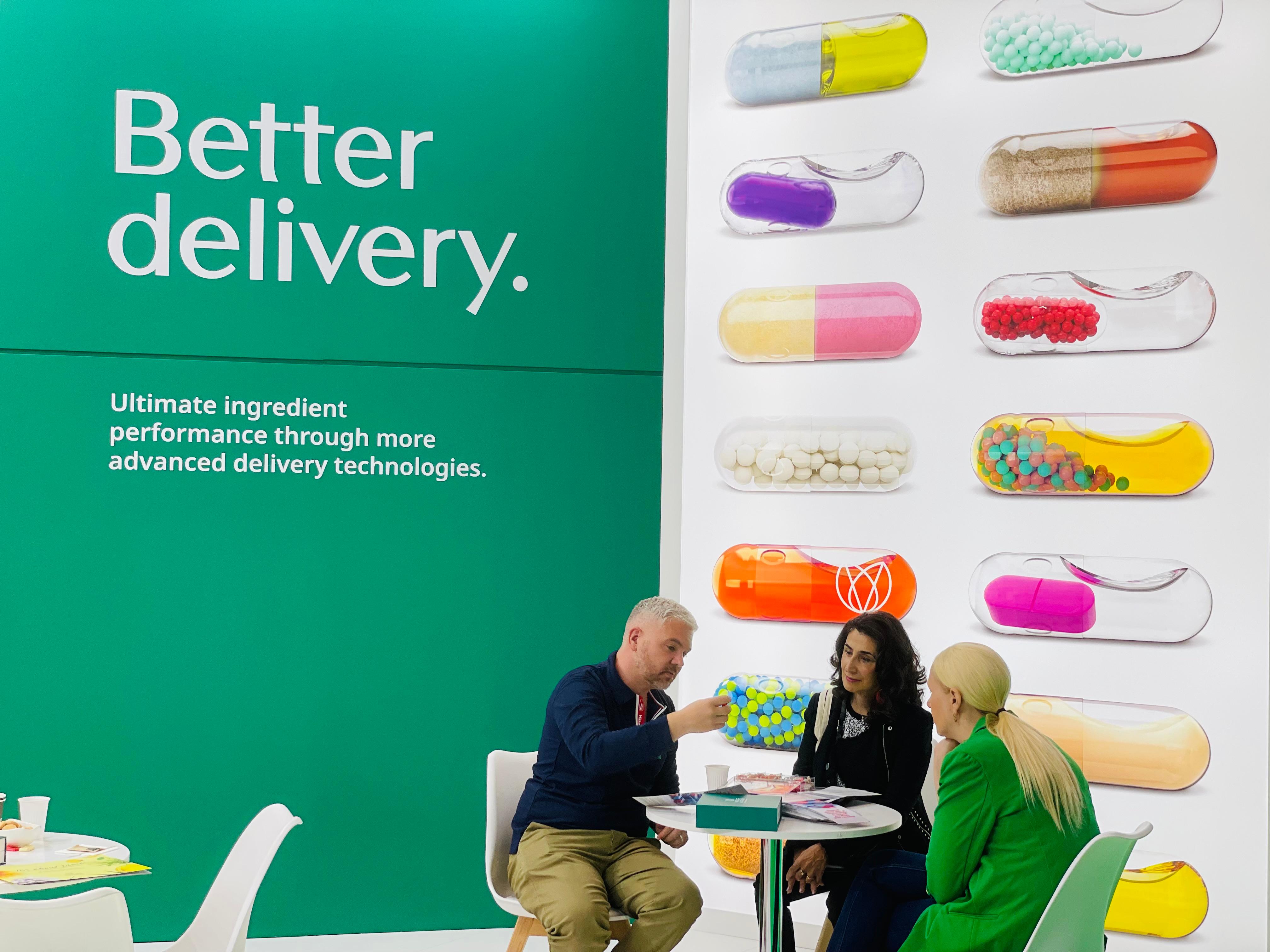
Vantage Nutrition to champion ‘better delivery’ at Vitafoods Europe 2024
At this year’s Vitafoods Europe, Vantage Nutrition (an ACG group company), will be showcasing and championing the term ‘better delivery’. With a real focus on innovation, the team will be debuting the outstanding beadlet technology, a complete product offering ultimate ingredient performance.Other ACG Capsules products on show will include ACGcaps™ H+, the world's first independently certified* ‘Clean Label' eco-friendly capsule, which is made using thermogelation technology (water and cellulose only). Alongside will be the ACGcaps™ TSafe opaque and TiO2-free clean capsules, with the enhanced version offering flexibility with pigmentation options.Aaron Quinn, head of business development at Vantage Nutrition – Europe, commented: “We know that the world’s healthiest products demand the world’s cleanest capsules performance through more advanced technologies. Through our innovations, we are committed to supporting nutraceutical brands when it comes to time consuming and costly R&D.“With the development of beadlet technology we are able to offer ultimate ingredient performance and enhanced delivery. Beadlets release ingredients over time, boost absorption and improve bioavailability. And by working with one supplier, manufacturers can ensure they have full control over all processes, with the 360 service – ensuring better results and enhanced uptake.”ACG is the world’s largest integrated supplier of pharmaceutical and nutraceutical solid dosage products and services. Along with the commitment to delivering integrated solutions and cutting-edge technology, Vantage Nutrition aims to provide the most comprehensive and advanced multiphase solutions to customers globally. The team’s focus in on turning product ideas into reality fast – helping companies enable, enhance, and differentiate nutra brands - from a full-service partnership to specific value additions.ACG will be exhibiting on stand H37, between 14-16 May in Geneva.* Certifications are applicable to certain colours and/or variants.About ACG For over 60 plus years, ACG has been innovating the production solutions for pharmaceutical and nutraceutical companies, that help make people better.As the world’s most integrated provider of oral dosage products and services, we produce capsules, barrier packaging materials, manufacturing machinery, and visual inspection and traceability solutions. All fully compliant with international standards.Today, ACG fosters long-term collaborative partnerships with customers in 138 countries across six continents.Together, we share a common purpose: to solve the world’s greatest health challenges and make it better for everybody we serve. For more information, please contact the ACG media relations team:madhurima.chakraborty@acg-world.com
Read more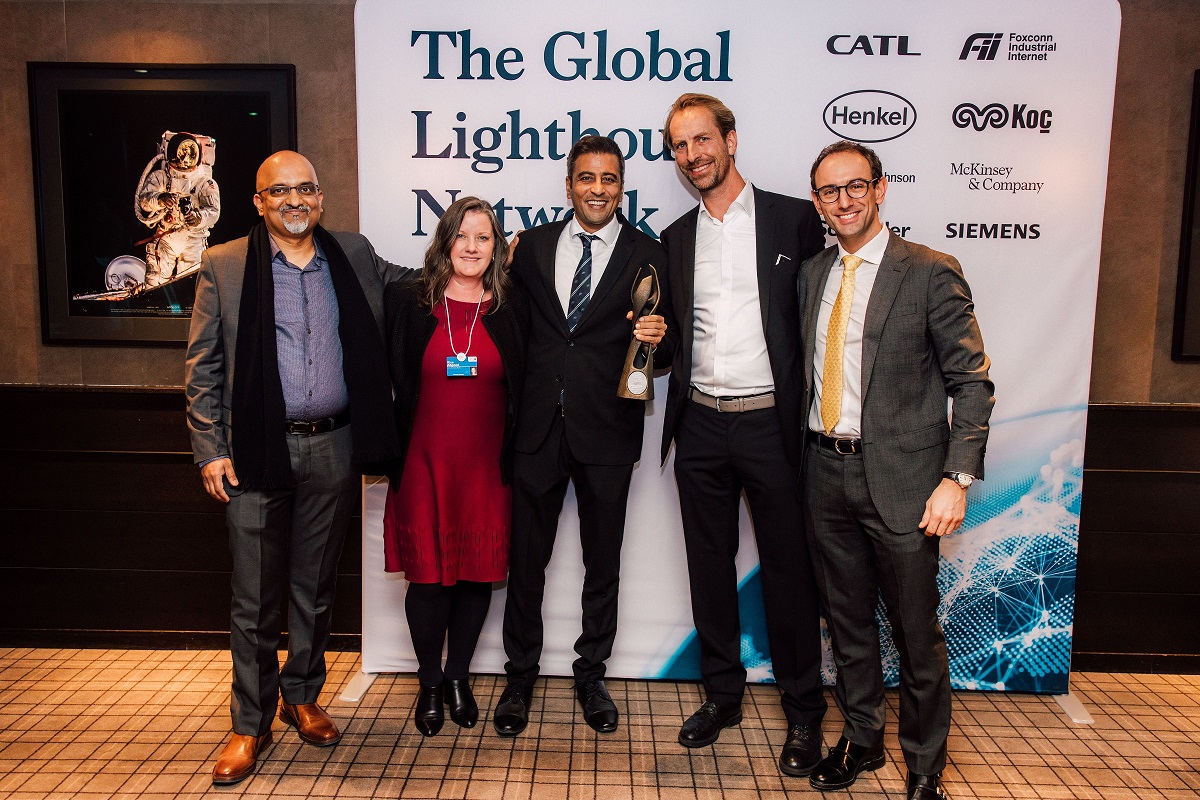
ACG Becomes the World’s First Capsule Manufacturing Factory to Join the Global Lighthouse Network Community 2023-24
ACG Capsules Pithampur, India is ACG’s 1st lighthouse to join the community Karan Singh, Managing Director and Balajikasiram Sundararajan, Chief Digital Officer attend the Global Light House Network ceremony in Davos to collect the award. ACG, the world's largest integrated supplier and service provider to pharmaceutical industry celebrated the inclusion of its capsule manufacturing facility in Pithampur, India, into the esteemed Global Lighthouse Network (GLN) by the World Economic Forum at the 54th Annual Davos Summit. The World Economic Forum’s Global Lighthouse Network has acknowledged the exemplary integration of Fourth Industrial Revolution (4IR) technologies, including artificial intelligence and big data analytics, by select factories globally. These facilities have been distinguished for their commitment to enhancing efficiency, fostering sustainable development, and simultaneously advancing their workforce’s skills and safeguarding the environment.Upon receiving the award, Mr. Karan Singh, Managing Director, said: “I am delighted to receive this recognition on behalf of my team. For me the most unforgettable part of our journey wasn't any technology or efficiency milestone, but the incredible team that made it all possible. Just ordinary people, united towards one goal, bringing about innovative collaborations to push boundaries of what is possible.” He added: “One of the stand-out features of our application was the Gen-AI integration. Something that was done in the less than two weeks. In between all the debate on what Gen-AI can do to humans it is a beautiful reminder that ‘technology is brilliant, but humans drive the change’. Let's remember that!”ACG operates across 138 countries in six continents and has positioned itself as a leader in the pharmaceutical sector by focusing on high-quality capsule production, increasing responsiveness, improving production yields, and boosting workforce efficiency. The company produces billions of capsules annually and has implemented over 25 innovative applications of 4IR technologies, including the industrial internet of things (IIoT), machine learning (ML), deep learning (DL), digital twins, extended reality, and generative AI.Selwyn Noronha, CEO, ACG Capsules, added: “We are extremely proud of our first factory lighthouse. From its inception the facility has pioneered in its field, but this latest honour recognises the excellence in adopting AI at speed and scale.“Our continued future-focused approach sets new benchmarks in quality and innovation, with the aim of ensuring maximum benefit for customers, regulators and the entire pharmaceutical ecosystem.”About Global Lighthouse Network Global Lighthouse Network is a collaborative platform bringing together forward-thinking manufacturers leading the charge in adopting Fourth Industrial Revolution technologies. Leveraging innovations like artificial intelligence, 3D-printing, and big data analytics, Lighthouses drive efficiency, competitiveness, and transformative business models at scale, fostering economic growth while championing workforce augmentation, environmental protection and providing a collaborative learning journey for all-sized manufacturers globally. The Global Lighthouse Network is a World Economic Forum initiative co-founded with McKinsey & Company and counselled by an Advisory Board of industry leaders, including Contemporary Amperex Technology (CATL), Foxconn Industrial Internet, Henkel, Johnson & Johnson, Koç Holdings, Schneider Electric, and Siemens. Factories and value chains that join the network are designated by an independent panel of experts.About ACG For over 60 plus years, ACG has been innovating the production solutions for pharmaceutical and nutraceutical companies, that help make people better. As the world’s most integrated provider of oral dosage products and services, we produce capsules, barrier packaging materials, manufacturing machinery, and visual inspection and traceability solutions. All fully compliant with international standards. Today, ACG fosters long-term collaborative partnerships with customers in 138 countries across six continents. Together, we share a common purpose: to solve the world’s greatest health challenges and make it better for everybody we serve.For more information, please contact the ACG media relations team:madhurima.chakraborty@acg-world.com
Read more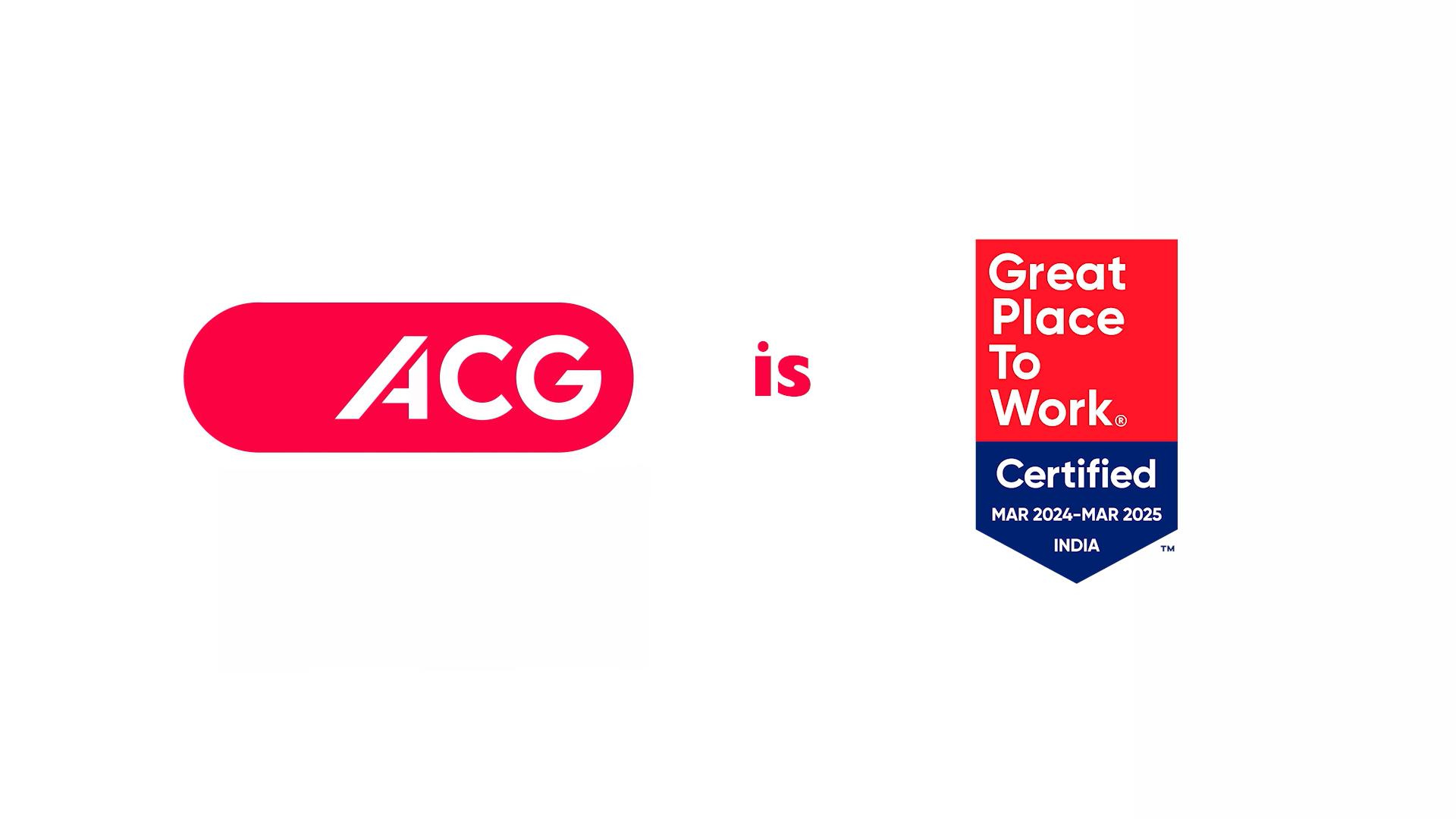
ACG awarded ‘Great Place To Work’ certification for a fourth consecutive year
ACG, the world’s largest integrated supplier and service provider to the pharmaceutical industry, is delighted to announce that for the fourth consecutive year, it has achieved the ‘Great Place To Work’ certification. This certification recognises employers who create an outstanding employee experience.Within ACG, five business units (Capsules, Corporate, Scitech – Research and Development Centre, Machinery, and Inspection), have been certified as a ‘Great Place to Work’. The comprehensive study, spanning five locations in India, encompassed approximately 3000 associates across management and plant categories. The process entailed a thorough survey based on key levers that define an organization's culture.Nikita Panchal, Group Head Talent, OD and DEI at ACG, said: “Winning this award for the fourth consecutive year fills me with pride and gratitude, recognizing the collective effort of our associates. It serves as a reminder of our commitment to excellence and the fact that institution-building is at the centre of all our actions as an organization.“ACG fosters collaboration by nurturing teamwork and effective communication. We care for our associates and the business community through support initiatives, and we remain progressive by supporting change and innovation. Our associates are encouraged to embrace our values, seize opportunities for growth and contribute their unique talents to shape a bright future together.”Sunil Jha, Group CHRO of ACG Group, added: “ACG thrives on collaboration through cross-functional teamwork, and – at all times – we prioritize the wellbeing of our associates.“Winning this award is incredibly gratifying and I am appreciative that all our associates have worked together to make this happen.”-Ends-About ACGFor over sixty years, ACG has been innovating the production solutions for pharmaceutical and nutraceutical companies, that help make people better. As the world’s most integrated provider of oral dosage products and services, we produce capsules, barrier packaging materials, manufacturing machinery, and visual inspection and traceability solutions. All fully compliant with international standards.Today, ACG fosters long-term collaborative partnerships with customers in 138 countries across six continents. Together, we share a common purpose: to solve the world’s greatest health challenges and make it better for everybody we serve. For more information, please contact the ACG media relations team:madhurima.chakraborty@acg-world.com
Read more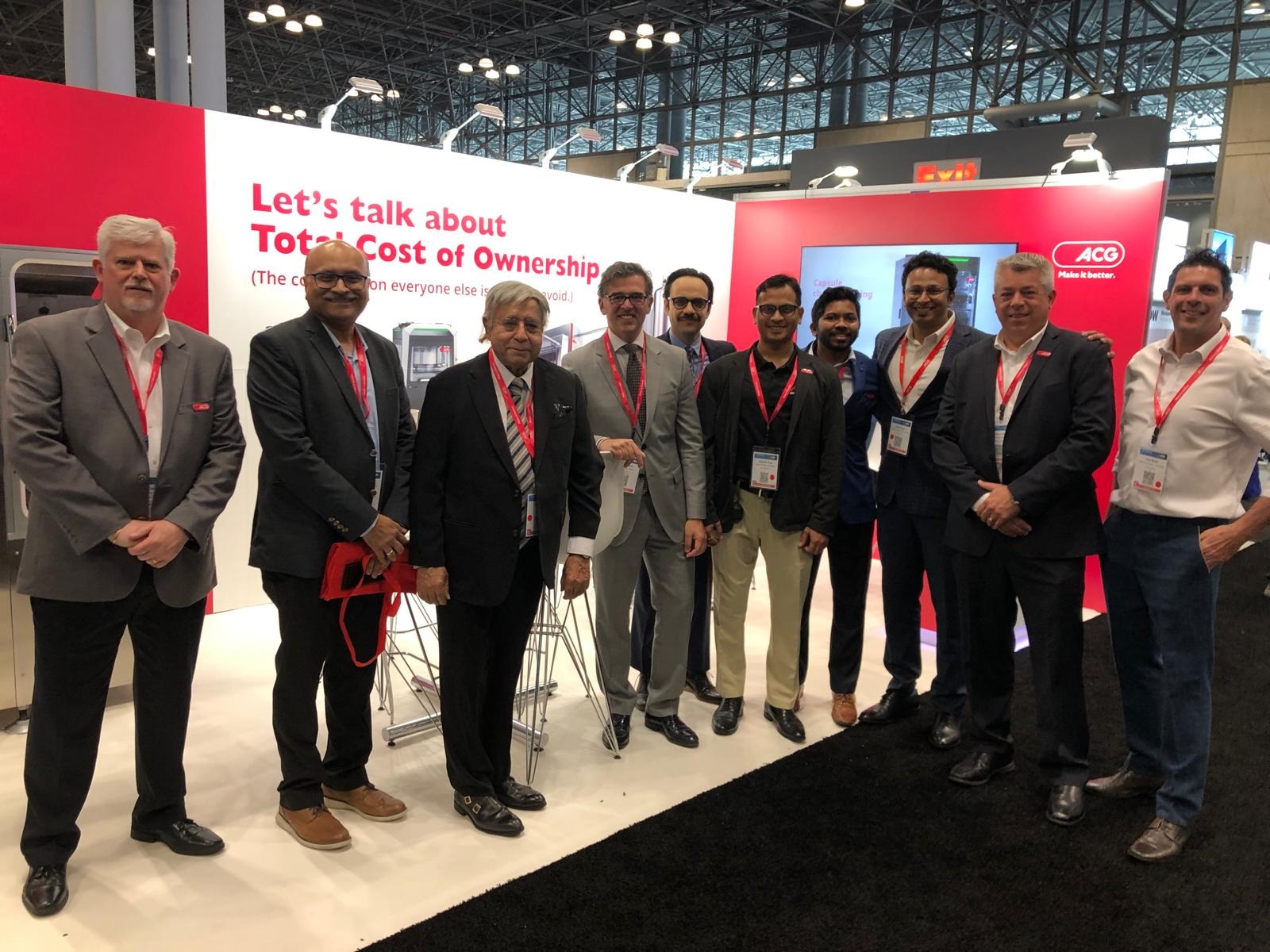
Interphex 2024: ‘ACG focuses on lowering manufacturer’s TCO’
At this year’s Interphex, ACG Engineering, part of ACG - the world's only integrated pharmaceutical solutions and manufacturing company - will be focusing on its cost-effective approach to taking generics to market.ACG’s methodology is based on speed-to-market, production efficiency and reducing manufacturing costs.Borja Guerra, vice-president of international sales at ACG, said: “As a highly experienced global supplier of process and packaging machinery of all oral solid dosage requirements, we are attuned to local market requirements. We aim to provide a low TCO (total cost of ownership) for premium pharmaceutical equipment.“With over six decades of experience partnering in the oral solid dosage space, we have taken over 8000 generics to market, working with more than 1000 pharmaceutical manufacturers to achieve this.”ACG will be showcasing its ACCURA 100 FF. The capsule checkweigher is designed specifically for precise, automatic, and continuous weighing of each capsule – whether empty, filled or partially filled, with anything from powder to pellets, and which is format free.ACG is the world’s largest integrated supplier of pharmaceutical and nutraceutical solid dosage products and services. The company will be exhibiting on stand 3515 between 16-18 April in New York.About ACG For over 60 plus years, ACG has been innovating the production solutions for pharmaceutical and nutraceutical companies, that help make people better.As the world’s most integrated provider of oral dosage products and services, we produce capsules, barrier packaging materials, manufacturing machinery, and visual inspection and traceability solutions. All fully compliant with international standards.Today, ACG fosters long-term collaborative partnerships with customers in 138 countries across six continents.Together, we share a common purpose: to solve the world’s greatest health challenges and make it better for everybody we serve. For more information, please contact the ACG media relations team:madhurima.chakraborty@acg-world.com
Read more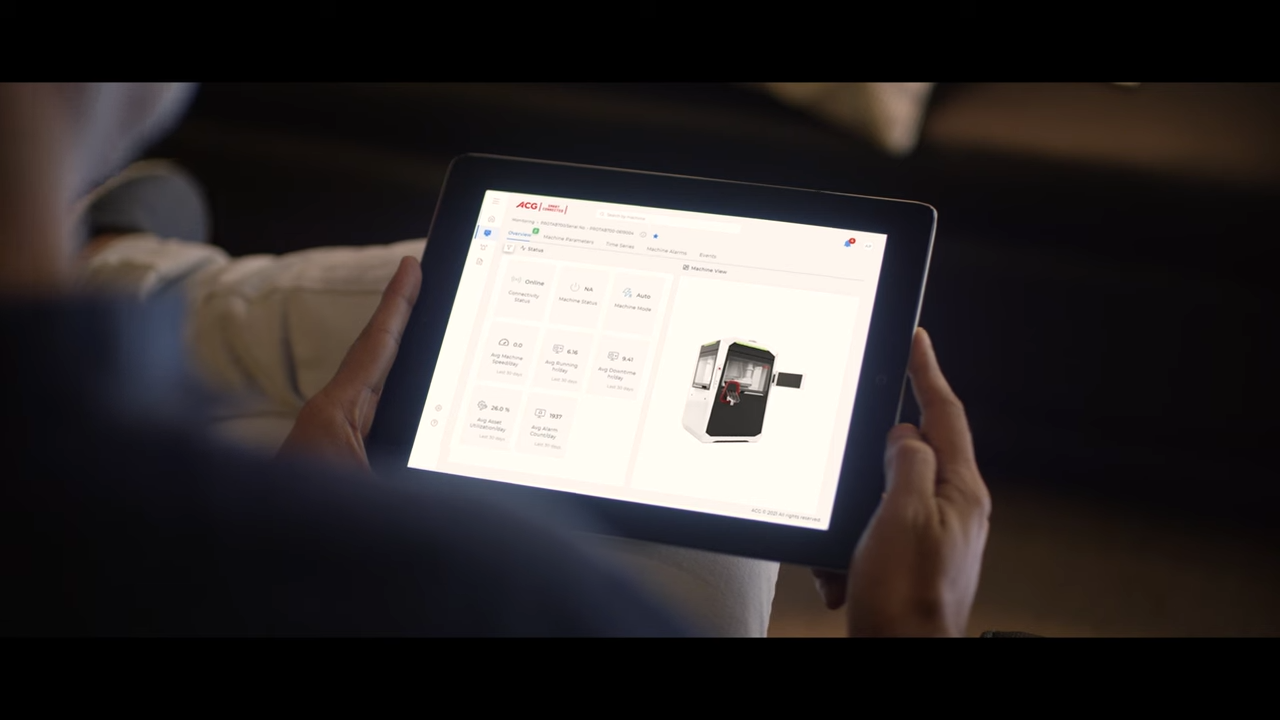
ACG Inspection launches new cloud-based offering to address upcoming VRS requirements under DSCSA regulations
In light of the impending Drug Supply Chain Security Act (DSCSA) regulations, ACG Inspection, a leading track and trace solutions provider for the pharmaceutical industry, has launched its new cloud-based Verification Router Service (VRS).The new system, which forms part of the ACG’s Inspections Life Sciences Cloud Service and Compliance Gateway, enables the automatic verification of saleable returns through product identifiers by routing requests and responses between stakeholders. Serialized products are assigned a unique identifier that can be used to track the product throughout its entire journey, enabling wholesalers to verify the authenticity of the products before they are resold.Shine Vijayan, CTO at ACG, commented: “The regulations, which have now been delayed by 12 months (coming into force in November 2024), will require all trading partners in the pharmaceutical supply chain to verify the identifier of any serialized drug product before redistributing it.“ACG’s existing VeriShield solutions tackles the implementation and interoperability challenges faced at Level 1, through to Level 3. With DSCSA’s regulation in place, ACG’s VRS covers level 4 - helping pharmaceutical manufacturers, distributors and retailers easily track and verify the saleable returns and secure their supply chain from counterfeit and substandard products.“ACG works closely with its customers, helping to address their pain points - one of which being concerns around data security. Our VRS employs robust security measures to safeguard serialized product information, guaranteeing the confidentiality and integrity of sensitive data throughout the verification process.”The system also guarantees real-time verification, to enhance operational efficiency and prevent supply chain delays. Additionally, it provides scalability assurance to accommodate an expanding volume of serialized data, to ensure continued robustness and reliability. And it incorporates exception handling, empowering stakeholders to address issues promptly to help maintain supply chain integrity.Shine Vijayan: “We are trusted experts and through our Life Sciences Cloud Service and Compliance Gateway, we can support counterfeit prevention, improving recall efficiency and data security. At all times, ensuring our clients are fully compliant with international standards and ready to meet the requirements as laid out in the impending DSCSA regulations.” -Ends- About ACGFor over sixty years, ACG has been innovating the production solutions for pharmaceutical and nutraceutical companies, that help make people better. As the world’s most integrated provider of oral dosage products and services, we produce capsules, barrier packaging materials, manufacturing machinery, and visual inspection and traceability solutions. All fully compliant with international standards.Today, ACG fosters long-term collaborative partnerships with customers in 138 countries across six continents. Together, we share a common purpose: to solve the world’s greatest health challenges and make it better for everybody we serve. For more information, please contact the ACG media relations team:madhurima.chakraborty@acg-world.com
Read more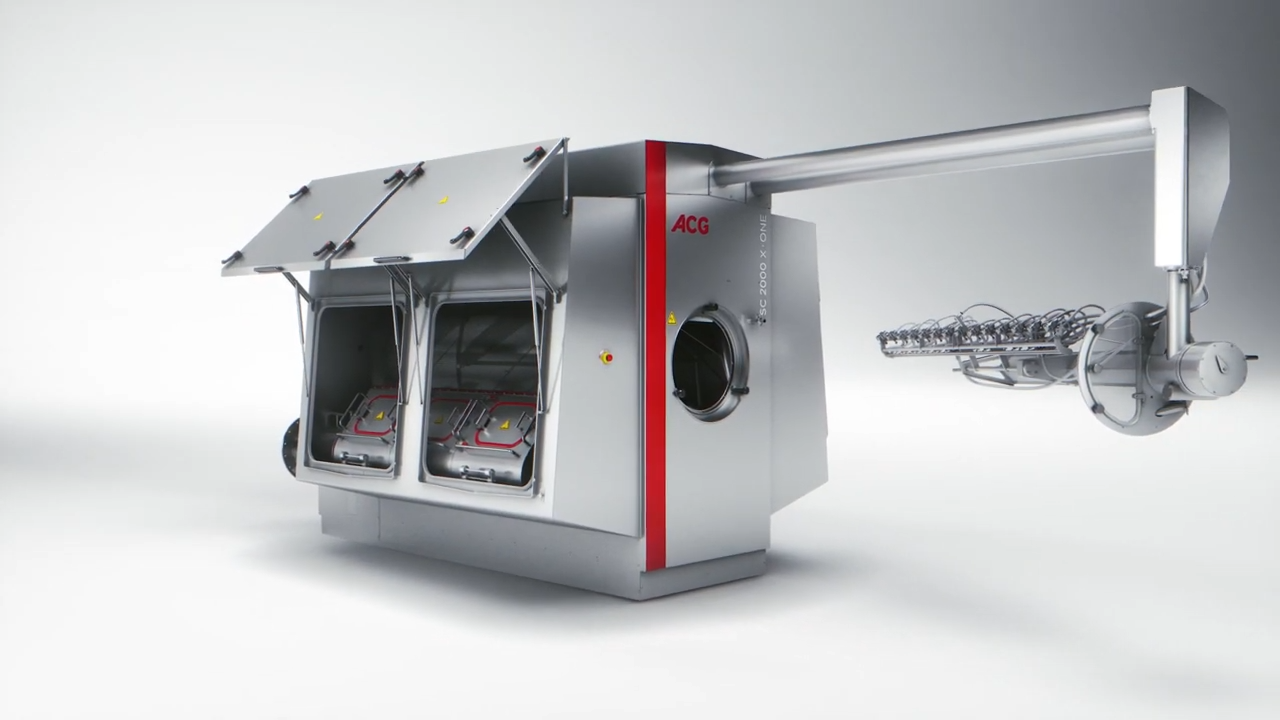
ACG Engineering launches the Smart Coater X.ONE Series Company’s fastest tablet coater ensures optimised production processes
