We value our partnerships with the media and welcome any inquiries about the ACG Group. Please use the resources on this page, or if you have any specific queries please reach out to the media contact listed below.
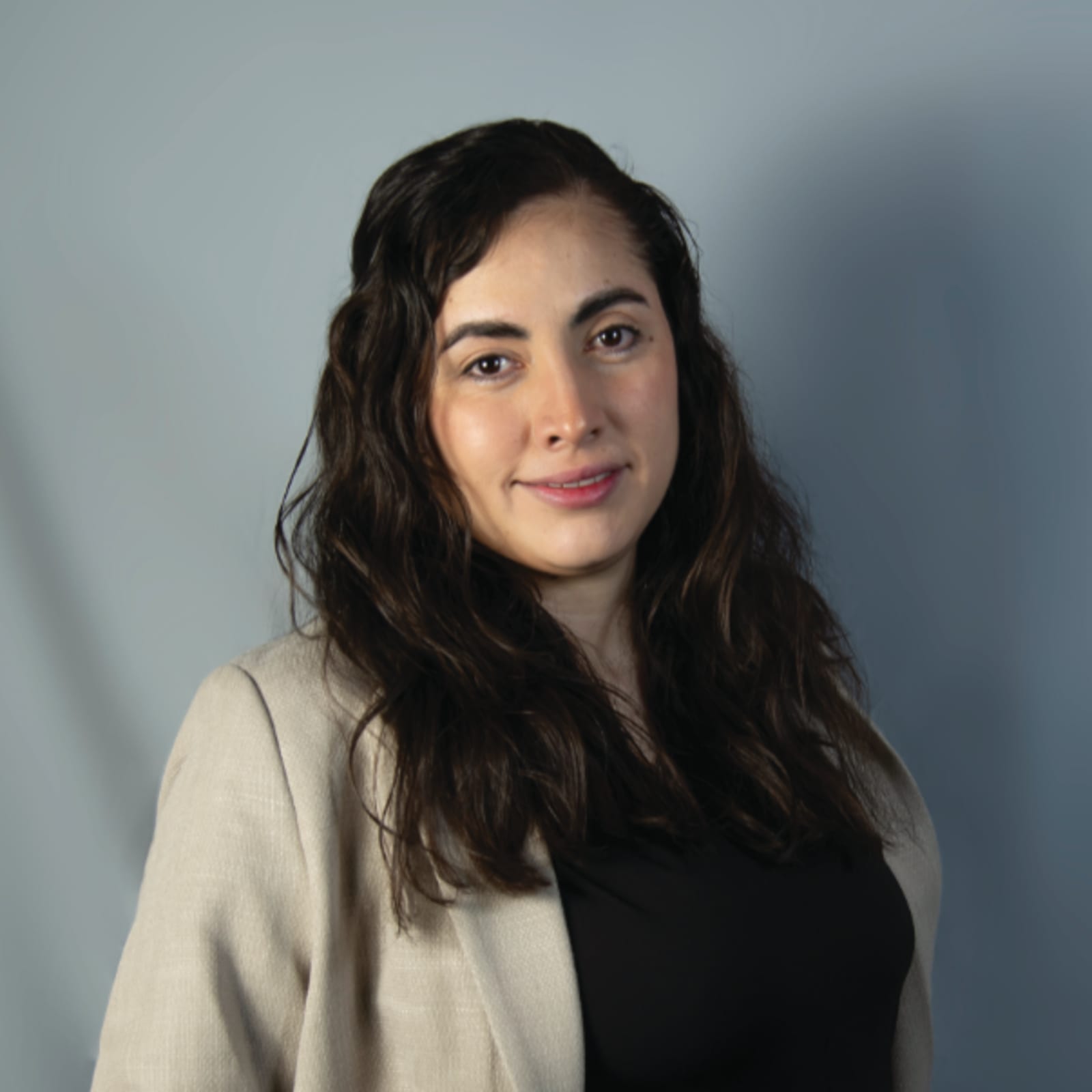
ACG to boost Mexico presence with appointment of Jessica Alfaro
ACG Engineering, a division of ACG, the world's only integrated pharmaceutical solutions and manufacturing company, is delighted to announce the appointment of Jessica Alfaro as territory sales manager for the Mexico region, as the company seeks to vastly increase its presence in the territory. In her new role, Jessica Alfaro will be responsible for promoting ACG’s portfolio of process and packaging machinery in Mexico, establishing new bonds with customers through the commitment of providing integral solutions to improve their processes. With a passion for engineering, Jessica previously worked as a sales engineer for Nicolás, Sven, Pacheco Y Andresen, Design and Engineering. Her responsibilities included the monitoring of technical specifications and industry standards, as well as the continuous development of the overall product offering. She also led board sessions, assigning requirements to valid use cases that highlighted the capabilities of the product. In addition, she worked closely with customers and the engineering team to determine the needs of the process and the requirements of the system. Commenting on the appointment, John Carey, vice-president of Sales at ACG Engineering, said: “We’re delighted to welcome Jessica into this pivotal new role. ACG is currently placing real focus and investment in the Mexico region for our process and packing machinery supporting both pharmaceutical and nutraceutical manufacturers with state-of-the-art technologies. We believe her experience and dedication will play a key part in building strong customer relations in the area.”Jessica Alfaro added: “I am delighted to be joining ACG, and embracing the challenges associated with gaining a deep understanding of our clients and providing them with the best solutions to help drive their business success. “I am excited by the idea of applying my analytical skills to design efficient and sustainable processes. My chemical engineering background gives me the opportunity to merge my passions for problem solving and teamwork, allowing me to contribute to the development of technologies and solutions that have a positive impact on the world around us.”About ACGFor over sixty years, ACG has been innovating the production solutions for pharmaceutical and nutraceutical companies, that help make people better. As the world’s most integrated provider of oral dosage products and services, we produce capsules, barrier packaging materials, manufacturing machinery, and visual inspection and traceability solutions. All fully compliant with international standards.Today, ACG fosters long-term collaborative partnerships with customers in 138 countries across six continents. Together, we share a common purpose: to solve the world’s greatest health challenges and make it better for everybody we serve. For more information, please contact the ACG media relations team:madhurima.chakraborty@acg-world.com
Read more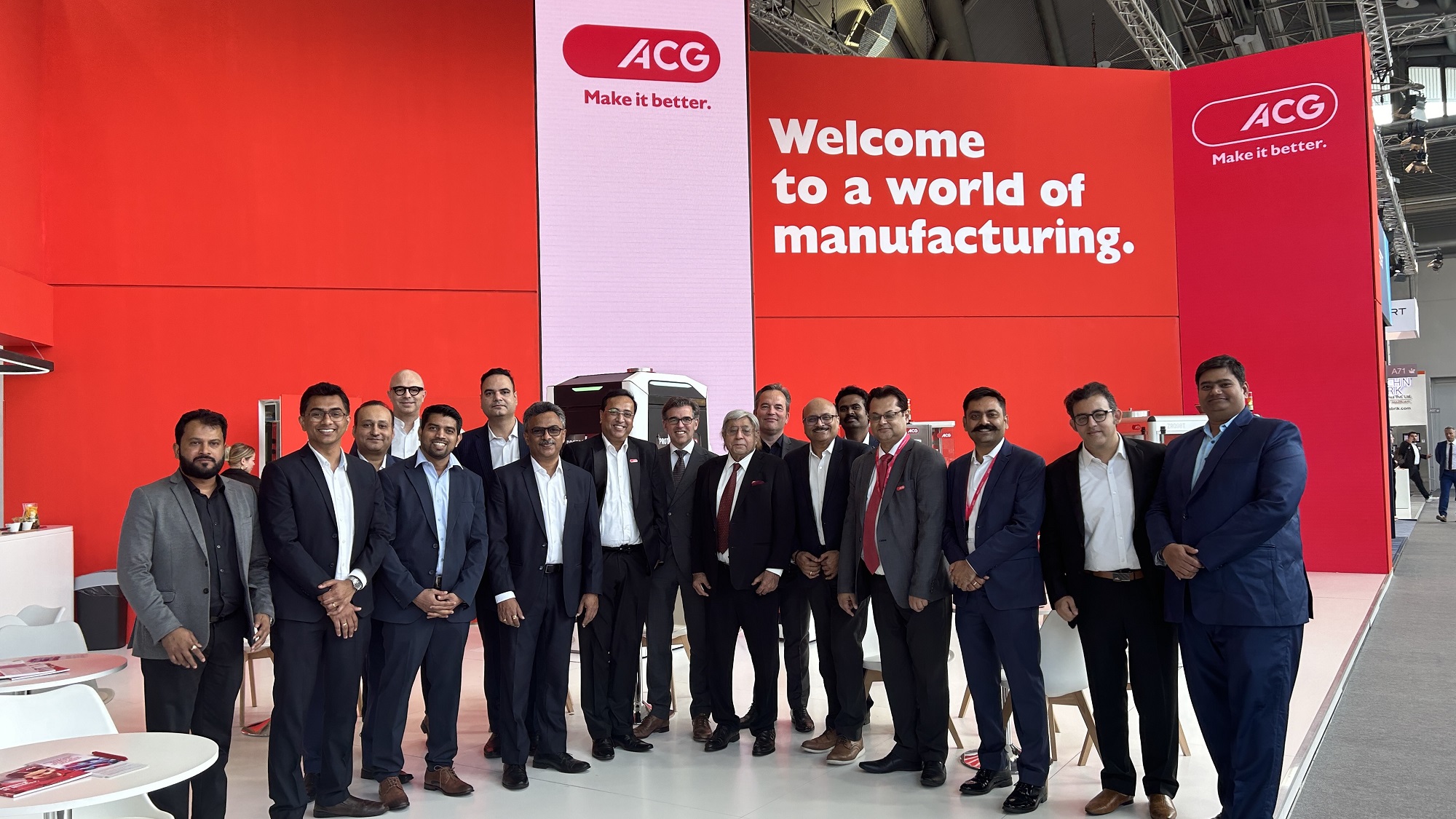
ACHEMA 2024: ACG Engineering on a mission to collectively ‘Make it Better’ World’s largest integrated supplier to the solid dosage manufacturing industry to display wide range of engineering and capsules products
At ACHEMA 2024 ACG Engineering, which provides end-to-end pharmaceutical engineering solutions,will be displaying its broadest range of products to date – underlining its commitment to ‘Making it Better’ for the industry and patients alike.The all-encompassing machines displayed will include the QUEST FB I, which is a highly versatile 'plug and play' fluid-bed unit for lab-scale feasibility studies. Also on show will be the ZRO 90T - a high-yield capsule filler. As will be the ACCURA 100FF - ACG's precision capsule checkweigher, suited for medium to large production batches with a capacity of 100,000 capsules per hour. Also on display will be the PROTAB 300 – a single rotary tablet press, which is suitable for R&D, small and medium-batch production, making scalability far easier, and the SECURECOAT TC III tablet coater, designed with operator safety and for use with highly potent active pharmaceutical ingredients (HPAPIs).Borja Guerra, vice president of international sales at ACG Engineering, said: “At ACG, we deliver efficient cutting-edge technology and a highly consistent ROI ratio for our global customer base, because we actively listen to them and their needs and take a collective approach towards ‘Making it Better’.“By aligning our shared strength and cross-divisional synergies with our Capsule and Films and Foils business units we are able to offer a whole world of different and highly targeted products and services – supporting large pharmaceutical companies and generic manufacturers with equal focus.”“We are really looking forward to ACHEMA 20024 and meeting with the industry to share knowledge and insights and to hopefully forge some new and exciting partnerships, continuing the expansion of ACG’s global footprint.”ACG will be exhibiting on stand A71 in Hall 3.1, between 10-14 June in Frankfurt.-Ends-About ACG For over 60 plus years, ACG has been innovating the production solutions for pharmaceutical and nutraceutical companies, that help make people better.As the world’s most integrated provider of oral dosage products and services, we produce capsules, barrier packaging materials, manufacturing machinery, and visual inspection and traceability solutions. All fully compliant with international standards.Today, ACG fosters long-term collaborative partnerships with customers in 138 countries across six continents.Together, we share a common purpose: to solve the world’s greatest health challenges and make it better for everybody we serve. For more information, please contact the ACG media relations team:madhurima.chakraborty@acg-world.com
Read more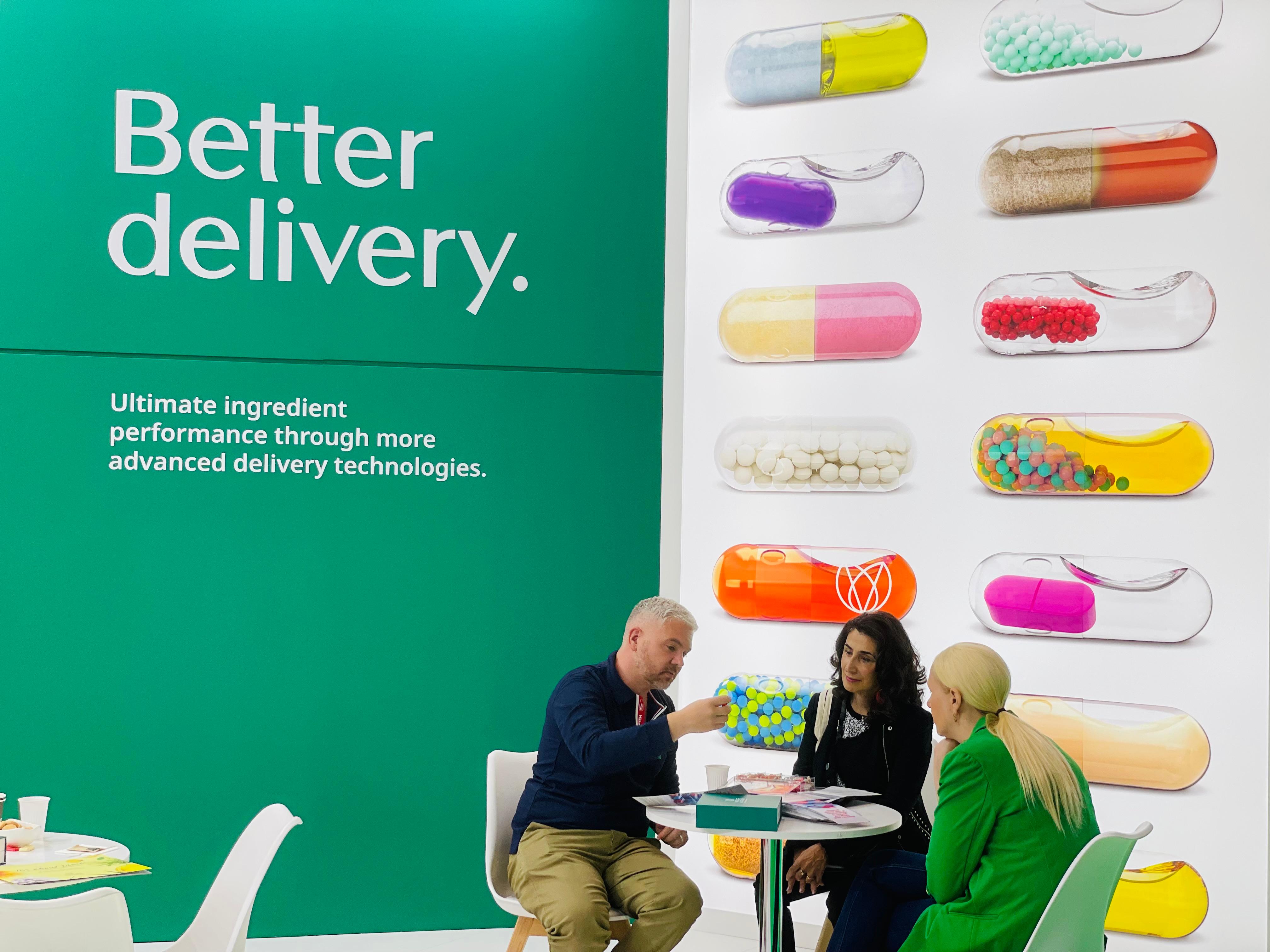
Vantage Nutrition to champion ‘better delivery’ at Vitafoods Europe 2024
At this year’s Vitafoods Europe, Vantage Nutrition (an ACG group company), will be showcasing and championing the term ‘better delivery’. With a real focus on innovation, the team will be debuting the outstanding beadlet technology, a complete product offering ultimate ingredient performance.Other ACG Capsules products on show will include ACGcaps™ H+, the world's first independently certified* ‘Clean Label' eco-friendly capsule, which is made using thermogelation technology (water and cellulose only). Alongside will be the ACGcaps™ TSafe opaque and TiO2-free clean capsules, with the enhanced version offering flexibility with pigmentation options.Aaron Quinn, head of business development at Vantage Nutrition – Europe, commented: “We know that the world’s healthiest products demand the world’s cleanest capsules performance through more advanced technologies. Through our innovations, we are committed to supporting nutraceutical brands when it comes to time consuming and costly R&D.“With the development of beadlet technology we are able to offer ultimate ingredient performance and enhanced delivery. Beadlets release ingredients over time, boost absorption and improve bioavailability. And by working with one supplier, manufacturers can ensure they have full control over all processes, with the 360 service – ensuring better results and enhanced uptake.”ACG is the world’s largest integrated supplier of pharmaceutical and nutraceutical solid dosage products and services. Along with the commitment to delivering integrated solutions and cutting-edge technology, Vantage Nutrition aims to provide the most comprehensive and advanced multiphase solutions to customers globally. The team’s focus in on turning product ideas into reality fast – helping companies enable, enhance, and differentiate nutra brands - from a full-service partnership to specific value additions.ACG will be exhibiting on stand H37, between 14-16 May in Geneva.* Certifications are applicable to certain colours and/or variants.About ACG For over 60 plus years, ACG has been innovating the production solutions for pharmaceutical and nutraceutical companies, that help make people better.As the world’s most integrated provider of oral dosage products and services, we produce capsules, barrier packaging materials, manufacturing machinery, and visual inspection and traceability solutions. All fully compliant with international standards.Today, ACG fosters long-term collaborative partnerships with customers in 138 countries across six continents.Together, we share a common purpose: to solve the world’s greatest health challenges and make it better for everybody we serve. For more information, please contact the ACG media relations team:madhurima.chakraborty@acg-world.com
Read more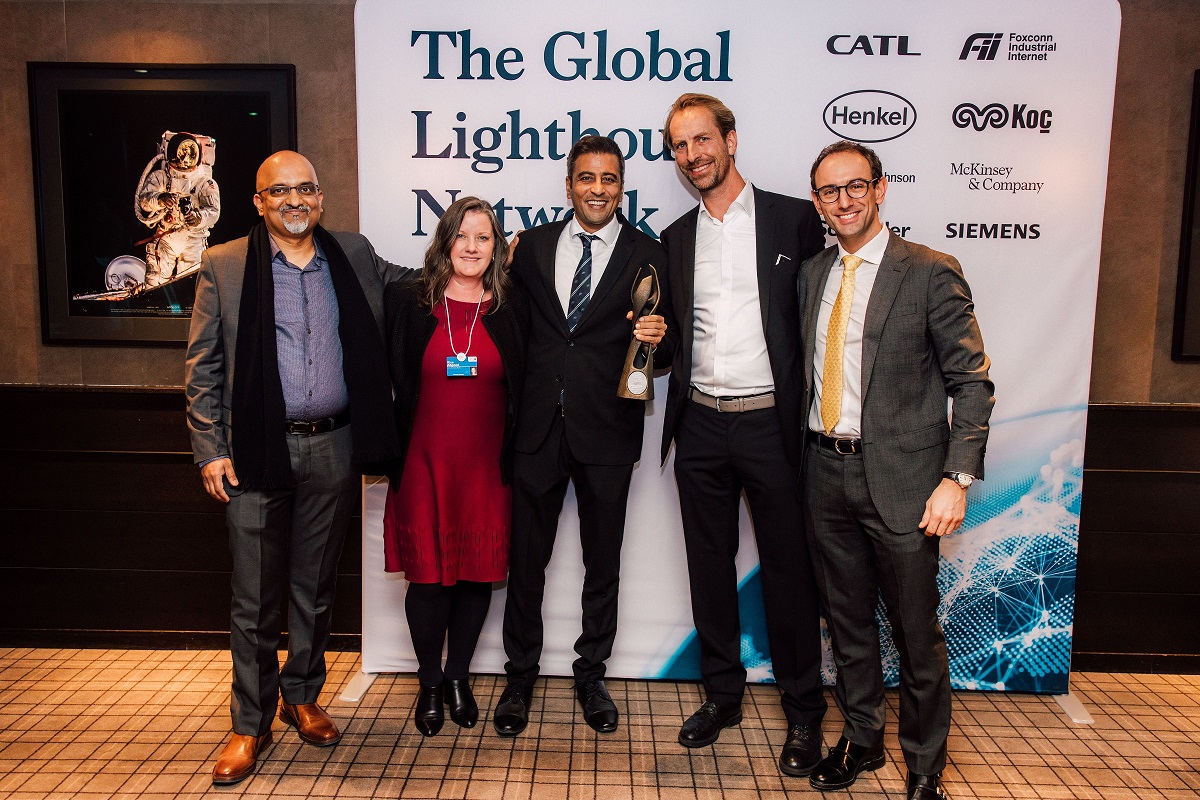
ACG Becomes the World’s First Capsule Manufacturing Factory to Join the Global Lighthouse Network Community 2023-24
ACG Capsules Pithampur, India is ACG’s 1st lighthouse to join the community Karan Singh, Managing Director and Balajikasiram Sundararajan, Chief Digital Officer attend the Global Light House Network ceremony in Davos to collect the award. ACG, the world's largest integrated supplier and service provider to pharmaceutical industry celebrated the inclusion of its capsule manufacturing facility in Pithampur, India, into the esteemed Global Lighthouse Network (GLN) by the World Economic Forum at the 54th Annual Davos Summit. The World Economic Forum’s Global Lighthouse Network has acknowledged the exemplary integration of Fourth Industrial Revolution (4IR) technologies, including artificial intelligence and big data analytics, by select factories globally. These facilities have been distinguished for their commitment to enhancing efficiency, fostering sustainable development, and simultaneously advancing their workforce’s skills and safeguarding the environment.Upon receiving the award, Mr. Karan Singh, Managing Director, said: “I am delighted to receive this recognition on behalf of my team. For me the most unforgettable part of our journey wasn't any technology or efficiency milestone, but the incredible team that made it all possible. Just ordinary people, united towards one goal, bringing about innovative collaborations to push boundaries of what is possible.” He added: “One of the stand-out features of our application was the Gen-AI integration. Something that was done in the less than two weeks. In between all the debate on what Gen-AI can do to humans it is a beautiful reminder that ‘technology is brilliant, but humans drive the change’. Let's remember that!”ACG operates across 138 countries in six continents and has positioned itself as a leader in the pharmaceutical sector by focusing on high-quality capsule production, increasing responsiveness, improving production yields, and boosting workforce efficiency. The company produces billions of capsules annually and has implemented over 25 innovative applications of 4IR technologies, including the industrial internet of things (IIoT), machine learning (ML), deep learning (DL), digital twins, extended reality, and generative AI.Selwyn Noronha, CEO, ACG Capsules, added: “We are extremely proud of our first factory lighthouse. From its inception the facility has pioneered in its field, but this latest honour recognises the excellence in adopting AI at speed and scale.“Our continued future-focused approach sets new benchmarks in quality and innovation, with the aim of ensuring maximum benefit for customers, regulators and the entire pharmaceutical ecosystem.”About Global Lighthouse Network Global Lighthouse Network is a collaborative platform bringing together forward-thinking manufacturers leading the charge in adopting Fourth Industrial Revolution technologies. Leveraging innovations like artificial intelligence, 3D-printing, and big data analytics, Lighthouses drive efficiency, competitiveness, and transformative business models at scale, fostering economic growth while championing workforce augmentation, environmental protection and providing a collaborative learning journey for all-sized manufacturers globally. The Global Lighthouse Network is a World Economic Forum initiative co-founded with McKinsey & Company and counselled by an Advisory Board of industry leaders, including Contemporary Amperex Technology (CATL), Foxconn Industrial Internet, Henkel, Johnson & Johnson, Koç Holdings, Schneider Electric, and Siemens. Factories and value chains that join the network are designated by an independent panel of experts.About ACG For over 60 plus years, ACG has been innovating the production solutions for pharmaceutical and nutraceutical companies, that help make people better. As the world’s most integrated provider of oral dosage products and services, we produce capsules, barrier packaging materials, manufacturing machinery, and visual inspection and traceability solutions. All fully compliant with international standards. Today, ACG fosters long-term collaborative partnerships with customers in 138 countries across six continents. Together, we share a common purpose: to solve the world’s greatest health challenges and make it better for everybody we serve.For more information, please contact the ACG media relations team:madhurima.chakraborty@acg-world.com
Read more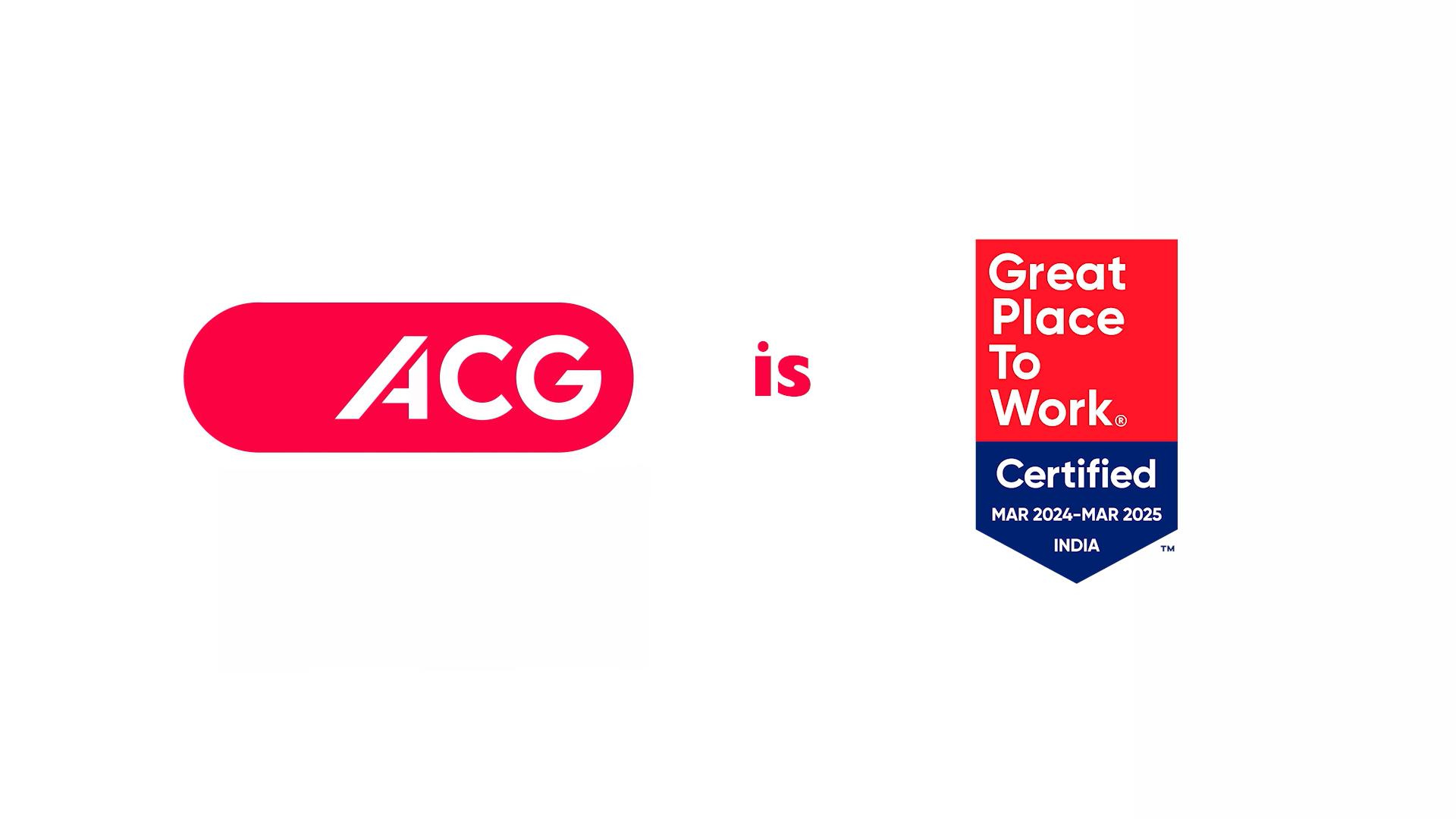
ACG awarded ‘Great Place To Work’ certification for a fourth consecutive year
ACG, the world’s largest integrated supplier and service provider to the pharmaceutical industry, is delighted to announce that for the fourth consecutive year, it has achieved the ‘Great Place To Work’ certification. This certification recognises employers who create an outstanding employee experience.Within ACG, five business units (Capsules, Corporate, Scitech – Research and Development Centre, Machinery, and Inspection), have been certified as a ‘Great Place to Work’. The comprehensive study, spanning five locations in India, encompassed approximately 3000 associates across management and plant categories. The process entailed a thorough survey based on key levers that define an organization's culture.Nikita Panchal, Group Head Talent, OD and DEI at ACG, said: “Winning this award for the fourth consecutive year fills me with pride and gratitude, recognizing the collective effort of our associates. It serves as a reminder of our commitment to excellence and the fact that institution-building is at the centre of all our actions as an organization.“ACG fosters collaboration by nurturing teamwork and effective communication. We care for our associates and the business community through support initiatives, and we remain progressive by supporting change and innovation. Our associates are encouraged to embrace our values, seize opportunities for growth and contribute their unique talents to shape a bright future together.”Sunil Jha, Group CHRO of ACG Group, added: “ACG thrives on collaboration through cross-functional teamwork, and – at all times – we prioritize the wellbeing of our associates.“Winning this award is incredibly gratifying and I am appreciative that all our associates have worked together to make this happen.”-Ends-About ACGFor over sixty years, ACG has been innovating the production solutions for pharmaceutical and nutraceutical companies, that help make people better. As the world’s most integrated provider of oral dosage products and services, we produce capsules, barrier packaging materials, manufacturing machinery, and visual inspection and traceability solutions. All fully compliant with international standards.Today, ACG fosters long-term collaborative partnerships with customers in 138 countries across six continents. Together, we share a common purpose: to solve the world’s greatest health challenges and make it better for everybody we serve. For more information, please contact the ACG media relations team:madhurima.chakraborty@acg-world.com
Read more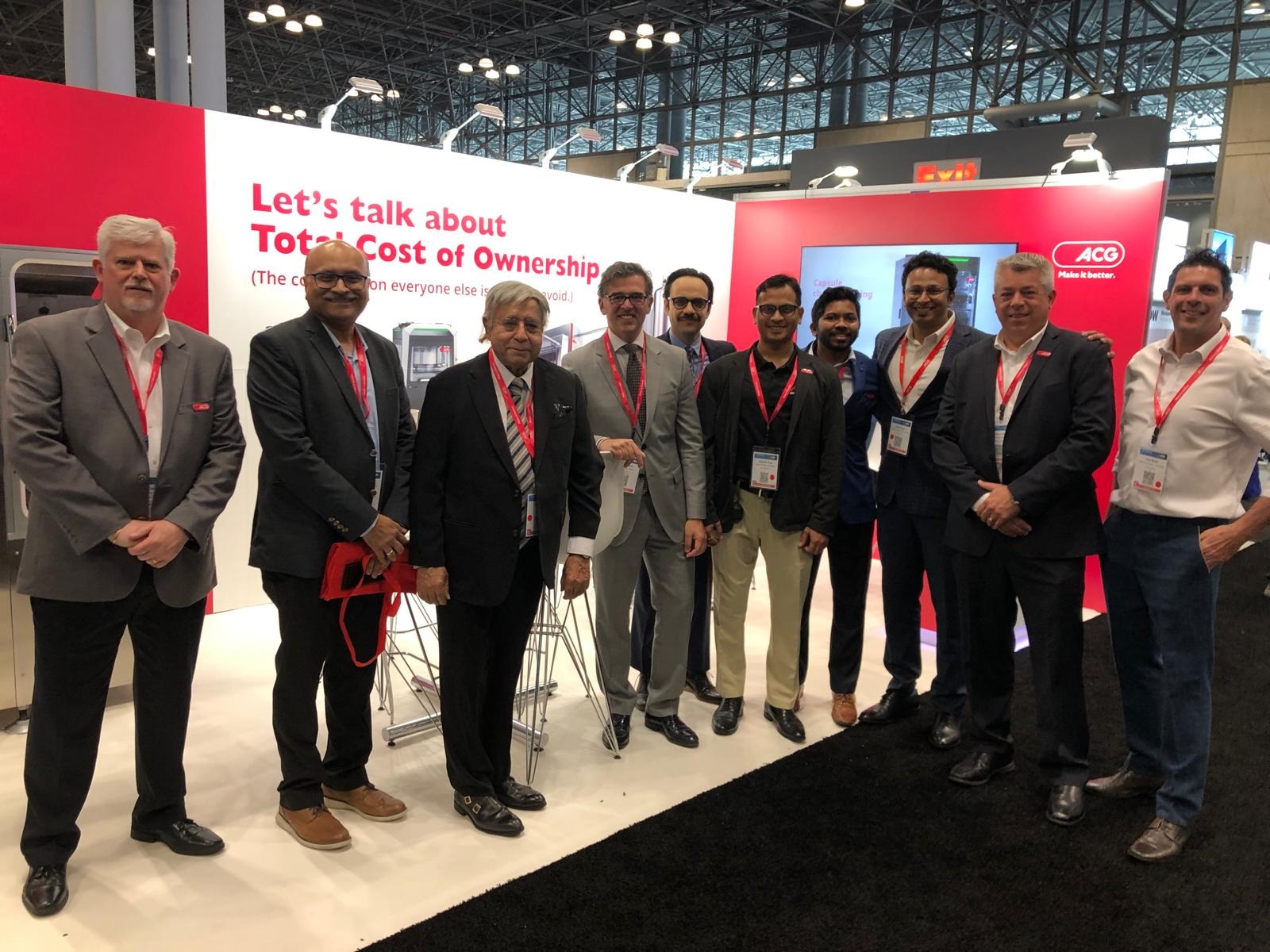
Interphex 2024: ‘ACG focuses on lowering manufacturer’s TCO’
At this year’s Interphex, ACG Engineering, part of ACG - the world's only integrated pharmaceutical solutions and manufacturing company - will be focusing on its cost-effective approach to taking generics to market.ACG’s methodology is based on speed-to-market, production efficiency and reducing manufacturing costs.Borja Guerra, vice-president of international sales at ACG, said: “As a highly experienced global supplier of process and packaging machinery of all oral solid dosage requirements, we are attuned to local market requirements. We aim to provide a low TCO (total cost of ownership) for premium pharmaceutical equipment.“With over six decades of experience partnering in the oral solid dosage space, we have taken over 8000 generics to market, working with more than 1000 pharmaceutical manufacturers to achieve this.”ACG will be showcasing its ACCURA 100 FF. The capsule checkweigher is designed specifically for precise, automatic, and continuous weighing of each capsule – whether empty, filled or partially filled, with anything from powder to pellets, and which is format free.ACG is the world’s largest integrated supplier of pharmaceutical and nutraceutical solid dosage products and services. The company will be exhibiting on stand 3515 between 16-18 April in New York.About ACG For over 60 plus years, ACG has been innovating the production solutions for pharmaceutical and nutraceutical companies, that help make people better.As the world’s most integrated provider of oral dosage products and services, we produce capsules, barrier packaging materials, manufacturing machinery, and visual inspection and traceability solutions. All fully compliant with international standards.Today, ACG fosters long-term collaborative partnerships with customers in 138 countries across six continents.Together, we share a common purpose: to solve the world’s greatest health challenges and make it better for everybody we serve. For more information, please contact the ACG media relations team:madhurima.chakraborty@acg-world.com
Read more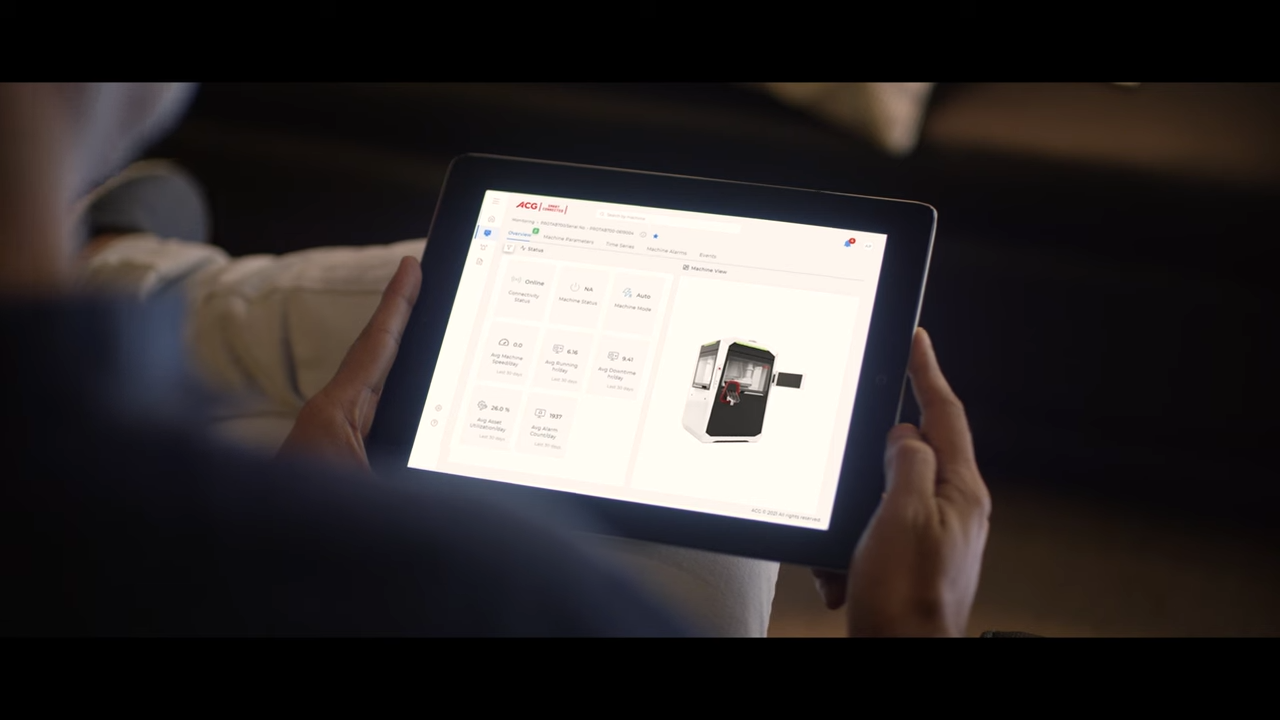
ACG Inspection launches new cloud-based offering to address upcoming VRS requirements under DSCSA regulations
In light of the impending Drug Supply Chain Security Act (DSCSA) regulations, ACG Inspection, a leading track and trace solutions provider for the pharmaceutical industry, has launched its new cloud-based Verification Router Service (VRS).The new system, which forms part of the ACG’s Inspections Life Sciences Cloud Service and Compliance Gateway, enables the automatic verification of saleable returns through product identifiers by routing requests and responses between stakeholders. Serialized products are assigned a unique identifier that can be used to track the product throughout its entire journey, enabling wholesalers to verify the authenticity of the products before they are resold.Shine Vijayan, CTO at ACG, commented: “The regulations, which have now been delayed by 12 months (coming into force in November 2024), will require all trading partners in the pharmaceutical supply chain to verify the identifier of any serialized drug product before redistributing it.“ACG’s existing VeriShield solutions tackles the implementation and interoperability challenges faced at Level 1, through to Level 3. With DSCSA’s regulation in place, ACG’s VRS covers level 4 - helping pharmaceutical manufacturers, distributors and retailers easily track and verify the saleable returns and secure their supply chain from counterfeit and substandard products.“ACG works closely with its customers, helping to address their pain points - one of which being concerns around data security. Our VRS employs robust security measures to safeguard serialized product information, guaranteeing the confidentiality and integrity of sensitive data throughout the verification process.”The system also guarantees real-time verification, to enhance operational efficiency and prevent supply chain delays. Additionally, it provides scalability assurance to accommodate an expanding volume of serialized data, to ensure continued robustness and reliability. And it incorporates exception handling, empowering stakeholders to address issues promptly to help maintain supply chain integrity.Shine Vijayan: “We are trusted experts and through our Life Sciences Cloud Service and Compliance Gateway, we can support counterfeit prevention, improving recall efficiency and data security. At all times, ensuring our clients are fully compliant with international standards and ready to meet the requirements as laid out in the impending DSCSA regulations.” -Ends- About ACGFor over sixty years, ACG has been innovating the production solutions for pharmaceutical and nutraceutical companies, that help make people better. As the world’s most integrated provider of oral dosage products and services, we produce capsules, barrier packaging materials, manufacturing machinery, and visual inspection and traceability solutions. All fully compliant with international standards.Today, ACG fosters long-term collaborative partnerships with customers in 138 countries across six continents. Together, we share a common purpose: to solve the world’s greatest health challenges and make it better for everybody we serve. For more information, please contact the ACG media relations team:madhurima.chakraborty@acg-world.com
Read more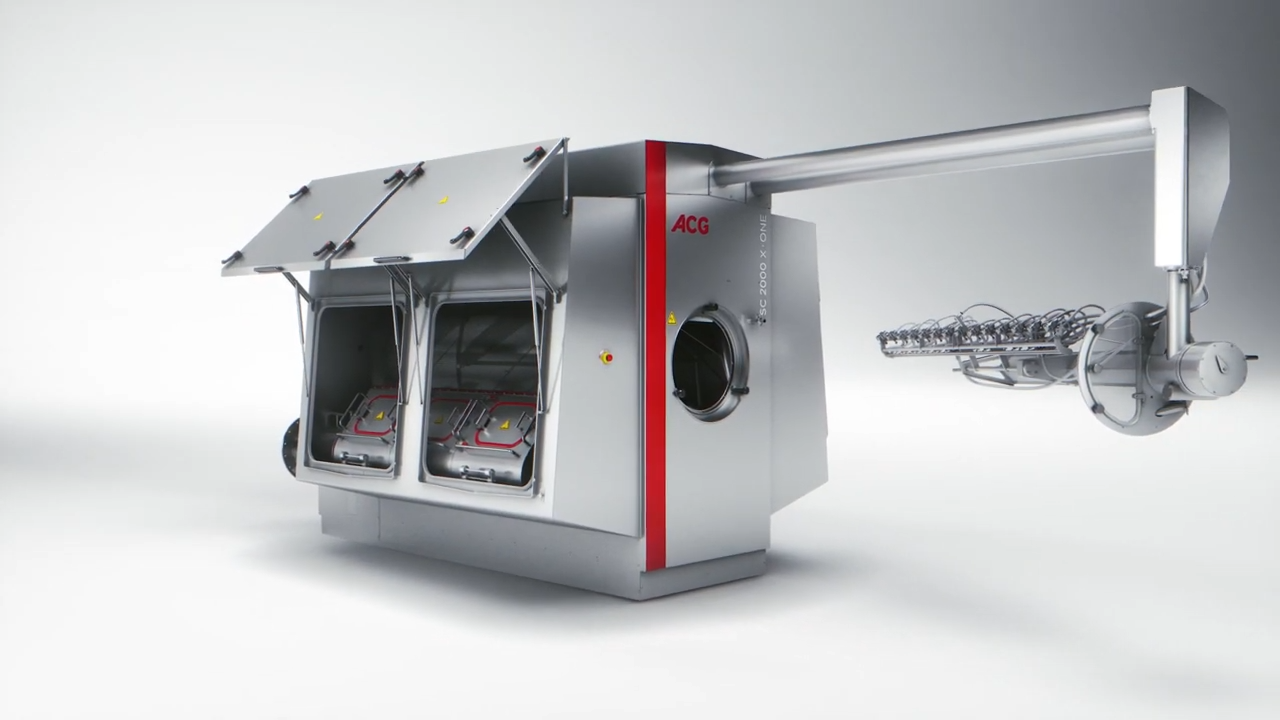
ACG Engineering launches the Smart Coater X.ONE Series Company’s fastest tablet coater ensures optimised production processes
