Optimising investment in hot-melt granulation the smart way
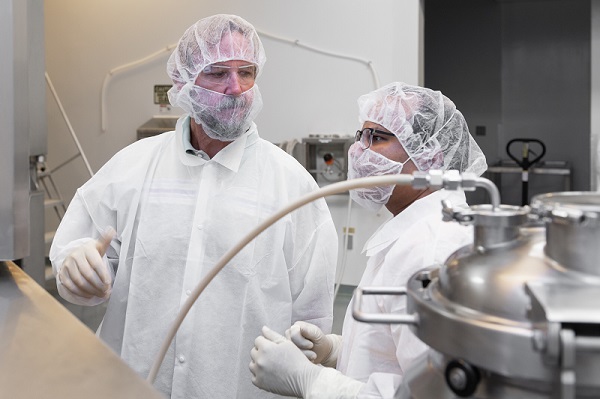
Understanding hot-melt granulation
Traditional granulation methods, such as wet granulation, involve the use of liquid binders and subsequent drying steps, which can be time-consuming and costly. Dry granulation, while eliminating the need for liquids, often results in lower granule strength and poor compressibility.
Melt granulation offers a middle ground. The process employs a meltable binder that remains solid at room temperature but forms liquid bridges between particles when heated. As the powder bed cools, these liquid bridges solidify, creating robust granules with superior density and reduced porosity. The binder remains an integral component of the formulation, eliminating the need for drying steps while producing granules with excellent compressibility.
One significant advantage of hot-melt granulation is its avoidance of aqueous solutions, which can pose risks to moisture-sensitive drugs. As we delve into the various approaches for hot-melt granulation, we will specifically focus on three prominent technologies: high shear granulation, fluid bed granulation, and twin-screw melt granulation.
Capital investment considerations
High shear mixers tend to be the most cost-effective option when it comes to initial expenditures. Their design is relatively straightforward, requiring minimal auxiliary components beyond heating systems and temperature controls. This simplicity keeps installation costs low, making hot-melt granulation an attractive choice for smaller operations or pilot projects.
On the other hand, fluid bed granulators typically incur higher capital costs due to their more complex nature. These systems involve various components, such as air handling units, heating and cooling systems, and spray nozzles. However, if your facility already has a fluid bed equipment in place, adapting this technology for hot melt granulation can be a practical solution. Retrofitting existing fluid bed systems can help you avoid the costs associated with purchasing new equipment.
In the case of twin-screw extruders, while they require substantial initial costs, especially for facilities starting from scratch, they can offer impressive efficiency for large-scale operations. Justifying these upfront expenses is essential, particularly if your facility anticipates high production volumes.
Operating costs and efficiency
Next, let’s turn our attention to operating costs. High shear mixers generally have moderate energy requirements since they rely on mechanical shear rather than extensive heating or air handling. While material waste tends to be low, it’s crucial to manage the process carefully to avoid excess fines that could lead to higher downstream costs. Additionally, the batch nature of high-shear mixers can lead to increased labour costs, as operators must oversee transitions between batches.
Fluid bed granulators, while effective, typically come with higher energy demands due to the need for air handling and heating. But fluid bed technology offers a key advantage: superior temperature control and stability. Unlike high shear mixers, where heat also derives from shear forces, fluid bed systems rely solely on the temperature of fluidisation air. This configuration enables more precise control over the energy input, resulting in a highly regulated granulation process leading to the production of uniform granules with minimal material waste. Their semi-continuous operation usually results in lower labour costs compared to high shear mixing, making fluid-bed granulation a cost-effective option for many facilities.
Twin-screw extruders are noteworthy for their continuous processing capabilities, which significantly enhance efficiencies, particularly in high-volume production scenarios. They effectively use both conductive and shear-based heating within the screw sections, allowing precise control of temperature at various stages. This feature can be especially beneficial when processing binders that require gradual melting and homogenization. While energy consumption may rise with scale, twin-screw systems can still remain cost-effective with minimal material waste, as granules are extruded continuously with minimal product left in the system at the end of a run and reduced manual oversight. Additionally, the continuous nature of this continuous melt-granulation technique reduces the labour required to manage batch transitions, lowering operational costs in high-volume facilities.