ACG Engineering, a division of ACG, a leading supplier of integrated manufacturing solutions to the global pharmaceutical and nutraceutical industries, is delighted to launch its new Smart Coater X.ONE series, the company’s fastest tablet coater to date.The Smart Coater X.ONE has been designed to make tablet coating extremely fast, with an extra emphasis on process speed, efficiency and operator ease. Its advanced baffle design ensures the quickest process times for batches from 10-100%.Features of the new coater include a unique airflow pattern for optimized drying, a fully-perforated coating drum, closed dust-free charging, integrated discharge baffles, temperature sensor, a high-performing spray-arm and a 2.0 spray nozzle which has been developed with an anti-bearding cap. It also incorporates ACG’s exclusive X•ONE command and control system, designed to facilitate compliance with cGMP standards. Richard Stedman, CEO at ACG Engineering, said: “Our Smart Coater machines are already renowned for their innovative features and operator friendly designs. Now, after a lengthy period of development, we are excited to announce the launch of the X.ONE series.“Our quality-commitment philosophy means that the new machine has been crafted to achieve maximimum efficiency and flexibility for superior tablet coating, across every process – from charging to coating, discharging to cleaning. Each and every cycle is now swifter, more streamlined and profitable.“The fast tablet coater to date is already garnering real interest, and we look forward to continuing to showcase it capabilities at the upcoming CPhI event in Barcelona at the end of the month.” (XXX – may want to adapt this sentence, to reflect true accuracy)-Ends-About ACGFor over 60 years, ACG has been innovating the production solutions for pharmaceutical and nutraceutical companies, that help make people better.As the world’s most integrated provider of oral dosage products and services, we produce capsules, barrier packaging materials, manufacturing machinery, and visual inspection and traceability solutions. All fully compliant with international standards.Today, ACG fosters long-term collaborative partnerships with customers in 138 countries across six continents. Together, we share a common purpose: to solve the world’s greatest health challenges and make it better for everybody we serve.For more information, please contact the ACG media relations team:madhurima.chakraborty@acg-world.com
Read more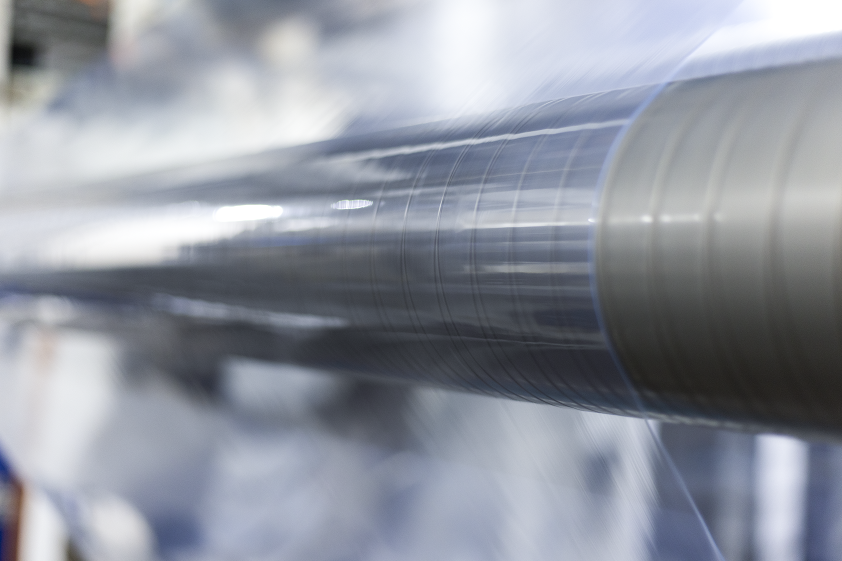
ACG acquires Technical Aluminium Foil Company
Further underpinning business growth across the Middle Eastern and African marketsACG announces full shareholding ownership of Technical Aluminium Foil Company (TAFC). This strategic move further solidifies ACG's growth trajectory across the Middle Eastern and African markets.As the world's only integrated pharma manufacturing solutions company, ACG offers a diverse range of products including capsules, films, foils, engineering equipment and inspection systems. The addition of TAFC, a prominent aluminium foil packaging company based in the UAE, strengthens ACG's position as a leading provider of comprehensive packaging solutions.TAFC boasts over a decade of experience serving the pharmaceutical and food industries with its extensive range of aluminium and specialty packaging foils renowned for their exceptional high barrier properties. The company's expertise in lacquering, lamination, printing and slitting further enhances ACG’s capabilities in meeting the diverse packaging needs of its clients.This acquisition represents ACG Group's inaugural venture in the Middle East, following recent successful acquisitions of ComboCap and AquaCap in the Americas. TAFC seamlessly aligns with ACG Films and Foils' existing business operations, enabling both entities to harness their collective strengths and expertise for accelerated growth.Shivshankar S.R., CEO at ACG Films & Foils, said: “We are excited to be making our first acquisition in the UAE. This strategic collaboration will further support our work in bringing innovative and high-quality packaging products to market, while reducing lead times and improving service levels.“By joining forces, the companies will be able to leverage their combined strengths and expertise to propel the business forward in the Middle Eastern and African markets.”-Ends-About ACGIn accordance with its commitment to making the world healthier, ACG has been delivering exceptional solutions to the global pharmaceutical and nutraceutical industry for sixty years, across six continents and in a hundred countries.Collaboration is at the core of ACG’s ethos. ACG is the world’s only integrated pharma manufacturing solutions company, with products ranging from capsules to films & foils, to engineering equipment and inspection systems – all that meet international regulatory requirements. For ACG, it’s always about finding innovative solutions to the world’s greatest health challenges, together.For more information, please contact the ACG media relations team:madhurima.chakraborty@acg-world.com
Read more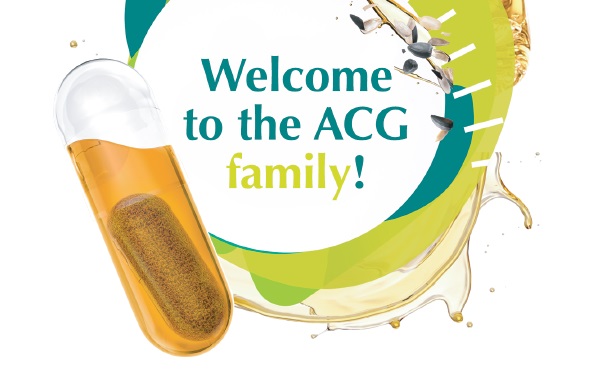
Vantage Nutrition LLC acquires ComboCap Inc
This acquisition positions Vantage Nutrition as the only company in the world supplying Sidebysideä health products to nutritional and pharmaceutical markets, for enhanced combinations.Vantage Nutrition, an ACG group company announces full shareholding ownership of ComboCap Inc (USA) and BioCap (South Africa).ComboCap is renowned for the invention and commercialization of its Sidebyside technology, the world’s first three-piece capsule health product that contains an internal divider, enabling wet and dry ingredients to be brought to market side by side, separated-but-together. Backed by 80 international patent awards ComboCap has been supplying nutritional brand customers with unique finished product solutions out of its cutting-edge cGMP plant in NJ, USA. This acquisition marks a significant milestone for Vantage Nutrition and ACG, as it further expands its technology and customer solutions footprint in North America and around the world.ACG is the world’s largest integrated supplier of pharmaceutical and nutraceutical solid dosage products and services. Vantage Nutrition, an ACG group company, already has an excellent reputation as an innovator of liquid filled capsule solutions. ComboCap marks Vantage Nutrition’s second US investment in less than a year, and first in S.A, after Philadelphia-based ‘AquaCap’ was acquired from Nestlé S.A. With this expansion of manufacturing capabilities and patented technology, along with the commitment to delivering integrated solutions and cutting-edge technology, Vantage Nutrition aims to provide the most comprehensive and advanced multiphase solutions to customers globally.Karan Singh, Managing Director at ACG, said, "As one of world’s largest producers of empty hard-shell capsules, at ACG we have often thought, what next? Strengthening our portfolio of most comprehensive vegetarian and gelatin capsules, in every imaginable size, I am thrilled to announce the acquisition of ComboCap Inc and BioCap. We now will hold the patented design and specialized equipment used inproducing the world’s first 2-in-1 capsule product with a movable membrane, becoming the sole proprietor of this technology globally.With our partners, we will usher a new era in new combinations of dietary supplements, and even non-prescription or over-the counter (OTC) remedies as well as prescription (Rx) medicines to be delivered in a single dose. This technological breakthrough is a solution to current formulation challenges with many combination therapies, including incompatible ingredients or molecules. Capsules are arguably the safest and most reliable way to deliver medicine and we at ACG strive to make it better.”Tobie Louw, a Founder and CEO of ComboCap Inc, said: “Vantage Nutrition is the perfect partner for our business, and we are very excited to be part of the ACG family. We share a passion for innovation and the commitment to bring nutraceutical and pharmaceutical customers the best possible solutions and services. By joining forces and leveraging our collective capabilities we’ll no doubt bring Sidebysideä to nutraceutical and pharmaceutical markets the world over.”-Ends-About Vantage NutritionVantage Nutrition, part of the ACG Group, is one of the world’s largest and most respected manufacturer of hard-shell liquid-fill capsule solutions. As a strategic consultancy and manufacturing partner in the nutraceutical space, Vantage Nutrition helps clients bring high-quality and innovative products to market, fast. About ACGIn accordance with its commitment to making the world healthier, ACG has been delivering exceptional solutions to the global pharmaceutical and nutraceutical industry for sixty years, across six continents and in a hundred countries.Collaboration is at the core of ACG’s ethos. ACG is the world’s only integrated pharma manufacturing solutions company, with products ranging from capsules to films & foils, to engineering equipment and inspection systems – all that meet international regulatory requirements. For ACG, it’s always about finding innovative solutions to the world’s greatest health challenges, together.For more information, please contact the ACG media relations team:madhurima.chakraborty@acg-world.com
Read more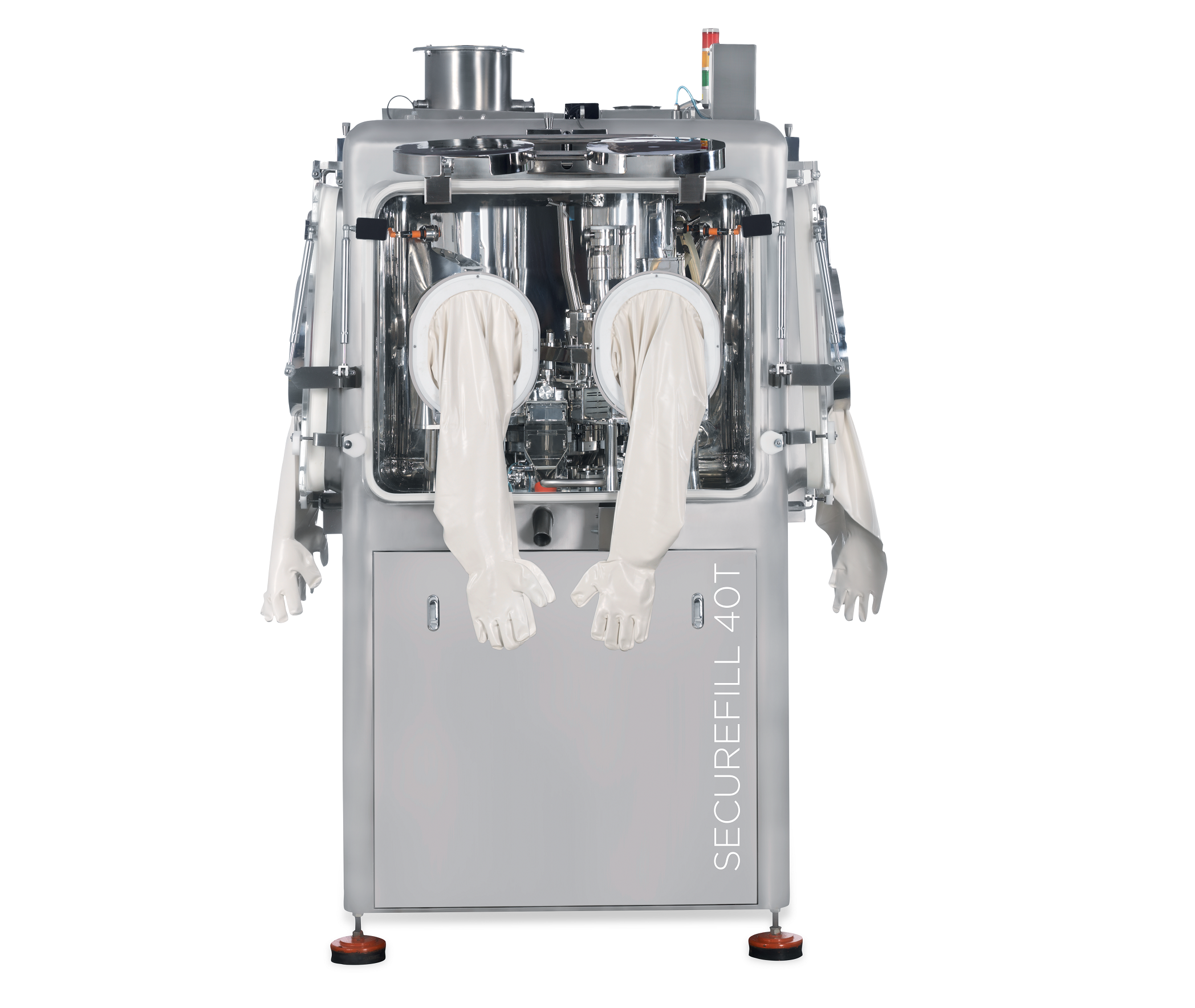
ACG Engineering – SECUREFILL 40T
Tablets & CapsulesCapsule Filling Equipment & Supplies (February 2023)ACG Engineering – SECUREFILL 40TThe Securefill series is ACG’s high-level containment capsule-filling machine range. Designed for filling capsules with highly potent and/or toxic drugs, the machines comply with occupational exposure band (OEB) up to level 4.Built with operator safety in mind, these machines are equipped for filling capsules with oncological, biopharmaceutical, antiviral formulations, and other such highly potent active pharmaceutical ingredients (HPAPIs).Features:• SS316L monoblock structure containing HEPA filters, a rapid transfer port (RTP), glove ports, and accurate dosing mechanisms maintained in a negative pressure environment.• Provision for contained charging and discharging.• Wet-in-place system to ensure wetting of all suspended particles in the pharma zone.• Can be integrated with check-weighers, metal detectors and de-dusters under containment conditions.Benefits:• Ensures complete containment, thereby avoiding operator contact within OEL range 1-10µg/m3.• Integrated containment philosophy for upstream and downstream processes.• Enables easy cleaning.• Supports the production of life-saving drugs that contain HPAPIs.Technical specifications: SECUREFILL 40T Capsule size 00 - 5 Maximum speed 40,000 capsules/hour OEL 1-10µg/m3About ACGIn accordance with its commitment to making the world healthier, ACG has been delivering exceptional solutions to the global pharmaceutical and nutraceutical industry for sixty years, across six continents and in a hundred countries.Collaboration is at the core of ACG’s ethos. ACG is the world’s only integrated pharma manufacturing solutions company, with products ranging from capsules to films & foils, to engineering equipment and inspection systems – all that meet international regulatory requirements. For ACG, it’s always about finding innovative solutions to the world’s greatest health challenges, together.For more information, please contact the ACG media relations team:madhurima.chakraborty@acg-world.com
Read more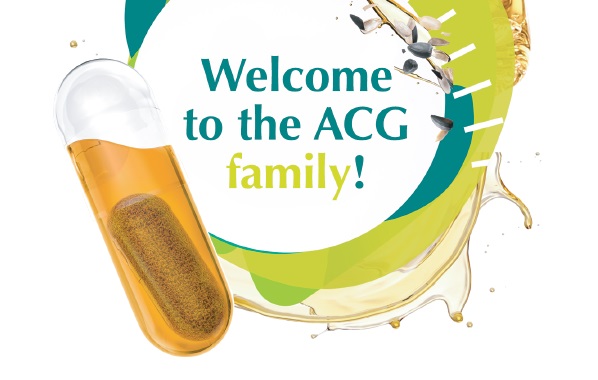
Vantage Nutrition LLC acquires Aquacaps from Nestlé Health Science
Vantage Nutrition’s innovative nutraceutical offering expands into North America.. Vantage Nutrition, an ACG Group company, announced on 1st December 2022 that it has acquired Philadelphia-based ‘Aquacaps’ – an asset of Nestlé Health Science. Aquacaps is a leading contract manufacturer of liquid-filled capsules within the nutritional supplement industry in the United States. Its novel liquid delivery technology allows for the liquid filling of hard gelatin and vegetarian capsules. ACG is the world’s largest integrated supplier of pharmaceutical and nutraceutical products and services. Vantage Nutrition, an ACG group company, already has an excellent reputation as an innovator of two-piece liquid fill capsule solutions. The company’s mission is to be the most efficient partner in delivering innovative and high-quality nutraceutical products to customers globally. Karan Singh, Managing Director of ACG, said: “Although ACG has been established in North America for the last 20 years, this marks our first acquisition in the territory and is a key next step in our global expansion strategy. With this increase in our footprint and manufacturing capabilities, coupled with Vantage’s innovative technologies and 360-degree service offering, we aim to provide the most advanced combination liquid-fill solutions for customers across the region.” About VantageVantage Nutrition, part of the ACG Group, is one of the world’s largest and most respected manufacturer of hard-shell liquid-fill capsule solutions. As a strategic consultancy and manufacturing partner in the nutraceutical space, Vantage helps clients bring high-quality and innovative products to market, fast. About ACGIn accordance with its commitment to making the world healthier, ACG has been delivering exceptional solutions to the global pharmaceutical and nutraceutical industry for sixty years, across six continents and in a hundred countries.Collaboration is at the core of ACG’s ethos. ACG is the world’s only integrated pharma manufacturing solutions company, with products ranging from capsules to films & foils, to engineering equipment and inspection systems – all that meet international regulatory requirements. For ACG, it’s always about finding innovative solutions to the world’s greatest health challenges, together.For more information, please contact the ACG media relations team:madhurima.chakraborty@acg-world.com
Read more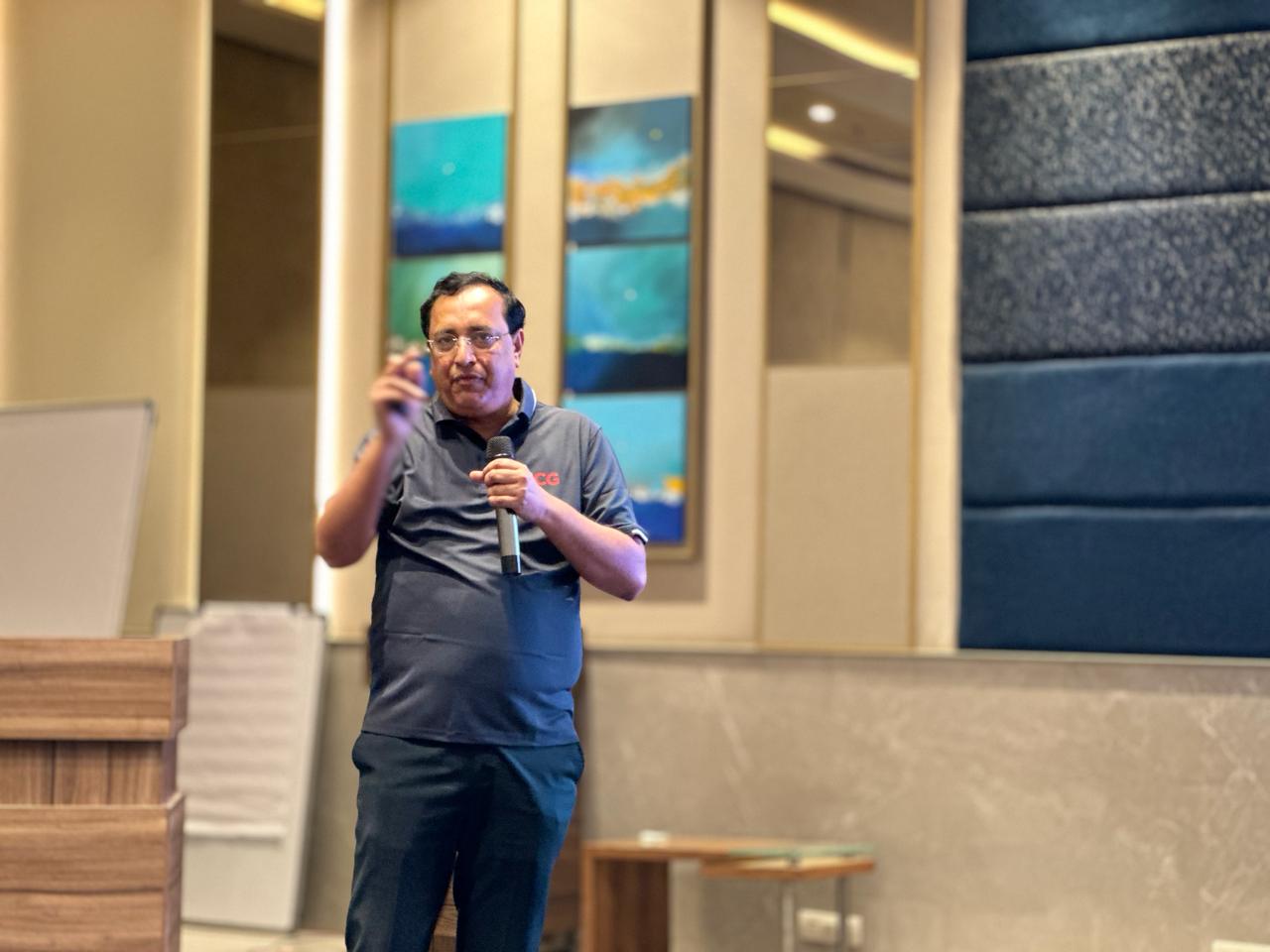
ACG appoints Shankar Gupta as Chief Sales Officer Industry authority to re-join business in a newly created role
ACG, the world’s largest integrated pharmaceutical and nutraceutical manufacturing solutions provider, is delighted to announce that Shankar Gupta will be re-joining the business in the newly created role of Chief Sales Officer.In his new role, Shankar will be responsible for driving sales across all four ACG divisions (Films and Foils, Capsules, Inspection and Engineering) in order to continue building the company’s ‘One ACG’ agenda. Essentially, this will involve bringing further uniformity to ACG's customer outreach processes, creating more integrated solutions, and ultimately providing a consistent brand experience to ACG’s global customers, regardless of business division or location. He will also focus on scaling new initiatives.Shankar will report directly into the managing director, Karan Singh, who comments:"I am so pleased that Shankar Gupta has decided to rejoin the business during this exciting time. His understanding of ACG and its deliverables, and deep insight into our customers’ businesses will help us to align ourselves better to their changing needs. More importantly, he will champion and support better collaboration and partnership with customers.“Shankar will be pivotal in calibrating and aligning our business units to our goal of ‘Making it Better’, and our belief that everyone deserves access to good medicine."Shankar Gupta adds: “I am excited to use my experience in the pharmaceutical industry to augment ACG's growth by aligning the organisation to the changing dynamics of the global healthcare Industry.“It will certainly call for a huge collaboration of efforts both internally and with our customers, but will ultimately lead to a richer, deeper and more numerous partnerships.”-Ends-About ACGIn accordance with its commitment to making the world healthier, ACG has been delivering exceptional solutions to the global pharmaceutical and nutraceutical industry for sixty years, across six continents and in a hundred countries.Collaboration is at the core of ACG’s ethos. ACG is the world’s only integrated pharma manufacturing solutions company, with products ranging from capsules to films & foils, to engineering equipment and inspection systems – all that meet international regulatory requirements. For ACG, it’s always about finding innovative solutions to the world’s greatest health challenges, together.For more information, please contact the ACG media relations team:madhurima.chakraborty@acg-world.com