ACG Engineering, a division of ACG, a leading supplier of integrated manufacturing solutions to the global pharmaceutical and nutraceutical industries, is delighted to launch its new Smart Coater X.ONE series, the company’s fastest tablet coater to date.The Smart Coater X.ONE has been designed to make tablet coating extremely fast, with an extra emphasis on process speed, efficiency and operator ease. Its advanced baffle design ensures the quickest process times for batches from 10-100%.Features of the new coater include a unique airflow pattern for optimized drying, a fully-perforated coating drum, closed dust-free charging, integrated discharge baffles, temperature sensor, a high-performing spray-arm and a 2.0 spray nozzle which has been developed with an anti-bearding cap. It also incorporates ACG’s exclusive X•ONE command and control system, designed to facilitate compliance with cGMP standards. Richard Stedman, CEO at ACG Engineering, said: “Our Smart Coater machines are already renowned for their innovative features and operator friendly designs. Now, after a lengthy period of development, we are excited to announce the launch of the X.ONE series.“Our quality-commitment philosophy means that the new machine has been crafted to achieve maximimum efficiency and flexibility for superior tablet coating, across every process – from charging to coating, discharging to cleaning. Each and every cycle is now swifter, more streamlined and profitable.“The fast tablet coater to date is already garnering real interest, and we look forward to continuing to showcase it capabilities at the upcoming CPhI event in Barcelona at the end of the month.” (XXX – may want to adapt this sentence, to reflect true accuracy)-Ends-About ACGFor over 60 years, ACG has been innovating the production solutions for pharmaceutical and nutraceutical companies, that help make people better.As the world’s most integrated provider of oral dosage products and services, we produce capsules, barrier packaging materials, manufacturing machinery, and visual inspection and traceability solutions. All fully compliant with international standards.Today, ACG fosters long-term collaborative partnerships with customers in 138 countries across six continents. Together, we share a common purpose: to solve the world’s greatest health challenges and make it better for everybody we serve.For more information, please contact the ACG media relations team:madhurima.chakraborty@acg-world.com
Read more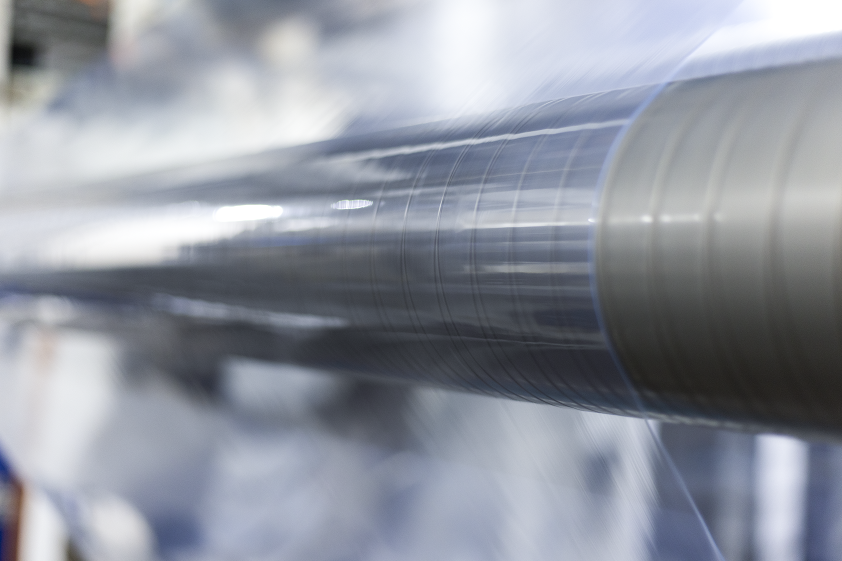
ACG acquires Technical Aluminium Foil Company
Further underpinning business growth across the Middle Eastern and African marketsACG announces full shareholding ownership of Technical Aluminium Foil Company (TAFC). This strategic move further solidifies ACG's growth trajectory across the Middle Eastern and African markets.As the world's only integrated pharma manufacturing solutions company, ACG offers a diverse range of products including capsules, films, foils, engineering equipment and inspection systems. The addition of TAFC, a prominent aluminium foil packaging company based in the UAE, strengthens ACG's position as a leading provider of comprehensive packaging solutions.TAFC boasts over a decade of experience serving the pharmaceutical and food industries with its extensive range of aluminium and specialty packaging foils renowned for their exceptional high barrier properties. The company's expertise in lacquering, lamination, printing and slitting further enhances ACG’s capabilities in meeting the diverse packaging needs of its clients.This acquisition represents ACG Group's inaugural venture in the Middle East, following recent successful acquisitions of ComboCap and AquaCap in the Americas. TAFC seamlessly aligns with ACG Films and Foils' existing business operations, enabling both entities to harness their collective strengths and expertise for accelerated growth.Shivshankar S.R., CEO at ACG Films & Foils, said: “We are excited to be making our first acquisition in the UAE. This strategic collaboration will further support our work in bringing innovative and high-quality packaging products to market, while reducing lead times and improving service levels.“By joining forces, the companies will be able to leverage their combined strengths and expertise to propel the business forward in the Middle Eastern and African markets.”-Ends-About ACGIn accordance with its commitment to making the world healthier, ACG has been delivering exceptional solutions to the global pharmaceutical and nutraceutical industry for sixty years, across six continents and in a hundred countries.Collaboration is at the core of ACG’s ethos. ACG is the world’s only integrated pharma manufacturing solutions company, with products ranging from capsules to films & foils, to engineering equipment and inspection systems – all that meet international regulatory requirements. For ACG, it’s always about finding innovative solutions to the world’s greatest health challenges, together.For more information, please contact the ACG media relations team:madhurima.chakraborty@acg-world.com
Read more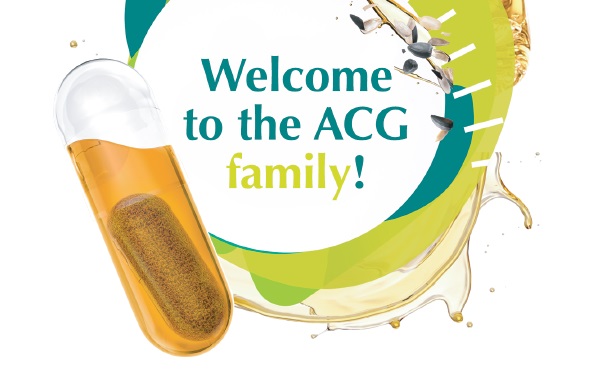
Vantage Nutrition LLC acquires ComboCap Inc
This acquisition positions Vantage Nutrition as the only company in the world supplying Sidebysideä health products to nutritional and pharmaceutical markets, for enhanced combinations.Vantage Nutrition, an ACG group company announces full shareholding ownership of ComboCap Inc (USA) and BioCap (South Africa).ComboCap is renowned for the invention and commercialization of its Sidebyside technology, the world’s first three-piece capsule health product that contains an internal divider, enabling wet and dry ingredients to be brought to market side by side, separated-but-together. Backed by 80 international patent awards ComboCap has been supplying nutritional brand customers with unique finished product solutions out of its cutting-edge cGMP plant in NJ, USA. This acquisition marks a significant milestone for Vantage Nutrition and ACG, as it further expands its technology and customer solutions footprint in North America and around the world.ACG is the world’s largest integrated supplier of pharmaceutical and nutraceutical solid dosage products and services. Vantage Nutrition, an ACG group company, already has an excellent reputation as an innovator of liquid filled capsule solutions. ComboCap marks Vantage Nutrition’s second US investment in less than a year, and first in S.A, after Philadelphia-based ‘AquaCap’ was acquired from Nestlé S.A. With this expansion of manufacturing capabilities and patented technology, along with the commitment to delivering integrated solutions and cutting-edge technology, Vantage Nutrition aims to provide the most comprehensive and advanced multiphase solutions to customers globally.Karan Singh, Managing Director at ACG, said, "As one of world’s largest producers of empty hard-shell capsules, at ACG we have often thought, what next? Strengthening our portfolio of most comprehensive vegetarian and gelatin capsules, in every imaginable size, I am thrilled to announce the acquisition of ComboCap Inc and BioCap. We now will hold the patented design and specialized equipment used inproducing the world’s first 2-in-1 capsule product with a movable membrane, becoming the sole proprietor of this technology globally.With our partners, we will usher a new era in new combinations of dietary supplements, and even non-prescription or over-the counter (OTC) remedies as well as prescription (Rx) medicines to be delivered in a single dose. This technological breakthrough is a solution to current formulation challenges with many combination therapies, including incompatible ingredients or molecules. Capsules are arguably the safest and most reliable way to deliver medicine and we at ACG strive to make it better.”Tobie Louw, a Founder and CEO of ComboCap Inc, said: “Vantage Nutrition is the perfect partner for our business, and we are very excited to be part of the ACG family. We share a passion for innovation and the commitment to bring nutraceutical and pharmaceutical customers the best possible solutions and services. By joining forces and leveraging our collective capabilities we’ll no doubt bring Sidebysideä to nutraceutical and pharmaceutical markets the world over.”-Ends-About Vantage NutritionVantage Nutrition, part of the ACG Group, is one of the world’s largest and most respected manufacturer of hard-shell liquid-fill capsule solutions. As a strategic consultancy and manufacturing partner in the nutraceutical space, Vantage Nutrition helps clients bring high-quality and innovative products to market, fast. About ACGIn accordance with its commitment to making the world healthier, ACG has been delivering exceptional solutions to the global pharmaceutical and nutraceutical industry for sixty years, across six continents and in a hundred countries.Collaboration is at the core of ACG’s ethos. ACG is the world’s only integrated pharma manufacturing solutions company, with products ranging from capsules to films & foils, to engineering equipment and inspection systems – all that meet international regulatory requirements. For ACG, it’s always about finding innovative solutions to the world’s greatest health challenges, together.For more information, please contact the ACG media relations team:madhurima.chakraborty@acg-world.com
Read more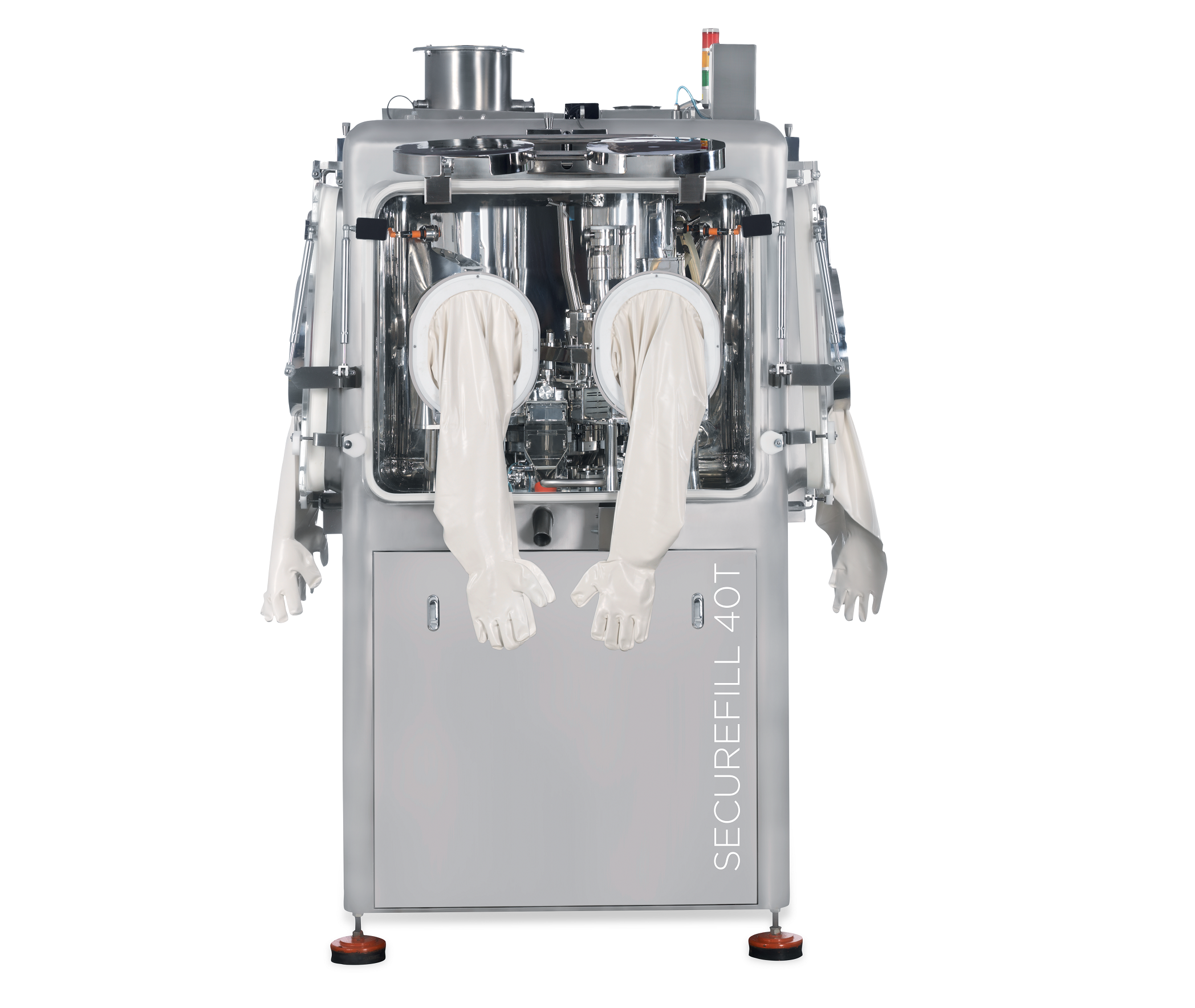
ACG Engineering – SECUREFILL 40T
Tablets & CapsulesCapsule Filling Equipment & Supplies (February 2023)ACG Engineering – SECUREFILL 40TThe Securefill series is ACG’s high-level containment capsule-filling machine range. Designed for filling capsules with highly potent and/or toxic drugs, the machines comply with occupational exposure band (OEB) up to level 4.Built with operator safety in mind, these machines are equipped for filling capsules with oncological, biopharmaceutical, antiviral formulations, and other such highly potent active pharmaceutical ingredients (HPAPIs).Features:• SS316L monoblock structure containing HEPA filters, a rapid transfer port (RTP), glove ports, and accurate dosing mechanisms maintained in a negative pressure environment.• Provision for contained charging and discharging.• Wet-in-place system to ensure wetting of all suspended particles in the pharma zone.• Can be integrated with check-weighers, metal detectors and de-dusters under containment conditions.Benefits:• Ensures complete containment, thereby avoiding operator contact within OEL range 1-10µg/m3.• Integrated containment philosophy for upstream and downstream processes.• Enables easy cleaning.• Supports the production of life-saving drugs that contain HPAPIs.Technical specifications: SECUREFILL 40T Capsule size 00 - 5 Maximum speed 40,000 capsules/hour OEL 1-10µg/m3About ACGIn accordance with its commitment to making the world healthier, ACG has been delivering exceptional solutions to the global pharmaceutical and nutraceutical industry for sixty years, across six continents and in a hundred countries.Collaboration is at the core of ACG’s ethos. ACG is the world’s only integrated pharma manufacturing solutions company, with products ranging from capsules to films & foils, to engineering equipment and inspection systems – all that meet international regulatory requirements. For ACG, it’s always about finding innovative solutions to the world’s greatest health challenges, together.For more information, please contact the ACG media relations team:madhurima.chakraborty@acg-world.com
Read more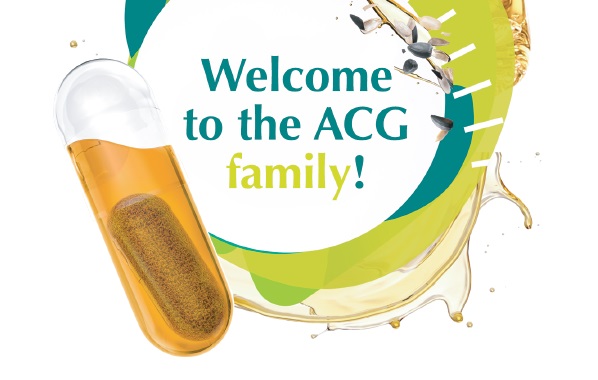
Vantage Nutrition LLC acquires Aquacaps from Nestlé Health Science
Vantage Nutrition’s innovative nutraceutical offering expands into North America.. Vantage Nutrition, an ACG Group company, announced on 1st December 2022 that it has acquired Philadelphia-based ‘Aquacaps’ – an asset of Nestlé Health Science. Aquacaps is a leading contract manufacturer of liquid-filled capsules within the nutritional supplement industry in the United States. Its novel liquid delivery technology allows for the liquid filling of hard gelatin and vegetarian capsules. ACG is the world’s largest integrated supplier of pharmaceutical and nutraceutical products and services. Vantage Nutrition, an ACG group company, already has an excellent reputation as an innovator of two-piece liquid fill capsule solutions. The company’s mission is to be the most efficient partner in delivering innovative and high-quality nutraceutical products to customers globally. Karan Singh, Managing Director of ACG, said: “Although ACG has been established in North America for the last 20 years, this marks our first acquisition in the territory and is a key next step in our global expansion strategy. With this increase in our footprint and manufacturing capabilities, coupled with Vantage’s innovative technologies and 360-degree service offering, we aim to provide the most advanced combination liquid-fill solutions for customers across the region.” About VantageVantage Nutrition, part of the ACG Group, is one of the world’s largest and most respected manufacturer of hard-shell liquid-fill capsule solutions. As a strategic consultancy and manufacturing partner in the nutraceutical space, Vantage helps clients bring high-quality and innovative products to market, fast. About ACGIn accordance with its commitment to making the world healthier, ACG has been delivering exceptional solutions to the global pharmaceutical and nutraceutical industry for sixty years, across six continents and in a hundred countries.Collaboration is at the core of ACG’s ethos. ACG is the world’s only integrated pharma manufacturing solutions company, with products ranging from capsules to films & foils, to engineering equipment and inspection systems – all that meet international regulatory requirements. For ACG, it’s always about finding innovative solutions to the world’s greatest health challenges, together.For more information, please contact the ACG media relations team:madhurima.chakraborty@acg-world.com
Read more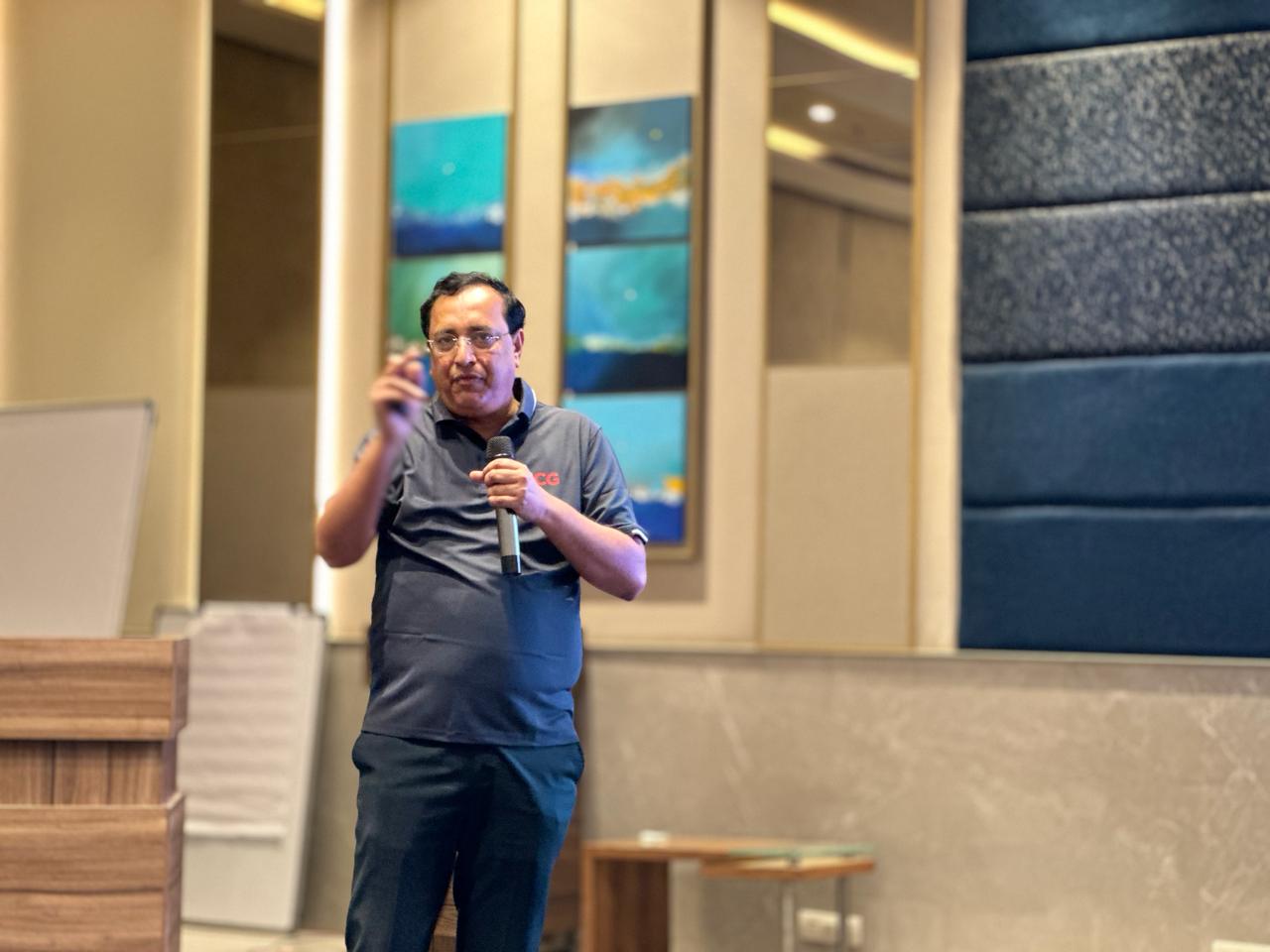
ACG appoints Shankar Gupta as Chief Sales Officer Industry authority to re-join business in a newly created role
ACG, the world’s largest integrated pharmaceutical and nutraceutical manufacturing solutions provider, is delighted to announce that Shankar Gupta will be re-joining the business in the newly created role of Chief Sales Officer.In his new role, Shankar will be responsible for driving sales across all four ACG divisions (Films and Foils, Capsules, Inspection and Engineering) in order to continue building the company’s ‘One ACG’ agenda. Essentially, this will involve bringing further uniformity to ACG's customer outreach processes, creating more integrated solutions, and ultimately providing a consistent brand experience to ACG’s global customers, regardless of business division or location. He will also focus on scaling new initiatives.Shankar will report directly into the managing director, Karan Singh, who comments:"I am so pleased that Shankar Gupta has decided to rejoin the business during this exciting time. His understanding of ACG and its deliverables, and deep insight into our customers’ businesses will help us to align ourselves better to their changing needs. More importantly, he will champion and support better collaboration and partnership with customers.“Shankar will be pivotal in calibrating and aligning our business units to our goal of ‘Making it Better’, and our belief that everyone deserves access to good medicine."Shankar Gupta adds: “I am excited to use my experience in the pharmaceutical industry to augment ACG's growth by aligning the organisation to the changing dynamics of the global healthcare Industry.“It will certainly call for a huge collaboration of efforts both internally and with our customers, but will ultimately lead to a richer, deeper and more numerous partnerships.”-Ends-About ACGIn accordance with its commitment to making the world healthier, ACG has been delivering exceptional solutions to the global pharmaceutical and nutraceutical industry for sixty years, across six continents and in a hundred countries.Collaboration is at the core of ACG’s ethos. ACG is the world’s only integrated pharma manufacturing solutions company, with products ranging from capsules to films & foils, to engineering equipment and inspection systems – all that meet international regulatory requirements. For ACG, it’s always about finding innovative solutions to the world’s greatest health challenges, together.For more information, please contact the ACG media relations team:madhurima.chakraborty@acg-world.com
Read more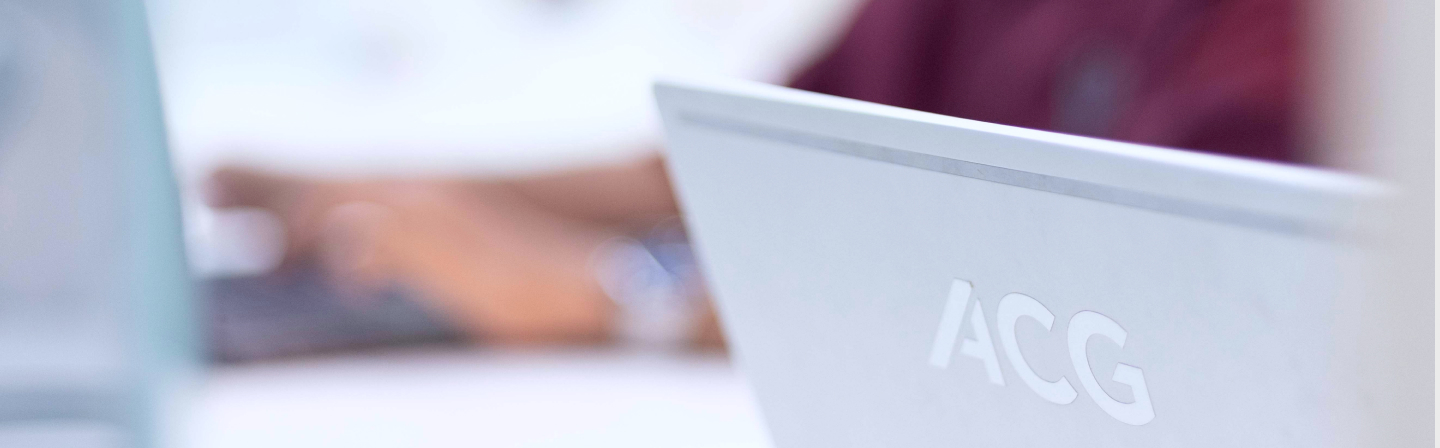
ACG to Launch German Process Laboratory in 2023
Following the success of its first-to-market laboratory for process development in India, ACG (the world’s biggest integrated pharmaceutical and nutraceutical manufacturing solutions provider) is now also committed to launching a sister process lab in Germany in 2023.This new process development laboratory will be located at ACG’s XERTECS GmbH site in Mulheim in the South West of Germany, with the first phase occupying approximately 250 square metres. ACG’s staffing recruitment plan for the lab will be to attract top academic talent from local universities, as well as trained and experienced process engineers, pharmacists and lab technicians.The aim of ACG’s new laboratory will remain consistent with the first – to provide customers and partners access to the latest knowledge, skills and equipment to collaboratively keep pushing the boundaries of all aspects of process development. So customers can test solid dosage optimisation limits, for example, and co-create alongside ACG’s team of experts to develop new process solutions.The extensive range of available equipment covers areas including feasibility studies, research and development work, pilot-scaling, and tailored in-house technical training courses. Customers also get to experience and test products from ACG’s portfolio and gain operational and maintenance training on premise.Dr Marcus Michel, CEO of ACG Engineering, explains: “ACG’s process labs reinforce our commitment to ‘making it better’. Requested by the Indian market, our first lab has enabled customers to build their competencies and capabilities, as well as to scale up – with many of these customers now operating at high capacity and efficiency. Our plan is simply to replicate this model in the European market, and we are working at full speed to ensure the launch of our new facility in 2023.“The lab in India is home to some of the smartest and finest technologies in powder processing, and is fully equipped for all aspects of granulation, drying, tablet compression and coating. Many of our machines are unique because they have been built or modified in direct response to our customers’ needs – helping them on their manufacturing journey.”About ACGIn accordance with its commitment to making the world healthier, ACG has been delivering exceptional solutions to the global pharmaceutical and nutraceutical industry for over sixty years, across six continents and in a hundred countries.Collaboration is at the core of ACG’s ethos, and ACG is the world’s only fully integrated pharma manufacturing solutions company, with products ranging from capsules to films & foils, to engineering equipment and inspection systems – all that meet international regulatory requirements. For ACG, it’s always about finding innovative solutions to the world’s greatest health challenges, together.For more information, please contact the ACG media relations team:madhurima.chakraborty@acg-world.com
Read more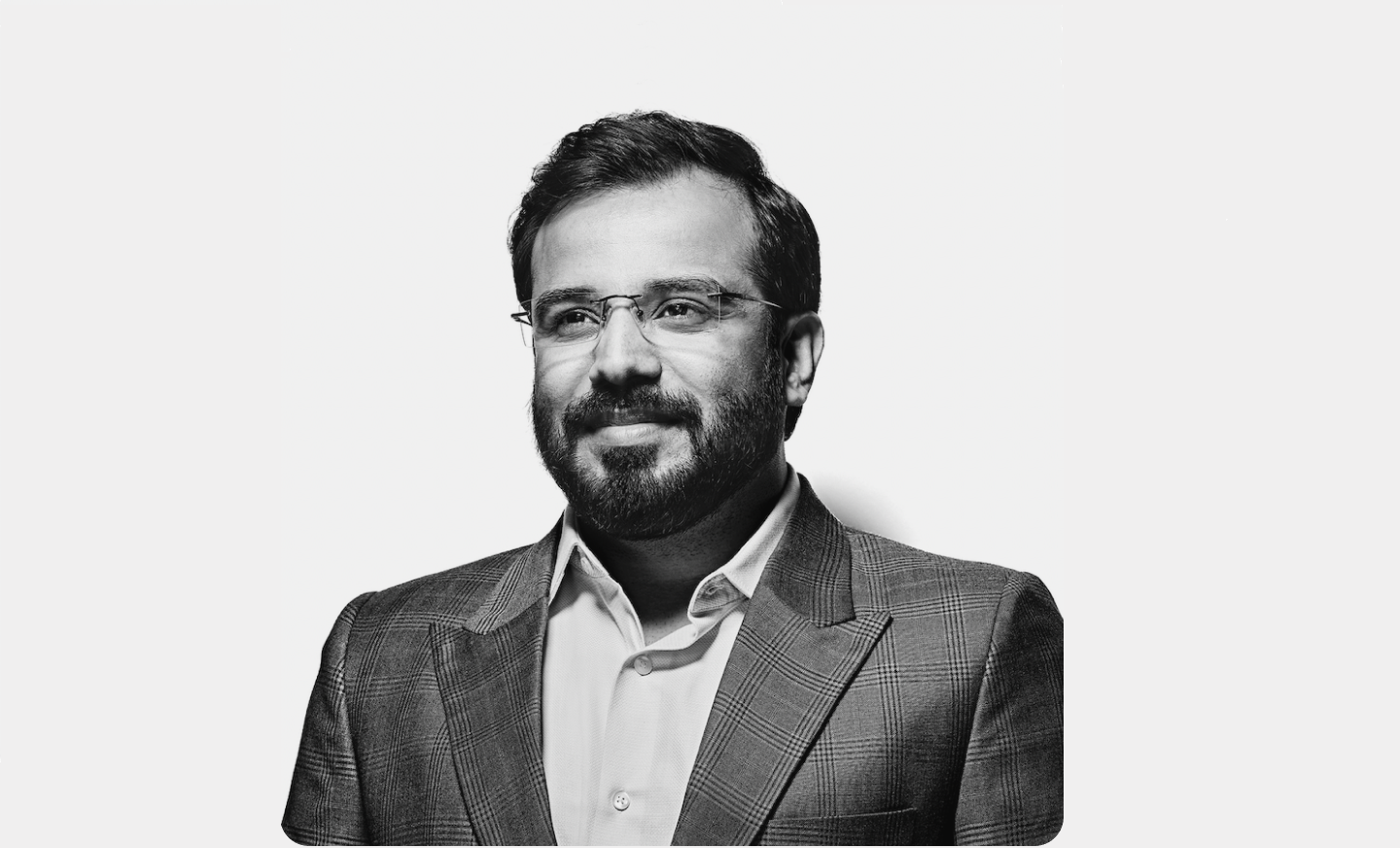
ACG appoints Udit K Singh as CEO of ACG Inspection
ACG, a leading supplier of fully integrated manufacturing solutions to the global pharmaceutical and nutraceutical industry, is pleased to announce the appointment of Mr. Udit K Singh as the new chief executive officer (CEO) of its Inspection Division.Mr. Singh will be supporting the company as it continues its growth and global expansion. He will be responsible for ensuring that every dose of medication that ACG Inspection’s pharmaceutical and nutraceutical partners provide is manufactured and delivered exactly as intended. That is down to the fact that ACG’s visual inspection systems track and monitor the manufacturing lines to guarantee flawless, safe products.Karan Singh, managing director, ACG said: “ACG is focused on building a diverse, world-class team by hiring top international talent. We are delighted to welcome Udit Singh to ACG Inspections. He has had an illustrious career and brings diverse and unique capabilities, including a robust understanding of the pharmaceutical sector.“The team looks forward to tapping into his deep experience to enrich our global work towards making the world safer and healthier. With his knowledge and expertise in this field, Udit Singh is sure to take ACG Inspection to newer heights.”Mr. Singh added, “I am pleased to join ACG and will work to ensure that our advanced serialisation, aggregation and anti-counterfeiting solutions track and protect medicines all the way through the supply chain, and into the hands of those who need them.“We are investing substantially to ensure our track and trace platform performs seamlessly and complies with regulatory requirements all over the world. I look forward to playing an integral role, and contributing towards the continued development, working with a world-class team.”About ACGIn accordance with its commitment to making the world healthier, ACG has been delivering exceptional solutions to the global pharmaceutical and nutraceutical industry for almost sixty years, across six continents and in a hundred countries.Collaboration is at the core of ACG’s ethos, and ACG is the world’s only integrated pharma manufacturing solutions company, with products ranging from capsules to films & foils, to engineering equipment and inspection systems – all that meet international regulatory requirements. For ACG, it’s always about finding innovative solutions to the world’s greatest health challenges, together.For more information, please contact the ACG media relations team:madhurima.chakraborty@acg-world.com
Read more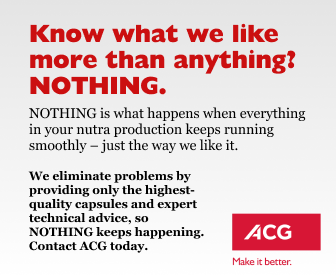
ACG Capsules launches campaign to promote problem-free pharmaceutical production