Quality control and regulatory compliance
Quality control is a vital component of pharmaceutical manufacturing, and each technology offers distinct advantages in this area. High shear mixers may experience variability between batches, necessitating rigorous quality assurance processes to maintain consistency. Although regulatory compliance is manageable, the extensive documentation required for each batch can increase administrative burdens.
Fluid bed granulators shine in producing consistent, uniform granules, simplifying quality control. They align well with GMP, making validation processes more straightforward, especially in facilities already utilising similar equipment. This familiarity can help ensure smoother operations.
Twin-screw granulators also provide consistent quality due to their continuous processing capabilities. However, their initial validation process can be more complex, particularly for facilities adopting this technology for the first time. Regulatory bodies are increasingly recognising the advantages of continuous manufacturing, but the upfront validation requirements can present a challenge.
Scalability and flexibility
Scalability is another critical factor to consider when choosing a granulation technology. High shear mixers offer moderate scalability, making them suitable for small to medium batch sizes. Their flexibility allows for rapid formulation changes, which is particularly advantageous in research and development settings.
Fluid bed granulators are effective for medium to large batch sizes but require considerable investment to scale up efficiently. While they do possess a degree of flexibility, they cannot pivot as easily as high shear mixers when it comes to formulation changes, making them better suited for stable products.
In contrast, twin-screw granulators excel in scalability, particularly in high-volume production environments. Their continuous processing capabilities allow them to handle large output volumes efficiently. However, it’s essential to note that these systems may lack flexibility; mid-process formulation changes can necessitate downtime, impacting overall production efficiency.
Maintenance and lifecycle management
When evaluating total cost of ownership, maintenance and lifecycle costs are critical considerations. High shear mixers typically require less maintenance due to their simpler mechanical design, which translates into lower lifecycle costs. However, the batch transition process can lead to indirect costs in high-volume settings, where downtime becomes a concern.
Fluid bed granulators can incur higher maintenance costs due to their complex air handling and heating systems. This complexity may lead to increased lifecycle expenses, especially in large-scale operations. Nonetheless, facilities with established fluid bed systems may benefit from their familiarity, which can mitigate some maintenance challenges.
Twin-screw extruders generally present moderate maintenance requirements. Their continuous operation typically results in lower wear and tear compared to batch systems. While specialised maintenance for screws and extruder components may be necessary, they can ultimately provide long-term cost benefits due to reduced material loss and downtime.
Making the right choice
In conclusion, selecting the appropriate hot melt granulation technology requires careful consideration of several factors, including capital costs, operational efficiency, product quality, and facility capabilities. For those with existing fluid bed granulators, adapting this technology for hot-melt granulation often proves to be the most practical and cost-effective approach. The familiarity with fluid bed systems can facilitate smoother implementation and compliance.
High shear mixing may be ideal for smaller-scale operations that prioritise flexibility, despite the potential for increased labour costs. On the other hand, twin-screw melt granulation presents a compelling option for facilities aiming for high-volume production, provided they can justify the initial investment based on expected outputs.
Ultimately, the decision-making process should focus on aligning each technology with the specific needs and objectives of the facility. By thoughtfully weighing the pros and cons of high shear, fluid bed, and twin-screw systems, pharmaceutical manufacturers can ensure they select the most suitable hot melt granulation method for their production requirements.
- Parikh, D.M. (Ed.). (2021). Handbook of Pharmaceutical Granulation Technology (4th ed.). CRC Press. https://doi.org/10.1201/9780429320057
- An ACG 360 webinar https://www.acg-world.com/resources/webinars/webinar-hot-melt-granulation-have-you-looked-yet