Read more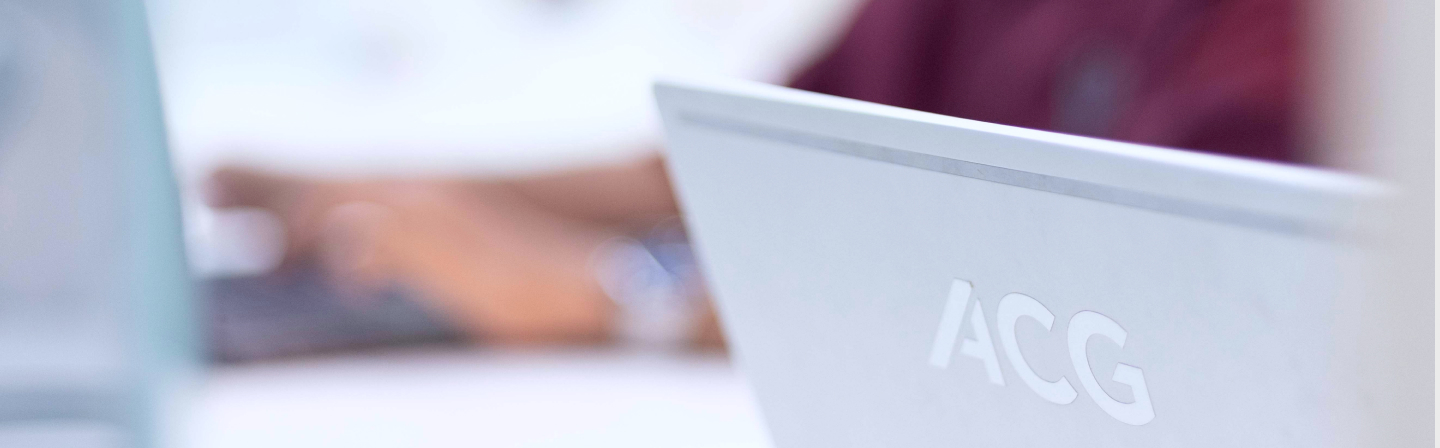
ACG to Launch German Process Laboratory in 2023
Following the success of its first-to-market laboratory for process development in India, ACG (the world’s biggest integrated pharmaceutical and nutraceutical manufacturing solutions provider) is now also committed to launching a sister process lab in Germany in 2023.This new process development laboratory will be located at ACG’s XERTECS GmbH site in Mulheim in the South West of Germany, with the first phase occupying approximately 250 square metres. ACG’s staffing recruitment plan for the lab will be to attract top academic talent from local universities, as well as trained and experienced process engineers, pharmacists and lab technicians.The aim of ACG’s new laboratory will remain consistent with the first – to provide customers and partners access to the latest knowledge, skills and equipment to collaboratively keep pushing the boundaries of all aspects of process development. So customers can test solid dosage optimisation limits, for example, and co-create alongside ACG’s team of experts to develop new process solutions.The extensive range of available equipment covers areas including feasibility studies, research and development work, pilot-scaling, and tailored in-house technical training courses. Customers also get to experience and test products from ACG’s portfolio and gain operational and maintenance training on premise.Dr Marcus Michel, CEO of ACG Engineering, explains: “ACG’s process labs reinforce our commitment to ‘making it better’. Requested by the Indian market, our first lab has enabled customers to build their competencies and capabilities, as well as to scale up – with many of these customers now operating at high capacity and efficiency. Our plan is simply to replicate this model in the European market, and we are working at full speed to ensure the launch of our new facility in 2023.“The lab in India is home to some of the smartest and finest technologies in powder processing, and is fully equipped for all aspects of granulation, drying, tablet compression and coating. Many of our machines are unique because they have been built or modified in direct response to our customers’ needs – helping them on their manufacturing journey.”About ACGIn accordance with its commitment to making the world healthier, ACG has been delivering exceptional solutions to the global pharmaceutical and nutraceutical industry for over sixty years, across six continents and in a hundred countries.Collaboration is at the core of ACG’s ethos, and ACG is the world’s only fully integrated pharma manufacturing solutions company, with products ranging from capsules to films & foils, to engineering equipment and inspection systems – all that meet international regulatory requirements. For ACG, it’s always about finding innovative solutions to the world’s greatest health challenges, together.For more information, please contact the ACG media relations team:madhurima.chakraborty@acg-world.com
Read more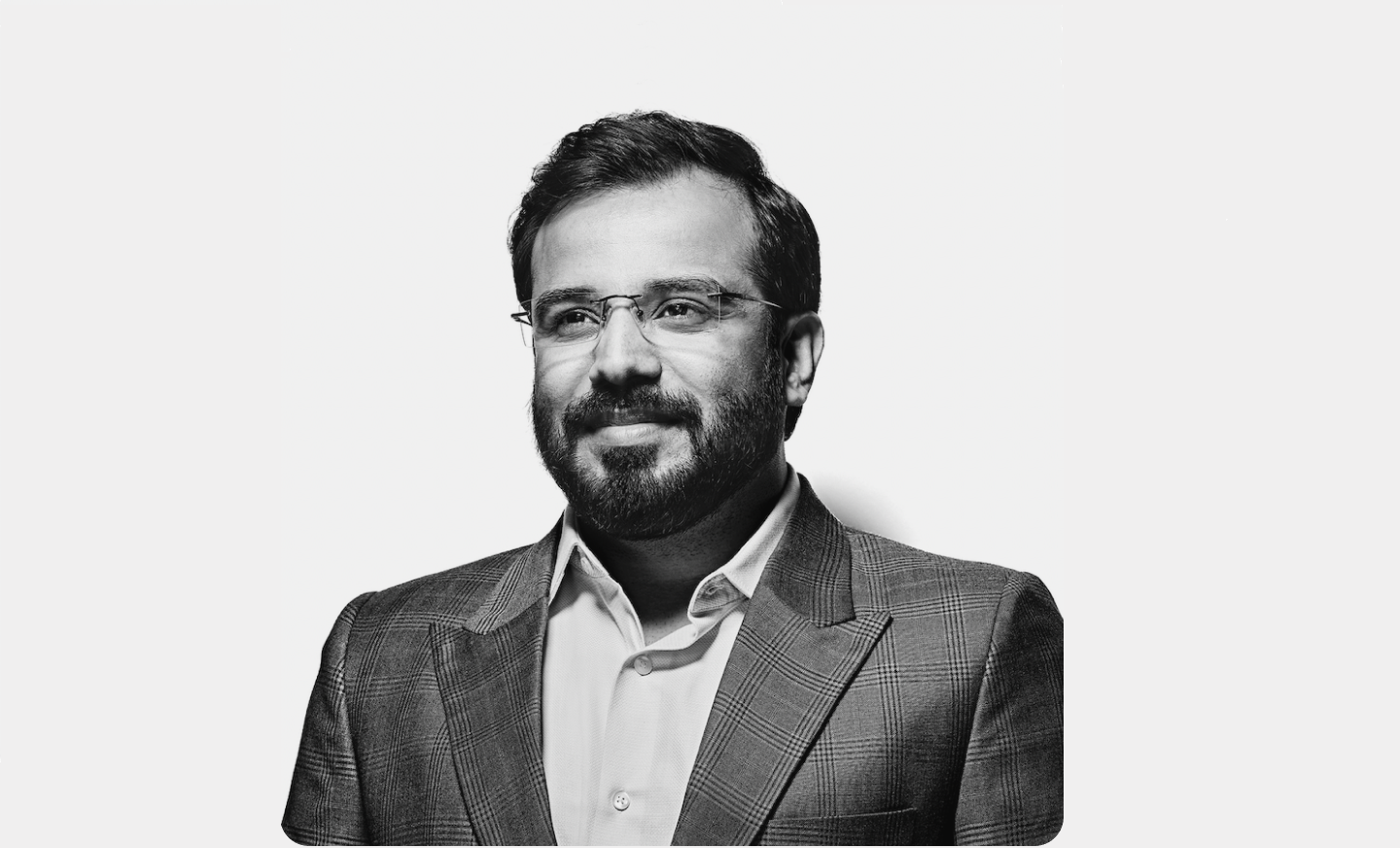
ACG appoints Udit K Singh as CEO of ACG Inspection
ACG, a leading supplier of fully integrated manufacturing solutions to the global pharmaceutical and nutraceutical industry, is pleased to announce the appointment of Mr. Udit K Singh as the new chief executive officer (CEO) of its Inspection Division.Mr. Singh will be supporting the company as it continues its growth and global expansion. He will be responsible for ensuring that every dose of medication that ACG Inspection’s pharmaceutical and nutraceutical partners provide is manufactured and delivered exactly as intended. That is down to the fact that ACG’s visual inspection systems track and monitor the manufacturing lines to guarantee flawless, safe products.Karan Singh, managing director, ACG said: “ACG is focused on building a diverse, world-class team by hiring top international talent. We are delighted to welcome Udit Singh to ACG Inspections. He has had an illustrious career and brings diverse and unique capabilities, including a robust understanding of the pharmaceutical sector.“The team looks forward to tapping into his deep experience to enrich our global work towards making the world safer and healthier. With his knowledge and expertise in this field, Udit Singh is sure to take ACG Inspection to newer heights.”Mr. Singh added, “I am pleased to join ACG and will work to ensure that our advanced serialisation, aggregation and anti-counterfeiting solutions track and protect medicines all the way through the supply chain, and into the hands of those who need them.“We are investing substantially to ensure our track and trace platform performs seamlessly and complies with regulatory requirements all over the world. I look forward to playing an integral role, and contributing towards the continued development, working with a world-class team.”About ACGIn accordance with its commitment to making the world healthier, ACG has been delivering exceptional solutions to the global pharmaceutical and nutraceutical industry for almost sixty years, across six continents and in a hundred countries.Collaboration is at the core of ACG’s ethos, and ACG is the world’s only integrated pharma manufacturing solutions company, with products ranging from capsules to films & foils, to engineering equipment and inspection systems – all that meet international regulatory requirements. For ACG, it’s always about finding innovative solutions to the world’s greatest health challenges, together.For more information, please contact the ACG media relations team:madhurima.chakraborty@acg-world.com
Read more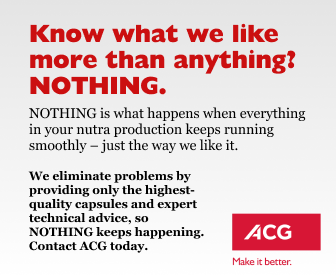
ACG Capsules launches campaign to promote problem-free pharmaceutical production
-One of the world’s largest producers of empty hard-shell capsules is on a mission to‘Love NOTHING’ when it comes to zero-problem productionACG, one of the world’s largest producers of empty hard-shell capsules, has launched its global pharmaceutical campaign: ‘ACG loves NOTHING’. The campaign is aimed at significantly improving pharmaceutical production through collaboration and industry-leading innovation. With a host of value-added services on offer, ACG has taken a pledge to strive for zero-problem pharmaceutical and nutraceutical manufacturing.Alex Robertson, CMO at ACG, said: “The messaging at the centre of this campaign is: ‘ACG loves NOTHING’ – we are putting every effort towards zero-problem production. That’s because when ‘nothing’ happens during pharmaceutical and nutraceutical production, everything runs reliably, and our customers can get the products they make to the people who need them. We will achieve this by providing the highest quality empty capsules and all the holistic advice and expertise required for seamless operations.”Founded 60 years ago, ACG was created on the simple principle of ‘Make it Better’. As the world’s largest integrated supplier of solid dosage pharmaceutical and nutraceutical products, and with the most comprehensive ranges of vegetarian and gelatin capsules globally, ACG has the scale and range to have a far-reaching impact on pharmaceutical production and human health.Selwyn Noronha, CEO ACG Capsules, added: “The pharmaceutical sector is regulated and highly competitive. Companies operating within it need a diverse range of quality capsules that help them stand out from the crowd, while also meeting demands for clean and natural products.“Beyond exceptional products, these companies need expertise and a lifetime of targeted support to ensure efficient manufacturing and guarantee regulatory compliance. With proficiency in all aspects of manufacturing from capsules to machines and protective barriers, for the last 60 years ACG has been the only company to offer this level of support, and it continues with this focus at the heart of operations.”So, at ACG, there really is something about NOTHING. The company is on a mission to drive towards problem free production and collaborating with its customers to collectively deliver on its mission of creating a healthier world.About ACGIn accordance with its commitment to making the world healthier, ACG has now been delivering exceptional solutions to the global pharmaceutical and nutraceutical industry for 60 years, across six continents and in 138 countries.‘Collaboration’ is at the core of ACG’s ethos, and ACG is the world’s only integrated pharma manufacturing solutions company, with products ranging from capsules to films & foils, to engineering equipment, and inspection systems – all that meet international regulatory requirements.For ACG, it’s always about finding innovative solutions to the world’s greatest health challenges, together.For more information, please contact the ACG media relations team:madhurima.chakraborty@acg-world.com
Read more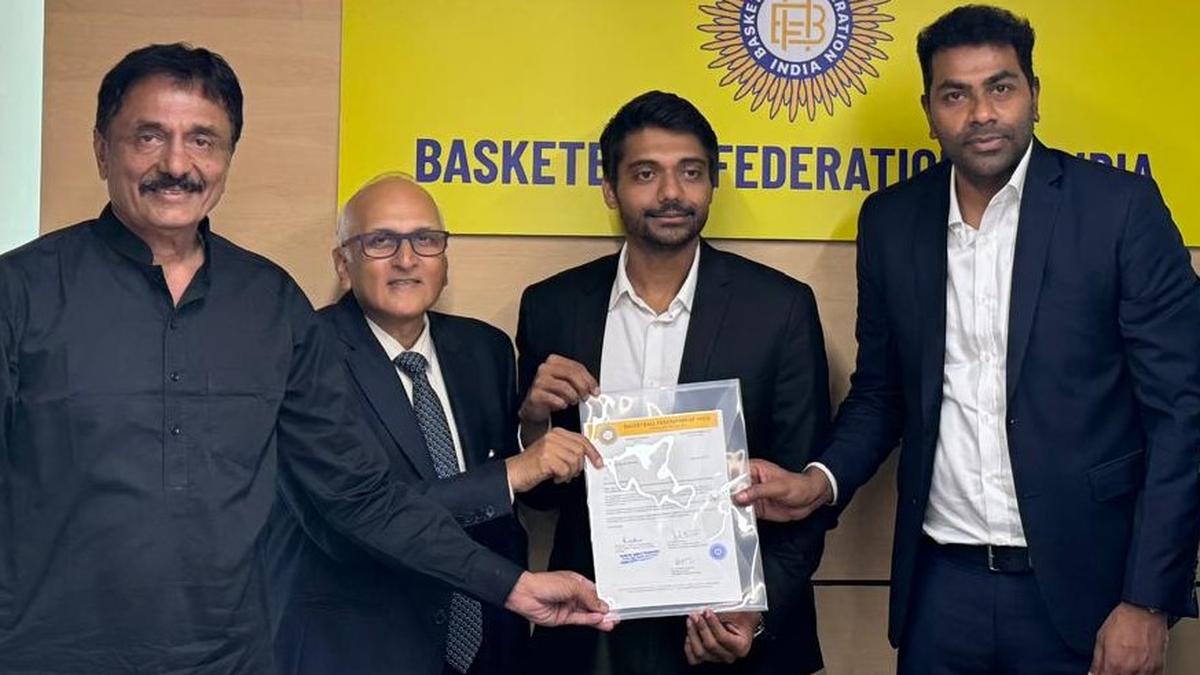
BFI president Aadhav Arjuna, right, and secretary general Kulvinder Gill, left,…
BFI signs seven-year deal with ACG Sports for professional basketball league
Addressing the media here on Friday, the president of BFI, Aadhav Arjuna said that for each year, the amount would be Rs. 20.6 crore rupees for the 5x5 format and Rs. 10.3 crore for the 3x3 format.“It was a transparent system, and we gave it to the highest bidder. It is a medical group of companies, and has already been associated with supporting basketball through many events,” said the BFI president al Star Basketball League in Delhi on Friday.The Basketball Federation of India (BFI) has signed a seven-year deal with ACG Sports Limited, with a guarantee of Rs.216.30 crore for hosting the National Star Basketball League for men and women.Addressing the media here on Friday, the president of BFI, Aadhav Arjuna said that for each year, the amount would be Rs. 20.6 crore rupees for the 5x5 format and Rs. 10.3 crore for the 3x3 format.“It was a transparent system, and we gave it to the highest bidder. It is a medical group of companies, and has already been associated with supporting basketball through many events,” said the BFI president “It is a new beginning for Indian basketball. We hope to pay substantial money to our players. We call all the big corporate companies and sponsors to invest in the league and make it a success,” Arjuna said.“We will host both the men’s and women’s leagues. The BFI would hold 100% ownership of the league so that we put the revenue generated back into the game for our developmental projects,” he said.It was stated that about 100 Indian players would stand to benefit from the league, which would also feature about four foreign players in each team.“We call all the players and coaches, to be ready, and to be fit, for the new journey,” said Arjuna.The league is expected to feature 10 men’s teams, and eight women’s teams.While the 5x5 format is expected to be played in stadiums, the 3x3 format could be staged on the beach, parks and malls so as to take the game to the people.The BFI president also said that he had an extensive tour of the USA to collaborate with the NBA for the betterment of Indian basketball.“We already have Scott Flemming for the men’s team. We will soon have an American coach for the women’s team and an American fitness coach also,” he said.Some of the money generated from the league is expected to be invested in making world-class infrastructure for Indian basketball.“In the USA, even colleges have a world-class stadium,” said Arjuna.The secretary general of BFI, Kulvinder Gill said, “Now Indian players can take up basketball as a career. We have enough talent in the country to nurture and build.”The details of the teams, structure, venues and fixtures are expected to be announced in a few weeks time. Source: BFI signs seven-year deal with ACG Sports for professional basketball league
Read more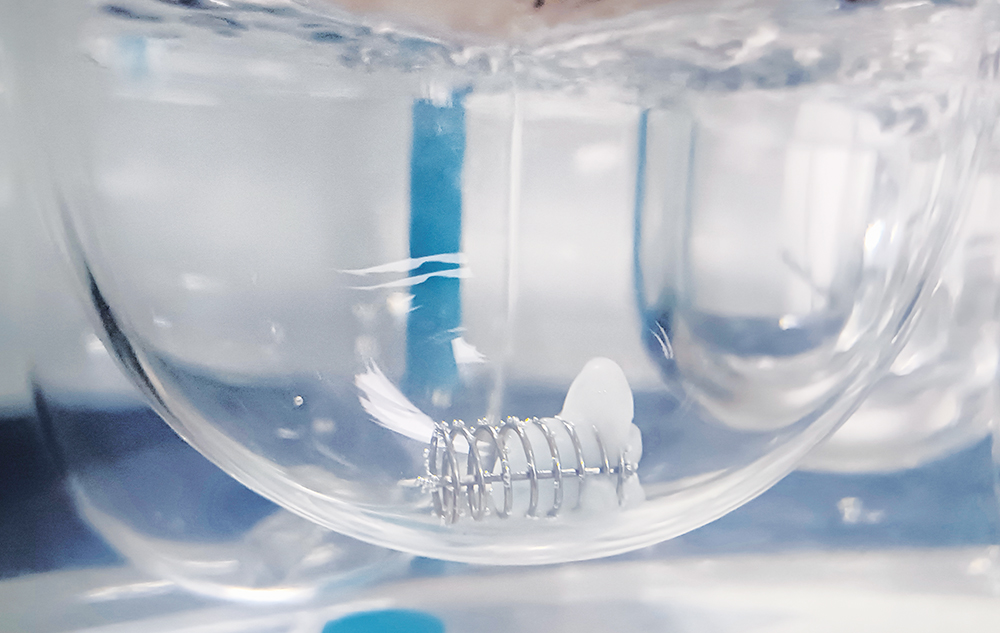
Strategies to mitigate gelatin cross-linking in oral solid drug delivery
Strategies to mitigate gelatin cross-linking in oral solid drug delivery
The oral solid drug delivery system is a prominent mode of drug administration. It is recognised for being non-invasive, patient compliant and convenient; steadfastly catering to the multifaceted demands of the market through its pioneering methodologies.Despite the emergence of cutting-edge techniques such as biologics, molecular delivery and parenteral administration, the prevalence of solid delivery systems continues to undergo ongoing innovation. From traditional pills and capsules to novel variations, such as gummies, soft chews, granules, lozenges and pastilles, the oral delivery mechanism has revolutionised pharmaceutical formulations, capturing the attention of both healthcare professionals and consumers. Its adaptability, accessibility and effectiveness have propelled it to the forefront, surpassing even the established parenteral and intravenous routes.Irrespective of the product type, the fundamental goal of processing oral solid dosage (OSD) forms remains unwavering: to create formulations that guarantee consistent dosing, reliable distribution of ingredients, and uniform dissolution and bioavailability. However, achieving this objective is contingent upon the dosage forms, actives and excipients employed.Gelatin often serves as a crucial excipient in OSD formulations. Whether encapsulating active ingredients within hard or soft shells or serving as a coating agent for tablets or a gelling agent in any other formulations, gelatin emerges as a fundamental ingredient across various oral delivery formats. Its versatility finds applications in a wide range of dosage formats.However, despite its extensive use, OSD manufacturers grapple with a persistent challenge: gelatin cross-linking within formulations, initially observed in 1974 for hard capsules containing chloramphenicol. This phenomenon poses a threat to the dissolution of pharmaceutical products, underscoring the need for strategies to mitigate such barriers. As we navigate the complexities of drug formulations, addressing issues such as gelatin cross-linking becomes paramount in advancing the efficacy and reliability of oral drug delivery systems.CROSS-LINKING IN THE GELATINFollowing the ingestion of gelatin capsules or gelatin-coated tablets, the primary objective of the formulation lies in releasing the inner content into the biological media. However, it is often observed that gelatin-based formulations tend to experience dissolution failures upon ageing, which is primarily attributed to cross-linking in stressed gelatin-containing products. It causes the formation of a swollen, thin, tough, rubbery, water-insoluble membrane, known as a pellicle (Figure 1). This may act as a barrier to the drug release from the formulation, resulting in the slower release of the filled formulation, which consequently leads to a decrease in dissolution values or no release at all in in vitro studies. The degree of cross-linking can vary within and between capsules, making it difficult to predict the extent of the issue. Once formed, these pellicles are irreversible, rendering the gelatin insoluble. As a consequence, dissolution results will have higher variability when gelatin capsule/coated tablets are cross-linked. This phenomenon – during the early stages of drug insertion into the market – often results in failure to meet regulatory guidelines for in vitro studies, prompting regulatory authorities to recall the product.MECHANISM OF GELATIN CROSS-LINKINGGelatin, derived from collagen via hydrolysis, is a soluble protein mixture primarily composed of amino acids (Figure 2). These amino acids, linked by amide bonds, form a linear polymer with molecular weights ranging from 15,000 to 250,000. Cross-linking in gelatin can arise from chemical interactions between its peptide chains or