-One of the world’s largest producers of empty hard-shell capsules is on a mission to‘Love NOTHING’ when it comes to zero-problem productionACG, one of the world’s largest producers of empty hard-shell capsules, has launched its global pharmaceutical campaign: ‘ACG loves NOTHING’. The campaign is aimed at significantly improving pharmaceutical production through collaboration and industry-leading innovation. With a host of value-added services on offer, ACG has taken a pledge to strive for zero-problem pharmaceutical and nutraceutical manufacturing.Alex Robertson, CMO at ACG, said: “The messaging at the centre of this campaign is: ‘ACG loves NOTHING’ – we are putting every effort towards zero-problem production. That’s because when ‘nothing’ happens during pharmaceutical and nutraceutical production, everything runs reliably, and our customers can get the products they make to the people who need them. We will achieve this by providing the highest quality empty capsules and all the holistic advice and expertise required for seamless operations.”Founded 60 years ago, ACG was created on the simple principle of ‘Make it Better’. As the world’s largest integrated supplier of solid dosage pharmaceutical and nutraceutical products, and with the most comprehensive ranges of vegetarian and gelatin capsules globally, ACG has the scale and range to have a far-reaching impact on pharmaceutical production and human health.Selwyn Noronha, CEO ACG Capsules, added: “The pharmaceutical sector is regulated and highly competitive. Companies operating within it need a diverse range of quality capsules that help them stand out from the crowd, while also meeting demands for clean and natural products.“Beyond exceptional products, these companies need expertise and a lifetime of targeted support to ensure efficient manufacturing and guarantee regulatory compliance. With proficiency in all aspects of manufacturing from capsules to machines and protective barriers, for the last 60 years ACG has been the only company to offer this level of support, and it continues with this focus at the heart of operations.”So, at ACG, there really is something about NOTHING. The company is on a mission to drive towards problem free production and collaborating with its customers to collectively deliver on its mission of creating a healthier world.About ACGIn accordance with its commitment to making the world healthier, ACG has now been delivering exceptional solutions to the global pharmaceutical and nutraceutical industry for 60 years, across six continents and in 138 countries.‘Collaboration’ is at the core of ACG’s ethos, and ACG is the world’s only integrated pharma manufacturing solutions company, with products ranging from capsules to films & foils, to engineering equipment, and inspection systems – all that meet international regulatory requirements.For ACG, it’s always about finding innovative solutions to the world’s greatest health challenges, together.For more information, please contact the ACG media relations team:madhurima.chakraborty@acg-world.com
Read more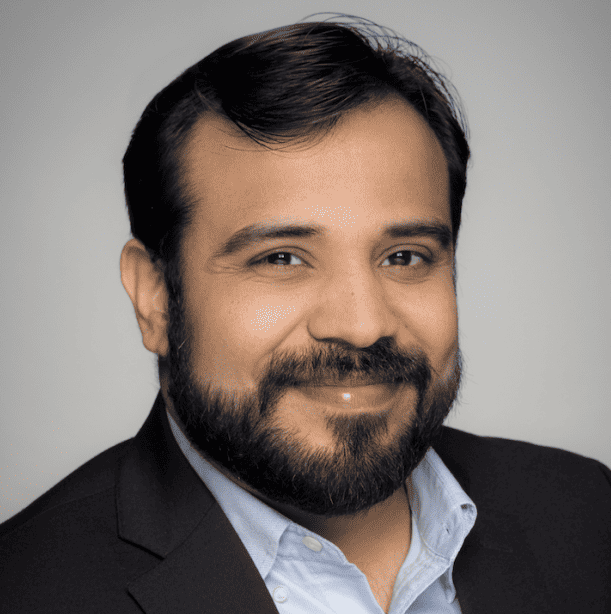
Virtual Inspections: Embracing the Digital Change
Virtual inspections must become a part of companies’ repertoires if they aim to maintain quality standards in their organisations.Digital tools and technologies are advancing rapidly – but how can pharma make the best use of them? One area of manufacturing that is ripe for enhancement via digital tools is product inspections.Udit K Singh, Chief Executive Officer at ACG Inspections explains.What historical challenges affect inspections today?Manual inspection methods increase the chance of rejecting an entire batch because of an anomaly in a single tablet or capsule from that batch. Whereas digital tools can identify defects at the individual product level – rejecting the defective products only. These tools also verify that the inspection has been carried out to the required parameters and that data, associated with the inspection, is stored.When inspecting products manually there is also the potential for defects to be missed. If these products reach the market, they can cause reputational damage to a brand, potentially resulting in lawsuits and revenue losses.Another historical challenge is that there hasn’t been any real-time qualification and analytics of manufacturing output. In my view, being able to provide assurance that each capsule or tablet has been qualified against the quality standards and a benchmark has been set by aggregators in this space is of crucial importance.What are the key benefits of digital inspections?The benefits of digital inspections are immense. Better throughput, improved quality outcomes and higher visibility are all possible to achieve when businesses choose to integrate digital inspections into their operations.Camera sensors use images captured to determine the chemistry, orientation, hardness and other product characteristics such as moisture. They work at high speed and on fast-moving production lines. Because they remove faulty products before they reach packaging the production performance is optimised. The operators just need to be trained to ensure the standard operating procedures (SOPs) are followed.Manual inspection is subjective. Humans require training and education and have limitations. For example, manual inspection makes it difficult to distinguish a “look-alike” product, minute variances in colour and other characteristics. Manual inspection is repetitive work, in often brightly lit conditions which means human performance will be varied and subject to fatigue – therefore the quality assurance cannot be validated.In the past, inspections at single points in a manufacturing plant, such as in-line and end-of-line product sampling were acceptable. Clearly, this type of check wouldn’t provide companies with a full picture. Digital inspections offer manufacturers the opportunity to create better data to support business decisions and the means to view the strengths and weaknesses of processes with improved transparency.In your view, are there any important limitations that must be considered?Technology evolution is happening at an enormously fast pace. As pharmaceutical manufacturing is governed by a set of compliance rules the adoption of technology takes time.You can’t adopt rapid changes in technology because the industry must go through phases of testing, adaptability, efficiency and productivity. By the time they are complete, five years may have already elapsed. Trying to keep up with the pace of technology development is becoming tough.Regulatory bodies and the pharmaceutical service industry need to collaborate regarding the regulations that become the baseline for technology development. This should allow for faster technology adoption for pharmaceutical companies.What are your thoughts on current penalties for facilities that don’t comply with regulations?Patient safety in drug manufacturing is the absolute top priority. There cannot be any compromise. Regulatory bodies are doing everything in their power to ensure that this is the case. If this is managed by imposing penalties, stopping production, recalling products or even questioning manufacturers they have the authority to decide what’s right to protect patients.However, the methods used to ensure that companies meet the regulation are at the discretion of the manufacturer. For inspections, they could adopt optical inspection using cameras or non-optical methods that use infrared ultrasound – to check the structure of drugs. Regardless of the approach they take, frequent checks and balances will always be their biggest responsibility. Quality checks at all stages of the process from raw material, batch mixing, API production, to the manufacture of the final finished tablet or capsule must be consistent. But the quality assurance process doesn’t stop there, companies must also invest time into evaluating blister packaging and bottles, label print quality, boxing, packing and shipping.Managing all these aspects of the manufacturing process can be quite intense, but technology can help in streamlining it. If companies choose to embrace the obvious benefits of digital inspections, they will certainly be able to better support patients worldwide.Source: https://pharmafile.com/news/virtual-inspections-embracing-the-digital-change/
Read more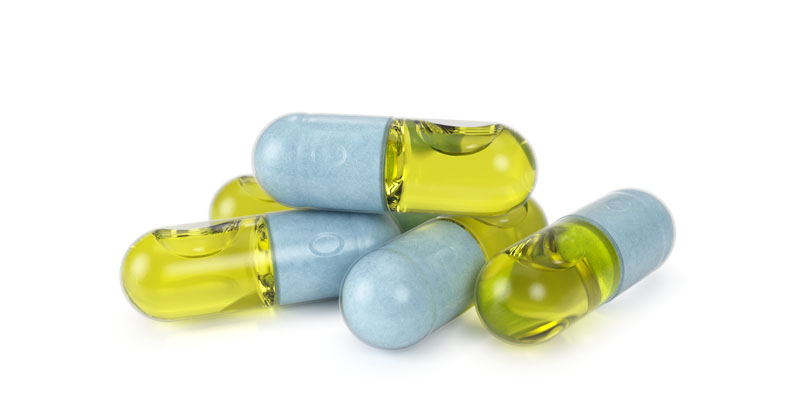
Adding a new chapter to the history of capsule-based drug delivery
For more than 100 years, capsules have consisted of two pieces (a body and a cap). Nutritional or pharmaceutical ingredients are dosed into the body and the cap is then placed over the mouth and snapped shut. Now, however, next-generation technology is bringing a new dimension to this popular oral solid dosage form.Dr Kevin Robinson (KSR) recently caught up with Tobie Louw (TL), Vice President of Operations at Vantage Nutrition (An ACG Group Company), to discuss the market introduction of a new dietary supplement format called “Sidebysides”, brought about by the invention of the world’s first three-piece capsule, and to discover how they came to be.“The oral capsule has for more than 100 hundred years been the most effective and efficient way to bring the widest range of fixed-dose oral health solutions to market. There continues to be significant new investment in its ongoing evolution to assist with human health endeavours. This is the latest chapter in its rich history,” says Tobie.“Sidebysides” are the world’s first side by side separated oral dose health products for nutraceuticals and pharmaceuticals,” he says, “that have been created by the invention of a new three-piece capsule.”The third piece is the inventive introduction of a cup-shaped divider membrane inside a standard off-the-shelf capsule — made from the same material as the capsule — that acts as a divider inside the body of the capsule.""This enables wet and dry ingredients or incompatible actives to be housed side by side — together but separate in one product. “Sidebyside dietary supplements are rapidly gathering momentum since being launched in a vegetarian capsule format in 2020,” he adds.ComboCap, the technology-based start-up that invented and commercialised Sidebyside technology and products during the past 10 years, has developed and received 80 international patent awards for Sidebysides.The company designed, optimised and produced the unique Sidebyside technology and manufacturing process as well as the machines used to currently produce Sidebyside dietary supplements exclusively in their own world-first Sidebyside plant in New Jersey, US. ACG acquired ComboCap in early 2023.ACG is known for its enabling innovation and technology in the dietary supplement and pharmaceutical spaces.Discussing the manufacturing process, Tobie explains that a completely new type of encapsulation machine technology and process is used to produce Sidebyside products. “A Sidebyside machine takes an empty off-the-shelf hard capsule, removes the cap, doses the liquid and then inserts and seals the membrane into place. The cap is then replaced,” he says.“In the second stage of the process, the powder encapsulation takes place; the cap is removed, the powder dosed and the cap put back on — completing a Sidebyside product. This innovative technology is being extended to enable multiphase dosing on one single Sidebyside machine.”Groundbreaking technologyKey benefits for the greater life sciences industries include the fact that the three-piece Sidebyside form factor maximises the dose volumes on both sides of the membrane. It also enables customised dose sizes because the membrane position within the capsule is movable. Transparent capsules are used so that the contents of both chambers are fully visible.“The Sidebyside product format provides an ideal way to combine generally sensitive ingredients, such as probiotics, with other incompatible nutrients and actives,” adds Tobie.The dual-phase capsule-in-a-capsule has, of course, existed in the market for some time. In a cap-in-cap, a small capsule containing a powder dose is placed inside a larger one containing a liquid dose. This form factor results in the outer liquid capsule and dose being dissolved before the inner powder capsule and dose are. “With Sidebysides, the capsule shell of both chambers dissolve at the same time, enabling the ingredients to disperse and work together simultaneously; this delivers benefits such as the better absorption of key nutrients in the presence of oils.”The future rollout programme for Sidebyside products includes a number of features that cover the delayed release of the whole capsule and the release of the two independent chambers at different stages.“Delayed release is relevant because there is a significant market demand for health products that dissolve later in the digestive tract, or require a dual-stage instant beneficial effect followed by a gradual sustained one. An example of the latter is an oral health product that assists with falling asleep followed by staying asleep,” notes Tobie. KSR: What is the movable membrane and what is its function? TL: The membrane acts as a barrier between the two ingredients. It can be located in the optimum position, allowing the manufacturer to size the doses and the chambers accordingly — such as when one of the two ingredients requires a larger dose than the other.KSR: How do Sidebyside products differ from capsule-in-capsule products?TL: With Sidebysides, the separate ingredients operate together after ingestion; the chambers dissolve together. With cap-in-cap products, the separated ingredients dissolve sequentially. There are application needs for the sequential dissolution dynamic, especially when the inner chamber is required for late release.The Sidebyside product format and technology can however enable both parallel or sequential release, and can discharge either chamber ahead of the other depending on the need.Often, Sidebyside products can help to solve incompatibilities; examples include when ingredients haven’t previously been able to be combined or in the general case of needing to pair liquid and powder nutrients.By housing them with a dividing membrane, it’s possible to retain the identity and efficiency of the separated doses that may otherwise have been compromised if they had been combined and started reacting together sooner. This plays a role in enhanced product stability and shelf-life.When it comes to capsule-in-capsule products, the outer oil protects the inner capsule after ingestion and the powder is thereafter released for digestion. The oil helps to function as a delayed release solution. With Sidebysides, the use of clear capsules brings an added benefit in that a consumer has full side by side visibility of both separated ingredients in the capsule.This transparency can help to enhance patient trust ion the product and co-use buy-in and compliance. Product communication and marketing is also facilitated when references can be made to the separated contents.KSR: Can you expand on some of the enhanced combinations and what they can achieve? TL: Sidebyside products launched by brand companies to date have covered the following applications: general vitality, immunity, prenatal, woman’s health, men’s health, thyroid, sleep, calm, weight management and others.Select pharmaceutical Sidebyside applications are also being considered. One example is VASCEPA (icosapent ethyl) a pharmaceutical-grade fish oil. Published research by Amarin shows that VASCEPA DHA, when co-used with statins, brings patients a substantial enhancement in the benefits of the statin.Bringing a single two-in-one Sidebyside “VASVEPA-STAT” product to market would ensure co-use and give the combination solution in a more convenient single product format.KSR: Where next for this technology? TL: We are currently exploring a number of exciting controlled released options. This includes bringing single-stage, two-stage and triple-delayed release Sidebysides to market.Triple-delayed release Sidebysides can utilise a number of ingredient formats including liquids, powders and beadlets, whereby a mix of delayed-release beadlets is used to achieve the second and third stage release after the early stage release of the liquid dose.We are also progressing the development of beadlet-liquid and powder-powder and liquid-liquid Sidebyside health products. To date, no commercially available separated powder-powder oral health dose product exists in the market … and they have not been possible in existing capsule formats.In addition, we’re looking at developing the science behind exciting combinations such as prebiotic/probiotic Sidebysides in powder-powder form.By continuing to invest, extend, and bring to market the latest, most effective and efficient capsule technologies and innovative oral-dose health products, ACG continues to build its lead innovator status as a global top tier capsule company.Source: https://manufacturingchemist.com/
Read more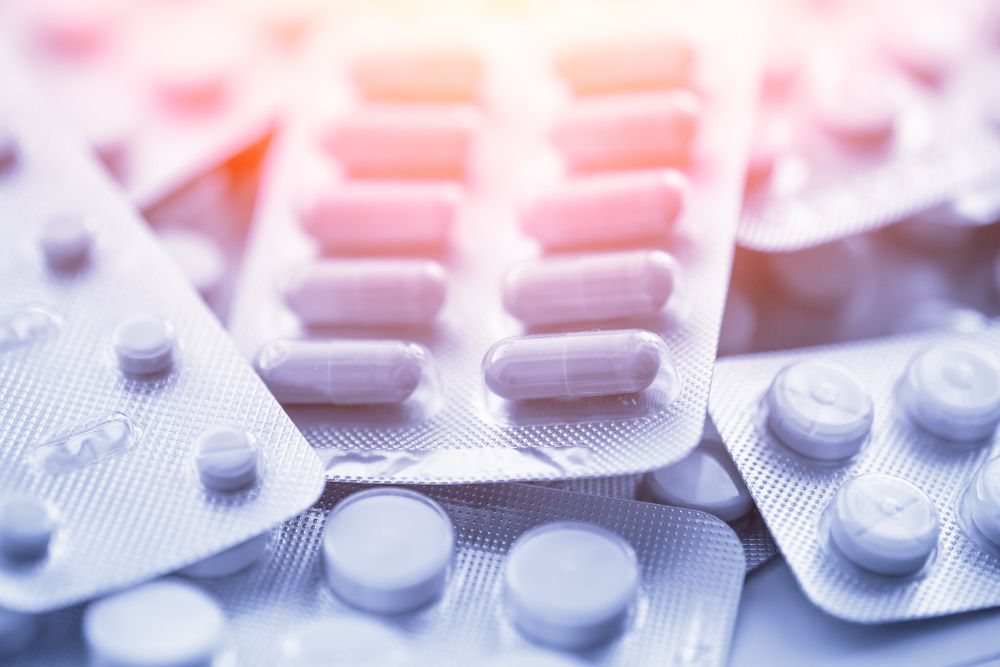
ACG acquires specialty packaging foils supplier
ACG strengthened its packaging solutions services by acquiring Technical Aluminum Foil Company.Capsules and packaging manufacturer ACG (Mumbai, India) has acquired specialty packaging foils supplier Technical Aluminum Foil Company (TAFC; Ajman, United Arab Emirates). ACG says this acquisition strengthens its comprehensive packaging solutions, especially in the Middle Eastern and African markets.TAFC’s aluminum and specialty packaging have high barrier properties and are used in both the pharmaceutical and food industries. The company also specializes in lacquering, lamination, printing, and slitting services.Source: https://www.nutritionaloutlook.com/
Read more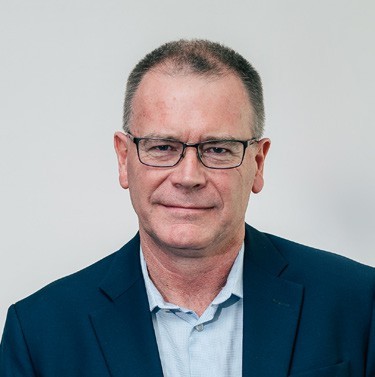
Improving Machinery in Pharmaceutical Manufacturing
IPT talks to Richard Stedman of ACG Engineering about the rise of connected and digitalised machines, and how these will improve pharmaceutical manufacturing in the futureIPT: Which pharmaceutical manufacturing innovation has had the most significant effect?Richard Stedman (RS): I have been a consumer of pharmaceuticals for a great deal longer than I have been on the manufacturing side of the industry. I therefore greatly value innovations that make the life of the patient easier – those which help to reduce any suffering.I believe that innovations such as fixed dosage combinations and modified release pills have been inspirational in terms of combatting patient reluctance around consuming multiple dosages.IPT: What are ‘connected machines’ and how has their rise benefited pharmaceutical manufacturing?RS: Connected machines focus on holistically improving total cost of ownership (TCO) through optimising equipment efficiency and performance. Numerous sensors collect data across various aspects, including the production process, overall energy consumption, maintenance and machine health. This combined information helps subject matter experts (technicians) to build curated dashboards to enable pharma manufacturers to effectively monitor their equipment. This, in turn, helps them to identify opportunities and adjust the process, improve productivity, reduce downtime and eliminate unnecessary energy consumption.The goal of such machines is to help manufacturers maintain the processes of the equipment at optimum levels, helping to maximise overall productivity and, in doing so, improve TCO.IPT: What are some of the most important aspects to consider when collaborating with other countries for equipment design?RS: Firstly, process and communication are crucial. Clear and effective communication channels must be established, taking factors such as language barriers, cultural differences and time zones into consideration. Regular video conferences and meetings, emails and documentation exchange are all essential for successful collaboration. The process of collaboration must be clearly defined.Secondly, understanding the regulatory requirements of the target country is vital. It’s important to have an appreciation of the fact that each country may have different standards and regulations for equipment design in the pharmaceutical industry. Compliance with these regulations is essential to ensure the safety, quality and efficacy of the final product.Thirdly, intellectual property (IP) protection must be evaluated. Collaborating with other countries may involve sharing sensitive information and designs. Robust contracts, including non-disclosure agreements (NDAs) and intellectual property protection measures, should be in place to safeguard proprietary information and the end user.Fourth, technical expertise is critical. Collaborating with partners who have the necessary technical knowledge and experience in the pharmaceutical industry is paramount when it comes to designing high-quality and efficient equipment.Lastly, cultural understanding and mutual respect are important. Being aware of cultural differences, customs and business practices can foster a positive and productive working relationship with international partners.In conclusion, successful collaboration for equipment design with other countries requires effective communication, defined processes, understanding of regulatory requirements, IP protection, technical expertise and cultural awareness.IPT: How are developments in pharmaceutical machines enabling tabletting and capsuling devices to maintain high standards of production?RS: As has always been the ethos of the pharma industry, which underlies the cGMP (current Good Manufacturing Practices), quality remains of utmost importance. Every enhancement of the quality and OEE (overall equipment effectiveness) in pharma manufacturing means more lives made better. Significant advancements in pharmaceutical machines have enabled tabletting and capsuling devices to maintain the highest standards of production. Such developments have been instrumental in improving the efficiency, precision and quality of tablet and capsule production across the industry.One key development is the integration of automation in pharmaceutical machines. Automation has revolutionised the manufacturing process by reducing human intervention, thereby minimising the risk of errors and contamination. Automatic systems have been incorporated into tabletting and capsuling devices, allowing for