Virtual Inspections: Embracing the Digital Change
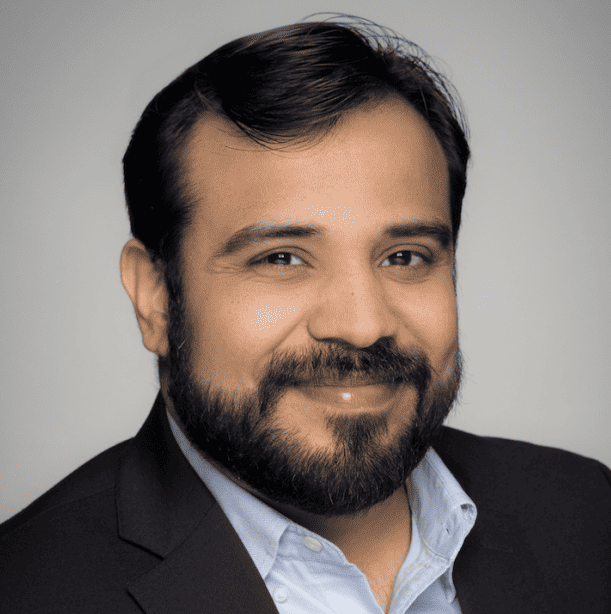
Virtual inspections must become a part of companies’ repertoires if they aim to maintain quality standards in their organisations.
Digital tools and technologies are advancing rapidly – but how can pharma make the best use of them? One area of manufacturing that is ripe for enhancement via digital tools is product inspections.
Udit K Singh, Chief Executive Officer at ACG Inspections explains.
What historical challenges affect inspections today?
Manual inspection methods increase the chance of rejecting an entire batch because of an anomaly in a single tablet or capsule from that batch. Whereas digital tools can identify defects at the individual product level – rejecting the defective products only. These tools also verify that the inspection has been carried out to the required parameters and that data, associated with the inspection, is stored.
When inspecting products manually there is also the potential for defects to be missed. If these products reach the market, they can cause reputational damage to a brand, potentially resulting in lawsuits and revenue losses.
Another historical challenge is that there hasn’t been any real-time qualification and analytics of manufacturing output. In my view, being able to provide assurance that each capsule or tablet has been qualified against the quality standards and a benchmark has been set by aggregators in this space is of crucial importance.
What are the key benefits of digital inspections?
The benefits of digital inspections are immense. Better throughput, improved quality outcomes and higher visibility are all possible to achieve when businesses choose to integrate digital inspections into their operations.
Camera sensors use images captured to determine the chemistry, orientation, hardness and other product characteristics such as moisture. They work at high speed and on fast-moving production lines. Because they remove faulty products before they reach packaging the production performance is optimised. The operators just need to be trained to ensure the standard operating procedures (SOPs) are followed.
Manual inspection is subjective. Humans require training and education and have limitations. For example, manual inspection makes it difficult to distinguish a “look-alike” product, minute variances in colour and other characteristics. Manual inspection is repetitive work, in often brightly lit conditions which means human performance will be varied and subject to fatigue – therefore the quality assurance cannot be validated.
In the past, inspections at single points in a manufacturing plant, such as in-line and end-of-line product sampling were acceptable. Clearly, this type of check wouldn’t provide companies with a full picture. Digital inspections offer manufacturers the opportunity to create better data to support business decisions and the means to view the strengths and weaknesses of processes with improved transparency.
In your view, are there any important limitations that must be considered?
Technology evolution is happening at an enormously fast pace. As pharmaceutical manufacturing is governed by a set of compliance rules the adoption of technology takes time.
You can’t adopt rapid changes in technology because the industry must go through phases of testing, adaptability, efficiency and productivity. By the time they are complete, five years may have already elapsed. Trying to keep up with the pace of technology development is becoming tough.
Regulatory bodies and the pharmaceutical service industry need to collaborate regarding the regulations that become the baseline for technology development. This should allow for faster technology adoption for pharmaceutical companies.
What are your thoughts on current penalties for facilities that don’t comply with regulations?
Patient safety in drug manufacturing is the absolute top priority. There cannot be any compromise. Regulatory bodies are doing everything in their power to ensure that this is the case. If this is managed by imposing penalties, stopping production, recalling products or even questioning manufacturers they have the authority to decide what’s right to protect patients.
However, the methods used to ensure that companies meet the regulation are at the discretion of the manufacturer. For inspections, they could adopt optical inspection using cameras or non-optical methods that use infrared ultrasound – to check the structure of drugs. Regardless of the approach they take, frequent checks and balances will always be their biggest responsibility. Quality checks at all stages of the process from raw material, batch mixing, API production, to the manufacture of the final finished tablet or capsule must be consistent. But the quality assurance process doesn’t stop there, companies must also invest time into evaluating blister packaging and bottles, label print quality, boxing, packing and shipping.
Managing all these aspects of the manufacturing process can be quite intense, but technology can help in streamlining it. If companies choose to embrace the obvious benefits of digital inspections, they will certainly be able to better support patients worldwide.
Source: https://pharmafile.com/news/virtual-inspections-embracing-the-digital-change/