individual amino acids. These interactions can be triggered by small amounts of aldehydes, which are present in excipients or APIs. They may also occur from the breakdown of formulation components or packaging materials – or exposure to harsh conditions such as high temperatures and humidity. Figure 2: Gelatin structure.There are two main types of cross-linking reactions observed in gelatin: internal and external. Internal cross-linking takes place when gelatin capsules are exposed to high temperatures and humidity, primarily affecting their inner surfaces. In contrast, external cross-linking occurs when gelatin-based formulations, such as hard or soft capsules and gelatin-coated tablets, interact with substances such as aldehydes, peroxides or sulfonic acids.These substances cause chemical changes in the gelatin molecules, transforming them from a random coil configuration to a collagen triple helix structure.The mechanism of gelatin cross-linking involves three distinct pathways, each driven by specific molecular interactions and catalytic factors.Intrastrand and Interstrand Cross-Linking: Gelatin’s reactivity stems from interactions among amino acids within the same gelatin molecule (intrastrand) or between neighbouring molecules (interstrand). Key amino acids involved in this process (most notably lysine) exhibit trifunctional properties. Lysine residues in close proximity undergo oxidative deamination, yielding terminal aldehyde groups. These aldehyde groups can then react with neighbouring ε-amino groups of lysine, forming imine intermediates. Subsequent aldol condensation reactions lead to the formation of cross-linked products containing pyridinium rings. This cascade of reactions is catalysed by external factors such as heat and relative humidity or the presence of a chemical agent.Reaction with Carbonyl Groups: Another mechanism involves the interaction between lysyl ε-amino groups and aldehydic impurities present as contaminants. This reaction generates hydroxymethylamino derivatives, which undergo dehydration to form imines. These imines then engage in further reactions with hydroxymethyl lysine residues, forming dimethyl ether bridges. Ultimately, rearrangement reactions result in methylene linkages between lysyl ε-amino groups, facilitating cross-link formation. Similar reactions can occur with aldose sugars commonly found in pharmaceutical formulations, wherein imine intermediates react with free amino groups to yield ketose sugars. Subsequent reactions between imines and sugars lead to cross-linking via carbonyl functionalities.Formation of Aminals: Additionally, gelatin cross-linking can occur through the formation of aminals, which are amine derivatives of acetals. This process is influenced by the pH of the environment. Aminals formed between gelatin chains contribute to cross-linking, further enhancing the structural integrity of the gelatin network.FACTORS CONTRIBUTING TO GELATIN CROSS-LINKINGCross-linking in gelatin formulations can stem from various environmental and chemical factors, significantly impacting their stability and performance (Table 1). Drug NameDosage FormUSP ApparatusSpeed (RPMs)MediumVolume (mL)Recommended Sampling Times (minutes)UpdatedLopinavir/RitonavirCapsulte (Soft-Gelatin)II (Paddle)50Tier 1: 0.5 M Polyoxyethylene 10 Lauryl Ether with 10 mM Sodium Phosphate monobasic (pH 6.8) Tier II: same as above with NMT 1750 USP units/L of Pancreatin90010,15, 30 and 4506/18/2007CelecoxibCapsuleII (Paddle)50, 100 and 200 mg: 50 rpm; 400 mg: 75 rpmTier I Medium: 0.04 M tribasic sodium phosphate (pH 12) with 1% SLS. Tier II Initial Medium: 750 mL of simulated gastric fluid, USP (includes pepsin); At 20 minutes, while stirring, add 180 mL of appropriate concentrations of SLS solution (for a final concentration of 1% SLS). Add about 70 mL of 1.2 N NaOH to adjust the pH to 12.Tier I: 1,000 mL Tier II: 750 mL (initial) 1,000 mL (final)10, 20, 30, 45 and 6007/01/2010Table 1: Representative two-tier dissolution method.Environmental FactorsElevated humidity, temperatures and intense light exposure can trigger cross-linking reactions within gelatin-based formulations, resulting in prolonged in vitro dissolution times. The presence of high humidity facilitates direct catalysis of imine formation, a crucial step in cross-linking reactions.Additionally, certain excipients may produce byproducts in moist environments, further promoting cross-linking. For example, corn starch may contain hexamethyl tetramine, which decomposes in humidity, generating ammonia and formaldehyde, thus facilitating cross-linking in gelatin. Moreover, high humidity conditions can induce arginine-arginine cross-linking in gelatin. Elevated temperatures accelerate the rate of cross-linking reactions, hastening the formation of insoluble gelatin networks.Light or ultraviolet (UV)-visible radiation exposure can influence dissolution properties. Intense light exposure correlates with reduced in vitro dissolution rates, adding complexity to the matter of gelatin cross-linking in pharmaceutical products.Chemical FactorsSeveral chemical factors can exacerbate gelatin cross-linking in pharmaceutical formulations (Table 2). HumidityHeatLightExcipients or APIs with carbonyl functional groupAldehydes (furfural, acrolein, formaldehyde, glyceryl aldehyde) and ketonesIminesSugars (glucose and aldose sugar)Oxidising agentPEGs (containing peroxide/aldehydes)Metal ions (colorants/dyes)Sulfated polysaccharides (chondroitin sulfate)Table 2: Causative agents for cross-linking.One prominent contributor is formaldehyde, which can be released from various sources commonly found in formulation excipients. These sources include plasticisers, preservatives and polyethylenated compounds, such as polyethylene glycol (PEG). Interestingly, ethers of PEG, aliphatic alcohols or phenols, polyethylenated glycerides and non-ionic surfactants can all contribute to formaldehyde release, thus promoting the cross-linking of gelatin. PEGs, frequently employed as solvents in pharmaceutical formulations, can release low-molecular-weight aldehydes when exposed to aerobic conditions, thereby further enhancing gelatin cross-linking. Additionally, aldehydes such as furfural, commonly found in bottles containing rayon coils, have been demonstrated to react with gelatin, resulting in the formation of insoluble cross-linked products.To confirm whether gelatin cross-linking has occurred, instrumental techniques such as various spectroscopies have been applied, including nuclear magnetic resonance (NMR), UV spectroscopy using 2, 4, 6-trinitrobenzene sulfonic acid (TNBS) assay, fluorescence spectrophotometry (FS), near infrared (NIR) and Fourier transform-infrared (FT-IR). However, it is important to note that these spectroscopic techniques may have limitations for identifying cross-linking in gelatin capsule shells when the formulations experience dissolution slowdown due to stress tests in stability studies or a long-time storage of marketed formulations.STRATEGIES TO MITIGATE THE CHALLENGE POSED BY CROSS-LINKING IN GELATIN-BASED FORMULATIONSOvercoming the challenge of cross-linking in a dissolution study is crucial for innovators facing hurdles in the in vitro evaluation of gelatin formulations. Fortunately, there are several ways to mitigate the issue of cross-linking within the formulation. One such approach involves leveraging different grades of gelatin, each exhibiting distinct behaviours regarding cross-linking. Notably, type B gelatin demonstrates reduced cross-linking compared with type A gelatin.Another effective approach involves inhibiting the formation of aldehydes, which are crucial catalysts for cross-linking in capsules. Compounds such as lysine, phenylalanine, glutamine, p-aminobenzoic acid and glycine serve as potent scavengers for carbonyl compounds, obstructing aldehyde interaction with the gelatin shell and thereby significantly reducing cross-linking. Using glycine to scavenge aldehydes in the formulation effectively neutralises reactive aldehydic functional groups, preventing further cross-linking. Furthermore, combining glycine with citric acid proves highly effective, offering dual benefits by scavenging aldehydes and facilitating pH manipulation within the formulation.Other inhibitors, such as semicarbazide, piperidine and hydrochloride, can also modify capsule properties, effectively inhibiting cross-linking. An alternative approach involves using aldehyde-free excipients, presenting a promising avenue for tackling the dissolution challenge. Importantly, safeguarding formulations against moisture, temperature fluctuations and light exposure will also play a pivotal role in maintaining stability and preventing undesirable cross-linking reactions.A collaborative effort between the US FDA’s CDER, the United States Pharmacopeia (USP) and academia in the early 1990s yielded valuable insights into gelatin capsule non-compliance during dissolution tests and its impact on bioavailability.1 Notably, while cross-linking primarily occurs in vitro, the behaviour shifts markedly during in vivo testing. Cross-linked capsules face minimal hurdles in vivo, suggesting a divergence between laboratory and real-world outcomes. This is due to the presence of the enzymes in the gastrointestinal (GI) environment acting as biological scissors, effectively breaking down the cross-linked bonds in capsule shells.This research led to the development of two-tier dissolution testing, which incorporates enzymes into the dissolution medium in some cases to account for potential in vivo enzyme activity, highlighting the importance of considering both in vitro and in vivo data when evaluating drug delivery systems. The USP two-tier dissolution method offers a standardised approach for handling formulations that fail initial dissolution assessments. This methodology aligns well with bioequivalence studies, streamlining processes and reducing associated time and costs.The USP General Chapters Dissolution <711>and Disintegration and Dissolution of Dietary Supplements <2040> offer provisions for incorporating enzymes into dissolution media when dosage forms fail to meet dissolution acceptance criteria due to gelatin cross-linking. More than 25 pharmaceutical products have used two-tier dissolution methods, as per the FDA’s dissolution database and USP standards (Table 1). In particular, GI enzymes such as pepsin and pancreatin have proven effective in breaking down cross-linked gelatin within the stomach, operating within specific pH ranges to optimise protease activity. By integrating these enzymes into dissolution studies, the observed slow drug release in vitro can be addressed effectively. This strategic inclusion ensures that dissolution assessments accurately reflect the intended performance of the formulation, aligning with regulatory standards and facilitating robust evaluation of product efficacy.The implementation of two-tier dissolution testing – primarily introduced in the First Supplement of USP 24 – involves the strategic addition of enzymes to dissolution media. Pepsin, added to acidic mediums or water, aims for an activity level of 750,000 units per litre or less. However, it demonstrates optimal proteolytic activity up to pH 4 and diminishes above pH 5.5, rendering it unsuitable for two-tier dissolution testing when the medium exceeds pH 4.On the other hand, pancreatin USP, included in mediums at or above pH 6.8, targets a protease activity level of not exceeding 1,750 units per litre. Pancreatin, renowned for its wide substrate specificity, boasts enzymes such as trypsin, α-chymotrypsin, carboxypeptidase, lipase and amylase, enabling it to hydrolyse proteins, fats and polysaccharides effectively. With a favourable proteolytic activity range around pH 6–8, pancreatin presents a versatile option for addressing gelatin cross-linking during dissolution testing.While pepsin and pancreatin offer valuable solutions for in vitro dissolution challenges, it is important to acknowledge their limitations in mimicking in vivo conditions fully. Factors such as the presence of bile salts and gastric motility, crucial in vivo mechanisms, are challenging to replicate accurately in routine dissolution testing. At this point, enzymes such as papain and bromelain, derived from papaya and pineapple, respectively, could be considered. These enzymes, not naturally found in the human body, are primarily employed to digest cross-linked gelatin during dissolution tests. Papain, with an optimal pH range of 4–7, and bromelain, optimal at pH 4.5–7.5, both exhibit potent protease activity and can be evaluated using the case in digestive power test, as delineated in the USP monographs.While these remedies offer promise in resolving the cross-linking challenge, careful consideration must be given to the cautionary note regarding the use of other additive media components when designing dissolution media. For example, the inclusion of surfactants such as sodium lauryl sulfate for solubility enhancement can compromise the activity of enzymes, introducing complexities in the two-tier dissolution study (Table 1). In such cases, a prudent approach involves pre-treating cross-linked gelatin capsules with enzyme-containing media devoid of surfactants. This ensures the maintenance of enzymatic activity, thus preserving the accuracy of dissolution testing. By navigating these intricacies thoughtfully, researchers could optimise dissolution protocols to emulate physiological conditions, thus enhancing the reliability of their findings more closely.SUMMARYWhile cross-linking in gelatin-based pharmaceuticals may pose challenges to dissolution during in vitro studies, it is important to note that in vivo dissolution is often unaffected. This is due to the enzymatic activity within the GI tract which digests cross-linking efficiently, aiding dissolution. Nonetheless, despite this natural process, several precautions should be taken to ensure regulatory acceptance of the product.Various strategies exist to prevent cross-linking during the formulation stage. These include tailoring gelatin formulations to specific grades, incorporating cross-linking inhibitors, integrating stability enhancers or exploring alternative excipients less prone to cross-linking. These approaches effectively mitigate cross-linking issues.However, if cross-linking does occur during formulation, strategic use of the USP two-tier dissolution method would be crucial, especially in capsule formulations. Optimising dissolution studies in this manner can enhance pharmaceutical evaluations, supporting the reliability and efficacy of drug development processes. Through these proactive measures, researchers can confidently and precisely navigate the complexities of cross-linking in gelatin-based pharmaceuticals.REFERENCEAikman M et al, “Collaborative development of two-tier dissolution testing for gelatin capsules and gelatin-coated tablets using enzyme-containing media”. Pharmacopeial Forum, Vol 24(5), Sep-Oct 1998. Source: Strategies to mitigate gelatin cross-linking in oral solid drug delivery
Read more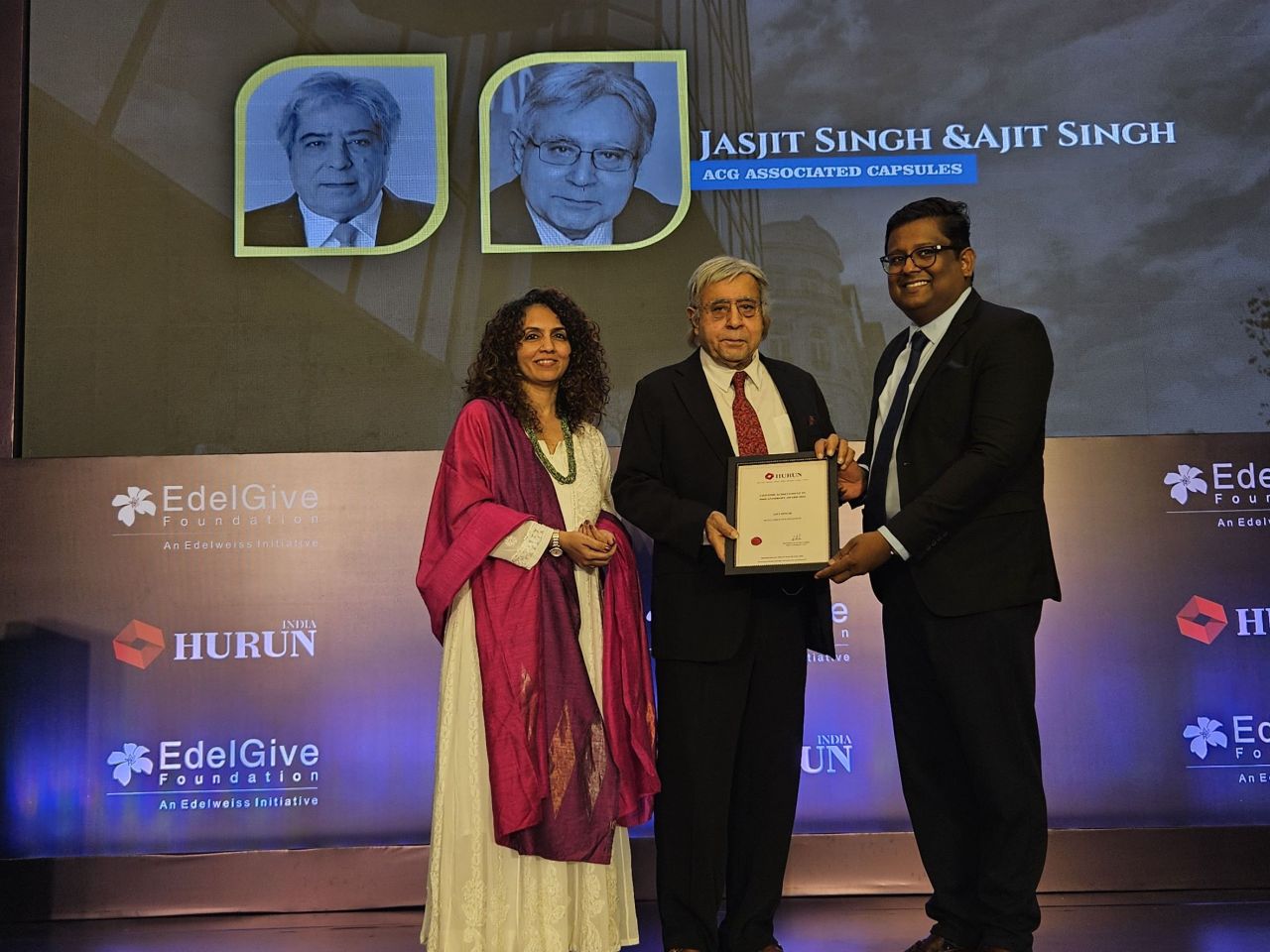
Ajit Singh, Jagjit Singh from ACG receive Lifetime Achievement Award from Hurun…
Ajit Singh, Jagjit Singh from ACG receive Lifetime Achievement Award from Hurun India
Ajit Singh, Chairman, ACG and Jasjit Singh, Vice Chairman, ACG have received Lifetime Achievement Awards from Hurun India.The Singh brothers joined the ranks of previous recipients such as Cyrus and Adar Poonawala of Serum Institute of India, K Dinesh, Co-Founder, Infosys and Jalaj Dani, Co- Promoter, Asian Paints.The Singh brothers acknowledged the support received from the pharma industry, their families, the ACG Global Leadership, ACG team, ACG Cares Foundation, and their customers and suppliers, during their acceptance speech.They also spoke about ACG’s values and emphasised their commitment to industry and philanthropy. Source: https://www.expresspharma.in/ajit-singh-jagjit-singh-from-acg-receive-lifetime-achievement-award-from-hurun-india/