precise and consistent dosing, filling and sealing of tablets and capsules. This has resulted in higher production rates and improved product quality, as automatic systems can consistently perform repetitive tasks with minimal variation.Another significant advancement is the use of cutting-edge sensors and monitoring systems. These sensors provide real-time data on critical process parameters such as temperature, pressure and humidity, allowing for precise control and monitoring of the manufacturing process. This ensures that tablets and capsules are produced within the specified tolerances, maintaining high standards of quality and consistency.Advancements in material handling and feeding systems have also contributed to maintaining high standards of production. These ensure that the right amount of raw materials is accurately measured, mixed and fed into the machines, resulting in uniformity in both the composition and weight of tablets and capsules.Additionally, improvements in machine design and construction have led to machines that are more hygienic and easier to clean, reducing the risk of cross-contamination and ensuring compliance with the industry’s strict regulatory requirements.Developments in pharmaceutical machines, including automation, advanced sensors and monitoring systems, material handling and feeding systems and improved machine design, have resulted in increased efficiency, precision and quality in the manufacture of tablets and capsules. As a result, this has hugely benefited the pharmaceutical industry and, ultimately, the patients who rely on these medications for their health and well-being.IPT: Where do you see the developments in pharmaceutical machine manufacturing heading in the next decade?RS: I believe the future of pharmaceutical machine manufacturing will be characterised by a number of significant advancements and innovations.First and foremost, automation and digitisation will continue to play a crucial role in the pharmaceutical machine manufacturing industry. We will witness the integration of cutting-edge technologies, such as artificial intelligence (AI), machine learning (ML) and the Internet of Things (IoT), into pharmaceutical machines to enhance their efficiency and precision. This will result in increased productivity, reduced downtime and improved quality control, leading to higher yields and cost savings for pharmaceutical manufacturers and the lowering of TCO.Moreover, there will be a growing emphasis on sustainability and environmental consciousness over the next decade. Pharmaceutical machine manufacturers will focus on developing eco-friendly machines that minimise waste, reduce energy consumption and comply with stringent environmental regulations. This will involve the use of renewable energy sources, the implementation of green manufacturing practices and the adoption of recyclable and biodegradable materials across machine components.Furthermore, the trend towards personalised medicine and customised pharmaceutical products will impact pharmaceutical machine manufacturing. Machines that can handle smaller batches, accommodate varying formulations and enable rapid changeovers will be in high demand. Manufacturers will need to be flexibile and adaptable in order to meet the evolving needs of the pharmaceutical industry.Regulatory compliance will continue to be a top priority in pharmaceutical machine manufacturing. Stringent regulations governing the production of pharmaceuticals, including tablets and capsules, will drive the development of machines that ensure compliance with good manufacturing practices (GMP), international standards and regulatory guidelines. This will involve robust documentation, validation and qualification processes to ensure the safety, efficacy and quality of pharmaceutical products.In summary, the developments in pharmaceutical machine manufacturing in the next decade will be characterised by automation, digitisation, sustainability, customisation and regulatory compliance. The industry will witness the integration of advanced technologieIPT talks to Richard Stedman of ACG Engineering about the rise of connected and digitalised machines, and how these will improve pharmaceutical manufacturing in the futureIPT: Which pharmaceutical manufacturing innovation has had the most significant effect?Richard Stedman (RS): I have been a consumer of pharmaceuticals for a great deal longer than I have been on the manufacturing side of the industry. I therefore greatly value innovations that make the life of the patient easier – those which help to reduce any suffering.I believe that innovations such as fixed dosage combinations and modified release pills have been inspirational in terms of combatting patient reluctance around consuming multiple dosages.IPT: What are ‘connected machines’ and how has their rise benefited pharmaceutical manufacturing?RS: Connected machines focus on holistically improving total cost of ownership (TCO) through optimising equipment efficiency and performance. Numerous sensors collect data across various aspects, including the production process, overall energy consumption, maintenance and machine health. This combined information helps subject matter experts (technicians) to build curated dashboards to enable pharma manufacturers to effectively monitor their equipment. This, in turn, helps them to identify opportunities and adjust the process, improve productivity, reduce downtime and eliminate unnecessary energy consumption.The goal of such machines is to help manufacturers maintain the processes of the equipment at optimum levels, helping to maximise overall productivity and, in doing so, improve TCO.IPT: What are some of the most important aspects to consider when collaborating with other countries for equipment design?RS: Firstly, process and communication are crucial. Clear and effective communication channels must be established, taking factors such as language barriers, cultural differences and time zones into consideration. Regular video conferences and meetings, emails and documentation exchange are all essential for successful collaboration. The process of collaboration must be clearly defined.Secondly, understanding the regulatory requirements of the target country is vital. It’s important to have an appreciation of the fact that each country may have different standards and regulations for equipment design in the pharmaceutical industry. Compliance with these regulations is essential to ensure the safety, quality and efficacy of the final product.Thirdly, intellectual property (IP) protection must be evaluated. Collaborating with other countries may involve sharing sensitive information and designs. Robust contracts, including non-disclosure agreements (NDAs) and intellectual property protection measures, should be in place to safeguard proprietary information and the end user.Fourth, technical expertise is critical. Collaborating with partners who have the necessary technical knowledge and experience in the pharmaceutical industry is paramount when it comes to designing high-quality and efficient equipment.Lastly, cultural understanding and mutual respect are important. Being aware of cultural differences, customs and business practices can foster a positive and productive working relationship with international partners.In conclusion, successful collaboration for equipment design with other countries requires effective communication, defined processes, understanding of regulatory requirements, IP protection, technical expertise and cultural awareness.IPT: How are developments in pharmaceutical machines enabling tabletting and capsuling devices to maintain high standards of production?RS: As has always been the ethos of the pharma industry, which underlies the cGMP (current Good Manufacturing Practices), quality remains of utmost importance. Every enhancement of the quality and OEE (overall equipment effectiveness) in pharma manufacturing means more lives made better. Significant advancements in pharmaceutical machines have enabled tabletting and capsuling devices to maintain the highest standards of production. Such developments have been instrumental in improving the efficiency, precision and quality of tablet and capsule production across the industry.One key development is the integration of automation in pharmaceutical machines. Automation has revolutionised the manufacturing process by reducing human intervention, thereby minimising the risk of errors and contamination. Automatic systems have been incorporated into tabletting and capsuling devices, allowing for precise and consistent dosing, filling and sealing of tablets and capsules. This has resulted in higher production rates and improved product quality, as automatic systems can consistently perform repetitive tasks with minimal variation.Another significant advancement is the use of cutting-edge sensors and monitoring systems. These sensors provide real-time data on critical process parameters such as temperature, pressure and humidity, allowing for precise control and monitoring of the manufacturing process. This ensures that tablets and capsules are produced within the specified tolerances, maintaining high standards of quality and consistency.Advancements in material handling and feeding systems have also contributed to maintaining high standards of production. These ensure that the right amount of raw materials is accurately measured, mixed and fed into the machines, resulting in uniformity in both the composition and weight of tablets and capsules.Additionally, improvements in machine design and construction have led to machines that are more hygienic and easier to clean, reducing the risk of cross-contamination and ensuring compliance with the industry’s strict regulatory requirements.Developments in pharmaceutical machines, including automation, advanced sensors and monitoring systems, material handling and feeding systems and improved machine design, have resulted in increased efficiency, precision and quality in the manufacture of tablets and capsules. As a result, this has hugely benefited the pharmaceutical industry and, ultimately, the patients who rely on these medications for their health and well-being.IPT: Where do you see the developments in pharmaceutical machine manufacturing heading in the next decade?RS: I believe the future of pharmaceutical machine manufacturing will be characterised by a number of significant advancements and innovations.First and foremost, automation and digitisation will continue to play a crucial role in the pharmaceutical machine manufacturing industry. We will witness the integration of cutting-edge technologies, such as artificial intelligence (AI), machine learning (ML) and the Internet of Things (IoT), into pharmaceutical machines to enhance their efficiency and precision. This will result in increased productivity, reduced downtime and improved quality control, leading to higher yields and cost savings for pharmaceutical manufacturers and the lowering of TCO.Moreover, there will be a growing emphasis on sustainability and environmental consciousness over the next decade. Pharmaceutical machine manufacturers will focus on developing eco-friendly machines that minimise waste, reduce energy consumption and comply with stringent environmental regulations. This will involve the use of renewable energy sources, the implementation of green manufacturing practices and the adoption of recyclable and biodegradable materials across machine components.Furthermore, the trend towards personalised medicine and customised pharmaceutical products will impact pharmaceutical machine manufacturing. Machines that can handle smaller batches, accommodate varying formulations and enable rapid changeovers will be in high demand. Manufacturers will need to be flexibile and adaptable in order to meet the evolving needs of the pharmaceutical industry.Regulatory compliance will continue to be a top priority in pharmaceutical machine manufacturing. Stringent regulations governing the production of pharmaceuticals, including tablets and capsules, will drive the development of machines that ensure compliance with good manufacturing practices (GMP), international standards and regulatory guidelines. This will involve robust documentation, validation and qualification processes to ensure the safety, efficacy and quality of pharmaceutical products.In summary, the developments in pharmaceutical machine manufacturing in the next decade will be characterised by automation, digitisation, sustainability, customisation and regulatory compliance. The industry will witness the integration of advanced technologieIPT talks to Richard Stedman of ACG Engineering about the rise of connected and digitalised machines, and how these will improve pharmaceutical manufacturing in the futureIPT: Which pharmaceutical manufacturing innovation has had the most significant effect?Richard Stedman (RS): I have been a consumer of pharmaceuticals for a great deal longer than I have been on the manufacturing side of the industry. I therefore greatly value innovations that make the life of the patient easier – those which help to reduce any suffering.I believe that innovations such as fixed dosage combinations and modified release pills have been inspirational in terms of combatting patient reluctance around consuming multiple dosages.IPT: What are ‘connected machines’ and how has their rise benefited pharmaceutical manufacturing?RS: Connected machines focus on holistically improving total cost of ownership (TCO) through optimising equipment efficiency and performance. Numerous sensors collect data across various aspects, including the production process, overall energy consumption, maintenance and machine health. This combined information helps subject matter experts (technicians) to build curated dashboards to enable pharma manufacturers to effectively monitor their equipment. This, in turn, helps them to identify opportunities and adjust the process, improve productivity, reduce downtime and eliminate unnecessary energy consumption.The goal of such machines is to help manufacturers maintain the processes of the equipment at optimum levels, helping to maximise overall productivity and, in doing so, improve TCO.IPT: What are some of the most important aspects to consider when collaborating with other countries for equipment design?RS: Firstly, process and communication are crucial. Clear and effective communication channels must be established, taking factors such as language barriers, cultural differences and time zones into consideration. Regular video conferences and meetings, emails and documentation exchange are all essential for successful collaboration. The process of collaboration must be clearly defined.Secondly, understanding the regulatory requirements of the target country is vital. It’s important to have an appreciation of the fact that each country may have different standards and regulations for equipment design in the pharmaceutical industry. Compliance with these regulations is essential to ensure the safety, quality and efficacy of the final product.Thirdly, intellectual property (IP) protection must be evaluated. Collaborating with other countries may involve sharing sensitive information and designs. Robust contracts, including non-disclosure agreements (NDAs) and intellectual property protection measures, should be in place to safeguard proprietary information and the end user.Fourth, technical expertise is critical. Collaborating with partners who have the necessary technical knowledge and experience in the pharmaceutical industry is paramount when it comes to designing high-quality and efficient equipment.Lastly, cultural understanding and mutual respect are important. Being aware of cultural differences, customs and business practices can foster a positive and productive working relationship with international partners.In conclusion, successful collaboration for equipment design with other countries requires effective communication, defined processes, understanding of regulatory requirements, IP protection, technical expertise and cultural awareness.IPT: How are developments in pharmaceutical machines enabling tabletting and capsuling devices to maintain high standards of production?RS: As has always been the ethos of the pharma industry, which underlies the cGMP (current Good Manufacturing Practices), quality remains of utmost importance. Every enhancement of the quality and OEE (overall equipment effectiveness) in pharma manufacturing means more lives made better. Significant advancements in pharmaceutical machines have enabled tabletting and capsuling devices to maintain the highest standards of production. Such developments have been instrumental in improving the efficiency, precision and quality of tablet and capsule production across the industry.One key development is the integration of automation in pharmaceutical machines. Automation has revolutionised the manufacturing process by reducing human intervention, thereby minimising the risk of errors and contamination. Automatic systems have been incorporated into tabletting and capsuling devices, allowing for precise and consistent dosing, filling and sealing of tablets and capsules. This has resulted in higher production rates and improved product quality, as automatic systems can consistently perform repetitive tasks with minimal variation.Another significant advancement is the use of cutting-edge sensors and monitoring systems. These sensors provide real-time data on critical process parameters such as temperature, pressure and humidity, allowing for precise control and monitoring of the manufacturing process. This ensures that tablets and capsules are produced within the specified tolerances, maintaining high standards of quality and consistency.Advancements in material handling and feeding systems have also contributed to maintaining high standards of production. These ensure that the right amount of raw materials is accurately measured, mixed and fed into the machines, resulting in uniformity in both the composition and weight of tablets and capsules.Additionally, improvements in machine design and construction have led to machines that are more hygienic and easier to clean, reducing the risk of cross-contamination and ensuring compliance with the industry’s strict regulatory requirements.Developments in pharmaceutical machines, including automation, advanced sensors and monitoring systems, material handling and feeding systems and improved machine design, have resulted in increased efficiency, precision and quality in the manufacture of tablets and capsules. As a result, this has hugely benefited the pharmaceutical industry and, ultimately, the patients who rely on these medications for their health and well-being.IPT: Where do you see the developments in pharmaceutical machine manufacturing heading in the next decade?RS: I believe the future of pharmaceutical machine manufacturing will be characterised by a number of significant advancements and innovations.First and foremost, automation and digitisation will continue to play a crucial role in the pharmaceutical machine manufacturing industry. We will witness the integration of cutting-edge technologies, such as artificial intelligence (AI), machine learning (ML) and the Internet of Things (IoT), into pharmaceutical machines to enhance their efficiency and precision. This will result in increased productivity, reduced downtime and improved quality control, leading to higher yields and cost savings for pharmaceutical manufacturers and the lowering of TCO.Moreover, there will be a growing emphasis on sustainability and environmental consciousness over the next decade. Pharmaceutical machine manufacturers will focus on developing eco-friendly machines that minimise waste, reduce energy consumption and comply with stringent environmental regulations. This will involve the use of renewable energy sources, the implementation of green manufacturing practices and the adoption of recyclable and biodegradable materials across machine components.Furthermore, the trend towards personalised medicine and customised pharmaceutical products will impact pharmaceutical machine manufacturing. Machines that can handle smaller batches, accommodate varying formulations and enable rapid changeovers will be in high demand. Manufacturers will need to be flexibile and adaptable in order to meet the evolving needs of the pharmaceutical industry.Regulatory compliance will continue to be a top priority in pharmaceutical machine manufacturing. Stringent regulations governing the production of pharmaceuticals, including tablets and capsules, will drive the development of machines that ensure compliance with good manufacturing practices (GMP), international standards and regulatory guidelines. This will involve robust documentation, validation and qualification processes to ensure the safety, efficacy and quality of pharmaceutical products.In summary, the developments in pharmaceutical machine manufacturing in the next decade will be characterised by automation, digitisation, sustainability, customisation and regulatory compliance. The industry will witness the integration of advanced technologieIPT talks to Richard Stedman of ACG Engineering about the rise of connected and digitalised machines, and how these will improve pharmaceutical manufacturing in the futureIPT: Which pharmaceutical manufacturing innovation has had the most significant effect?Richard Stedman (RS): I have been a consumer of pharmaceuticals for a great deal longer than I have been on the manufacturing side of the industry. I therefore greatly value innovations that make the life of the patient easier – those which help to reduce any suffering.I believe that innovations such as fixed dosage combinations and modified release pills have been inspirational in terms of combatting patient reluctance around consuming multiple dosages.IPT: What are ‘connected machines’ and how has their rise benefited pharmaceutical manufacturing?RS: Connected machines focus on holistically improving total cost of ownership (TCO) through optimising equipment