About the FBC 1800 X•ONE
Supreme safety with ultimate versatility – that’s what you get with the FBC X•ONE series developed at our Design Centre in Mülheim, Germany. While you can use it for diverse applications, including drying, top-spray granulation and Wurster coating, its cutting-edge design and features don’t compromise process or operator safety. In short, you get the very best outcomes and unbeatable protection.
Drying, top-spray granulation, Wurster coating, rotor-based drug layering or tangential spray processes… the FBC 1800 X•ONE does it all, for batches of up to 1800 l.
Applications
Top-spray granulation, wet-mass drying, hot-melt granulation, tangential spray granulation, Wurster coating
Features | Benefits | |
---|---|---|
The 12-bar pressure shock-resistant system features the MOST™ (Maximum Operator Safety Technology) concept approved by the FSA and compliant with ATEX (Directive 2014/34/EU) | No mechanical deformation caused in case of a pressure-shock event Production can be resumed with the machine in the shortest possible time
| |
Unique C-flanges | Prevents the transfer of the explosion pressure beyond the machine | |
X•ONE inflatable seals | Safety at low pressure (as low as low as 4.5 bar) | |
QASV (Quick Action Stop Valves) | Ensures explosion is contained within 20 milliseconds of detection | |
Customised charging, discharging and WIP (wash-in-place) systems available in standalone and granulation-train configuration | Makes processing of granules and pellets highly efficient, while ensuring safety and achieving faster changeovers | |
ACG’s exclusive X•ONE command process control system | Compliant with ATEX (Directive 2014/34/EU), GAMP 5 and 21 CFR Part 11, this advanced technology allows intuitive, secure monitoring and control | |
Patented nozzles developed with Düsen-Schlick GmbH, Germany exclusively for ACG | Enhanced productivity, and simplified operation and cleaning |
Features & Benefits
The 12-bar pressure shock-resistant system features the MOST™ (Maximum Operator Safety Technology) concept approved by the FSA and compliant with ATEX (Directive 2014/34/EU)
No mechanical deformation caused in case of a pressure-shock event
Production can be resumed with the machine in the shortest possible time
Far safer for the environment, thanks to a non-vented, fully contained design
Unique C-flanges
Prevents the transfer of the explosion pressure beyond the machine
X•ONE inflatable seals
Safety at low pressure (as low as low as 4.5 bar)
QASV (Quick Action Stop Valves)
Ensures explosion is contained within 20 milliseconds of detection
Customised charging, discharging and WIP (wash-in-place) systems available in standalone and granulation-train configuration
Makes processing of granules and pellets highly efficient, while ensuring safety and achieving faster changeovers
ACG’s exclusive X•ONE command process control system
Compliant with ATEX (Directive 2014/34/EU), GAMP 5 and 21 CFR Part 11, this advanced technology allows intuitive, secure monitoring and control
Patented nozzles developed with Düsen-Schlick GmbH, Germany exclusively for ACG
Enhanced productivity, and simplified operation and cleaning
Technical specifications
Working volume* | Top-spray granulation | Wurster coating | |
Min | 525 l | 180 l | |
Max | 1956 l | 1185 l |
*Dependent on bulk density
Also Available In
|
Related products
You can’t have healthy people without a healthy planet.
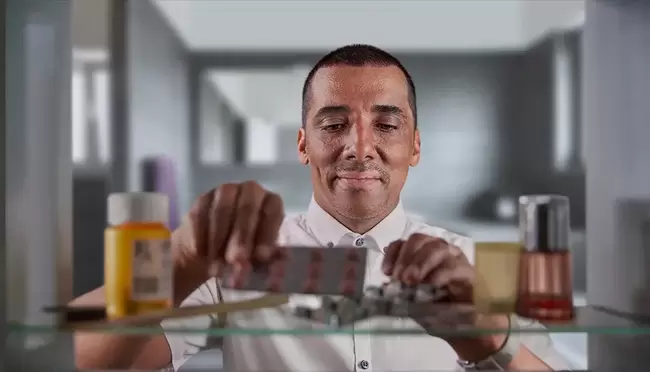