Read more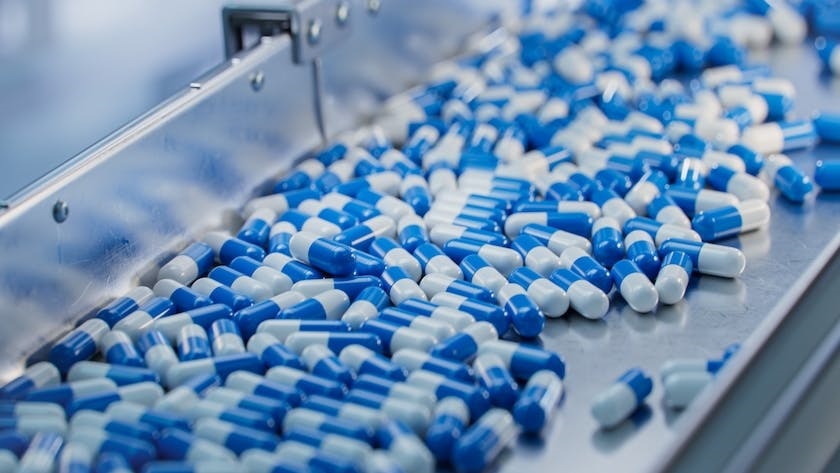
What groundbreaking innovations lie ahead for capsules and how will these devel…
The untapped potential of drug capsules
Today’s health care market is overflowing with myriad products, making it increasingly difficult for businesses to stand out. This is particularly true for oral dosage forms, which currently account for over 80% of the market. This creates a daunting challenge for drug developers who must continually innovate in order to differentiate products. Unlike prescription drugs, the visibility of over-the-counter (OTC) medicines on the shelf play a significant role in consumer decision-making. In a saturated market where consumers are constantly bombarded with choices, product differentiation allows a brand to distinguish itself and gain competitive advantage by highlighting its unique features, benefits or qualities. It can also contribute to building brand loyalty, attracting a specific target audience, and done correctly it can enable a company to charge a premium for its distinctive offerings.Achieving product differentiation in these sectors is not without challenges, however. Stringent regulatory requirements can limit the scope for innovation, necessitating companies to navigate complex approval processes. Moreover, the restrictions on advertising prescription drugs poses a significant hurdle for pharmaceutical companies. Overcoming these challenges requires a delicate balance between scientific credibility, regulatory compliance, and effective marketing strategies to establish a brand as a trusted and differentiated player in the market.Capsules are a widely adopted oral dosage form for pharmaceutical use and are favored by formulators for their versatility. Patients and consumers appreciate capsules for their convenience. They offer a convenient and easily ingestible option for delivering a range of active ingredients, ensuring high dosage adherence. Nevertheless, researchers may have overlooked the potential of capsules as a product differentiator. Despite the continual advancements, the pharma industry has yet to witness a revolutionary breakthrough in the design or functionality of empty hard capsules. The question looms: What groundbreaking innovations lie ahead for capsules, and how will these developments redefine their role in drug delivery? Capsules for every purposeCapsules offer a versatile range of ready-to-use options that extend beyond the more conventional immediate-release applications for powders. For example, the possibility of delayed-release and enteric capsules have proven invaluable for formulations like enzymes and probiotics, requiring protection from stomach acid and necessitating targeted delivery in the intestines. Delayed release ensures that active ingredients reach their intended site of action, enhancing the efficacy of the pharmaceutical or nutraceutical products in question.The ability to encapsulate liquids, semi-solids, and pastes in a single unit also sets capsules apart from other dosage forms. This diverse application supports precise dosing, as compared to solutions and suspensions dispensed via bottles. Capsules also offer a unique solution for formulating poorly soluble drugs, enabling the use of lipids as a carrier to enhance their solubility and bioavailability. They offer a plethora of liquid-filled combinations, such as capsule-in-capsules, pellets-in-capsules and tablets-in-capsules which, when delivered in clear transparent capsules, also provide an aesthetic appeal to the final product. In addition, the smooth surface and easily ingestible nature of capsules contributes to a positive consumer experience, a crucial factor in today’s competitive landscape.Moreover, the unique advantage of encapsulating various active ingredients — even if they are incompatible — within a single capsule presents new possibilities. This addresses specific patient compliance challenges, by offering a convenient means of administering multiple medications or supplements simultaneously, to help simplify treatment regimens.Beyond conventional methods The simple idea of sprinkle capsules, utilizing standard capsules in the drug delivery system, stands as an excellent example of value-added product differentiation. This innovation, made possible through capsules, sets it apart from other oral dosage forms. It offers significant benefits, particularly to geriatric and pediatric patients with swallowing difficulties, where a capsule can be opened to disperse its contents over liquid or soft food for ingestion. And, in both cases, the convenience and adaptability of sprinkle capsules contribute to improved patient compliance.Tabsules — featuring a caplet enclosed in two identical capsule shells — provide a multifaceted approach to product enhancement. Not only do they offer tamper-proofing, serving as a visible indicator of product integrity, but tabsules also offer a competitive advantage by providing an innovative approach to existing formulations without the need for a comprehensive reformulation. This innovation allows companies to refresh their product presentation without compromising the established formulation. Additionally, tabsules contribute to an improved customer experience by masking the potentially bitter taste of tablets and facilitating easier swallowing.Clinicaps are capsules with unconventional dimensions customized to enable execution of double-blind clinical trials. These are engineered with relatively longer caps to ensure a tamper-evident design. They have broader width and available in different lengths which facilitates the concealment and blinding of large or uniquely shaped tablets or other forms of solid oral dosages. This unconventional design can be leveraged to serve as a visual differentiator, enhance aesthetic appeal and communicate a sense of innovation adding value and uniqueness in a saturated market. Naturally clean capsulesToday’s consumers are well-informed and are increasingly conscious of what they’re consuming. This has translated into a rising demand for all things natural and clean. In recent years, the shift from animal-sourced gelatin towards plant-based alternatives has marked a significant evolution in the realm of empty hard capsules. Among these alternatives, hydroxypropyl methylcellulose polymer (HPMC), has emerged as the front-runner, holding an undeniable dominance in the capsule market. HPMC caters to vegetarian and vegan consumers, while delivering performance characteristics comparable to gelatin. This remarkable balance of suitability and performance has cemented HPMC's position as the leading capsule polymer. In line with this growing demand for animal-free products, new-generation polymers like pullulan and starch are also gaining prominence in capsule manufacturing. These polymers, renowned for their exceptional film-forming properties and stability, are making waves as compelling alternatives. Their versatility allows them to encapsulate a diverse range of formulations, catering to the evolving needs of the pharmaceutical and nutraceutical industries.With natural choices gaining prominence, the evolution of capsules extends beyond the choice of polymers to encompass the coloring agents used. Today's capsules can now be colored using natural colorants derived from fruits, vegetables or plant-based sources.Transformative capsule customizationToday, almost endless capsule customization options exist — helping to make brands become instantly recognizable.For example, the introduction of capsules with a pearl-like finish offers exciting possibilities for creating aesthetically appealing products, particularly for nutraceuticals or cosmetics. This innovative approach aligns with premium consumer expectations, adding elegance and luxury to capsules to help them stand out on shelves. Furthermore, the array of customizable printing options for capsules can enhance product distinctiveness and brand appeal. From intricate logos to specific color combinations, these techniques allow companies to align capsules with brand aesthetics.360° printing — a technology that's difficult to replicate — safeguards capsules from counterfeiting. Printing dosage information, branding elements or unique patterns can enhance product recognition and foster a stronger connection between the product and its brand, aiding their visibility on market shelves — and recognition by consumers. Additionally, capsule printing aids polypharmacy patients, particularly the elderly, in correctly identifying medications in order to prevent potential mix-ups.Capsules: a testament to formulation innovationIn essence, capsules not only serve as a vehicle for drug delivery, but also stand as a testament to innovation in pharmaceutical formulations. Their adaptability to diverse release profiles, compatibility with different types of formulations, and ability to simultaneously enhance both bioavailability and patient compliance make them a cornerstone in the pursuit of effective and patient-centric health care solutions. As the industry continues to evolve, capsules remain steadfast and adaptable vehicles for delivering health-promoting substances, contributing to the broader landscape of product differentiation. About the AuthorShincy Jacob | Product Manager, ACG CapsulesSubhashis Chakraborty | Head, Global Product Manager, ACG CapsulesReference- https://www.pharmamanufacturing.com/
Read more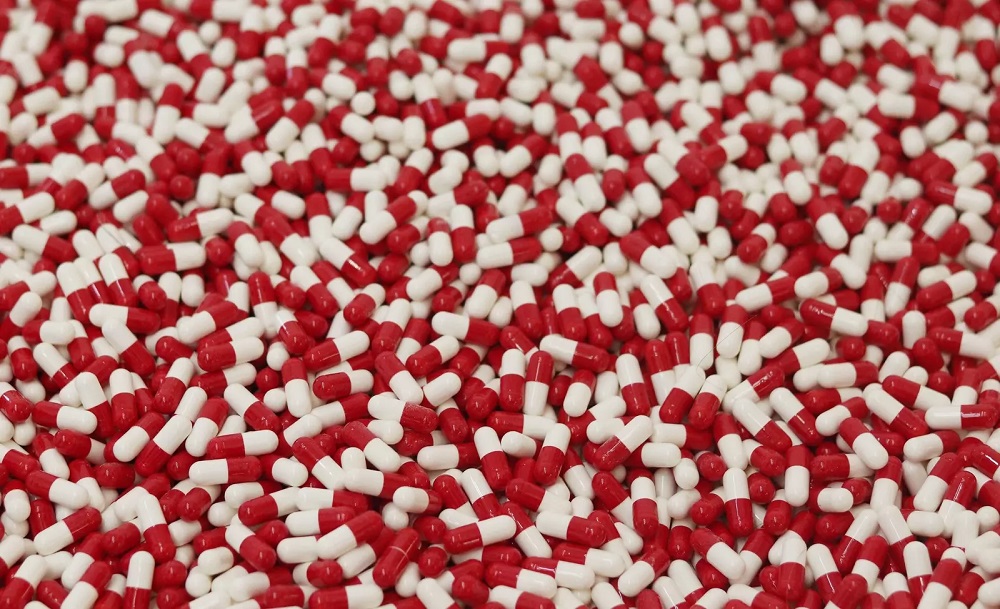
Third-generation capsules: What lies ahead for drug delivery
Third-generation capsules: What lies ahead for drug delivery
• Capsules offer benefits over other forms of medication, including ease of self-administration, precise dosing and targeted delivery.• They can be used to treat a range of conditions and produced at lower cost than other dosage forms, with a longer shelf life.• Advances in combination liquid fill and two-in-one capsules look set to revolutionize drug delivery to the benefit of all.The story of modern-day healthcare is often told through the lens of drug-development in medical sciences, and rightly so. However, the role of pharmacology and drug delivery systems cannot be overstated.In the last four decades, capsules have emerged as a crucial device for advancing healthcare across continents. They offer obvious benefits over other forms of medication, including ease of self-administration, precise dosing and targeted delivery.They are used to treat a range of conditions and can be produced at a lower cost than other dosage forms. They also have longer shelf life, are easier to store and transport to the last mile – other benefits include taste masking, as well as being aesthetically pleasing and tamper evident.Capsules have been around for more than 100 years and, with an impeccable track record and with billions of units manufactured every year, they lead the fight to make medication more safe, accessible and affordable in high- and low-income countries alike. As the world's population grows and ages and diseases rise, the humble capsule also evolves.A couple of Frenchmen are credited with patenting the capsule in 1834 – a small gelatine shell enclosed with a drug, released after ingestion. In their early days, what we called the first-generation, capsules were unstable, prone to cracking and leaking, unpackaged and thus unsanitary and thereby potentially dangerous for patients.Absence of automated filling machines also created limitations on how many capsules can be filled manually and stuck together by workforces. I personally have had a front-row seat to the evolution of capsules.Advances in capsule technologyAdvances in technology led to the development of packaging that has added shelf life, making them more stable and reliable, and the advent of automated filling machines increased productivity, decreased human intervention making them more hygienic and reducing possibilities for human error.Cut to 2000s, the second generation of capsules really pivoted and scaled from animal-based gelatine to plant-based cellulose. Though the technology existed previously, enhanced scale made these capsules more accessible to people with dietary restrictions and addressed ethical concerns on animal products.Capsules are no longer limited to delivering drugs in powder form, as advances in materials and manufacturing have led to diversification in ingredients that can be encapsulated. They are a versatile drug delivery system that can be used to deliver various formulations, including granules, pellets, pastes and even liquids.Not just for humans, capsules have evolved for making animals drug delivery easier. Flavouring to improve the intake of capsules is another catching trend, which is used for making medicines for pets and cattle.Advances in materials and manufacturing processes have led to a diversification in the kind of ingredients that can be encapsulated. The shell of a capsule can be leveraged to design capsules for delayed-release and targeted-release of drugs in the body, enhancing the efficacy of the medication. Manufacturers can also make specific capsule shells that protect the ingredients inside against degradation, thus improving the shelf life of finished products.Combination fill capsules the next revolutionToday we are at the precipice of revolutionizing this technology once again. Advances in combination liquid fill solutions and the probability of scaling world’s first two-in-one (any combination pellets with liquid, or pellets with powder or liquid with liquid, the combinations are versatile) capsule product with a movable membrane, is now a possibility.Collectively these capsule technologies will usher in a new era in new combinations of dietary supplements, and even non-prescription or over-the counter remedies as well as prescription medicines to be delivered in a single dose. Research has shown that water and fat-based liquids are often necessary for the proper absorption of active ingredients in the digestive system.By providing these components in the liquid portion of the capsule products, the bioavailability – the ability of a drug or other substance to be absorbed and used by the body – of the key ingredients can be considerably improved. The more bioavailable a product is, the greater its beneficial effect on the body. As a result, lower dosages may be required, side effects are potentially reduced, and the efficiency of delivery is substantially boosted.This revolutionary breakthrough also allows previously nonviable combinations to be delivered simultaneously. Various liquids, including oils, can be contained within a product together with other active ingredients. This allows for a single capsule to deliver multiple ingredients, resulting in an unprecedented level of convenience and an innovative product delivery. This technological breakthrough is a solution to current formulation challenges with many combination therapies, including incompatible ingredients or molecules.In the end, we are left with one question – what can you buy today for $0.20, which is reliable, safe to consume and helps you get better? That you trust the health of your family with? Capsules are arguably the safest and most reliable way to deliver medicine and as the march of progress continues in the fields of science and medicine, they continue to offer opportunities for innovation and will remain relevant in the years and decades to come. Source: https://www.weforum.org/agenda/2023/05/next-gen-capsules-drug-delivery/
Read more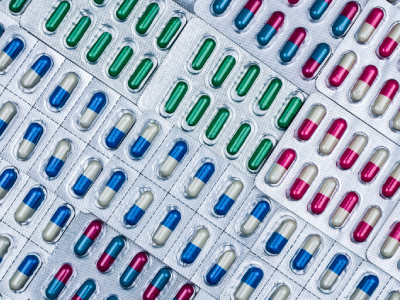
Capsule Manufacturing Technology: Innovations Shaping the Future