efficiency and performance. Numerous sensors collect data across various aspects, including the production process, overall energy consumption, maintenance and machine health. This combined information helps subject matter experts (technicians) to build curated dashboards to enable pharma manufacturers to effectively monitor their equipment. This, in turn, helps them to identify opportunities and adjust the process, improve productivity, reduce downtime and eliminate unnecessary energy consumption.The goal of such machines is to help manufacturers maintain the processes of the equipment at optimum levels, helping to maximise overall productivity and, in doing so, improve TCO.IPT: What are some of the most important aspects to consider when collaborating with other countries for equipment design?RS: Firstly, process and communication are crucial. Clear and effective communication channels must be established, taking factors such as language barriers, cultural differences and time zones into consideration. Regular video conferences and meetings, emails and documentation exchange are all essential for successful collaboration. The process of collaboration must be clearly defined.Secondly, understanding the regulatory requirements of the target country is vital. It’s important to have an appreciation of the fact that each country may have different standards and regulations for equipment design in the pharmaceutical industry. Compliance with these regulations is essential to ensure the safety, quality and efficacy of the final product.Thirdly, intellectual property (IP) protection must be evaluated. Collaborating with other countries may involve sharing sensitive information and designs. Robust contracts, including non-disclosure agreements (NDAs) and intellectual property protection measures, should be in place to safeguard proprietary information and the end user.Fourth, technical expertise is critical. Collaborating with partners who have the necessary technical knowledge and experience in the pharmaceutical industry is paramount when it comes to designing high-quality and efficient equipment.Lastly, cultural understanding and mutual respect are important. Being aware of cultural differences, customs and business practices can foster a positive and productive working relationship with international partners.In conclusion, successful collaboration for equipment design with other countries requires effective communication, defined processes, understanding of regulatory requirements, IP protection, technical expertise and cultural awareness.IPT: How are developments in pharmaceutical machines enabling tabletting and capsuling devices to maintain high standards of production?RS: As has always been the ethos of the pharma industry, which underlies the cGMP (current Good Manufacturing Practices), quality remains of utmost importance. Every enhancement of the quality and OEE (overall equipment effectiveness) in pharma manufacturing means more lives made better. Significant advancements in pharmaceutical machines have enabled tabletting and capsuling devices to maintain the highest standards of production. Such developments have been instrumental in improving the efficiency, precision and quality of tablet and capsule production across the industry.One key development is the integration of automation in pharmaceutical machines. Automation has revolutionised the manufacturing process by reducing human intervention, thereby minimising the risk of errors and contamination. Automatic systems have been incorporated into tabletting and capsuling devices, allowing for precise and consistent dosing, filling and sealing of tablets and capsules. This has resulted in higher production rates and improved product quality, as automatic systems can consistently perform repetitive tasks with minimal variation.Another significant advancement is the use of cutting-edge sensors and monitoring systems. These sensors provide real-time data on critical process parameters such as temperature, pressure and humidity, allowing for precise control and monitoring of the manufacturing process. This ensures that tablets and capsules are produced within the specified tolerances, maintaining high standards of quality and consistency.Advancements in material handling and feeding systems have also contributed to maintaining high standards of production. These ensure that the right amount of raw materials is accurately measured, mixed and fed into the machines, resulting in uniformity in both the composition and weight of tablets and capsules.Additionally, improvements in machine design and construction have led to machines that are more hygienic and easier to clean, reducing the risk of cross-contamination and ensuring compliance with the industry’s strict regulatory requirements.Developments in pharmaceutical machines, including automation, advanced sensors and monitoring systems, material handling and feeding systems and improved machine design, have resulted in increased efficiency, precision and quality in the manufacture of tablets and capsules. As a result, this has hugely benefited the pharmaceutical industry and, ultimately, the patients who rely on these medications for their health and well-being.IPT: Where do you see the developments in pharmaceutical machine manufacturing heading in the next decade?RS: I believe the future of pharmaceutical machine manufacturing will be characterised by a number of significant advancements and innovations.First and foremost, automation and digitisation will continue to play a crucial role in the pharmaceutical machine manufacturing industry. We will witness the integration of cutting-edge technologies, such as artificial intelligence (AI), machine learning (ML) and the Internet of Things (IoT), into pharmaceutical machines to enhance their efficiency and precision. This will result in increased productivity, reduced downtime and improved quality control, leading to higher yields and cost savings for pharmaceutical manufacturers and the lowering of TCO.Moreover, there will be a growing emphasis on sustainability and environmental consciousness over the next decade. Pharmaceutical machine manufacturers will focus on developing eco-friendly machines that minimise waste, reduce energy consumption and comply with stringent environmental regulations. This will involve the use of renewable energy sources, the implementation of green manufacturing practices and the adoption of recyclable and biodegradable materials across machine components.Furthermore, the trend towards personalised medicine and customised pharmaceutical products will impact pharmaceutical machine manufacturing. Machines that can handle smaller batches, accommodate varying formulations and enable rapid changeovers will be in high demand. Manufacturers will need to be flexibile and adaptable in order to meet the evolving needs of the pharmaceutical industry.Regulatory compliance will continue to be a top priority in pharmaceutical machine manufacturing. Stringent regulations governing the production of pharmaceuticals, including tablets and capsules, will drive the development of machines that ensure compliance with good manufacturing practices (GMP), international standards and regulatory guidelines. This will involve robust documentation, validation and qualification processes to ensure the safety, efficacy and quality of pharmaceutical products.In summary, the developments in pharmaceutical machine manufacturing in the next decade will be characterised by automation, digitisation, sustainability, customisation and regulatory compliance. The industry will witness the integration of advanced technologieIPT talks to Richard Stedman of ACG Engineering about the rise of connected and digitalised machines, and how these will improve pharmaceutical manufacturing in the futureIPT: Which pharmaceutical manufacturing innovation has had the most significant effect?Richard Stedman (RS): I have been a consumer of pharmaceuticals for a great deal longer than I have been on the manufacturing side of the industry. I therefore greatly value innovations that make the life of the patient easier – those which help to reduce any suffering.I believe that innovations such as fixed dosage combinations and modified release pills have been inspirational in terms of combatting patient reluctance around consuming multiple dosages.IPT: What are ‘connected machines’ and how has their rise benefited pharmaceutical manufacturing?RS: Connected machines focus on holistically improving total cost of ownership (TCO) through optimising equipment efficiency and performance. Numerous sensors collect data across various aspects, including the production process, overall energy consumption, maintenance and machine health. This combined information helps subject matter experts (technicians) to build curated dashboards to enable pharma manufacturers to effectively monitor their equipment. This, in turn, helps them to identify opportunities and adjust the process, improve productivity, reduce downtime and eliminate unnecessary energy consumption.The goal of such machines is to help manufacturers maintain the processes of the equipment at optimum levels, helping to maximise overall productivity and, in doing so, improve TCO.IPT: What are some of the most important aspects to consider when collaborating with other countries for equipment design?RS: Firstly, process and communication are crucial. Clear and effective communication channels must be established, taking factors such as language barriers, cultural differences and time zones into consideration. Regular video conferences and meetings, emails and documentation exchange are all essential for successful collaboration. The process of collaboration must be clearly defined.Secondly, understanding the regulatory requirements of the target country is vital. It’s important to have an appreciation of the fact that each country may have different standards and regulations for equipment design in the pharmaceutical industry. Compliance with these regulations is essential to ensure the safety, quality and efficacy of the final product.Thirdly, intellectual property (IP) protection must be evaluated. Collaborating with other countries may involve sharing sensitive information and designs. Robust contracts, including non-disclosure agreements (NDAs) and intellectual property protection measures, should be in place to safeguard proprietary information and the end user.Fourth, technical expertise is critical. Collaborating with partners who have the necessary technical knowledge and experience in the pharmaceutical industry is paramount when it comes to designing high-quality and efficient equipment.Lastly, cultural understanding and mutual respect are important. Being aware of cultural differences, customs and business practices can foster a positive and productive working relationship with international partners.In conclusion, successful collaboration for equipment design with other countries requires effective communication, defined processes, understanding of regulatory requirements, IP protection, technical expertise and cultural awareness.IPT: How are developments in pharmaceutical machines enabling tabletting and capsuling devices to maintain high standards of production?RS: As has always been the ethos of the pharma industry, which underlies the cGMP (current Good Manufacturing Practices), quality remains of utmost importance. Every enhancement of the quality and OEE (overall equipment effectiveness) in pharma manufacturing means more lives made better. Significant advancements in pharmaceutical machines have enabled tabletting and capsuling devices to maintain the highest standards of production. Such developments have been instrumental in improving the efficiency, precision and quality of tablet and capsule production across the industry.One key development is the integration of automation in pharmaceutical machines. Automation has revolutionised the manufacturing process by reducing human intervention, thereby minimising the risk of errors and contamination. Automatic systems have been incorporated into tabletting and capsuling devices, allowing for precise and consistent dosing, filling and sealing of tablets and capsules. This has resulted in higher production rates and improved product quality, as automatic systems can consistently perform repetitive tasks with minimal variation.Another significant advancement is the use of cutting-edge sensors and monitoring systems. These sensors provide real-time data on critical process parameters such as temperature, pressure and humidity, allowing for precise control and monitoring of the manufacturing process. This ensures that tablets and capsules are produced within the specified tolerances, maintaining high standards of quality and consistency.Advancements in material handling and feeding systems have also contributed to maintaining high standards of production. These ensure that the right amount of raw materials is accurately measured, mixed and fed into the machines, resulting in uniformity in both the composition and weight of tablets and capsules.Additionally, improvements in machine design and construction have led to machines that are more hygienic and easier to clean, reducing the risk of cross-contamination and ensuring compliance with the industry’s strict regulatory requirements.Developments in pharmaceutical machines, including automation, advanced sensors and monitoring systems, material handling and feeding systems and improved machine design, have resulted in increased efficiency, precision and quality in the manufacture of tablets and capsules. As a result, this has hugely benefited the pharmaceutical industry and, ultimately, the patients who rely on these medications for their health and well-being.IPT: Where do you see the developments in pharmaceutical machine manufacturing heading in the next decade?RS: I believe the future of pharmaceutical machine manufacturing will be characterised by a number of significant advancements and innovations.First and foremost, automation and digitisation will continue to play a crucial role in the pharmaceutical machine manufacturing industry. We will witness the integration of cutting-edge technologies, such as artificial intelligence (AI), machine learning (ML) and the Internet of Things (IoT), into pharmaceutical machines to enhance their efficiency and precision. This will result in increased productivity, reduced downtime and improved quality control, leading to higher yields and cost savings for pharmaceutical manufacturers and the lowering of TCO.Moreover, there will be a growing emphasis on sustainability and environmental consciousness over the next decade. Pharmaceutical machine manufacturers will focus on developing eco-friendly machines that minimise waste, reduce energy consumption and comply with stringent environmental regulations. This will involve the use of renewable energy sources, the implementation of green manufacturing practices and the adoption of recyclable and biodegradable materials across machine components.Furthermore, the trend towards personalised medicine and customised pharmaceutical products will impact pharmaceutical machine manufacturing. Machines that can handle smaller batches, accommodate varying formulations and enable rapid changeovers will be in high demand. Manufacturers will need to be flexibile and adaptable in order to meet the evolving needs of the pharmaceutical industry.Regulatory compliance will continue to be a top priority in pharmaceutical machine manufacturing. Stringent regulations governing the production of pharmaceuticals, including tablets and capsules, will drive the development of machines that ensure compliance with good manufacturing practices (GMP), international standards and regulatory guidelines. This will involve robust documentation, validation and qualification processes to ensure the safety, efficacy and quality of pharmaceutical products.In summary, the developments in pharmaceutical machine manufacturing in the next decade will be characterised by automation, digitisation, sustainability, customisation and regulatory compliance. The industry will witness the integration of advanced technologies, increased focus on environmental sustainability and the development of flexible and compliant machines to meet the industry’s evolving needs.Richard Stedman is the CEO of ACG Engineering. With over 35 years of experience in the packaging, engineering and pharmaceutical manufacturing industries, Richard has led and transformed multiple businesses globally. Richard is committed to driving innovation and excellence in the pharmaceutical manufacturing industry. He is passionate about delivering high-quality products and services to customers and is dedicated to building a strong and sustainable future for ACG.Source: https://www.iptonline.com/
Read more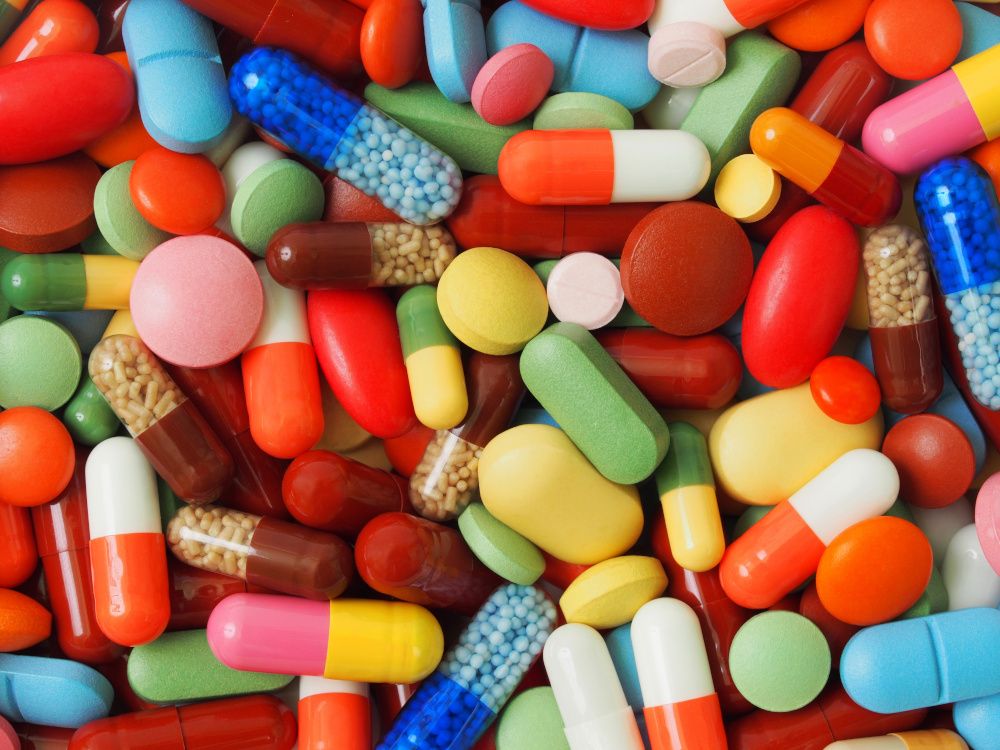
As nutraceutical and pharmaceutical firms compete for a bigger slice of the healthcare market, delivery innovations like pelletization will help them stand out
How pelletization can give the nutraceutical industry a boost, according to experts from Vantage Nutrition and ACG Capsules.The level of awareness individuals have of their own health and well-being grew exponentially during the COVID-19 pandemic. This awareness fueled a shift from a reactive approach to health and personal care to a more proactive and predictive one.The nutraceutical and pharmaceutical industries are now vying for a wider share of this growing base of health-conscious individuals. This has translated to greater innovation and an expanding portfolio of high-quality and convenient products aimed at improving consumer health.The Advantages of Pelletization for Oral SupplementsThe majority of nutraceutical supplements offered are available in an oral format. New technologies continue to pave the way for innovation when it comes to release modification and new product development.Pelletization has proved to be a boon for nutraceutical providers, opening the door to a plethora of opportunities for the nutraceutical sector. It can offer suitable, cost-efficient solutions to multiple challenges, including efficacy, dosage, delivery, and absorption challenges.Typically, the pellets found in supplements are small, free-flowing spherical or semi-spherical solid particles made up of fine powders or granules which then can be coated or encapsulated with other materials. They are used primarily for release modification of active ingredients and can therefore play a role in enhancing the efficacy of a supplement.Pelletization can also provide a greater degree of flexibility with respect to the evolution and appearance of product formulations. It allows the separation of active ingredients into completely different dose strengths, without the need for method changes, and can be used to administer incompatible, biologically active substances all at once. It also offers the scope for immediate or controlled oral delivery.Additionally, pellet formations can help to improve the absorption and distribution of actives. The coating applied during pelletization forms a protective layer, helping to mask the odor and unpleasant taste of active ingredients, improving palatability. This helps to increase consumer compliance, while the aesthetic appeal of the pellets enhances the distinction of the product, which can improve marketing efforts.Emerging InnovationsThese examples of the evolution and growth of pelletization over the last decade has nutraceutical innovators looking to the future. Developers are moving beyond simple pellet formulations and are exploring all the possible options, focusing on new and more effective technologies that can help to bring purer, more effective, and more complex products to market.Traditionally, pellets have been used in product forms like sachets, capsules, and tablets. Pellets in capsules are widely accepted nowadays and offer the most scope for overall product modification, with the hard capsule acting as an excellent container to deliver the pellets to the desired site.Sprinkle capsules have recently emerged as a new trend, aimed at people who have difficulty swallowing, including children and the elderly. These capsules carry the active content in pellet form, which can be sprinkled on food or juice.Capsules that combine two separate delivery systems, like pellets and liquid formulation in a single unit, are another example of an innovation gaining momentum. One of the challenges the nutraceutical industry currently faces is how to deliver complex materials in way that enhances their effectiveness and ensures maximum absorption in an efficient manner. This novel technique can provide the means to deliver complex actives by incorporating them in their original form, whether in a liquid or a solid. They can deliver the active ingredients immediately (via liquid), and in a controlled manner (through solid pellets), simultaneously. This format also satisfies compatibility issues on an operational level by offering the choice of pellets with tiny capsules in liquid-filled capsules.The FuturePelletization is not a new technology, but it continues to be a revolutionary one when it comes to providing versatile delivery formats for nutraceuticals and pharmaceuticals alike. It has shown an immense scope for customization and modification in release patterns, as well as aesthetic appeal. With its significant potential for growth and brand extension, pelletization is set to continue providing significant benefits to manufacturers, consumers, and market players.About the AuthorsSurya Singh, PhD, is senior manager of product development at Vantage Nutrition LLP (India). Jnanadeva Bhat, PhD, is head of formulation R&D, pharma and nutra, at Vantage Nutrition LLP and ACG Capsules (India). Manali Dalvi, M.Pharm, is the lead whitepaper and publications specialist, pharma and nutra, at Vantage Nutrition LLP and ACG Capsules.Source: https://www.nutritionaloutlook.com/
Read more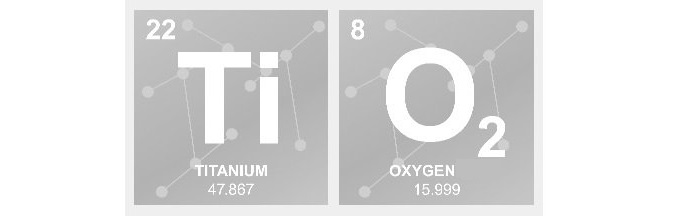
Is the pharmaceutical sector prepared to face a titanium dioxide ban?