The pharmaceutical capsule manufacturing industry stands at the forefront of innovation, continuously evolving with new technologies and trends that drive efficiency, improve product quality, and address the complexities of modern medicine. The past decade has witnessed significant strides in capsule manufacturing technology. Each step has been optimized for efficiency, stability, and compliance with ever-tightening regulations. This article delves into current trends, technological advancements, and prospects in capsule manufacturing. Informed by expert opinions, it draws from interviews with industry professionals spanning the pharmaceutical capsule manufacturing landscape.Manufacturing TechnologyCapsule manufacturing technology has undergone significant transformations driven by the pursuit of enhanced efficiency, precision, and versatility. Traditional encapsulation methods, such as manual filling and sealing, have gradually given way to automated processes leveraging cutting-edge machinery and robotics. High-speed encapsulation systems with advanced dosing mechanisms and quality control features have emerged as a game-changer.These cutting-edge machines have revolutionized production workflows, allowing pharmaceutical companies to meet the rapidly escalating demand for medicines while maintaining strict product quality. With the ability to encapsulate thousands of doses per hour, these systems have increased production speed and reduced manual labor, ultimately saving time and money. Incorporating quality control features, such as automated weight checks and accuracy monitors, ensures that every dose meets the high standards of the pharmaceutical industry. These high-speed encapsulation systems have transformed pharmaceutical production, enabling companies to meet growing demand and uphold the highest product quality and safety standards.AI in ManufacturingIntegrating automation and AI into capsule production processes represents a transformative leap forward in manufacturing efficiency and productivity. ACG’s capsule manufacturing factory in Pithampur, India, was recently incorporated into the World Economic Forum’s Global Lighthouse Network. ACG’s achievement as the world’s first capsule manufacturing facility to join this prestigious network underlines the pivotal role of automation in shaping the future of pharmaceutical production. At the heart of ACG’s success lies the adoption of generative AI, a cutting-edge technology that has revolutionized standard operating procedures (SOPs) and workforce training.“Our adoption of generative AI was a key reason for ACG’s selection.” Says Anil Andrade, Vice President of Global Sales at ACG World. “The team developed and deployed an AI-driven standard operating procedure (SOP)-interfacing co-pilot. Our in-house data science team drew from 200+ quality, manufacturing, and printing SOPs, maintenance instructions, and case sheets to build a learning model in just two weeks. It was then deployed over 4-6 weeks across multiple channels using the web, mobile, and kiosks to train shop-floor personnel. Using gamification with leader boards, rewards, and recognition, the system has supported a 44% rise in workforce productivity and a 30- 40% reduction in mean time to repair, resulting in a 98% reduction in critical defects.”This shift towards automation and leveraging modern technology in capsule manufacturing enhances operational efficiency and fosters a culture of continuous improvement and innovation. By harnessing the power of AI-driven technologies, manufacturers can optimize production workflows, mitigate risks, and drive sustainable growth in an increasingly competitive market landscape.Advancements in Soft Gel TechnologyAdvancements in soft gel technology have propelled the pharmaceutical industry towards more efficient and sustainable manufacturing practices, catering to both consumer demand and regulatory standards. Soft gel capsules, characterized by their versatility and suitability for large manufacturing batches, have become increasingly popular in recent years. Nutraceuticals have also adopted the use of soft gel capsules. However, challenges such as cross-linking between the capsule shell and the fill and leaking soft gels have prompted innovation in gelatin technology to address these concerns. GELITA, a manufacturer of collagen peptides, collagen, and gelatin, has innovated a solution to this pain point.“Specific gelatin grades help to avoid cross-linking – no matter how challenging the fill is and even under difficult storage conditions, the stability and shelf life of soft gel capsules can be improved.” Says Jessica Pföhler, Global Marketing & Innovation Management – Business Unit Performance Solutions, GELITA, “We have been able to develop pharmaceutical-grade soft gel gelatin that helps manufacturers to improve soft gel seams and, thus, avoid leaking soft gels, increasing machine speed, and even reducing the ribbon thickness (less raw material use for production) and not waste raw materials – especially when it comes to expensive fills. All this leads to improved efficiency, lower production costs, and more sustainable handling of raw materials and can be achieved by changing only one parameter in the production process: the right gelatin.”Furthermore, the demand for enteric soft gel capsules, designed to dissolve in the small intestine instead of the stomach, has surged due to their ability to protect acid-sensitive ingredients and enhance consumer compliance. Traditionally, enteric capsules require a separate coating process, adding complexity and cost to production. However, with the advancements in gelatin technology, GELITA has now enabled the production of truly enteric soft gels in a single step, streamlining manufacturing processes and making enteric technology accessible to all soft gel manufacturers.Advancements in soft gel technology, driven by innovative gelatin solutions, are reshaping capsule manufacturing by enhancing stability, efficiency, and sustainability. By addressing key challenges such as cross-linking, leaking, and enteric delivery, these advancements empower manufacturers to deliver safe, compliant, and high-quality products to consumers.Trends Shaping Capsule ManufacturingConsumer demand for personalized healthcare solutions has spurred a trend toward customized capsule formulations tailored to individual patient needs. From dosage adjustments to incorporating specific active ingredients, manufacturers increasingly embrace flexibility in capsule design and composition. This trend enhances patient adherence and therapeutic outcomes and fosters brand loyalty and differentiation in a competitive market landscape.Personalized HealthcareThe expanding trend towards personalized healthcare is paralleled by the rapid evolution of nutraceutical technology, exemplified by innovations such as Sidebyside dietary supplements. Sidebyside products represent a groundbreaking advancement in oral dose capsules. Using a three-piece capsule design, Sidebyside capsules feature a unique cup-shaped divider membrane separating wet and dry ingredients or incompatible actives within the same product. This innovative design allows for simultaneous but separate housing of ingredients, ensuring optimal efficacy and compatibility. With both chambers dissolving simultaneously upon ingestion, Sidebyside supplements facilitate the coordinated release of ingredients, leading to enhanced nutrient absorption, particularly in the presence of oils. ACG’s future Sidebyside roll-out program includes features such as delayed release, catering to the growing market demand for products that provide targeted benefits at different stages of digestion. This innovative approach not only underscores the shift towards personalized healthcare solutions but also highlights the potential of nutraceutical technology to address individualized health needs effectively.Environmentally Sustainable PracticesIn response to growing environmental concerns, the pharmaceutical industry is prioritizing sustainable manufacturing practices across the entire production lifecycle, including capsule manufacturing. From eco-friendly materials sourcing to energy-efficient manufacturing processes, companies are exploring innovative solutions to minimize their carbon footprint and reduce waste generation. Biodegradable capsule materials, reusable packaging, and closed-loop manufacturing systems are among the sustainable initiatives gaining traction in the industry.Pharmaceutical manufacturing companies are increasingly embracing environmentally sustainable practices across various facets of their operations, as evidenced by initiatives from GELITA and ACG. GELITA’s innovative enteric solution for soft gels represents a more sustainable alternative to traditional enteric capsules, offering enhanced environmental benefits. Additionally, GELITA’s development of EASYSEAL gelatin contributes to sustainability by minimizing waste in soft gel manufacturing processes through the prevention of leaks and reduction of raw material usage.ACG’s commitment to sustainability is evident in its adoption of HPMC capsules, which replace animal-derived resources with cellulose, aligning with global efforts to reduce dependence on animal products. Furthermore, ACG’s focus on recyclable and compostable packaging materials underscores their dedication to environmental stewardship throughout the product lifecycle. Investments in renewable energy sources, such as solar farms, and the implementation of Zero Liquid Discharge facilities further demonstrate the industry’s commitment to minimizing environmental impact. Recognitions like the Green Dot award highlight pharmaceutical manufacturing companies’ leadership in environmental sustainability, setting a precedent for responsible and ethical practices in the industry.ConclusionThe pharmaceutical capsule industry is experiencing a transformative shift driven by innovation, sustainability, and personalized healthcare solutions. Over the past decade, advancements in manufacturing technology, including automation and AI integration, have revolutionized the capsule production process[1]es, enhancing efficiency, precision, and versatility.Moreover, the trend towards personalized healthcare has prompted the development of customized capsule formulations tailored to individual patient needs, fostering patient adherence and therapeutic outcomes. Innovations such as Sidebyside dietary supplements exemplify this trend, offering groundbreaking solutions for simultaneous but separate housing of ingredients within a single capsule. Additionally, pharmaceutical companies prioritize environmental sustainability across the entire production lifecycle, with initiatives ranging from sourcing eco-friendly materials to energy-efficient manufacturing processes.Collaborative efforts from pharmaceutical capsule technology and service providers underscore the industry’s commitment to responsible and ethical practices, setting a precedent for a more sustainable and patient-centric future in capsule manufacturing. As the pharmaceutical landscape continues to evolve, these innovations and sustainability efforts will play a pivotal role in shaping the future of capsule manufacturing, ensuring safer, more effective, and environmentally conscious pharmaceutical products for patients worldwide.Publication DetailsThis article appeared in Tablets and Capsules Magazine:Source: https://www.tabletscapsules.com/
Read more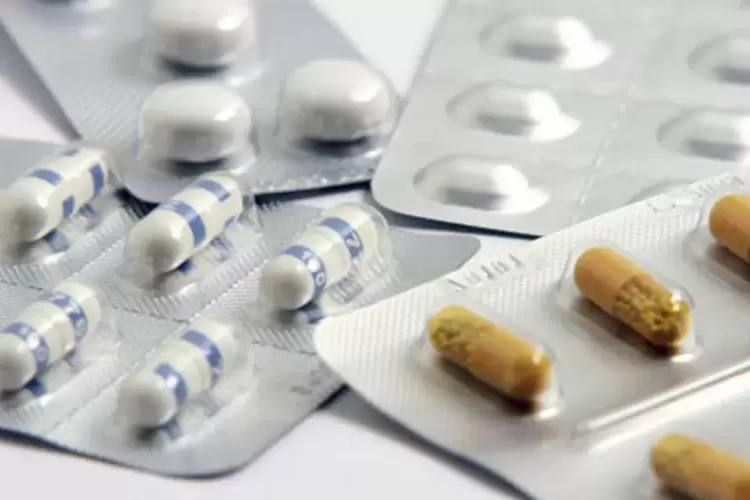
Produto, criado pela ACG, leva de cinco a dez anos para se decompor, enquanto o…
Empresa cria PVC biodegradável para cartões e embalagens de medicamentos
A ACG Packaging Materials, empresa do setor de embalagens plásticas, desenvolveu um plástico biodegradável que se degrada em até dez anos no aterro sanitário, inovação que pode reduzir a produção de plásticos tradicionais nos setores financeiro e de saúde.A empresa, que cria embalagens e soluções para as indústrias farmacêutica e de cartões bancários, desenvolveu uma tecnologia para incluir aditivos para a produção de um PVC de rápida decomposição, chamado de Bio D. Dessa forma, quando descartado, a ação de bactérias em aterros altera a estrutura química do material, acelerando sua degradação.De acordo com o CEO da ACG Packaging Materials América Latina, Daniel Aymard, o objetivo da criação era resolver o problema da geração de resíduos na indústria farmacêutica. Os blisters, plásticos que envolvem capsulas e pílulas de medicamentos, são PVCs de vida útil curta, mas com uma decomposição que pode levar até 500 anos.“Desde os anos 1960, quando a indústria começou a desenvolver soluções para as farmacêuticas, nossa consciência sobre a preservação do meio ambiente aumentou. Por isso, buscamos uma solução mais sustentável para essa realidade”, conta o CEO.Em um aterro sanitário, explica Aymard, a temperatura pode alcançar de 25 °C a 60 °C, o que influencia no tempo de decomposição do produto: na temperatura mais baixa, o PVC levaria dez anos para se desintegrar, mas, com a temperatura máxima atingida, o plástico criado pode se degradar completamente em cinco anos. A ACG ainda garante que o produto passa a se degradar apenas nas condições de temperatura, umidade e acidez de um aterro.A preocupação durante o desenvolvimento, segundo o CEO, era que a indústria não perdesse produtividade no manuseio do material. De acordo com Aymard, a produção se assemelha ao PVC comum em todas as esferas de performance, o que pode garantir uma maior adesão da indústria ao plástico biodegradável.O custo para a produção, no entanto, é 25% mais caro que o PVC comum. De acordo com Aymard, o motivo é a produção mais longa e complexa do que o feito no plástico comum para embalagens. Para o cliente final, o custo não aumentaria. “A embalagem representa até 2% do preço do medicamento. Um aumento de 25% nessa fatia não é de grande impacto para o consumidor, seria questão de centavos de aumento”, conta.Mesmo assim, para Aymard, o produto se destaca no custo-benefício. Ele explica que a maior preocupação sobre a gestão dos resíduos beneficia a produção de produtos biodegradáveis, e que evitar a produção de plásticos duráveis ajuda a reduzir os custos com o lixo posteriormente.A expectativa é que a indústria bancária seja mais receptiva para o produto a primeiro momento. Isso porque a regulação para a produção dos cartões é mais flexível — em algumas financeiras, os cartões já são produzidos a partir de plásticos reciclados, o que pode abrir portas para a inclusão do plástico biodegradável também. Para as farmacêuticas, a preocupação é com os critérios de regulamentação das embalagens, o que ainda deve atrasar a adesão da indústria a métodos mais sustentáveis.Source: Empresa cria PVC biodegradável para cartões e embalagens de medicamentos
Read more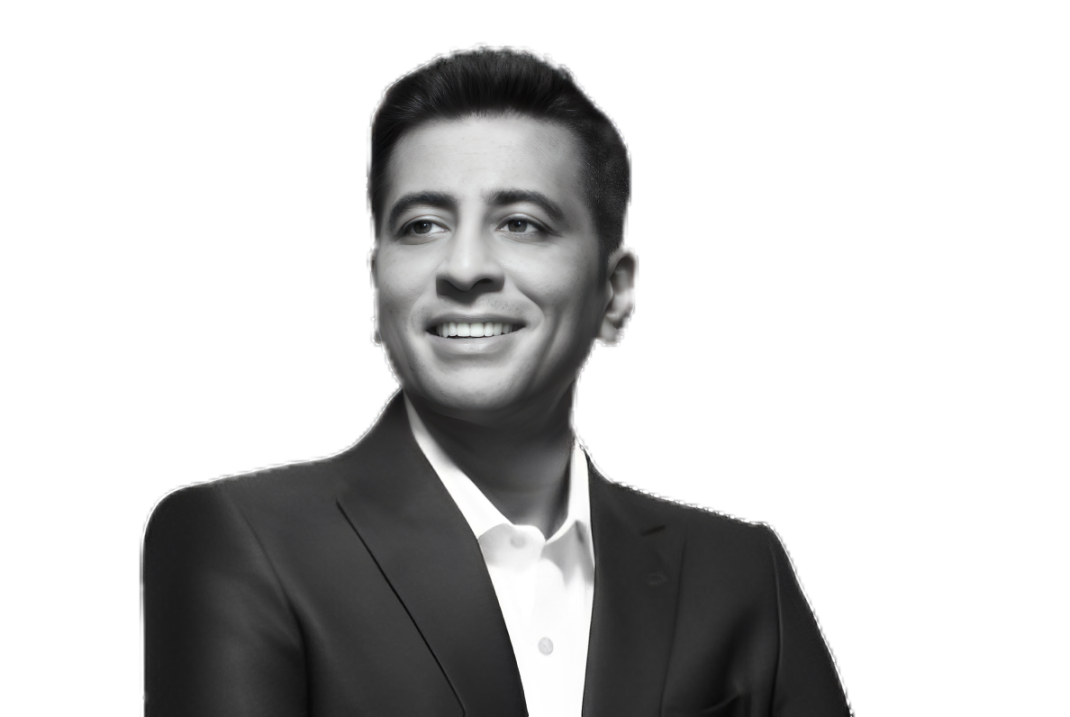
MD Karan Singh explains the journey in achieving the “Oscars of manufacturing”
ACG’s Moonshot Moment : becoming part of WEF’s GLN community
Last month, India’s largest capsules maker and the world’s second-largest – ACG – was feted in Davos, on joining the World Economic Forum’s Global Lighthouse network.“Lighthouses” are a beacon of sorts, when it comes to adopting advanced technologies to transform manufacturing, and globally there are 153 certified Lighthouses, across industries.ACG Managing Director Karan Singh explains their journey in achieving the “Oscars of manufacturing”. As a supplier to every other pharma company in India and major global companies – the milestone puts it in a small and elite group that is implementing advanced manufacturing technologies and boosting productivity, sustainability and supply chain resiliency - a beacon for others in the industry.Listen to the podcast at - Spotify, Apple Podcasts and Official Website.( Host: PT Jyoti Datta, Producers: Nabodita Ganguly & Siddharth Mathew Cherian)-----About the State of the Economy podcastIndia’s economy has been hailed as a bright spot amid the general gloom that seems to have enveloped the rest of the world. But several sectors continue to stutter even as others seem set to fire on all cylinders. To help you make sense of the bundle of contradictions that the country is, businessline brings you podcasts with experts ranging from finance and marketing to technology and start-ups
Read more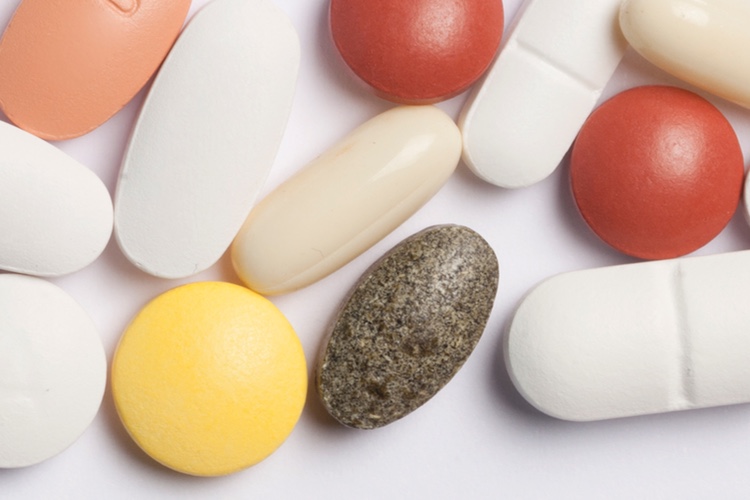
Multi-particulate Formulations
Multi-particulate Formulations - Tablets or Capsules?
After assessing the various routes of drug administration, oral delivery stands out as the safest and, as a result, the most universally accepted among patients. In this context, single-unit dosage forms, including tablets followed by capsules, have been identified as the preferred designs for immediate or modified release formulations. In addition, multiple-unit dosage forms, comprising of discrete particles like pellets or minitablets combined in a single dosage unit, have also gained significant popularity due to their benefits.Multi-particulate Formulations: The Power of ManyTraditionally, these multi- particulates are filled into empty hard capsules using automated capsule filling machines. However, more recent technologies have enabled the pellets to be compressed into multiple-unit pellet system (MUPS) tablets or pellet-containing tablets. Once these special tablets are exposed to the aqueous environment of the stomach, they disintegrate rapidly into individual pellets, releasing the drug like uncompressed pellets filled in capsules. MUPS technology has gained considerable acceptance, particularly in the European market, with a number of products coming to the fore, including: Beloc® ZOK (Metoprolol Succinate SR plus Hydrochlorothiazide), Antra® MUPS (Omeprazole) and Prevacid® SoluTabTM (Lansoprazole), Nexium (Esomeprazole), Galanil PR (Galantamine HBr), Lipidown (Orilistat), Esomezol (Esomperazole SR), TOP ROL XR (Metoprolol Succinate) and Cartia (Diltiazam).Since the total drug is divided equally into many units in a multiple-unit system, it demonstrates several advantages over single-unit systems. When administered orally, these particles (less than two mm in size) distribute evenly across the extensive surface area of the stomach. They behave like fluids and have a shorter retention time. Their small size also facilitates uniform gastric distribution, potentially reducing food induced variations in inter-and intra-individual bioavailability, minimizing chances of side-effects and local toxicity. MUPS tablets can also greatly reduce the risk of premature dose dumping leading to drug degradation or gastric irritation due to any failure in functional coating. This is because a failure of a few units may not be as detrimental as the failure of a single-unit system. Moreover, MUPS tablets also offer the possibility of adjusting dosage strengths, administering incompatible drugs together and combining multi-particulates with different drug-release rates to customize the release profiles.However, despite the various advantages that this unique dosage form provides, the appropriate presentation of these multiple units in the final formulation must be carefully considered. Should these pellets be filled in capsules or compressed into tablets? The best way to determine this depends on a comprehensive understanding of the overall formulation and manufacturing process of the MUPS technology.Key Variables in MUPS Tablet DevelopmentUnlike capsules, MUPS technology requires special excipients and critical process parameters to enable safe and easy compression. This ensures the pellets retain their properties, and that their drug release profile is unaffected. Some of the essential variables determining the success of MUPS tablets include:• particle size of coated pellets,• flexibility and thickness of functional coating,• type and quantity of cushioning agent, • and tablet compression forceIn capsule filling, there are no size limitations for pellets. Usually, larger pellets are preferred as they are easy to manufacture and handle. However, for MUPS, a smaller particle size of pellets is preferred as they are easy to compress and present minimal risk of pellet damage. Special excipients, also referred to as cushioning agents, are used as extra granular material for compression. Since these excipients are available in the powder state, they are often granulated to improve the particle size and density that help to ensure a homogenous distribution of the pellets in the excipient blend. It also minimises the possibility of size separation on the turret during tablet compression, thus maintaining content uniformity in the tablets.It is also important to realize that, by virtue of using smaller-dimension pellets, the resultant surface area increases exponentially as the particle size decreases. This demands higher polymer coating build up, which adds to the processing time and raw material cost. Moreover, the functional polymer coating must be flexible enough for the pellets to deform but not rupture under high compression force. This is typically addressed by using polymers that are inherently flexible or by adding the optimum amounts of plasticizers. Usually, a higher coating build up is preferred in these formulations to compensate for any slight damage without compromising the release profile. Finally, from a process perspective, the compression pressure is the most critical parameter. The mechanical properties of MUPS vary significantly from conventional tablets. Therefore, the compaction force required for pellets and powdered excipients are also very different. And the process becomes more critical if the pellets are functionally coated to modify the drug release. This requires an extremely tightly controlled manufacturing processes. For example, the range of compression force is kept narrow to ensure optimum pressure. Higher compression forces can damage the pellets, while low and inadequate compaction can result in friable tablets. The development of dedicated tablet compression machines with special turret designs and reduced vibration in recent years has helped to prevent blend segregation during operations.Despite all precautions, there remains the potential for pellet damage and the drugs being exposed to the external environment. This can sometimes manifest as minute spots on the surface, which are especially noticeable in sensitive Active Pharmaceutical Ingredients (APIs). However, in most cases, the therapeutic potency may not be significantly compromised. But, since such colour changes interfere with the aesthetics of the final formulation, an additional film coating becomes necessary to mask any possibilities of market rejections.A Prescription for the Drug Delivery DilemmaThe entire MUPS development process is a complex one. The combined impact of the raw materials along with critical process variables makes it extremely labour-intensive, time consuming and expensive. In the case of capsules, however, the absence of additional excipients, ready-made shells to fill, and a simple capsule filling process ensure far less complexity. Moreover, for scaling up or down pellet production for different strengths, capsules are much easier to handle. The absence of any extra granular powder excipients eliminates the possibility of dust generation, thus ensuring a safer and clean working environment. From a patient perspective, capsules also cater to pediatric and geriatric patients with swallowing difficulties by allowing the dispersion of multi-particulates directly into liquid or soft food, usually referred to as the “sprinkle” application. Moreover, encapsulating pellets doesn’t require any additional or specialized infrastructure, expertise, or technology since it employs a standard capsule filling process.Tablets are often favoured over capsules due to the lower production costs, but it is important to look at the bigger picture here. The total cost of ownership (TCO) for developing MUPS tablets extends beyond initial expense, requiring a high degree of precision that is achieved using not only specialised excipients and machinery but also expertise. These often-overlooked factors and hidden costs necessitate the importance of a comprehensive TCO analysis in making informed decisions about choosing the right drug delivery system.The questions we need to anwer include: is it worth developing a product loaded with so many risk factors? Why do ailing patients need to be exposed to unnecessary excipients with added costs? Why are simple available options no longer considered simple? Why are aesthetics more important than patients’ health? It is high time that we, the custodians of health, take cognizance and act accordingly for a better, healthier future.- Dr. Subhashis Chakraborty, Head, Global Product Management, ACG Capsules- Ananya Sen, Corporate Marketing, ACG GroupSource: https://www.pharmaindustrial-india.com/
Read more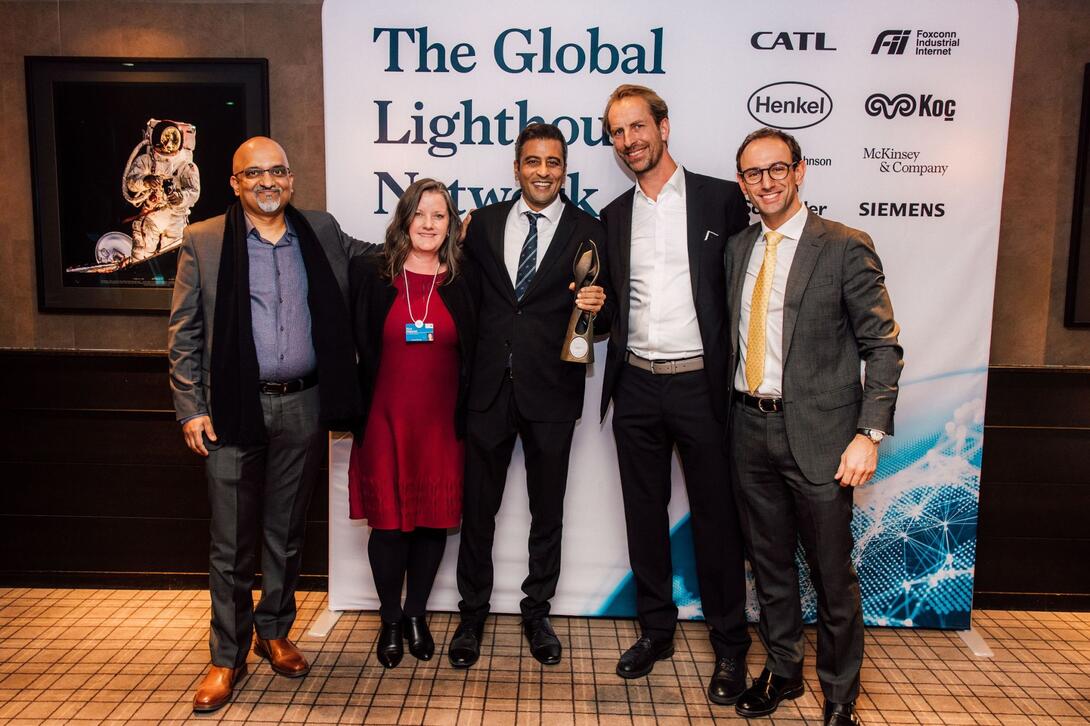
ACG Joins List of WEF’s Global Lighthouse Network
ACG Joins List of WEF’s Global Lighthouse Network
ACG recently announced the inclusion of its capsule manufacturing facility in Pithampur, India, into the Global Lighthouse Network (GLN) by the World Economic Forum (WEF). WEF’s Global Lighthouse Network is a community of manufacturers which shows leadership in using Fourth Industrial Revolution technologies to transform factories, value chains and business models, for compelling financial and operational returns. The GLN has experienced exponential growth since its inception, expanding from 16 to 153 lighthouses. This initiative is a collaboration between WEF and Mckinsey & Company with independent panel of experts designating factories and value chains that join the GLN.The certification comes after audits of 25-plus use cases for the facility that have not only led to manufacturing of superior quality products but also, transformed operations creating new benchmarks for timely production, according to the company. ACG added that the company’s Pithampur factory exemplifies accelerated deployment of GenAI, addressing the evolving skill sets of employees in manufacturing through a Standard Operating Procedure (SOP) and policy interfacing with GenAI.“When ACG embarked on its journey to digital transformation, I recall how Industry 4.0, AI and ML were emerging concepts,” said Karan Singh, managing director of ACG Group. “The focus was directed toward deploying these technologies to enhance productivity and transform the way we operate; aiming to ultimately enhance accessibility to affordable medicines. With an ambitious and dedicated team, we forged a collective commitment to raise the bar of excellence in delivering high-quality capsules worldwide.”For more information, visit www.acg-world.com. Source: ACG Joins List of WEF’s Global Lighthouse Network
Read more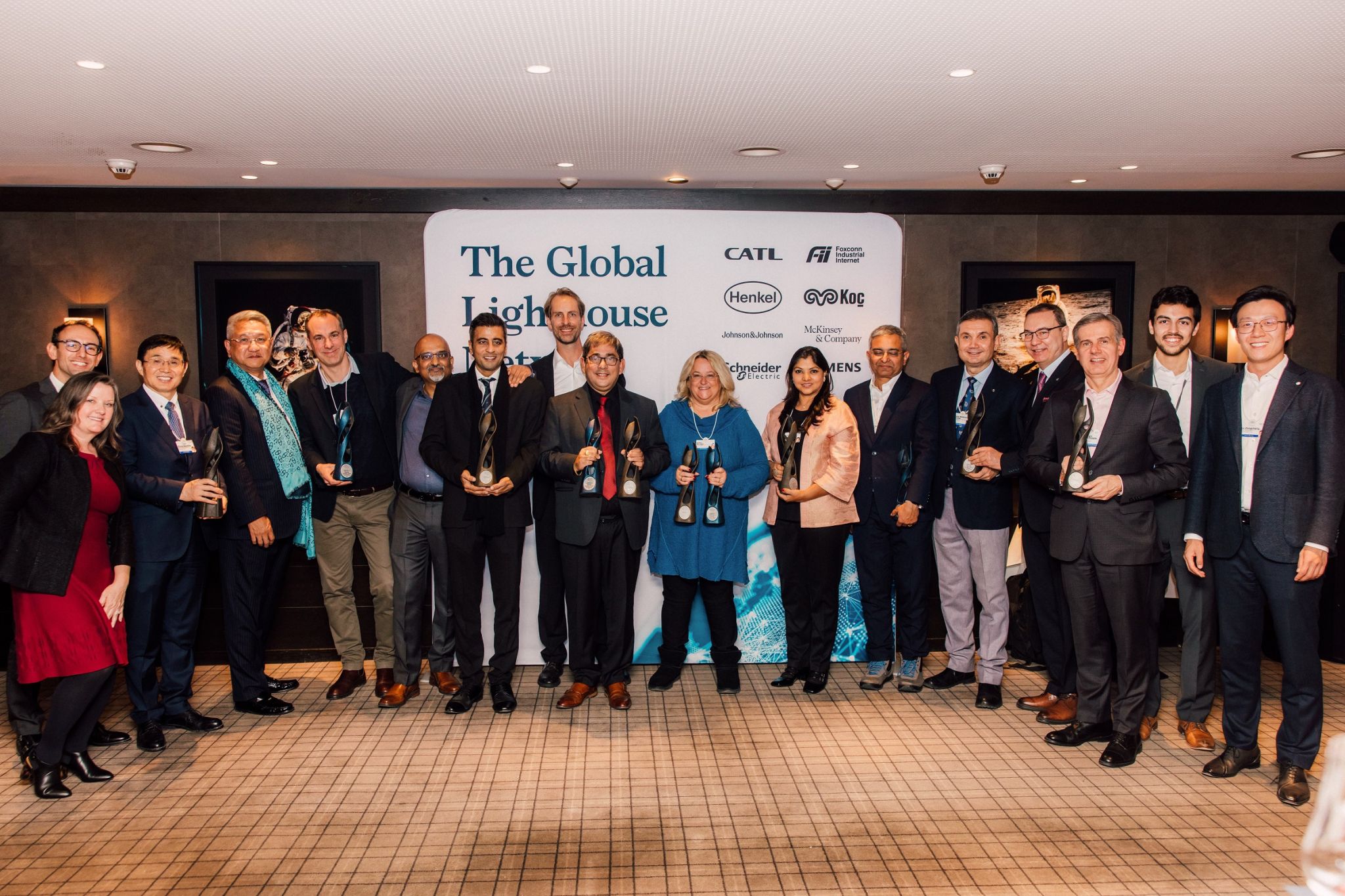
ACG joins coveted list of WEF's Global Lighthouse Network
ACG joins coveted list of WEF's Global Lighthouse Network
ACG, the world's largest integrated supplier and service provider to pharmaceutical industry celebrated the inclusion of its capsule manufacturing facility in Pithampur, India, into the esteemed Global Lighthouse Network (GLN) by the World Economic Forum. WEF's Global Lighthouse Network is a community of manufacturers which shows leadership in using Fourth Industrial Revolution technologies to transform factories, value chains and business models, for compelling financial and operational returns. Remarkably, the GLN has experienced exponential growth since its inception, expanding from 16 to 153 lighthouses. This initiative is a collaboration between WEF and Mckinsey & Company with independent panel of experts designating factories and value chains that join the GLN. The certification comes after robust audit of 25+ use cases for the facility, that have not only led to manufacturing of superior quality products but also, transformed operations creating new benchmarks for timely production. ACG's Pithampur factory exemplifies accelerated deployment of GenAI, addressing the evolving skill sets of employees in manufacturing through a remarkable Standard Operating Procedure (SOP) and policy interfacing with Gen AI. Commenting on the recognition, Karan Singh, Managing Director of ACG Group said, "When ACG embarked on its journey to digital transformation, I recall how Industry 4.0, AI and ML were emerging concepts. The focus was directed toward deploying these technologies to enhance productivity and transform the way we operate; aiming to ultimately enhance accessibility to affordable medicines. With an ambitious and dedicated team, we forged a collective commitment to raise the bar of excellence in delivering high quality capsules worldwide." He further added, "6 years into the journey, I am filled with pride as my team paves a path for leading advance manufacturing and securing a position in the World Economic Forum's prestigious community of Global Lighthouses. This certification is a testament to our commitment to excellence and creating new benchmarks of facilities that are operating on the leading edge of technological innovation. In time to come, we envision taking the learnings and success from this facility to scaling global operations collectively to make it better for our partners, customers, regulators and eventually the pharmaceutical ecosystem." Known for its many accolades, ACG's Pithampur factory had incorporated green features right during the design and layout stages marking a pioneer achievement as they were certified gold by LEED in 2014. Sharing valuable insights and expertise on the state-of-the-art technological advancements, Balajikasiram Sundararajan, Chief Digital Officer, ACG group added "Build the Future, ACG's enterprise-wide digital transformation program is based on four strategic pillars - transforming operations, building smart connected products, enhancing customer experience, and developing digital led business models. Under the ambit of build the future, ACG has been actively developing and implementing state-of-the-art solutions, powered by digital technologies ranging from Industrial IoT, machine learning, deep learning, generative AI, cloud computing, to digital twins, industrial robotics, and extended reality. He further added, "These solutions have helped us to better serve our global customer base by solving critical customer-centric business problems. This prestigious Global Lighthouse recognition from the World Economic Forum further inspires us to continually explore innovative ways of leveraging digital technologies to re-imagine our entire value chain starting from our suppliers to our customers" Kiva Allgood, Head, Centre for Advanced Manufacturing and Supply Chains, World Economic Forum, said, "The Global Lighthouse Network exemplifies the power of digital transformation. Lighthouses are pioneering a path to unprecedented global impact, strategically weaving innovation throughout their expansive network - sculpting both a sustainable future and an era of transformative and lasting change."Press release from the World Economic Forum can be accessed here https://www.weforum.org/press/2023/12/factories-of-the-future-show-how-to-apply-ai-to-benefit-people-planet-and-performance/ About the Global Lighthouse NetworkThe Global Lighthouse Network is a collaborative platform bringing together forward-thinking manufacturers leading the charge in adopting Fourth Industrial Revolution technologies. Leveraging innovations like artificial intelligence, 3D-printing, and big data analytics, Lighthouses drive efficiency, competitiveness, and transformative business models at scale, fostering economic growth while championing workforce augmentation, environmental protection and providing a collaborative learning journey for all-sized manufacturers globally. The Global Lighthouse Network is a World Economic Forum initiative co-founded with McKinsey & Company and counselled by an Advisory Board of industry leaders, including Contemporary Amperex Technology (CATL), Foxconn Industrial Internet, Henkel, Johnson & Johnson, Koc Holdings, Schneider Electric, and Siemens. Factories and value chains that join the network are designated by an independent panel of experts. About ACGFor over 60 plus years, ACG has been innovating the production solutions for pharmaceutical and nutraceutical companies. As the world's most integrated provider of oral dosage products and services, we produce capsules, barrier packaging materials, manufacturing machinery, and visual inspection and traceability solutions. All fully compliant with international standards. Today, ACG fosters long-term collaborative partnerships with customers in 138 countries across six continents. Together, we share a common purpose: to solve the world's greatest health challenges and make it better for everybody we serve.For more information, please contact the ACG media relations team: madhurima.chakraborty@acg-world.com (ADVERTORIAL DISCLAIMER: The above press release has been provided by PRNewswire. ANI will not be responsible in any way for the content of the same) Source: https://www.business-standard.com/content/press-releases-ani/acg-joins-coveted-list-of-wef-s-global-lighthouse-network-123121800955_1.html
Read more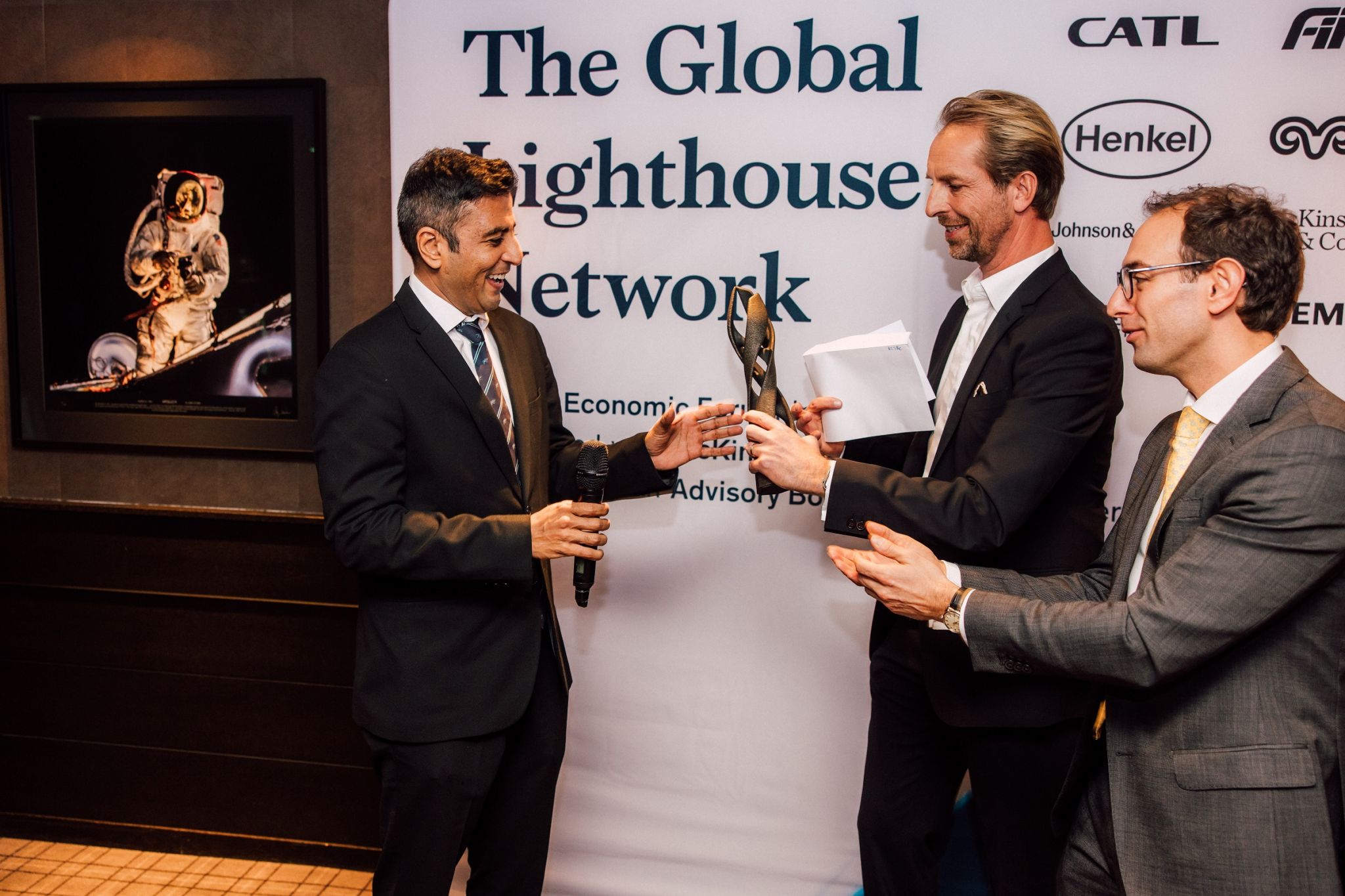
ACG se junta à lista da Global Lighthouse Network do WEF
ACG se junta à lista da Global Lighthouse Network do WEF
A ACG, a maior fornecedora e prestadora de serviços para a indústria farmacêutica do mundo, comemora a inclusão de sua unidade de fabricação de cápsulas em Pithampur, na Índia, na reconhecida Global Lighthouse Network (GLN) pelo Fórum Econômico Mundial. A Global Lighthouse Network do WEF é uma comunidade de fabricantes que demonstra liderança na utilização de tecnologias da Quarta Revolução Industrial para transformar fábricas, cadeias de valor e modelos de negócios, obtendo grandes retornos financeiros e operacionais.A certificação surge após uma auditoria robusta de mais de 25 casos de uso para a instalação, que não só levaram à fabricação de produtos de qualidade superior, mas também transformaram as operações, criando novos padrões de referência para a produção. A fábrica da ACG em Pithampur exemplifica a implantação acelerada da GenAI, abordando os conjuntos de habilidades em evolução na fabricação por meio de um notável Procedimento Operacional Padrão (SOP) e interface de política com a Gen AI.Comentando sobre o reconhecimento, Karan Singh, Diretor Geral do Grupo ACG, disse: “Quando a ACG embarcou em sua jornada para a transformação digital, lembro-me de como a Indústria 4.0, IA e ML eram conceitos emergentes. O foco foi direcionado para a implantação dessas tecnologias para aumentar a produtividade e transformar a forma como operamos; com o objetivo de melhorar a acessibilidade a medicamentos. Com uma equipe ambiciosa e dedicada, estabelecemos um compromisso coletivo para elevar o padrão de excelência no fornecimento de cápsulas de alta qualidade em todo o mundo.”Ele ainda acrescentou: “6 anos de jornada, estou muito orgulhoso de ver a minha equipe abrindo caminho para liderar a fabricação avançada e garantir uma posição na prestigiada comunidade GLN do Fórum Econômico Mundial. Esta certificação é uma prova do nosso compromisso com a excelência e com a criação de novos padrões de referência em instalações que operam na vanguarda da inovação tecnológica. No futuro, pretendemos levar os aprendizados e o sucesso desta instalação para escalar as operações globais coletivamente e torná-la melhor para nossos parceiros, clientes, reguladores e também para o ecossistema farmacêutico.”A fábrica da ACG em Pithampur incorporou características ecológicas logo durante as fases de design e layout, marcando uma conquista pioneira, pois foi certificada ouro pelo LEED em 2014.Compartilhando informações valiosas e conhecimentos sobre os avanços tecnológicos de última geração, Balajikasiram Sundararajan, diretor digital do grupo ACG, acrescentou: “Construa o Futuro, o programa de transformação digital de toda a empresa da ACG é baseado em quatro pilares estratégicos - transformando operações, construindo produtos inteligentes conectados, melhorando a experiência do cliente e desenvolvendo modelos de negócios digitais. Pensando em construir o futuro, a ACG tem desenvolvido e implementado ativamente soluções de última geração, alimentadas por tecnologias digitais que vão desde IoT Industrial, aprendizagem automática, aprendizagem profunda, IA generativa, computação em nuvem, até gémeos digitais, indústria robótica e realidade estendida.O diretor reforça: “Essas soluções nos ajudaram a atender melhor nossa base global de clientes, resolvendo problemas críticos de negócios centrados no cliente. Este prestigiado reconhecimento Global Lighthouse do Fórum Económico Mundial inspira-nos ainda mais a explorar continuamente formas inovadoras de aproveitar as tecnologias digitais para estruturar toda a nossa cadeia de valor, desde os nossos fornecedores até aos nossos clientes”.Kiva Allgood, chefe do Centro de Fabricação Avançada e Cadeias de Fornecimento do Fórum Econômico Mundial disse: "A Global Lighthouse Network exemplifica o poder da transformação digital. Os faróis são pioneiros em um caminho para um impacto global sem precedentes, tecendo estrategicamente a inovação em toda a sua rede expansiva - esculpindo um futuro sustentável e uma era de mudanças transformadoras e duradouras.”O comunicado na íntegra do Fórum Econômico Mundial está diponivel no link: https://www.weforum.org/press/2023/12/factories-of-the-future-show-how-to-apply-ai-to-benefit-people%20-planeta-e-desempenho/Sobre a Global Lighthouse NewtworkA Global Lighthouse Network é uma plataforma colaborativa que reúne fabricantes com visão de futuro que lideram a adoção de tecnologias da Quarta Revolução Industrial. Aproveitando inovações como inteligência artificial, impressão 3D, os Lighthouses impulsionam a eficiência, a competitividade e modelos de negócios transformadores em escala, promovendo o crescimento econômico e ao mesmo tempo defendendo o aumento da força de trabalho, a proteção ambiental e proporcionando uma jornada de aprendizagem colaborativa para fabricantes de todos os tamanhos em todo o mundo.A Global Lighthouse Network é uma iniciativa do Fórum Econômico Mundial co-fundada com a McKinsey & Company e aconselhada por um Conselho Consultivo de líderes da indústria, incluindo Contemporary Amperex Technology (CATL), Foxconn Industrial Internet, Henkel, Johnson & Johnson, Koç Holdings, Schneider Electric e Siemens. As fábricas e cadeias de valor que integram a rede são designadas por um painel independente de especialistas. Sobre o Grupo ACGFundado em 1964 e operando no Brasil há 20 anos, o Grupo ACG é o único fornecedor mundial de soluções de fabricação integradas para a indústria farmacêutica. A empresa recebeu este ano o segundo lugar no Prêmio Sindusfarma de Qualidade, na categoria Fabricantes nacionais de matérias-primas. Conta com uma unidade fabril em Cotia (SP), a ACG Films & Foils, que oferece soluções em embalagens para as indústrias farmacêutica, alimentícia & FMCG (Fast-Moving Consumer Goods), e outra em Pouso Alegre (MG) focada na fabricação de cápsulas para as áreas farmacêutica e nutracêutica. Possui importantes certificações, como GMP, Halal e Kosher, se tornando um importante fabricante e distribuidor para todo o mercado doméstico, Latino-Americano, Norte-Americano e, recentemente, para a África. A ACG tem o compromisso com uma única meta: oferecer um portfólio completo de tecnologias e soluções integradas para a fabricação eficiente de sólidos orais. A multinacional está presente em mais de 100 países e tem mais de 4.500 funcionários em todo o mundo. https://www.acg-world.com/pt/EsclarecimentoA área Empresas em Foco publica notícias elaboradas e enviadas pelas empresas associadas ao Sindusfarma; seu conteúdo é de exclusiva responsabilidade das empresas e não reflete anuência nem posições ou opiniões da entidade.Source: ACG se junta à lista da Global Lighthouse Network do WEF
Read more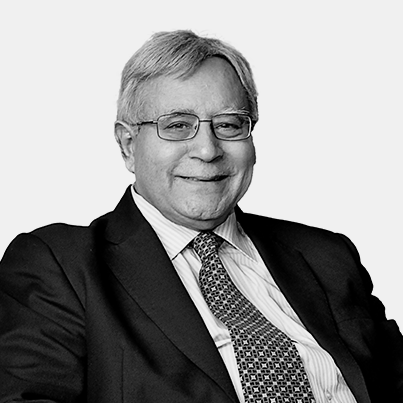
Ajit Singh
Ajit Singh earned his graduation degree from Cambridge University, UK, and post-graduation degree from Harvard Business School, USA. He currently resides in Mumbai, India, and travels widely to study pharmaceutical and allied industries.