Dr Subhashis Chakraborty, head of Global Product Management, ACG CapsulesIn the wake of the ban on titanium dioxide (TiO2) E171 in the production of food and dietary supplements in the EU, the pharmaceutical industry may face a similar ban as early as 2025.Why exactly is titanium dioxide’s safety being questioned? If its safety is really a concern, is there a possibility of phasing it out completely from the EU? How prepared is the industry to cope with this change? Won’t this decision affect other global markets? What position have other regulatory authorities already taken? What could be the potential implication of this ban across other geographies? These are just a few of the major questions that remain unanswered and a key concern for the pharmaceutical industry.Considering Europe as an important reference market, although the ban is applicable to the European jurisdiction, its restricted use or complete prohibition in the production of drug products by the European Medicine Agency (EMA) may soon result in a snowball effect on other global markets. Moreover, companies supplying medicines to the EU and other regions will find themselves having to handle two parallel versions of every product – one containing TiO2 and another devoid of it. More importantly, imagine the scenario of the drug shortage that could arise if appropriate alternatives are not identified, or they become inadequately available.TiO2 has been used as a colouring and opacifying agent in the pharmaceutical industry for more than half a century. From capsule shells, tablet and pellet coatings, to suspensions and pastes, it is almost ubiquitously used in a wide range of dosage forms to impart product aesthetics and protect sensitive APIs from degradation. Unfortunately, no other excipient has been able to demonstrate a similar whiteness and opacity to TiO2. Therefore, although there are possibilities, replacements will have certain limitations. New formulation development may not be challenging but finding alternatives for more than 90,000 existing marketed products will take a heavy toll from a financial, time and resource point of view. This could be coupled with the myriad uncertainties of drug products being withdrawn from the market impacting the health of millions.There is already diverse opinion in the scientific community. Many global regulators in geographies such as Canada, UK, Australia/New Zealand and the United States have already taken an independent stance to disagree with the precautionary measures taken in the EU. Reformulating the existing drug products is not as simple as it appears. Replacement of TiO2 with an alternative is a mammoth task as it requires assessment from different aspects including regulations, compatibility, safety, efficacy, processibility and stability. While the International Pharmaceutical Excipients Council (IPEC) along with the members of the Innovation & Quality (IQ) Consortium are working to explore the appropriate strategy to handle the situation, pharmaceutical companies are looking out for TiO2 alternatives for their new developments.The allied industry supporting the pharmaceutical sector has started offering alternative excipients like calcium carbonate, talc and starch for white options and iron oxides for colored options. Whichever has worked best to support their ecosystem is related to either a coating mixture or an empty hard capsule shell. At ACG Capsules, we sensed the looming issue some time ago and – irrespective of the fate of the TiO2 ban in the industry – have partnered with the industry to support them by offering the right available alternatives under the brand of ACGcaps TSafe – including different colored variants in both gelatin and cellulose-based capsules. Additionally, we have worked with the companies on technical training – focusing on educational aspects around the alternatives. At this stage, there are no answers. With so many unforeseen obstacles along the way, it is difficult to predict whether TiO2 will be banned in pharma. Its fate would depend on how the scientific data and rationale being generated takes shape and, on the other hand, how it will be perceived by the regulatory bodies. For now, the only option available for the excipient manufacturers is to support and work closely with the formulators, in order to ensure the industry can correctly progress and to be prepared to face the outcomes of a TiO2 ban. Source: https://pharmafile.com/
Read more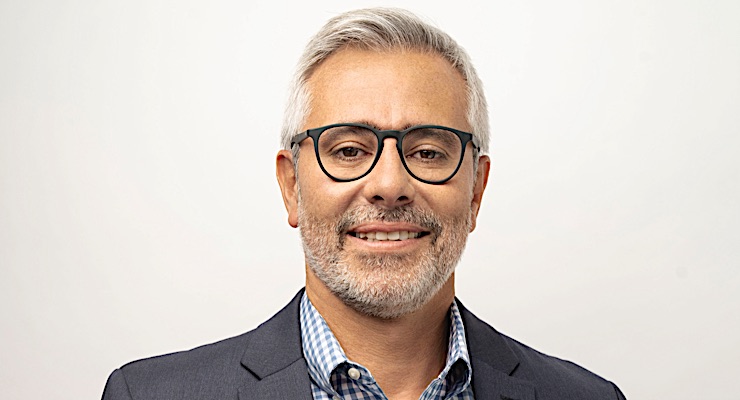
"3 Key Trends" with Rafael Costa
What are "3 Key Trends" shaping the CDMO industry in 2023 and beyond? ACG’s vice president of sales for Americas, Rafael Costa, shares his thoughts with Contract Pharma.High demand for flexible CDMOs with advanced capabilities and technologyAs the molecules used in drugs become increasingly complex, CDMOs with advanced capabilities and technology are likely to be in high demand. This includes CDMOs with expertise in areas such as biologics manufacturing, high-potency drug development, and continuous manufacturing. Those CDMOs which evolve to support complex supply chain management, compressed timelines and evolving regulations yet continue to introduce solutions to market faster will succeed. There is a growing need for flexibility and agility. Pharmaceutical companies will seek out CDMOs with the production technology to switch lines to new production requirements, or where they can quickly scale production up and down.Increasing globalizationThe combination of ongoing demands for advanced medicines, particularly in emerging economies and the drive to reduce manufacturing costs, has seen companies moving manufacturing facilities to new and different locations. This trend is likely to drive increasing demand for CDMOs with a global presence, and those with the ability to provide services to multiple regions. However, we should not ignore the fact that local manufacturing in the U.S. (post-pandemic) is also another key trend, with the government analyzing methods to incentivize the pharmaceutical industry to be less dependent on outside markets.Increasing use of outsourcing by small and mid-sized companiesIn addition to large pharmaceutical companies, small and midsize companies are also increasingly outsourcing their drug development and manufacturing to CDMOs. And, as before, those CDMOs which can provide services tailored to the needs of small and mid-sized companies are likely to be in greater demand.Source: https://www.contractpharma.com/
Read more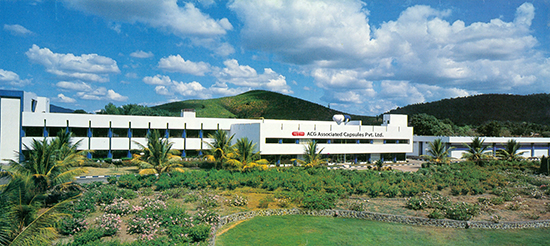
ACG shortlisted for Global Water Award
Dahanu-based Zero Liquid Discharge (ZLD) plant nominated for Industrial Project of the YearACG, a leading supplier of integrated manufacturing solutions to the global pharmaceutical and nutraceutical industries, is thrilled to announce its nomination for the Global Water Intelligence’s Industrial Project of the Year Award. Established in 2006 by Global Water Intelligence, the awards recognise the most important achievements in the international water industry.Each of the four finalists in the category represent an outstanding technical or environmental achievement in the field of industrial water and waste water.The ZLD project at ACG’s Dahanu plant recycles and recovers over 95% of water for reuse, helping to meet regulations and alleviate local water stress. The innovative combination of expanded granular sludge bed treatment, anoxic treatment for denitrification, membrane bioreactor and high-recovery RO were deployed. This was alongside advanced vacuum membrane distillation technology, which combines the advantages of thermal distillation and membranes to achieve high water quality at lower energy consumption. The membrane distillation technology used in the plant embodies an industry-changing move by ACG and its partner, industrial wastewater treatment specialist Aquatech. It is the first full-scale plant integrating advanced vacuum membrane distillation for membrane evaporation and an agitated thin film dryer for dewatering. The innovative solution enables ACG to save power and generate 400 Kwh per day of green energy through biomethane production, while achieving ZLD with an optimal energy footprint.The project at Dahanu is part of a larger water technology and service program implemented across multiple additional sites. The program aims to produce high-quality water for reuse from challenging waste streams by combining biological waste water treatment and membrane distillation to achieve ACG’s water sustainability goals.The winners of the 2023 Global Water Awards will be announced at the Global Water Summit in Berlin on 9 May.About ACGIn accordance with its commitment to making the world healthier, ACG has been delivering exceptional solutions to the global pharmaceutical and nutraceutical industry for sixty years, across six continents and in a hundred countries.Collaboration is at the core of ACG’s ethos. ACG is the world’s only integrated pharma manufacturing solutions company, with products ranging from capsules to films & foils, to engineering equipment and inspection systems – all that meet international regulatory requirements. For ACG, it’s always about finding innovative solutions to the world’s greatest health challenges, together.For more information, please contact the ACG media relations team:madhurima.chakraborty@acg-world.comAbout Aquatech:At Aquatech, we tackle the challenges of water scarcity and complexity by leveraging technology, expertise, and financing to deliver comprehensive solutions that reduce carbon and recycled water footprint. As a leading global provider of water and process technology solutions, we help the world’s most recognized companies achieve their sustainability and operational goals by implementing innovative approaches for water reuse, desalination, minimal and zero liquid discharge, and critical minerals recovery. Our work catalyzes the transition toward a more sustainable future and showcases our commitment to addressing water’s role in climate adaptation.Source: https://www.biospace.com
Read more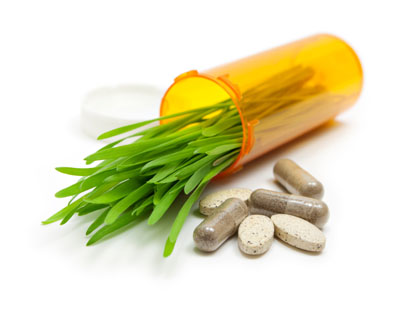
Immunity and awareness drive key innovations in nutraceuticals
Healthcare providers have evolved in recent years and broadened their business focus to new areas. An increased spotlight on health and wellness, heightened by COVID, continues to play a large part in the growth of pioneering segments involving nutraceuticals, functional foods and nutricosmeticsAccording to a recent study by Allied Market Research, the global nutraceuticals market size is projected to reach $650.5 billion by 2030, registering a CAGR of 3.9% from 2021 to 2030.1Consumer demand and an increasing preference for more natural, organic and herbal healthcare solutions — not to mention the rising costs and waiting times associated with healthcare — are helping to fuel this global growth and providing an opportunity for innovation in nutraceuticals.This article explores four major trends that are driving innovation in the nutraceutical industry in response to changing consumer views and behaviours.An increased focus on immune healthPeople are more aware of their own — and their children’s — overall health and immune systems than ever before. As such, there has been a massive rise in nutraceuticals owing to the numerous benefits, both individually and collectively, they have on the immune system.This is evidenced by the increased purchase of dietary supplements that promote better health and wellness, prevent the onset of chronic diseases, help to maintain bodily structure or function and lengthen life expectancy.The growing trend of genetic profiling also reflects people’s desire to invest in wellness and preventive measures to help stave off disease.The nutritional industry is responding to this growing awareness by embracing naturally active ingredients that draw attention to various health issues, such as gut health (pre/probiotics), eye health, sleep issues and menopausal symptoms, and help to provide affordable and practical solutions for a wider segment of the population.Variety is the spice of lifeConsumers are looking for more tailored — and palatable — healthcare products that feel (and taste) less like “medicine” and more like fuel to help meet their nutritional needs and individual health objectives.The industry is responding by offering a raft of different formats, such as liquid-filled capsules, gummies and chewables, dissolving strips, protein bars, shots, effervescents, sachets, softgels and powdered drink mixes to help people integrate nutrition into their daily routines.These variations not only make it easier to consume immune-boosting nutrients, but can also help with compliance when it comes paediatric supplements.Products with sympathetic shapes and flavours are more appealing to children (or even adults).And, by making them more palatable, these variations help to promote the regular consumption of nutritional supplements.Addressing dietary concerns In addition to nutraceuticals that target a range of specific categories, such as bone, brain, heart and eye health, dietary restrictions are a top priority when it comes to purchase decisions.People are looking for supplements that fit into their specific nutritional requirements. Product categories such as clean label, vegan, gluten-free, sugar-free, natural, organic, GMO-free and additive/preservative-free are designed to fulfil these customer needs and preferences.Many of these diverse varieties are ethically approved and offered with well-backed health claims that communicate the link between dietary choices and overall health.Holistic health and well-beingThe mental burden and stress that followed the COVID pandemic has highlighted the importance of mental health and mood, indicating the transition from focusing solely on physical health to adopting a more holistic view.People are now relying more on nutraceuticals than ever to support this view and their changing lifestyles, such as working from home. They are looking for natural alternatives that can enhance their fitness, support and preserve their emotional and psychological well-being, as well as protect them against the growing burden of chronic disease.They are adopting nutraceutical supplements such as ashwagandha to support mental health. In addition, new innovations such as probiotic-infused products can also be used to promote various health benefits.Since the pandemic, nutraceuticals have shown enormous potential. Consumers are choosing products that can positively boost their nutrition and complement their fitness regimes to strengthen their systems and gain maximum results.This change in focus towards more natural, proactive and holistic nutraceutical products, rather than chemical ones — together with the increasing challenges faced by global welfare systems — supports the industry’s growth and expansion, and paves the way for further opportunities for innovation.Referencehttps://www.alliedmarketresearch.com/nutraceuticals-market.For more informationSurya Singh, PhD, Senior Manager, Product Development, Vantage NutritionJnanadeva Bhat, PhD, Head of Formulation R&D (Pharma & Nutra), Vantage Nutrition and ACG CapsulesManali Dalvi, Whitepaper and Publication Lead (Pharma & Nutra), Vantage Nutrition and ACG CapsulesSource: https://nutraceuticalbusinessreview.com/
Read more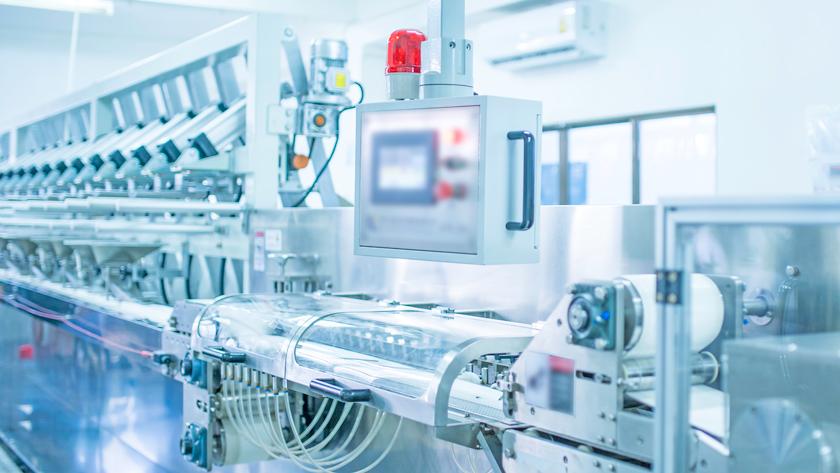
Advanced manufacturing to pave way for pharma industry
The time has come to transition to sustainable strategies – centred around inclusion, innovation, and integration. 2023 will continue to pave the way towards sustainable manufacturing, with a growing number of organisations placing focus on creating long-term solutions. Now is the time for the packaging industry to shine and to drive sustainable alternatives in a tangible way – moving away from the use of plastics during the process of manufacturing medicines and the single-use packaging containers, responsible for a massive environmental burden, in terms of waste management.A matter of mindsetHowever, it's important to note that, while some of the largest and most developed countries and regions are taking significant steps to introduce regulations to drive sustainability, others are still operating as per the status quo, with limited or no regulations in place. Resistance issues can only be overcome by changing the mindset of those involved. From top-down and across supply chains, it needs to be across all stakeholders.We are now seeing the rapid emergence of API facilities globally. Integrating these new facilities with state-of-the-art effluent management systems (for example, a zero or minimal liquid discharge), will help reduce water wastage, generate reusable water for creating more sustainable manufacturing, and help to diminish the industry burden. Companies must integrate a ‘just in case’ strategy, moving away from ‘just in time’, to ensure long-term sustainable manufacturing.Industry 4.0Manufacturing sites employing batch manufacturing methodology, built on legacy processes, will have high set-up costs, quality and reliability issues, and create a lot of wastage. The huge losses which result could be reversed with the use of industry 4.0 technologies. Now is the time for new manufacturing sites to adopt and implement new technologies; to transform pharma manufacturing from being reliant on historical operational methods and facilitate the growth of ‘smart factories’.Digital technology will speed up processes by enabling early detection of wear and tear on machinery lines. It will also help to reduce wastage and recalls by effectively tracking defective batches, allowing for timely interventions.Placing digital ‘Industry 4.0’ technologies – such as AI, machine learning, IoT, and Augmented and Virtual Reality – at the heart of manufacturing can further improve R&D and speed up testing, compliance, and efficiency. Adopting Industry 4.0 technology and new delivery models will build a more self-reliant and robust pharmaceutical supply chain to keep up with changing and increasingly complex healthcare needs. At ACG, our focus is on creating high-performing and quality driven manufacturing units that can support smart, connected, and intelligent systems.Healthcare innovationsThe growth of digital health technology and telemedicine will continue to drive healthcare innovations in 2023. Post Covid-19, health tech developments tend to be centred around at-home and remote diagnosis, ultimately aimed at improving clinical outcomes and pre- and post-consultation care for more ‘informed’ patients.The inception of digital technologies will help to aid R&D, improve compliance, and efficiency in manufacturing.Medical devices - The progress in the technology used in medical devices has enhanced the quality of healthcare delivery and support systems, which is creating better clinical outcomes. And I believe that, as an emerging economy and with the third highest start-up pool globally, India is well positioned to be the leader of MedTech innovation in the years ahead.Pre/post consultation care – The ‘informed patient’, thanks to the growth of digital health technology, and the increasing availability of information over the internet, has become prominent. Digital health technology and monitoring have massively helped towards improving the lives and healthcare remedies for people especially, senior citizens, and chronic disease patients. And this is an area where we will continue to see further developments. Appropriate practices and policies must align with our resources, as well as our existing and future needs.Telemedicine - Bridging the gap between hospitals and homes has become more prevalent than ever, following the pandemic. Aided by the adoption of advanced industry 4.0 technologies, as well as device integration, we are beginning to see increasing numbers of complicated tests, such as dialysis at home, being performed.Drug discovery – Finding efficient combinations of medicines and combining medicines into single doses with varied release profiles will be instrumental in-patient compliance.Preventative medicine – Advancements in personalised healthcare using AI and predictive analytics can help clinicians adjust the levels of care they provide based on factors such as age, genetics, or risk, rather than a one-size-fits-all approach to influence improvements to patient outcomes.Personal wellness – The pandemic gave way to a surge in interest and awareness of maintaining a healthy lifestyle, resulting in more attention being given to nutrition, physical activity, sleep, and positive habits related to wellness. Interest in plant-based, vegan, and vegetarian supplement products continues to increase with the growth of nutraceutical alternatives as the most credible solution.India – beyond generics to biosimilarsIndia has evolved into the third largest drugmaker in the world in terms of volume. It now supplies pharma products worth $24.47 billion (FY22), to 200 countries across the world, and generates an annual net trade surplus of $17 billion.Acquiring a leadership position in the pharmaceutical generics sector, now is the time to look beyond generics and the movement towards biosimilars.Inclusion, innovation, and integration will be keywords for the pharmaceutical industry in 2023. Corporates needs to re-think their strategy to fulfil the exponential growth in the sector, by leaning towards digital solutions that, in turn, will open the gates for more eco-friendly structures.About the authorAn organisational psychologist by education, Karan Singh is the managing director of ACG, a future-ready solutions provider to the pharma industry. Passionate about converting ideas into growth opportunities, Singh takes a keen interest in creating entrepreneurial visions that solve real-world challenges. He is an investor and mentor to 35+ health-tech start-ups guiding strategy, technology, expertise, and network. Years of playing basketball as a point guard drives his leadership, communication, and competitive spirit. Singh serves on the ‘India Advisory Board’ for the India-Brazil Chamber of Commerce and is an active contributor to the Global Lighthouse Network community of the World Economic Forum.Source: https://pharmaphorum.com/
Read more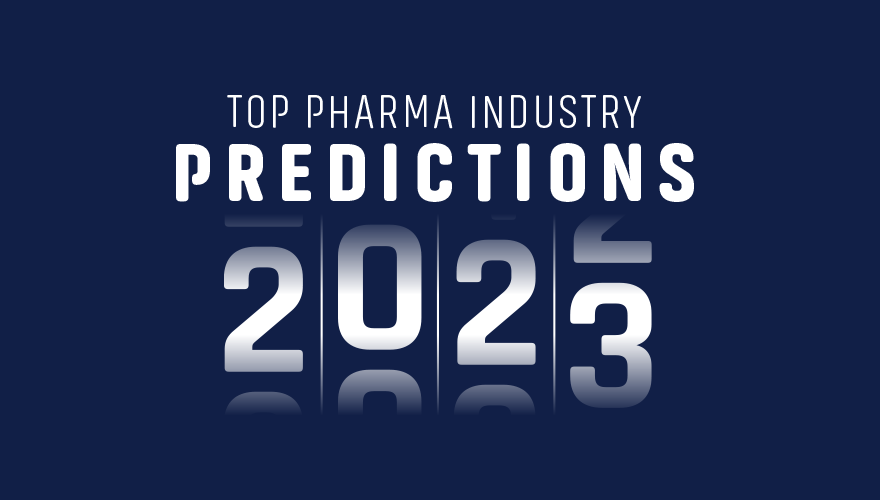
2023 pharma predictions