Ajit is the Chairman of the ACG Group (formerly known as the Associated Capsules Group of Companies), which is headquartered in Mumbai. He has played a prominent role in the development of the pharmaceutical and allied industries in India and has served as an executive committee member of the Federation of Indian Chambers of Commerce & Industry (FICCI), a regional council member of the Confederation of Indian Industry (CII), Western Region, and other prominent pharmaceutical associations in India. He has also been conferred with prestigious awards for his contributions and thoughtful leadership to the pharmaceutical industry.
Ajit was a founder-member of the Young Presidents’ Organization – India Chapter and the first Indian to be invited to serve on its international board in the USA.
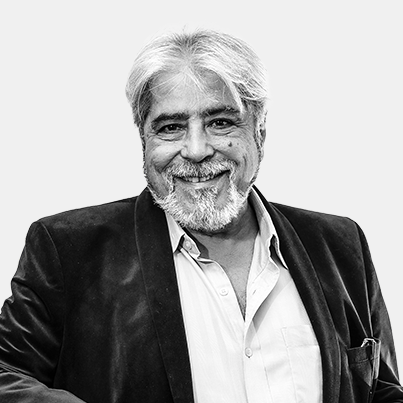
Jasjit Singh
Along with his brother, Ajit, Jasjit started the Associated Capsules Group in Mumbai in 1962.
Jasjit has always been interested in technology – particularly that relating to machine design – and earned a degree in Mechanical Engineering from London University. He has dozens of patents to his credit, and under his leadership the ACG Group has received numerous global awards for technology, excellence and social welfare.
Jasjit has been actively involved with starting new Forums of the Young Presidents’ Organisation. He served as the Chairman of the Mumbai Chapter, and helped found the Kolkata Chapter before becoming a founding President of the World Presidents’ Organisation. Jasjit has also received the Vijay Ratna Award for leadership in Industry, and recognition from UNIDO for his contribution to the fields of pharmaceutical technology and environmental science.
Jasjit’s other interests include self-education, reading, music, collecting rare works of arts and helping young contemporary artists, cooking, and travelling to different parts of the world – especially with his family.
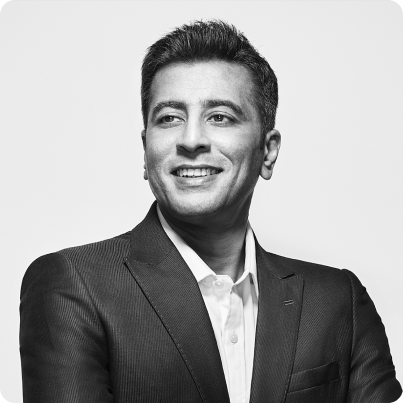
Karan Singh
An organisational psychologist by education, Karan has transformed ACG from a modest Indian business into a world-renowned institution, revolutionising its vision and long-term strategy to ensure global growth. Karan has overseen ACG’s remarkable digital transformation, adopting breakthrough technologies that not only keep medicines safe, affordable, and accessible – but also vastly improve manufacturing and supply chains. Meanwhile, he has led a series of tuck-in acquisitions that ensure ACG pioneers continuously in terms of innovation and scale.
Passionate about converting ideas into growth opportunities, he supports entrepreneurial visions that solve real-world challenges. As an investor and mentor to more than 35 health-tech start-ups, guiding strategy, technology, expertise and networks, Karan seeks to consolidate the next generation of leadership – one that will secure better access and bridge availability across the global health industry.
Karan serves on the India Advisory Board for the India-Brazil Chamber of Commerce, is Co-Chair for FICCI LAC Regional Council, a key advisor to Nasscom, and an active contributor to the Global Lighthouse Network community of the World Economic Forum. Years of keen basketball-playing underpin his leadership, communication, and competitive spirit, and have brought about ACG-NBA Jump, a grassroots programme to give Indian basketballers a global platform.
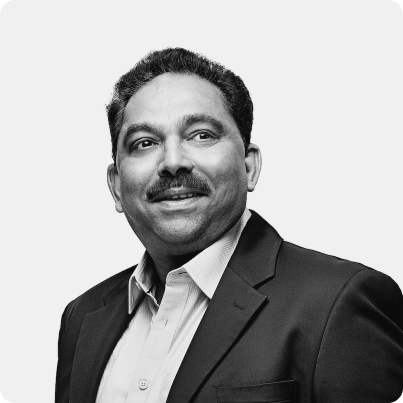
Selwyn Noronha
CEO ACG CAPSULES
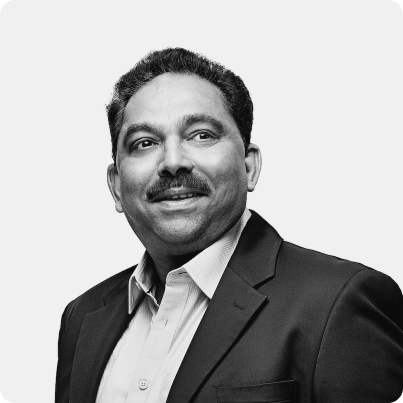
Selwyn Noronha
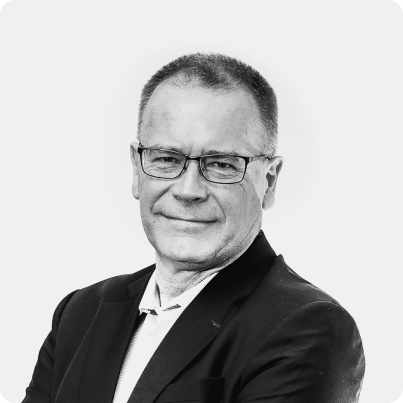
Richard Stedman
CEO ACG ENGINEERING
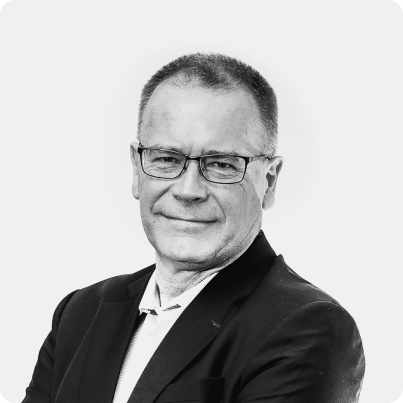
Richard Stedman
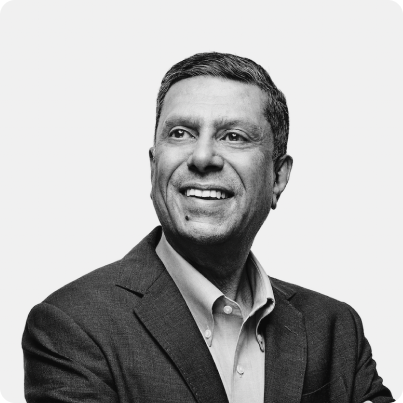
SR Shivshankar
CEO ACG PACKAGING MATERIALS
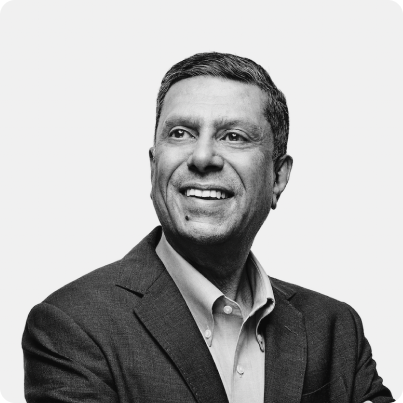
SR Shivshankar
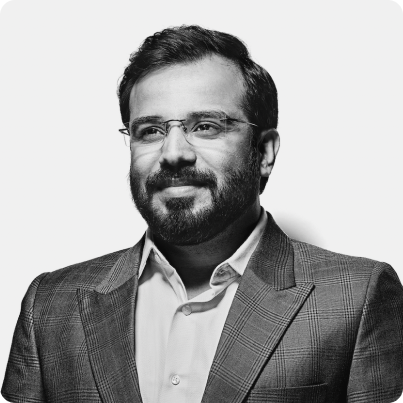
Udit Singh
CEO ACG INSPECTION
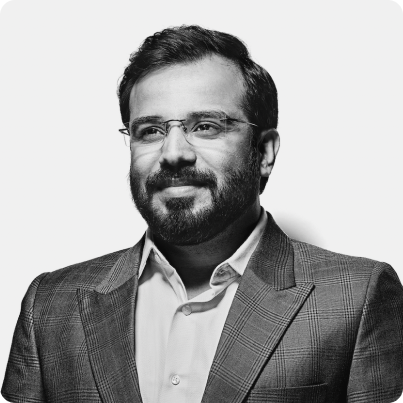
Udit Singh
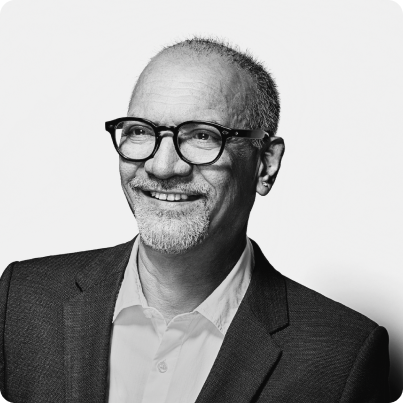
Sunil Jha
Chief Human Resource Officer
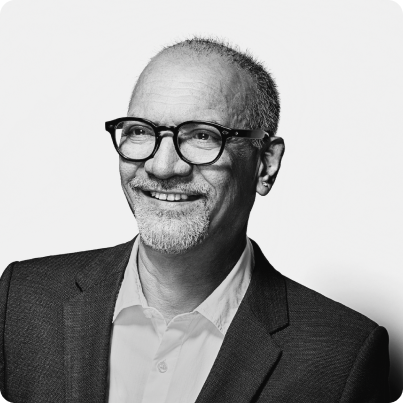
Sunil Jha
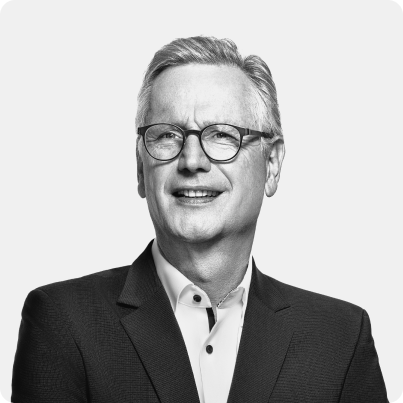
Werner Bongers
CEO SCITECH
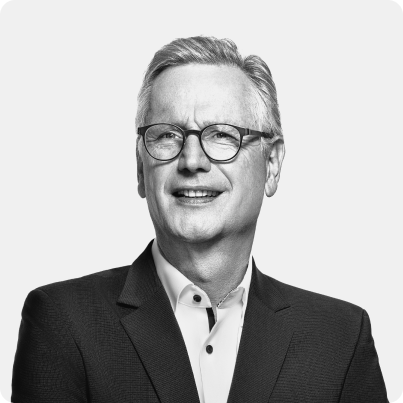
Werner Bongers
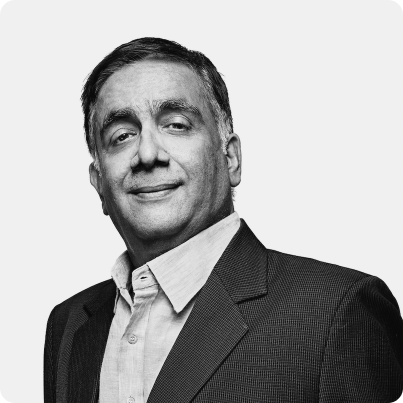
Nitin Desai
Chief Commercial Officer
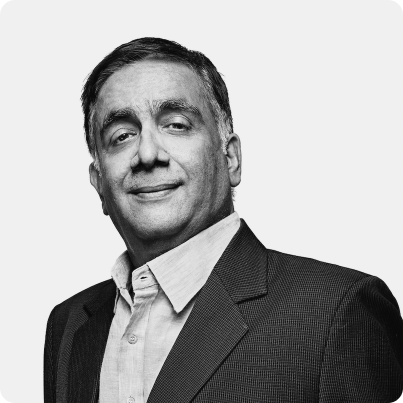
Nitin Desai
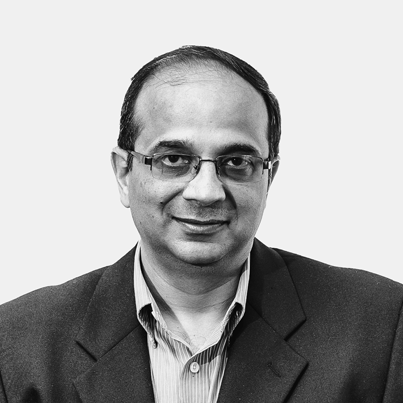
Parag Shah
Chief Financial Officer
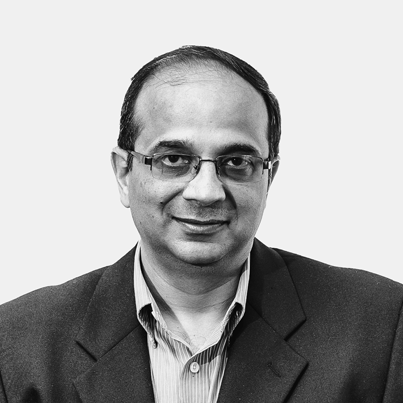
Parag Shah
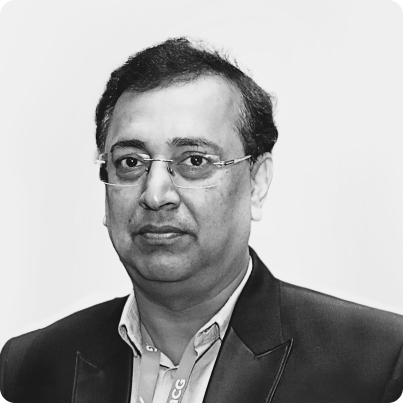
Shankar Gupta
Chief Sales Officer
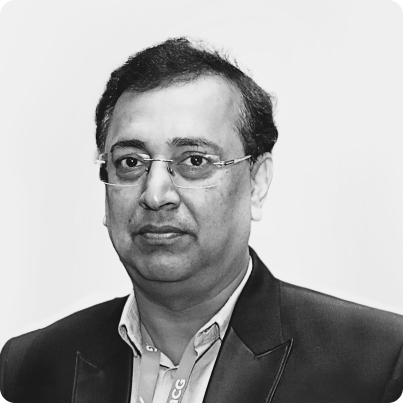
Shankar Gupta
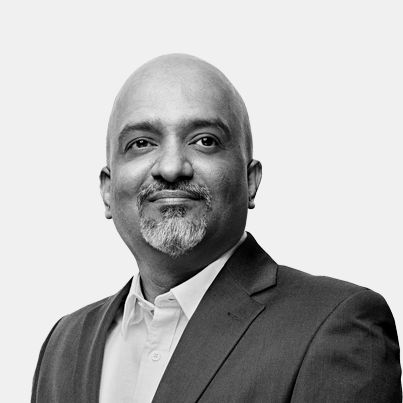
Balajikasiram Sundararajan
Chief Digital Officer
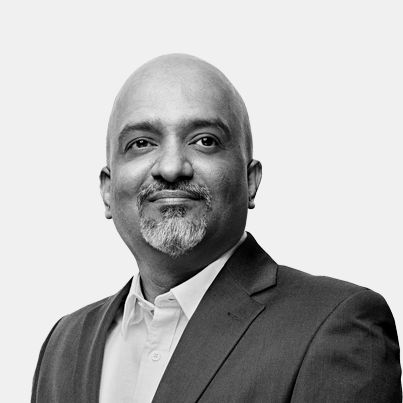
Balajikasiram Sundararajan
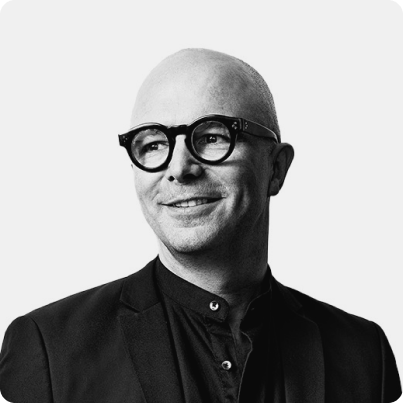
Alexander Robertson
Chief Marketing Officer
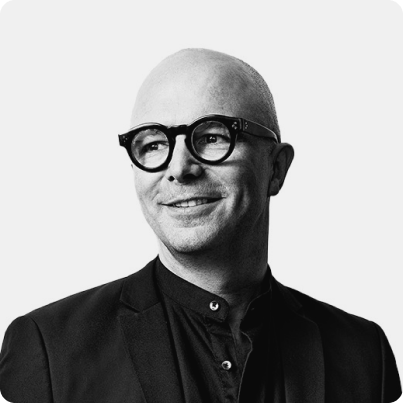
Alexander Robertson
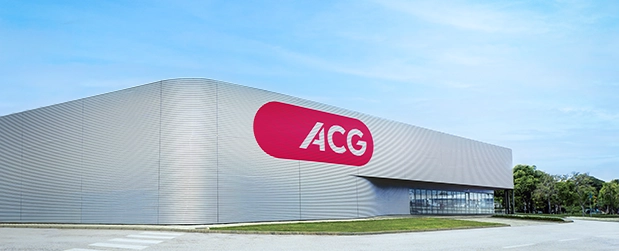
Boilerplate
For over 60 plus years, ACG has been innovating the production solutions for pharmaceutical and nutraceutical companies, that help make people better.
As the world’s most integrated provider of oral dosage products and services, we produce capsules, barrier packaging materials, manufacturing machinery, and visual inspection and traceability solutions. All fully compliant with international standards.
Today, ACG fosters long-term collaborative partnerships with customers in 138 countries across six continents.
Together, we share a common purpose: to solve the world’s greatest health challenges and make it better for everybody we serve.