The pandemic continued to affect supply chains, inflation was at a recent all-time high, and FDA approvals hit a five-year low. The Inflation Reduction Act was signed into law back in August, promising to limit the pharma industry’s pricing power.Despite these tests, the industry experienced pivotal moments. Humira’s patent expiration led to CDER’s 40th biosimilar approval — with more to follow. There was a surge of gene therapy approvals, including the first gene therapy for hemophilia B.Even though pharma’s bar for eventful years was set incredibly high after 2020, the industry is set up for a busy 2023. Here’s a glimpse at what industry leaders are predicting for the coming year.MANUFACTURING TECHNOLOGIESPharma’s insight will be crucial for tech improvements"Pharma manufacturing needs are in part restricted by the available technology manufacturers have access to in the marketplace. As the world population increases, the demand for innovative medicines and increased understanding of genetics, cancer therapies and infectious diseases are driving the need for accurate, repeatable and reliable instrumentation. Going forward, pharma manufacturers will need increased capacity, response time and accuracy — and repeatable instruments will help. Pharma companies partnering with their suppliers to design the products of the future will be critical. As we come from what was once an analog industry to what is now the digital era, it will be the vision of the pharmaceutical industry that drives the technology of tomorrow." — Jeff Gulla, Sales Manager, Scientific MEMS Product Line, Sierra Instruments"Encouraged by technology advancements that permit seamless access and granular control over information, more biopharmas and CDMOs will invite suppliers to participate in key processes within their quality management systems. CDMOs will also increasingly invite their customers directly into their QMS, quality documentation, and training systems for better visibility and real-time sharing of information. This approach will make it easier for smaller innovators to accept products, sign off and approve batches, review quality events, and share quality data. Over time, companies will develop distinct information-sharing strategies, training programs, and new processes tailored to each CDMO or supplier." — Ashley Wentworth, Senior Director, Vault Quality, Veeva SystemsDigitalization will help pharma streamline“Part of a digital transformation strategic solution will be to ‘find the hidden plant’ within a company’s global pharmaceutical manufacturing operations. That is to identify those processes that represent the untapped efficiencies of each manufacturing line and to make the most of capacity and productivity as sourcing needs continue to change throughout the year. Accessing auditable and traceable communication helps to ensure compliance as well as streamline workflows, reducing operational risk and increasing efficiencies." — Andreas Eschbach, CEO and Founder, Eschbach "This year, drug developers will embrace cognitive computing to streamline the safety signal process, positioning themselves to increase their strategic contributions and drive growth. Teams that don’t move forward will struggle with raising case volumes, noisy signals and manual tasks." — Elizabeth Smalley, Director of Product Management and Data and Analytics, ArisGlobal Companies that digitize will reap benefits"We are continuing to see digitalization become a major trend in the pharma manufacturing industry as proper implementation can lead to higher quality products, improved performance, increased customization, and time savings. Pharma companies should keep in touch with the latest trends, while partners focus on supporting customers in adopting new technologies and integrating them into production processes. At Stevanato Group, we witness first-hand how AI can help reduce parametrization and production costs, supporting pharma companies in leading a robust root analysis and moving to a predictive method, exploiting a large amount of data." — Raffaele Pace, Vice President, Engineering, Stevanato Group"Historically, companies have been hesitant to invest in technologies like AI and IoT, and simply tested the waters with small pilot programs. But in recent years, these technologies have matured tremendously, and have proven successful and scalable in global manufacturing environments of all kinds. Companies will ramp up their own digital transformation with confidence now, putting resources into smart technologies to keep a competitive edge. Those leaning into predictive and prescriptive analytics will lead the pack, using data-driven insights to understand and act on the risks posed by increased competition, tight labor markets, higher costs, new product quality standards, and emerging regulations. Lastly, we’ll see areas like maintenance and reliability be recognized as strategic opportunities to eliminate waste. " — Zach Gilula, Team Leader, Pharmaceutical, Life Sciences and Medical Products, Augury"We are seeing the industry beginning to show signs of moving towards more paperless solutions, including electronic batch records. The cost of the daunting number of systems and changes to consider is the most restrictive factor. Sites that adopt a robust digital platform and operating culture will be more successful in attracting and retaining a higher percentage of the workforce." — Cheryl Bondurant, Principal Consultant, CAI"The pharma industry is up against a complex landscape, including supply chain disruptions that are causing a shortage of antivirals and antibiotics, as well as gaps in global medicine access. In addition, the expectations for increased speed to market are higher than ever. In 2023, we can expect to see pharma manufacturers increase digital technology investments in order to help overcome these challenges. The development of smarter manufacturing strategies, powered by automation, AI, and advanced analytics, will drive progress and create new capabilities crucial to maximizing operational agility and efficiency—a major strategic goal for 44% of pharma manufacturers’ digital transformation journeys, according to a recent survey from AspenTech. Equipped with the right tech, pharma companies can make strides toward improving their global access to medicine strategies and ensuring resilient supply chains that can better address medicine shortages." — Kelly Doering, Sr. Director of Pharma, AspenTech Policy will drive adoption of advanced technologies“The Inflation Reduction Act (IRA) will have a profound impact on R&D investment as well as on overall industry earnings for innovator companies. With it, look for pharma to finally get the push they need to adopt more efficient, effective advanced manufacturing technologies like continuous manufacturing, designed to provide lower cost, high-quality drug manufacturing. Small molecule development will be hit hard as they are exempted from negotiation under the IRA for only nine years post-approval, compared to thirteen years for large molecule drugs.” — Bikash Chatterjee, CEO, Pharmatech AssociatesSUSTAINABILITY EFFORTSPharma companies will get serious about their environmental impact“The mission of improving lab sustainability is quickly becoming a top priority in both private and public sectors. As the industry shifts toward more sustainable practices, more responsibility will fall upon private businesses and individuals to enact and meet sustainability goals. The financial and environmental benefits of sustainable practices are prompting leaders in the scientific community to embrace these changes and move initiatives forward. While the requirement for sterility makes using single-use plastics unavoidable in many cases, there are basic adjustments — such as reducing energy and water consumption, conserving materials and properly disposing waste — that labs can make to reduce overall environmental impact without affecting workflow.” — Marwan Alsarraj, Biopharma Segment Manager, Bio-Rad“The life science community and the pharmaceutical industry need to re-double their commitments to long-term sustainability. Today’s innovations can only provide their anticipated impact if we protect them from the consequences of environmental damage. Our community has an opportunity to lead by example as a climate-conscious industry, and we have the scientific chops needed to make it a reality. We need to go beyond carbon offset programs by developing new technologies that significantly improve the sustainability of research workflows and bioprocesses." — Chris Fisher, Ph.D., Scientific Affairs Manager, Provectus Algae"Health care has a substantial carbon footprint, approximately 4% of global emissions, and medicines generate up to one third of that. Additionally, human health is directly impacted by rising temperatures. Health care providers should be motivated to reduce their carbon footprint — and they are. Twenty country health systems have pledged to achieve net zero with target dates between 2030 and 2050. To accomplish this, they will look to medicines suppliers among others, to respond with similar net zero commitments. So far, only eight of the top 100 pharma companies have made a net zero commitment in the same date range. This disparity between goals of health care purchasers and suppliers isn’t sustainable – 2023 might be the year in which the pressure on large pharma to get serious about carbon footprint becomes significant." — Aurelio Arias, Director, Thought Leadership, IQVIA “2023 will continue to pave the way towards sustainable manufacturing, with a growing number of organizations placing focus on creating long-term solutions. Now is the time for new manufacturing sites to adopt and implement new technologies; to transform pharma manufacturing from being reliant on costly legacy processes. Digital technology will speed up processes by enabling early detection of wear and tear on machinery lines. It will also help to reduce wastage and recalls by effectively tracking defective batches, allowing for timely interventions. Inclusion, innovation, and integration will be keywords for the pharmaceutical industry in 2023.” — Karan Singh, Managing Director, ACG"The best route to achieving sustainability goals is through manufacturing and operational efficiency. Securing those objectives requires process data, automation, and systems control, as well as other tools to create smarter manufacturing environments. Although the industry’s integration of digital technologies and its journey to Pharma 4.0 operating models is accelerating, the ability to do so successfully is one challenge I believe the industry will struggle to overcome. Regardless of what is being manufactured, these integrations will never be ‘plug and play’ because every organization, process and operation has unique attributes. Fortunately, accessing this valuable enterprise and operational data to achieve higher-order goals like efficiency and sustainability are becoming easier with the support of the industry’s digital technology and integration solutions providers." — Jim Lehane, Global Leader of Life Sciences Manufacturing, CognizantA look to used equipment “More companies will start to realize the benefits of redeploying equipment within their own network in terms of sustainability and cost savings. Not only is it the most prudent way to save money, but it will also make better use of their existing resources. And the best part, it's a great way to be more environmentally friendly, by reducing the need for new equipment purchases, companies can lower their carbon footprint. This can be a great way to showcase their commitment to sustainability. It's a win-win situation, and I think we'll see more businesses catching on to this trend this year.” — Justin Kadis, Business Development & Operations, Federal EquipmentDRUG DEVELOPMENTCompanies will use the COVID model to drive agility“COVID-19 saw multiple vaccines reach patients in less than a year without compromising safety or scientific integrity. Leading companies will use this blueprint to drive agility into the drug development cycle value chain. Disruptors in the industry will employ different ways of working or reallocating resources to revolutionize processes and decision-making. In certain areas, companies will experiment with smaller, agile teams that work in parallel to drive speed and innovation. This process will also result in increased collaboration with external partners where there is strong alignment, driving exclusive partnerships in certain areas.” — Stephan Ohnmacht, Vice President, Global R&D Business Consulting Lead, Veeva Systems Plant-based platforms will speed clinical development"Biologics are taking the world of medicine by storm and are being used for an ever-increasing number of therapeutic purposes. However, manufacturing biologics cannot occur by inorganic means; drug manufacturers must use live cells such as mammalian to produce the drug in question and then purify it and package it for use. Still, the process has a flaw: engineering mammalian cells to produce large amounts of a biological drug leads them to produce toxic proteins in the cells, inhibiting their ability to make the biologic and slowing down overall production. The use of plant-based platforms to quickly manufacture clinical-grade materials can shift the balance from mammalian cell platforms, which can often take a few months to produce target clinical-grade materials. Plant-based platforms can produce the same, less toxic proteins in a matter of weeks, allowing for multiple targets to be tested simultaneously and allowing clinical trials to get moving more quickly." — Bill Brydges, CEO, Phylloceuticals Drug discovery will move to the cloud"Life sciences companies must keep processes and discoveries out of the wrong hands. In the coming year, more providers of cloud-based life science services will direct the cloud lab conversation to protecting vital scientific data. Carnegie Mellon University is doing pioneering work on a $40 million plan for an internet-accessed cloud lab. This will enable undergraduates, graduates and researchers to perform life sciences experiments without ever setting foot in the lab. Only 10% of rare diseases have treatments, but one in 10 Americans suffer from them. With the ability to experiment in the cloud 24/7/365, rare diseases won’t have to be prioritized downward in pharma development." — Toby Blackburn, Head of Business Development and Strategy, Emerald Cloud Lab Pharma will looks for ways to streamline development"We're seeing real momentum in demand for fully integrated drug development services offerings that span ‘end-to-end’, all the way from candidate development through to late stage and commercial drug product manufacturing. Additionally, where customers can streamline and partner with a single outsourcing provider to meet all key development milestones, this eliminates the non-value add white space traditionally created by working across multiple vendors. Our customers validate these significant benefits, citing real risk reduction, reduced time and reduced expenditure. It is genuinely advantageous to embed deep molecule and program knowledge in a single, truly integrated outsourcing partner. Indeed, this advantage extends beyond the early development space into enabling readiness for commercial product launch." — Sarah Stevens, SVP & Head of Early Development & Late-Stage Commercial, Quotient Sciences"This year, drug developers will embrace cognitive computing to streamline the safety signal process, positioning themselves to increase their strategic contributions and drive growth. Teams that don’t move forward will struggle with raising case volumes, noisy signals and manual tasks." — Elizabeth Smalley, Director of Product Management and Data and Analytics, ArisGlobal SUPPLY CHAINWorkforce pools will widen"Due to the high number of promising transferred therapies in 2023, the pharmaceutical industry as a whole is going to be busier than ever and will therefore need to expand sites and staff. Biopharma sites will be widening their staffing pool. We see more sites hiring more people without GMP experience and/or without a college degree. With this trend emerging, now training, leadership and emphasis on quality culture is more important than ever from onboarding to full position engagement. " — Ellyn Ludden, Principal Consultant, CAICompanies will reinvest in domestic manufacturing capacity"The biotech industry has been historically good in maintaining dual sourcing; however, has not paid particular focus to where in the globe those multiple sources have been located, i.e. frequently for key materials, all commercially available sources are outside of the U.S. This should bring opportunities for re-investment in domestic manufacturing capacity as plants are pulled back from overseas and to win increased volume for smaller domestic manufacturers. Cost increases in biomanufacturing should be muted relative to the broader industry. Biomanufacturing costs are not particularly sensitive to changes in materials cost, and the expected economic downturn will help contain labor costs. Energy/fuel surcharges, particularly in the transportation sector, are here to stay." — Lisa Sellers, CEO, Vector Laboratories"The prevalence of drug shortages caused by reactions to the pandemic raised a difficult question: what's the real cost of no supply and the patient not getting what they need? Businesses are now looking at cost more holistically and acknowledging that the price for low-risk, reliable and quality supply may be higher upfront, but it could have serious advantages in the longer term. So, as a result, we've seen an increased interest in localized outsourcing and demand for our US manufactured APIs and intermediates. Pharma and biotechs sourcing APIs and intermediates are taking a harder look at their CDMO relationships and looking for partners that they trust will deliver against their development and manufacturing milestones. For CDMOs, a demonstrable ability to protect their customers’ patient bases through reliable supply is going to be paramount to growing their business." — Andy Anderson, Global Head of Strategic Account Management, APIs and Intermediates, Pfizer CentreOneBridge facilities will gain traction"Keeping up with market forces will require an increase in demand for advanced therapies that will outstrip current means of production. Building facilities requires validation that can delay the manufacturing process while CDMOs are already operating at capacity; neither alternative will satisfy growing demand. New approaches are being introduced to bridge the gap between building facilities and outsourcing capacity. These so-called ‘bridge facility’ scenarios have yielded a variety of alternatives, including cleanroom licensing. The facilities are being introduced across the country in areas with the greatest pharma and life sciences manufacturing capabilities. Bridge facilities are becoming a cost-effective way for pharma manufacturers to scale their operations to meet demand without building facilities that may remain largely vacant. " — Ravi Samavedam, Chief Innovation Officer, Azzur Group THERAPEUTIC INNOVATIONAlzheimer’s disease will be a key focus"Biopharma desperately needs to deliver clinical successes in 2023, to help remind investors why this sector can be worth the risks. Areas of focus next year include Alzheimer’s disease, where Eisai and Lilly are hoping to succeed where Biogen failed. " — Evaluate Vantage 2023CGT will continue to grow"In 2023, new platform technologies addressing current limitations in CGT will be a key growth area. Cell therapy 2.0 will continue to deliver innate immune cells such as natural killer cells and macrophages as an alternative to T-cells for engineering chimeric antigen receptors. In vivo cell therapy is an emerging field as well. Within gene therapy, alternatives to CRISPR-Cas9 gene editing technology to improve the range and specificity of gene editing will continue to be a focus area." — Sigma Mostafa, Senior Vice President and Site Head, KBI Biopharma"For the year ahead, key growth drivers will include the expanding diabetes and weight-loss market and a strong project pipeline in contract manufacturing, especially with regards to monoclonal antibody production capacity. The outlook for ATMP/personalized medicine will also remain positive. Increasingly, this sector is diversifying to focus on genetic and metabolic conditions, neurodegenerative disorders and cardiovascular disease. Similarly, the year ahead will see messenger RNA continue to evolve at a rapid pace, with more vaccines and therapeutics in the pipeline. mRNA manufacturing remains highly specialized, with each facility requiring specific responses. To address these complex challenges, collaborations between biopharma companies and solutions providers will become more commonplace." — John Noble, Vice President & General Manager, Life Sciences, JacobsChanges will be needed to enable advanced therapies“As commercial approvals continue to occur, for larger patient populations and with potentially long-term efficacy, pharmacoeconomics will loom large. Price and cost bases will have to start trending in a downward direction, or the long-term sustainability of the cell and gene therapy field will be questioned. From a technical perspective, cell and gene therapy needs to enter into an era of deeper product characterization. We will see old analytical methods applied in new ways and new methods applied to current and future products. This will also help with manufacturing cost: you can’t improve what you can’t control, you can’t control what you can’t measure. The volume of potentially successful gene and cell therapy programs is threatening to overwhelm the FDA and indeed the world’s regulators. A paradigm shift is needed in how advanced therapies are regulated if this is not to become an unacceptable bottleneck” — Anthony Davies, Dark Horse Consulting Group, CEO and Founder"To address the enhanced need for viral vectors, a manufacturing trend moving into 2023 will be the broader development and adoption of stable producer cell lines – enabling manufacturers to maintain the production of a consistent and high quality product while expanding output. Although the upfront development time can be extensive, the overall benefits of stable producer cell lines are advantageous in the long run and will continue to have developers switching to this from transient transfection methods. More specifically, a stable producer cell line will facilitate reduced vector variability, improved scaling, lower cost of goods, and remove the need for plasmid manufacturing." — Laura A. Kerepesi, Associate Director, Preclinical Manufacturing, Andelyn BiosciencesNeuropsychiatric disorders pipeline will advance"In 2023, the industry will see innovation in next generation medicines for neuropsychiatric disorders that we haven’t seen for decades. Soon, companies will start sharing data from the pipeline of clinical trials gaining momentum for patients with disorders such as schizophrenia, treatment-resistant depression, and Alzheimer’s Disease from companies like Sunovian’s phase 3 clinical trial of Ulotaront, COMPASS Pathways’ phase 2 psilocybin trial, and Lilly’s donanemab and Roches’s gantenerumab phase 3. Decentralized clinical trials (DCT’s) and simplification of studies will help accelerate clinical trials, and more companies will cut pipelines in response to the Inflation Reduction Act." — David Bleakman, President of Drug Discovery & Development, PsychoGenicsREGULATORY COMPLIANCEThe use of AI for regulatory operations will explode“Today’s regulatory technology solution uses center around gathering data to analyze and use in submissions. However, the use of AI for regulatory operations in life science is about to explode in 2023. Regulatory technology of the future will do much more than gather data – it will also use smart automation and predictive analytics to provide intelligent, actionable insights. Instead of simply inputting data for reporting purposes, intuitive solutions will guide the entire regulatory process while reducing associated risks. Connecting historical data, typically stored in silos, is the big caveat to achieving this next step in AI-driven regulatory capabilities. That’s where cross-functional integration comes in to provide massive amounts of data for regulatory analysis. By starting cross-functional integration with regulatory affairs and drug development, organizations can immediately see the impact of eliminating data silos and effectively managing valuable data across the enterprise. In addition, the comprehensive nature of now-connected data sources will enable more in-depth AI-driven analysis – leading to valuable, actionable insights that improve not only RADDS operations but enterprise success as a whole.” — Michelle Gyzen, Senior Director, Strategic Solutions, Regulatory Affairs & Drug Development Solutions, IQVIACompanies will align AI initiatives with data privacy regulations "In 2023, companies will enact policies that standardize how data is cleaned, managed and approved for AI analysis. Translations of data will be certified by human reviewers, and limitations will be put in place around personal patient information and how it’s stored. This will not only push AI initiatives to success, but will ensure IT landscapes and data analytics comply with regional regulations for data privacy." — Andrew Mitchell, Senior Director, Pharmacovigilance & Regulatory Technology, IQVIAData-based regulatory submissions will take hold“Increasing regulatory pressure will lead to more agile, connected data management approaches that enable companies to ensure compliance globally. In addition, the long-anticipated shift from document to data-based regulatory submissions will soon take place, starting with new FDA and industry initiatives that will use data management approaches for manufacturing CMC submissions. In 2023, more companies will focus on developing the systems, infrastructure, and skill sets required to work with data-based submissions. Far from a trivial effort, this will require an entirely new operating model and substantial organizational change.” — Marc Gabriel, Vice President, Vault RIM, Veeva Systems Source: https://www.pharmamanufacturing.com/home/article/21548855/2023-pharma-predictions
Read more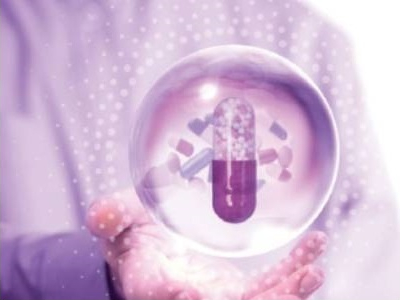
Looking into the OSD Crystal Ball: Industry Experts Reflect on Opportunities & Challenges in '23 & Beyond
The Future of Quality in ManufacturingThe next decade will see pharmaceutical companies change their manufacturing ecosystems with emphasis on product quality, speed to market, efficiency, waste reduction, cost containment and skill retention to meet regulatory and consumer demands. To achieve this, companies are embarking on a digital transformation journey towards a new manufacturing strategy, a concept called Pharma 4.0., to achieve their competitive advantage.The term Pharma 4.0 is a pharma industry interpretation of Industry 4.0—aimed at adopting innovative methods to deliver higher quality products to the market faster and more efficiently. The Pharma 4.0 concept focuses on connecting every segment of the manufacturing value chain to create new levels of transparency with real-time resolution, adaptability, speed from supply, manufacturing, laboratories, quality, distribution. The use of AI technology, data analytics, process analytical testing (PAT), not only provides real time data that quality can review immediately, but insights needed to optimize production, reduce deviations, ensure the right CAPA are implemented, improve metrics, and accelerate product release. While there has been much focus on ICH guidelines such as Quality Risk Management, (ICHQ9), Pharmaceutical Quality Systems (ICHQ10), Technical and Regulatory Considerations For Pharmaceutical Product Lifecycle (ICHQ 12), Validation 4.0, 21CFR Part 11 and Annex 11 in relation to software and data Integrity, it’s notable that these are foundational principles to the implementation of Pharma 4.0 and should not be overlooked.To understand why there is a focus on the Pharma 4.0 concept, it is important to review the critical issues that many organizations are facing. It is not new that market changes, increased competition, increased compliance requirements, scientific innovation of complex products—such as mRNA vaccines as an example—have led to increased manufacturing complexity.The reality within organizations is that once approval has been sought for a new product, or product change, the focus is on speed to market. The lack of robust quality processes, systems and teams connecting and aligning each part of the manufacturing environment, such as supply, manufacturing, quality, and distribution, leads to cumulative quality issues, which can snowball into equipment downtime, deviation setbacks and trends. In addition to this, the time taken for quality to review batch records, analytical data and resolve and document deviations, out-of-specification results at the end of the process doesn’t help either. Thus, organizations find themselves achieving the opposite of that which they set out to achieve and end up delaying product to market. With the focus on speed to market, many of the critical proactive quality steps are not completed thoroughly at the start of the process, by understanding:Risk Assessment & Mitigation (ICH Q9)Capabilities of the entire value stream including product/ process/equipment/software/connected systems. Reference Validation 4.0Continuous improvement strategies to enhance the entire value stream. Reference ICH Q10 and ICH Q12Individual and team strengths across the value stream. Retain, train and re-trainRisk assessment of each part of the process from supply of ingredients to distribution of final drug product is critical to identify effective mitigation steps should issues or deviations occur. Similarly, knowledge of process/product/equipment capabilities supports good root cause identification and critical quality attributes support risk-based decision making.Skill competency within the manufacturing environment also warrants consideration. The onboarding, training, and retention of highly skilled personnel in manufacturing should not be taken lightly. While there are many academic courses available in the quality and regulatory field, the same opportunity is not available in the manufacturing/operational fields. Experience is usually earned after years working in manufacturing with knowledge lost once key personnel leave the organization.The concept of moving from a reactivate approach to quality to a proactive approach to quality and compliance is a key takeaway from the Pharma 4.0 concept. The ability to use data for predictive and proactive purposes will be a must-have for the Quality/Manufacturing teams of the future. This concept will support an organization aligned, connected, motivated with one common goal and that is to provide a safe, quality product, fit for intended use and on time to the customer.Siobhan Ashmore, VP of Quality & Regulatory, Life Science Solutions LLC More Automation in TestingThe pharmaceutical industry is constantly evolving and seeking new ways to improve the efficiency and accuracy of its testing processes. One area in which automation has become increasingly important is in the testing of drugs and other pharmaceutical products. Automation can help reduce the risk of errors, increase the speed of testing, and improve the overall reliability of results.The growing complexity of testing procedures is one driver behind robust automation in the pharmaceutical testing space. As the science behind drug development becomes more advanced, the testing protocols used to evaluate the safety and efficacy of new products become increasingly complex as well. Automation can help streamline these processes, allowing faster testing, with fewer errors.The need for reliable results in the pharmaceutical testing space also contributed to automation’s expansion. In the pharmaceutical industry, even small errors or variations in testing results can have significant consequences. Automation helps ensure that results are consistent and accurate, reducing the risk of errors and improving the overall reliability of testing processes. By automating testing procedures, pharmaceutical companies can also reduce the time and resources needed to complete these tasks, freeing up staff to focus on other important areas of the business.Kevin Whitkanack Senior Director, Pharma Services, Product Development and Marketing, Sotax Customization is ComingA shift from “one-size-fits-most” to personalized products (especially in health and wellness) is an opportunity for businesses to provide more custom experiences. However, doing so without increasing cost or complexity can be a challenge.“One-size-fits-most” has been the guiding principle in medicine, health, and wellness since penicillin was first discovered. The model is based on finding a treatment that brings sick people back to homeostasis more often than not, and it has worked quite well. We’ve eradicated many diseases, extended lifespan and reduced death sentences to mere annoyances. While “one-size-fits-most” has been a boon to humans everywhere, a new trend has emerged, that not only helps bring sick people back up to baseline, but helps healthy people push past normalcy to optimize a healthier longer lifespan we never knew was possible.The ability to personalize products is the result of a confluence of technologies. First, e-commerce made it possible for consumers to shop for anything they desired with ease. Next, robotic advances increased the ability for manufacturers to delay the differentiation of products until just before shipping—making it possible to create slight variations on common products. We must now take that knowledge and technology and apply it where it makes the most sense—healthcare. Consumers don’t just go to a doctor for generalized treatment, but seek out personalized care that optimize their overall wellness. We have the capability to create more personalization through data from blood work, physical exams, and family history. With the availability of new technologies, it’s become easy to personalize wellness treatments at scale. It’s now easy to do this kind of personalization at scale at home without the need for a doctor for the basic things.By customizing the product, consumers get the maximum benefit to their overall health and well-being. In the future, emerging technology will further aid in healthcare personalization.Dr. Andrew Brandeis OK Capsule A Renewed Emphasis on Sustainability Strategies2023 will continue to pave the way towards sustainable manufacturing, with a growing number of organizations placing focus on creating long-term solutions.Now is the time for new manufacturing sites to adopt and implement new technologies; to transform pharma manufacturing from being reliant on costly legacy processes. Digital technology will speed up processes by enabling early detection of wear and tear on machinery lines. It will also help to reduce wastage and recalls by effectively tracking defective batches, allowing for timely interventions.Placing digital ‘Industry 4.0’ technologies – such as AI, machine learning, IoT, Augmented and Virtual Reality – at the heart of manufacturing can further improve R&D and speed up testing, compliance and efficiency. Adopting Industry 4.0 technology and new delivery models can help to build a more self-reliant and robust pharmaceutical supply chain to keep up with changing and increasingly complex healthcare needs. Our focus is on creating high-performing and quality-driven manufacturing units that can support smart, connected, and intelligent systems. Reams of data converts into actionable intelligence, improving several supply chain aspects such as inventory management, trend analysis, forecasting and predictive equipment maintenance.The growth of digital health technology and telemedicine will continue to drive healthcare innovations in 2023. Developments such as medical device integrations and software monitoring will be centered around at-home and remote diagnosis, ultimately aimed at improving clinical outcomes and pre- and post-consultation care for more ‘informed’ patients.Karan Singh Managing Director ACG Persistent Multiple Cost Pressures2023 may prove to be one of the more difficult years to predict and forecast. Cellulosic and other excipient capacities remain extremely tight, backed by strong manufacturing demand. This may ease somewhat in 2024 as more capacity comes on line from several global producers, but we expect inflationary pressure to persist. Producers are focusing on high volume, baseline products as a way of both satisfying customer core demand and keeping cost containment. By focusing on the most widely used products, gains are made in operational efficiency to produce at maximum levels. With fewer changeovers to low demand and low-yield specialty products, cost efficiency can be maximized.This means availability can be addressed at the best cost, but transfers the cost and availability pressure to those specialty and lower-demand products. Manufacturers will face challenges sourcing these specialty grades with limited availability, and thus a higher cost.There is still a lot of cost pressures in the marketplace. Like the ingredient manufacturers, raw material suppliers are approaching manufacturing efficiencies in the same manner – focus on core product in order to maximize output and minimize cost. We are seeing farmers focus on large-volume products like corn, soybean, etc., and less on specialty products, like cotton and sunflower, where they can’t achieve the same level of efficiency per acre. This compounds the availability problem for low volume, specialty products whether it is for the commodity itself, or any specialized versions like non-GMO or organically certified stock.Along with raw materials, cost pressures still persist across the board. New taxes levied in 2023 on energy will have a big impact in our markets. Logistics issues may have waned in the short term, but diesel prices remain high and have not come down at the same rate as gasoline. Equipment and labor shortages persist and will likely remain in tight supply as states like California reduce the number of old trucks on the road. If recessionary fears manifest to reality, logistics may be one of the few places where demand may drop and cost benefits can be achieved.If consumers face decisions with discretionary income, transportation may soften due to reduced overall demand, but basic needs like food, medicine, housing and fuel will likely remain constant.Inflationary pressures will push labor costs up as employees require higher salaries to offset cost increases. The Superfund Chemical Excise Tax re-implemented in mid-2022 will have an enormous impact on processing chemicals. As a result, many basic chemicals used as processing aids doubled, or more, in cost. Labor, oil, and raw materials will also have an impact on packaging so we see cost pressure across the entire supply chain from raw materials, labor, processing, and final packaging.In the end, with mid-term production capacities fixed, we expect high demand and limited availability. While we may get some short-term relief in logistics, inflationary pressures will continue across all sectors of the supply chain. Core products may see some stabilization, but specialty grades and niche products face limited availability and higher prices.Ken Seufert President JRS Pharma Better Tool ManagementOne of the biggest challenges in tablet manufacture continues to be the pressure on time to get a product to market and reducing costs. At I Holland, we are continually working on innovative solutions to help drive the demand for tablet manufacture. An area where we have seen significant growth, and a trend that we predict will continue to grow, is computer-based Tool Management Systems.Modern tablet production requires increased capacity, flexibility, rapid response and robust traceability, with the core objective of maximized press uptime. What was once monitored through simple manual methods is not enough in the current culture of high volume, tightly controlled and audited tablet production. To successfully produce tablets, manufacturers must undertake an in-depth analysis of production.Computer-based monitoring systems can help maximize productivity per punch to meet high-capacity manufacturing requirements. Put simply, a tool management system is a register of all tooling within a site or organization. It fundamentally automates the visibility of what is happening with the tools. Its main objective is to establish compliant, efficient, and accurate maintenance of punches and dies and ensure that the tooling is never a cause for delay in the production schedule.Within tablet production, it is crucial to have a complete audit trail covering tablet tooling usage and maintenance. Using software that has the capability to track this not only makes sense when it comes to production monitoring and management, but is also an essential regulatory requirement within the pharmaceutical industry.The data can also provide information to effectively measure performance areas by showing what and how many products have been produced and a summary of any production issues experienced.By implementing an advanced TMS, problems like wear to punch heads and tips can be detected before they impact production. It can also prompt a call to action highlighting when specific punch and die maintenance actions are required.Implementing a tool management system is invaluable and will always lead to better results. It enables manufacturers to effectively manage their tooling to produce high-quality tablets in an ordered, auditable, and traceable way. Successful tablet production requires forward thinking. Without investment in innovative solutions like TMS, tablet manufacturers are at risk of stalling company growth.Andy Dumelow Head of Technical Sales I Holland Materials-Sparing Formulations Will See Higher UptakeMaterials-sparing formulation development approaches enabled by compaction simulation will be widely adopted. This trend is driven by at least two factors:The need for developing a tablet formulation early so that Phase 2 studies can use the intended market dosage fo;Wider availability of compaction simulators that can simulate both die compaction and roller compaction.Rich information on the properties and performance of API and blends can be collected using grams of material on a compaction simulation. Punch sticking, air entrapment, speed effect, tooling design, and other process parameters can be studied to optimize formulation and manufacturing process so that they are amenable for commercial manufacturing. Companies without a compaction simulator can use resources available from universities and CROs with demonstrated expertise.Dr. Calvin Sun, Professor and Associate Department Head, Department of Pharmaceutics, University of MinnesotaSource: https://www.tabletscapsules.com/
Read more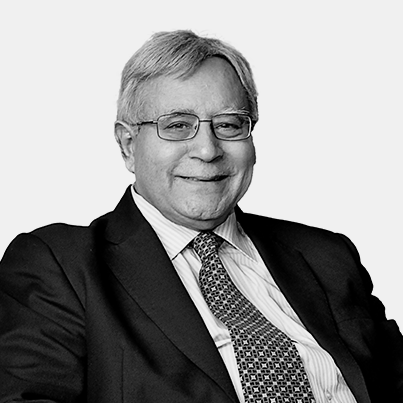
Ajit Singh
Ajit Singh earned his graduation degree from Cambridge University, UK, and post-graduation degree from Harvard Business School, USA. He currently resides in Mumbai, India, and travels widely to study pharmaceutical and allied industries.
Ajit is the Chairman of the ACG Group (formerly known as the Associated Capsules Group of Companies), which is headquartered in Mumbai. He has played a prominent role in the development of the pharmaceutical and allied industries in India and has served as an executive committee member of the Federation of Indian Chambers of Commerce & Industry (FICCI), a regional council member of the Confederation of Indian Industry (CII), Western Region, and other prominent pharmaceutical associations in India. He has also been conferred with prestigious awards for his contributions and thoughtful leadership to the pharmaceutical industry.
Ajit was a founder-member of the Young Presidents’ Organization – India Chapter and the first Indian to be invited to serve on its international board in the USA.
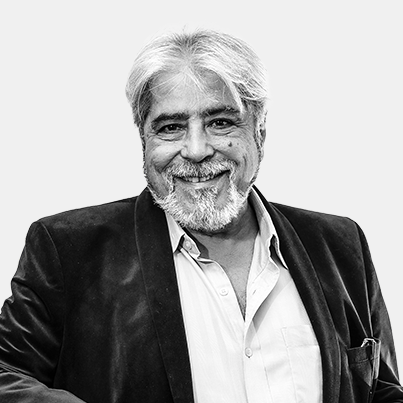
Jasjit Singh
Along with his brother, Ajit, Jasjit started the Associated Capsules Group in Mumbai in 1962.
Jasjit has always been interested in technology – particularly that relating to machine design – and earned a degree in Mechanical Engineering from London University. He has dozens of patents to his credit, and under his leadership the ACG Group has received numerous global awards for technology, excellence and social welfare.
Jasjit has been actively involved with starting new Forums of the Young Presidents’ Organisation. He served as the Chairman of the Mumbai Chapter, and helped found the Kolkata Chapter before becoming a founding President of the World Presidents’ Organisation. Jasjit has also received the Vijay Ratna Award for leadership in Industry, and recognition from UNIDO for his contribution to the fields of pharmaceutical technology and environmental science.
Jasjit’s other interests include self-education, reading, music, collecting rare works of arts and helping young contemporary artists, cooking, and travelling to different parts of the world – especially with his family.
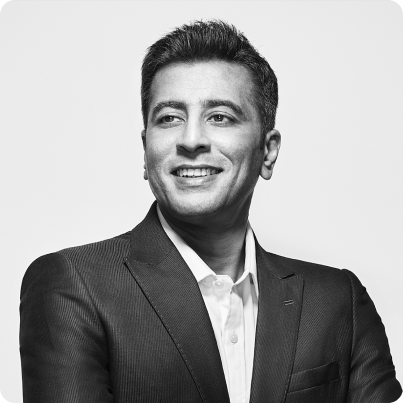
Karan Singh
An organisational psychologist by education, Karan has transformed ACG from a modest Indian business into a world-renowned institution, revolutionising its vision and long-term strategy to ensure global growth. Karan has overseen ACG’s remarkable digital transformation, adopting breakthrough technologies that not only keep medicines safe, affordable, and accessible – but also vastly improve manufacturing and supply chains. Meanwhile, he has led a series of tuck-in acquisitions that ensure ACG pioneers continuously in terms of innovation and scale.
Passionate about converting ideas into growth opportunities, he supports entrepreneurial visions that solve real-world challenges. As an investor and mentor to more than 35 health-tech start-ups, guiding strategy, technology, expertise and networks, Karan seeks to consolidate the next generation of leadership – one that will secure better access and bridge availability across the global health industry.
Karan serves on the India Advisory Board for the India-Brazil Chamber of Commerce, is Co-Chair for FICCI LAC Regional Council, a key advisor to Nasscom, and an active contributor to the Global Lighthouse Network community of the World Economic Forum. Years of keen basketball-playing underpin his leadership, communication, and competitive spirit, and have brought about ACG-NBA Jump, a grassroots programme to give Indian basketballers a global platform.
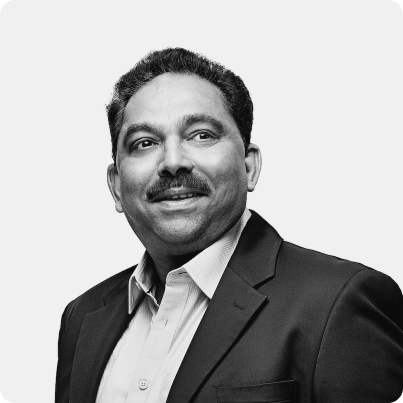
Selwyn Noronha
CEO ACG CAPSULES
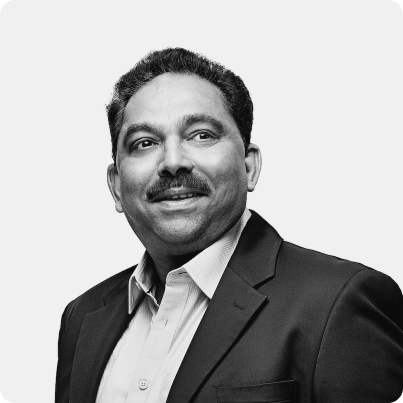
Selwyn Noronha
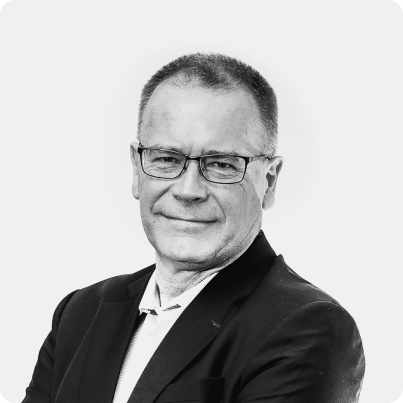
Richard Stedman
CEO ACG ENGINEERING
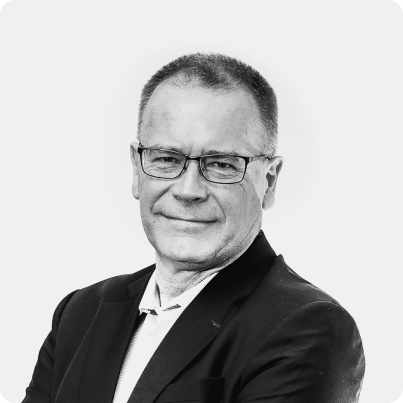
Richard Stedman
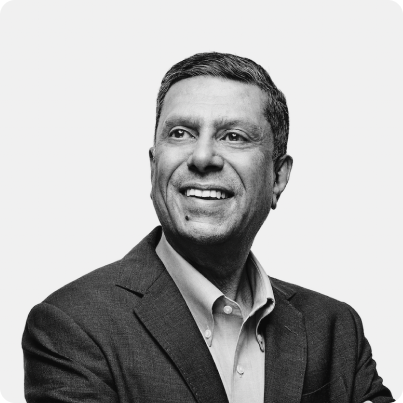
SR Shivshankar
CEO ACG PACKAGING MATERIALS
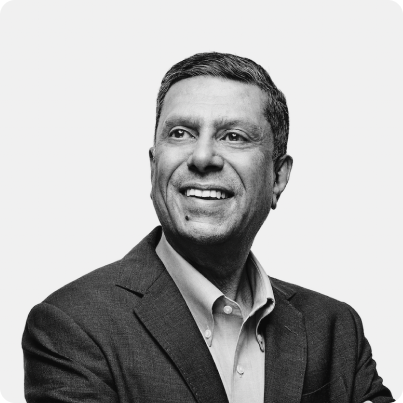
SR Shivshankar
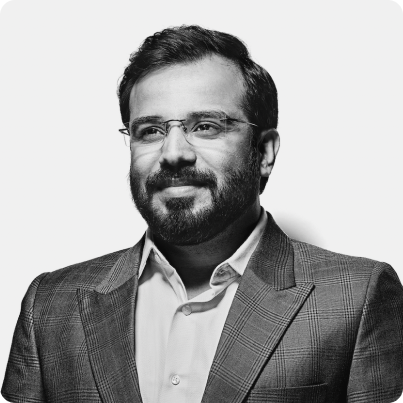
Udit Singh
CEO ACG INSPECTION
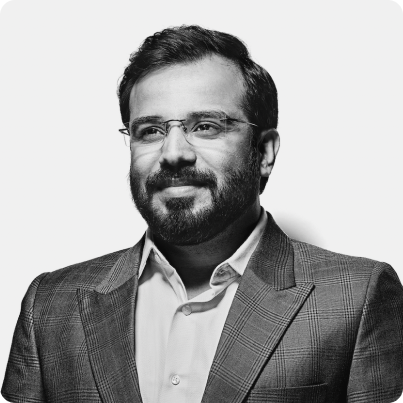
Udit Singh
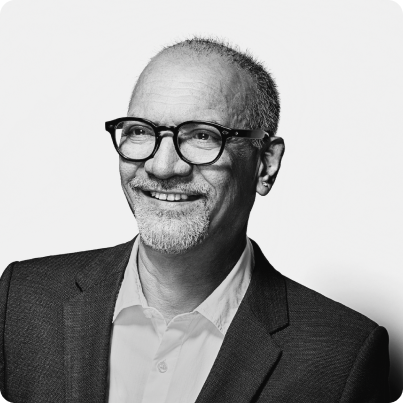
Sunil Jha
Chief Human Resource Officer
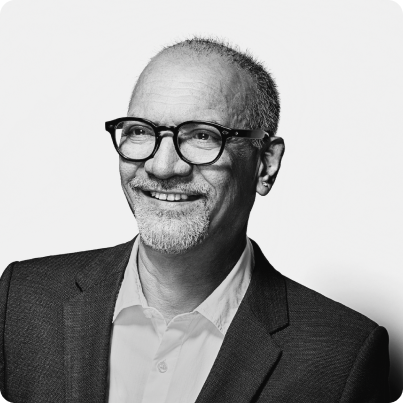
Sunil Jha
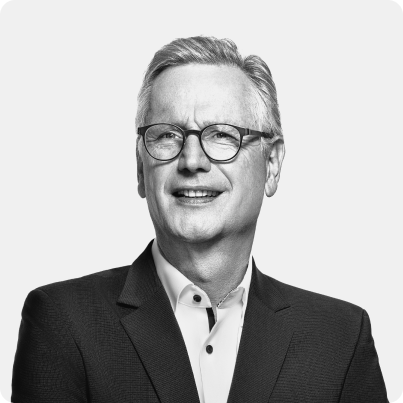
Werner Bongers
CEO SCITECH
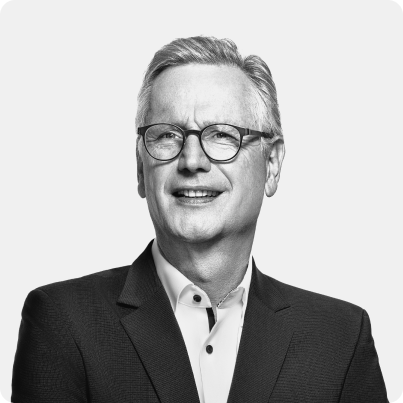
Werner Bongers
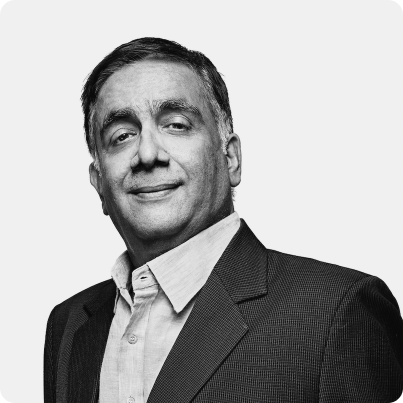
Nitin Desai
Chief Commercial Officer
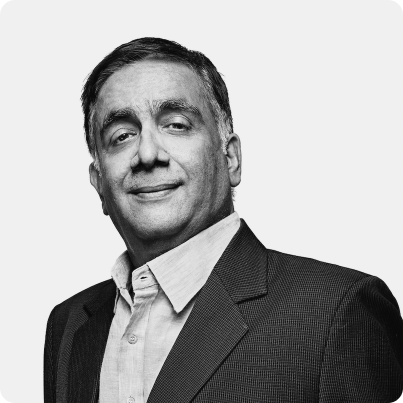
Nitin Desai
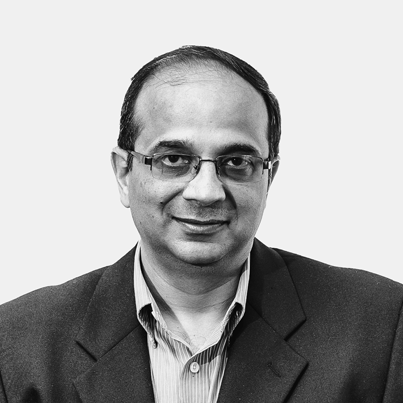
Parag Shah
Chief Financial Officer
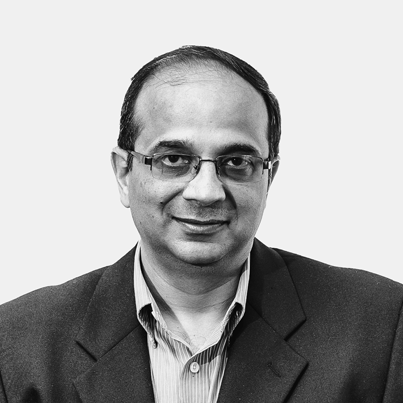
Parag Shah
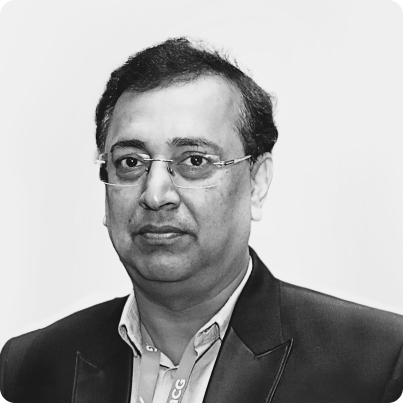
Shankar Gupta
Chief Sales Officer
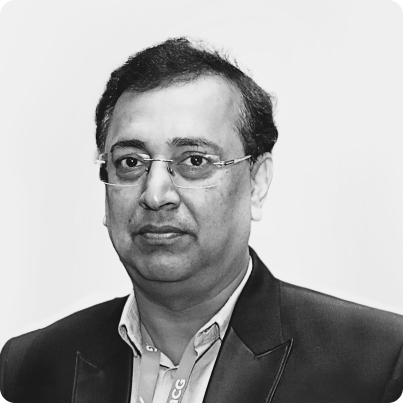
Shankar Gupta
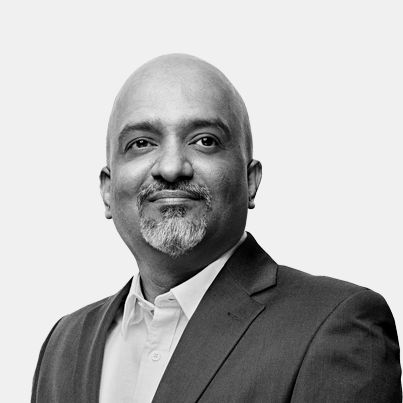
Balajikasiram Sundararajan
Chief Digital Officer
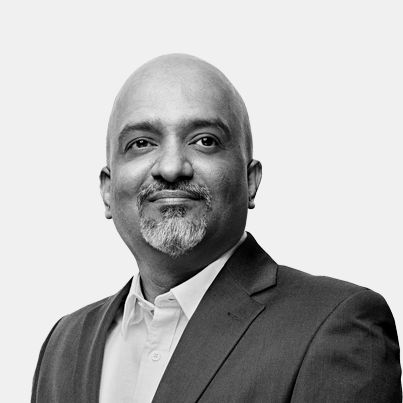
Balajikasiram Sundararajan
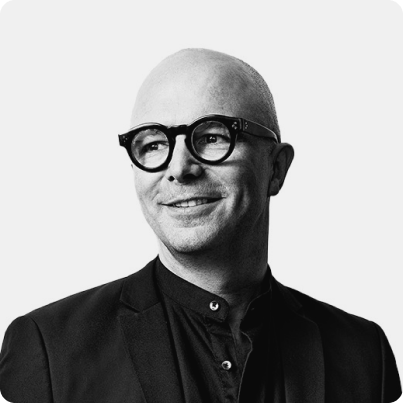
Alexander Robertson
Chief Marketing Officer
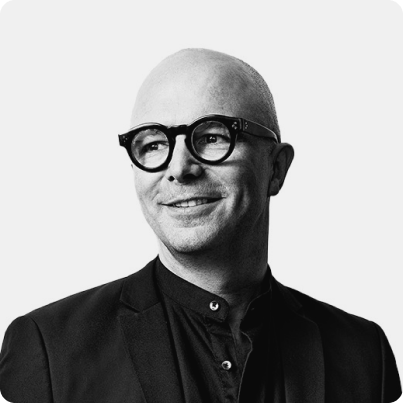
Alexander Robertson
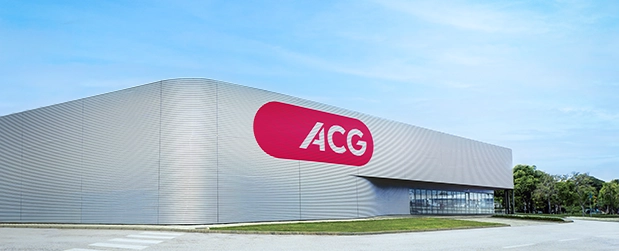
Boilerplate
For over 60 plus years, ACG has been innovating the production solutions for pharmaceutical and nutraceutical companies, that help make people better.
As the world’s most integrated provider of oral dosage products and services, we produce capsules, barrier packaging materials, manufacturing machinery, and visual inspection and traceability solutions. All fully compliant with international standards.
Today, ACG fosters long-term collaborative partnerships with customers in 138 countries across six continents.
Together, we share a common purpose: to solve the world’s greatest health challenges and make it better for everybody we serve.